— 9 min read
A Guide to Construction Risk Assessments in Australia
Last Updated Mar 13, 2025
Last Updated Mar 13, 2025
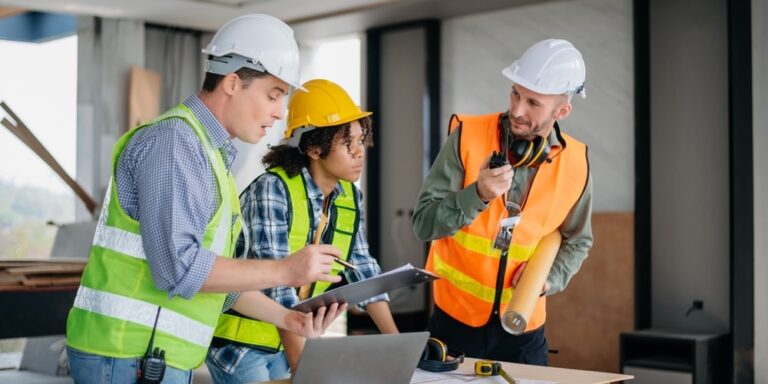
Construction is one of Australia’s most dynamic industries, driving economic growth, shaping skylines, and creating essential infrastructure. But with opportunity comes risk. From worker safety to cost pressures and regulatory compliance, project teams must navigate a complex landscape to keep construction sites safe, efficient, and legally sound.
In 2024, worker fatalities in the sector saw a 36% increase compared to its five-year average highlighting the need for stronger safety measures. Labour shortages and rising costs continue to impact project viability, while new regulations—such as the overhaul of the Environment Protection and Biodiversity Conservation (EPBC) Act and the introduction of the National Construction Code (NCC) 2022—are reshaping compliance requirements.
A well-structured construction risk assessment is one of the most effective ways to manage these challenges. By identifying, evaluating, and mitigating risks, project teams can enhance safety, maintain compliance, and improve overall project outcomes.
In this guide, we’ll consider the role that risk assessments play in Australian commercial construction projects, and how to implement a practical risk assessment process. Whether you’re a project manager, contractor, or developer, understanding how to conduct effective risk assessments will help you build safer, more resilient projects.
Table of contents
What Is a Construction Risk Assessment?
A construction risk assessment is a systematic process used to identify, evaluate, and mitigate risks that could impact a construction project. The goal of a construction risk assessment is to:
- Identify potential hazards and risks
- Determine who or what may be affected
- Eliminate or reduce risks where possible
- Increase awareness of existing and potential risks
- Ensure compliance with legal and regulatory requirements
By proactively managing risks, teams can prevent delays, control costs, and improve project outcomes. While safety hazards often come to mind, risk assessments go beyond physical dangers—they also help assess financial risks, compliance risks, and other factors that impact a project's success. For instance, an owner may conduct a financial risk assessment to evaluate potential cost overruns, market risks, or funding uncertainties.
The Importance of Risk Assessments
Pro Tip
WHS regulations require risks to be controlled in a specific order (the hierarchy of control measures). Using a structured risk assessment process helps ensure compliance with these regulations and reduces the risk of breaches. For example, when managing height-related risks, implementing edge protection and fall prevention systems not only protects workers but also ensures adherence to WHS standar
Risk assessments are essential to construction project management, enabling teams to identify and address potential hazards before they escalate into costly or dangerous issues. By proactively managing risks throughout a project’s lifecycle, teams can ensure a safer, more efficient project that stays on budget and on schedule.
Beyond just safety checklists—risk assessments serve as a strategic tool that helps teams anticipate and address project delays, budget overruns, and regulatory challenges, ensuring that projects run smoothly from start to finish.
Key Types of Risk Assessments in Construction Projects
Understanding the types of risks in construction helps you identify potential hazards and implement effective mitigation strategies. They can be categorised into five main areas.
Safety Hazards The primary goals of safety risk assessments is to ensure worker safety and minimise accidents. These assessments focus on identify risks such as: | Falls from heights—particularly in high-rise and scaffold-heavy construction Vehicle and machinery accidents—especially on tight urban worksites Heat stress and dehydration—common in remote and high-temperature areas Exposure to hazardous materials—such as silica dust, asbestos, and lead-based products |
Financial Risks Financial risk assessments aim to keep projects within budget and ensure profitability | Cost overruns—due to fluctuating material costs, especially concrete, timber, and steel Insolvency of key contractors or suppliers—a common issue in the Australian construction industry Rework and defect rectifications—especially on projects rushed to meet state-funded deadlines Inflation and rising labour costs—due to Australia’s high demand for skilled trades |
Project Management Risks The goal of project management risk assessments is to adhere to the project timeline and meet contractual obligations | Schedule delays—caused by extreme weather events such as bushfires, flooding, and cyclones Poor coordination—between local subcontractors and international suppliers Inadequate documentation—leading to non-compliance with regulatory audits Delays in approvals—due to complex processes from state and local government authorities |
Environmental and Regulatory Risks Environmental and regulatory risk assessments are designed to maintain compliance with state and federal regulations. | Water pollution—from improper stormwater management on commercial sites Non-compliance with the National Construction Code (NCC) 2022—energy efficiency requirements Delays in approvals—due to environmental impact assessments under the EPBC Act Noise and dust pollution—particularly in urban commercial projects |
Supply Chain and Workforce Risks Supply chain and workforce risk assessments ensure that teams have access to skilled workers and necessary materials, minimising delays and cost overruns. | Material shortages—caused by global supply chain disruptions, especially with steel and timber Volatility in material prices—due to import dependency and logistics issues Quality control issues—with non-compliant imported materials such as steel and cladding Delays in workforce availability—due to strict border controls affecting international skilled workers |
How to Perform a Risk Assessment
Performing an effective construction risk assessment is essential for ensuring project safety, efficiency, and compliance. Here’s an overview of the key steps involved in conducting a thorough construction risk assessment:
Pro Tip
Involving all stakeholders, including subcontractors and site workers, can improve buy-in and create greater accountability. This also helps overcome resistance to formal risk assessment processes.
Risk Identification
The first step in the process is to identify all potential risks that could affect the project.
This can be done through:
On-site inspection checklists: Regular site inspections help spot hazards and assess conditions.
Data from similar past projects: Drawing on past experiences provides insights into common risks.
Consultation with contractors, subcontractors, and WHS representatives: Gathering input from people involved in the project helps to uncover overlooked risks.Risk Analysis
Once risks have been identified, each one should be analyzed based on its likelihood and impact. To evaluate a risk, ask the following questions:
How likely is this risk to occur?
How severe would the consequences be if the risk occurs?
For example:
A major structural failure in a high-rise might have low likelihood but high impact.
A minor supply delay for non-essential materials may be highly likely but have a minimal impact.
A fall from height in a multi-storey project has a high likelihood and a severe potential impact.Risk Evaluation and Prioritisation
Not all risks need immediate attention. After identifying and analyzing the risks, you should prioritize them based on their likelihood and severity using a risk matrix.
This step helps determine which risks need immediate mitigation efforts and which can be monitored. Once the risks are ranked, focus on mitigating those with the highest priority (those that are rated Very High).Risk Mitigation Strategies
For each risk, identify appropriate mitigation strategies to reduce, transfer, or eliminate it. Common strategies include:
Engineering controls: For example, installing edge protection systems to prevent falls.
Administrative controls: Enforcing strict site safety protocols and ensuring contractor compliance.
Insurance and financial safeguards: Securing contract clauses that protect against supplier insolvency.Ongoing Monitoring and Review
Risk assessments are not a one-time task. Risks should be continually monitored and reassessed throughout the project lifecycle.
Regular site inspections: Check for new or emerging hazards.
Audits and compliance checks: Ensure the project is meeting regulatory standards and safety protocols.
Dynamic risk assessments: Reassess risks whenever conditions change, such as when a new contractor is brought on-site, regulations shift, or new machinery is introduced.
By continuously reviewing and updating your risk assessments, you can ensure that the project remains on track and risks are addressed proactively.
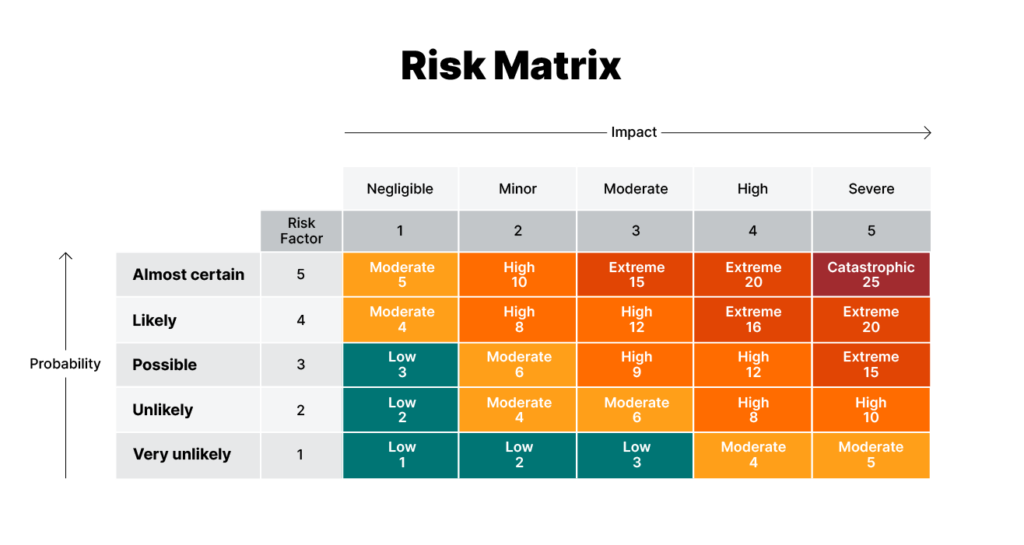
Leveraging Technology for Real-Time Risk Tracking and Reporting
Incorporating digital tools into risk assessments is crucial for real-time tracking and reporting. These tools enable site workers and managers to log hazards via mobile devices, ensuring proactive risk management. They also centralise risk data, helping teams maintain accurate records for regulatory compliance.
Pro Tip
Integrating risk assessments early on helps anticipate disruptions and incorporate them into the project schedule. For example, a project in Brisbane might anticipate heavy rainfall and schedule earthworks, excavation, and concrete pouring before the wet season, adding buffer time for possible delays.
Modern construction technology makes risk identification and mitigation itself easier, with advanced functionality like:
- Predictive risk analytics: Uses historical data and machine learning to identify patterns and anticipate potential risks before they escalate, often catching possible risks before a human could.
- Automated compliance tracking: Continuously monitors construction activities to ensure they meet regulatory and safety standards, reducing human error and oversight gaps.
- AI-driven safety monitoring: Leverages artificial intelligence to detect hazards, monitor worker behaviour, and enhance on-site safety in real-time.
When to Perform a Risk Assessment
Risk assessments are not a one-and-done affair; they should be carried out at various stages of the project to ensure continuous safety and efficiency. Below are the key moments when a risk assessment should be performed
Before the Project Begins
- During the planning and design phase, to identify potential hazards early
- When reviewing construction methods, materials, and site conditions
Before High-Risk Activities
- Working at heights (scaffolding, roofing, multi-storey work).
- Excavation, heavy lifting, and demolition activities.
After Site Conditions Change
- Introducing new equipment, machinery, or materials
- After significant weather events (e.g., heavy rain, strong winds) that impact site conditions.
After a Process Change
- When new work methods or design modifications are introduced.
Following an Incident or Near Miss
- After workplace accidents or near-miss events.
Regularly, As Part of Compliance and Safety Protocols
- Daily or weekly site inspections.
- Before major project phases (foundation, structural, final fit-out).
- As required by regulatory bodies like Safe Work Australia.
Build resilience through proactive risk management
Construction risk assessments are vital for ensuring safety, efficiency, and compliance throughout a project. By identifying and addressing potential hazards early, project teams can mitigate risks, avoid costly delays, and stay within budget. This process should be ongoing, integrated at multiple stages of the project to tackle both anticipated and emerging risks.
Leveraging technology enhances this approach, providing real-time tracking, predictive analytics, and improved decision-making. With the right tools and strategies in place, teams can stay ahead of disruptions and foster a culture of safety and accountability.
Ultimately, proactive risk management ensures that projects are completed successfully, delivering high-quality results while maintaining safety and regulatory standards. By prioritising risk assessments and embracing innovative solutions, construction professionals can confidently navigate challenges and build resilient, future-proof projects.
Categories:
Tags:
Written by
Samantha Nemeny
9 articles
Sam—Samantha if she’s feeling particularly academic—has spent a decade in content marketing, with eight years focused on Australia’s construction industry. She has a knack for making complex ideas easy to understand, turning industry jargon into clear, engaging stories. With a background in SEO and marketing, she’s spent the past three years at Procore, helping industry professionals navigate the world of construction with content that’s both insightful and easy to digest.
View profileExplore more helpful resources
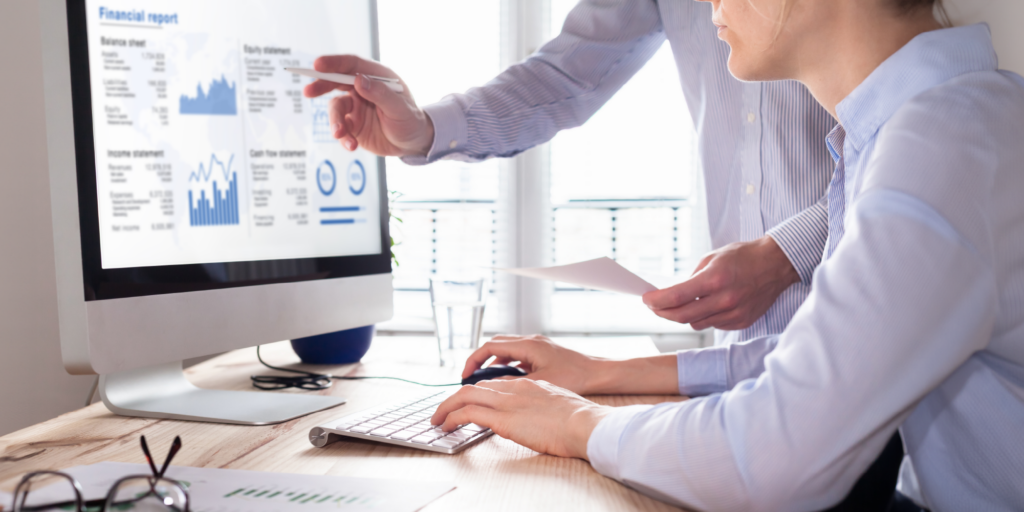
Cash Flow Forecasting in Construction: How to Stay Ahead of Funding Gaps and Protect Project Performance
Cash shortfalls are a leading cause of stalled projects, unpaid contractors, and budget blowouts in construction. Without a clear forecast of how cash will flow in and out over time,...
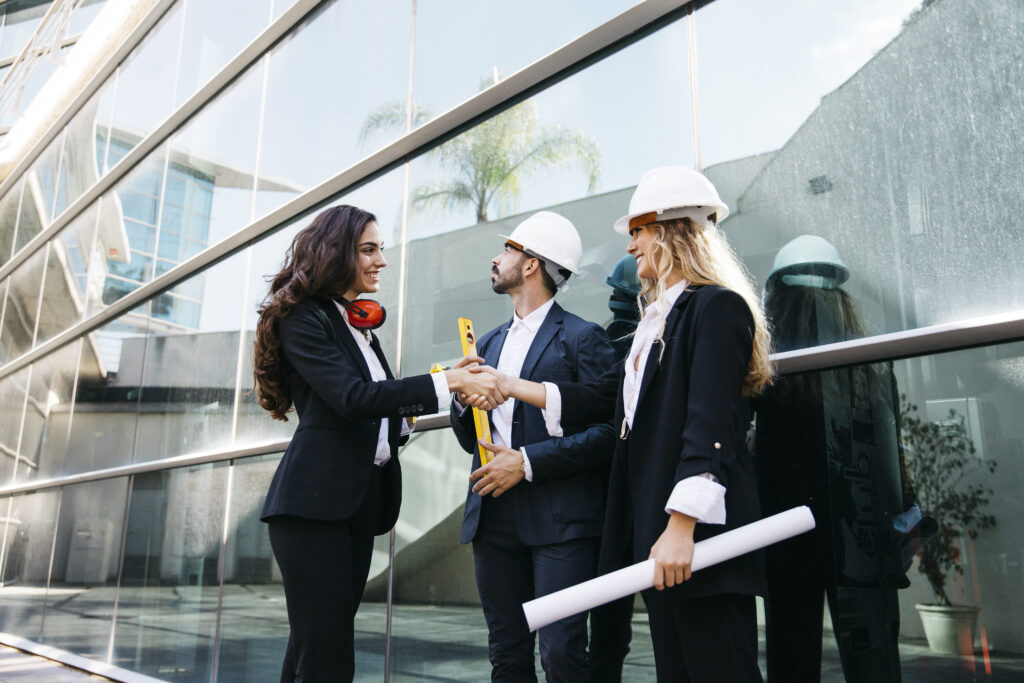
Construction Handover: The Keys to a Smooth and Successful Transition
Project handover should be a seamless transition, but its success is determined long before the last walkthrough. When teams consistently align on design, timelines, and quality, and support that alignment...
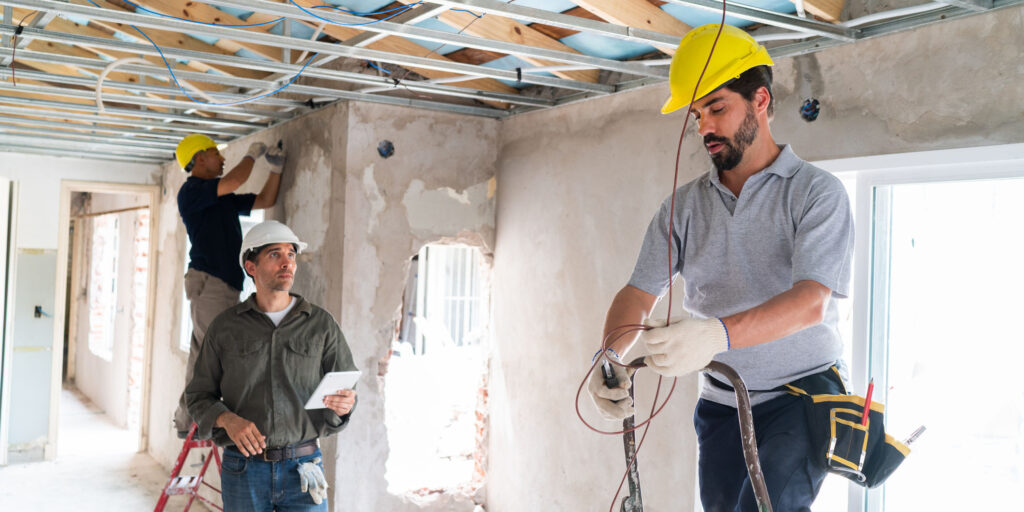
Cutting Delays and Costs: Proven Ways to Boost Construction Site Efficiency
On-site efficiency separates profitable construction projects from those plagued by delays and budget overruns. In Australia’s construction landscape—where supply chain disruptions, skilled labour shortages, and increasingly strict regulations are the...
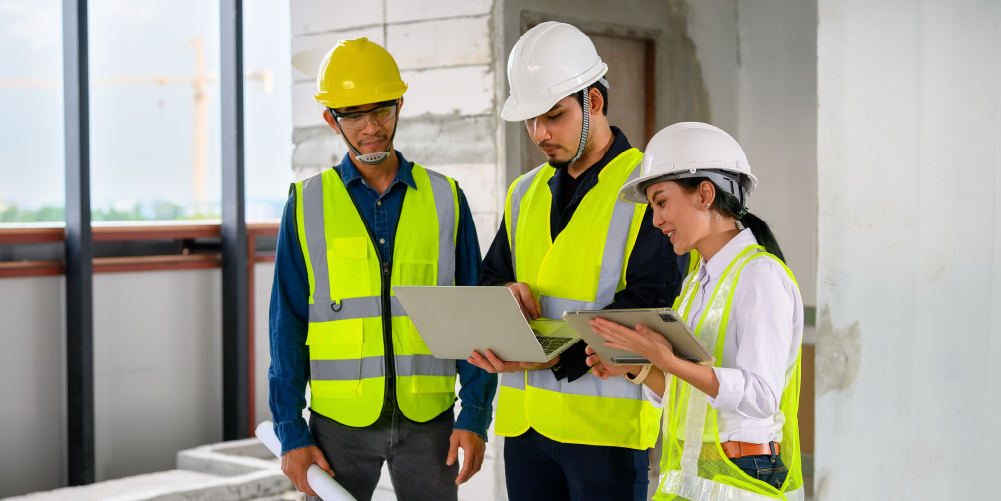
Why Communication is the Hidden Risk Factor in Construction
Construction is a high-risk industry—not just financially, but physically and reputationally. While significant effort goes into mitigating physical hazards, ensuring financial control, and protecting contractual interests, one of the biggest...