— 6 min read
Ctrl + Build: Copy. Paste. Power Up. – Why Standardisation Gives Data Centre Builders an Edge
Last Updated Apr 29, 2025
Last Updated Apr 29, 2025
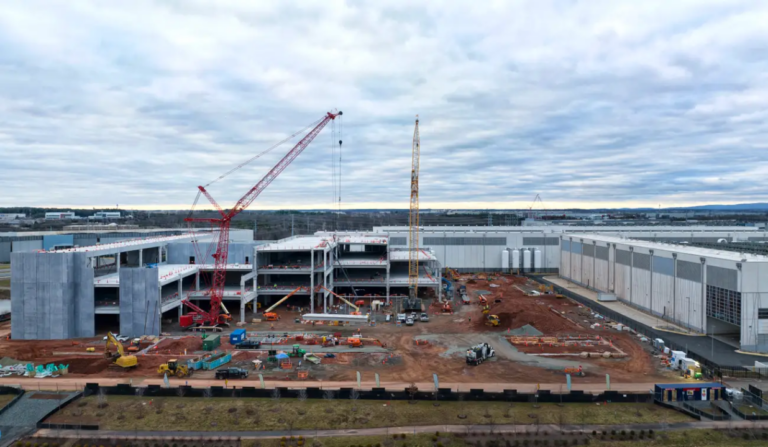
In a high-stakes race to deliver digital infrastructure, standardisation reduces risk, improves quality and gives project teams the “right first time” advantage.
Cranes across our city skylines tell the story: the data centre boom is on.
Australia’s data centre construction market is worth an estimated AU$3.64 billion today. By 2034, it could reach $6.24 billion according to some estimates – almost doubling in a decade.
Table of contents
A Boom Without a Blueprint
The skyline shift is visible in the data. RLB’s Crane Index shows data centre cranes across Australia increased 16% in the first quarter of 2025.
And yet, amid all this activity, one thing is missing: a blueprint.
“There’s no standard approach,” says Simon Baker, Solutions Engineer at Procore. “Every design is different. Every project team does it differently. Every builder has their own process and software. Every project has its own quirks.”
That might sound like innovation – but it’s not. It’s risk.
As builds scale and complexity rises, the absence of repeatable systems multiplies friction, confusion and cost. As digital demand accelerates, a bespoke-by-default mindset just won’t cut it.
There’s no standard process for data centre construction. That’s a huge challenge as we scale to meet demand.
Simon Baker
Procore
Why Repeatability Matters
Standardisation is the secret to scaling safely and predictably.
In other asset classes – think logistics parks, hospitals or schools – standardisation enables faster builds, lower costs and tighter quality control. The same is true for data centres.
And with data centre owners under pressure to deliver at speed while meeting exacting performance standards, predictable outcomes are non-negotiable.
Repeatable workflows also support smoother onboarding, cleaner handovers and stronger sustainability outcomes – especially when digital verification and audit trails are embedded from Day One.
Counting the Cost of Complexity
Standardisation is often framed around time and quality benefits. But the cost case is just as compelling.
According to Cushman & Wakefield’s 2025 Asia Pacific Data Centre Construction Cost Guide Australia is the third most expensive market in Asia Pacific for data centre development – behind only Japan and Singapore.
Construction costs in Australia rose by 5% in 2025. Average costs per megawatt have surged past US$9.6 million, and high-spec builds in Sydney and Melbourne are tipping over US$11.6 million.
These numbers capture more than steel and structure. They reflect a growing chunk of spend funnelled into services – mechanical, electrical, cooling, fire protection systems – along with cost blowouts from rework, scope creep and duplicated effort.
With skilled contractors commanding a premium, complexity adds even more to the bill.
Table 1: Data Centre Construction Costs Grow
Market | Mid-range Cost Per MW (USD) | Year-on-Year Increase (%) | Cost Rank |
---|---|---|---|
Japan | $13,235,400 | 4.0% | 1 |
Singapore | $11,740,262 | 4.5% | 2 |
Australia | $9,632,409 | 5.0% | 3 |
South Korea | $9,504,758 | 3.0% | 4 |
Hong Kong, China | $9,391,444 | 2.1% | 5 |
Source: Cushman & Wakefield, 2025.
How to Break the Bespoke Cycle
If every data centre has the same outcome – a secure, reliable facility to store data – why are no two builds alike?
There are several reasons, Simon Baker reflects. Each site introduces unavoidable regulatory, climate and infrastructure variables.
But the industry is young, with few shared delivery norms. Operators compete on innovation, using new design features – whether that’s immersion cooling or natural air filtration – as market differentiators. Overall, there’s a long-held belief that bespoke design equals competitive advantage.
Simon Baker
Procore
But as digital infrastructure matures, leading developers are shifting focus – from ‘one-of-a-kind’ to one-way-to-build.
Outcome is the same. Delivery’s the difference. And every difference adds cost.
Simon Baker
Procore
Custom builds often rely on legacy habits or informal knowledge – the site manager’s spreadsheet, the subcontractor’s paper checklist.
This might work once. But it won’t necessarily work twice.
When projects lack shared templates and structured workflows, mistakes get repeated, not resolved. Finger-pointing replaces accountability. Quality slips. And the bottom line suffers.
In contrast, a consistent process – delivered through a shared platform – reduces rework, clarifies responsibility and embeds trust.
Standardisation in Action
Some of the world’s largest technology companies are beginning to mandate standardisation.
Maryrose Walsh, Enterprise Solutions Engineering Manager with Procore, is working with one global technology company that requires all builders to use Procore for quality assurance – across every data centre, in every region. The goal? Build it right first time.
“Some of Procore’s clients are managing dozens of builds across as many countries, each with different contractors and project management teams,” Maryrose says. “But they’ve created a single source of truth.”
The benefits are immediate:
- A consistent quality assurance process across contractors
- Real-time dashboards to track progress and flag delays
- Digital inspection and defect management tools to reduce onsite paperwork
- Faster commissioning and fewer surprises during handover.
When you build it right first time, you don’t just save money. You build trust.
Maryrose Walsh
Hyperscale Hypothetical
Many data centre developers are shifting toward repeatable, modular construction models.
Offsite fabrication allows for site preparation and construction to run in parallel — shaving weeks or even months off project timelines. Pricing is locked in early and material waste is minimal.
Controlled factory environments produce consistent outcomes, lowering the risk of onsite defects. And with less work done onsite, modular methods reduce exposure to bad weather, safety incidents and rework.
Repeatable designs can be deployed rapidly across regions, giving data centre owners a competitive edge as they expand.
Here’s what this could look like in practice. Imagine a global tech company plans to roll out five hyperscale data centres across the Asia Pacific. To accelerate deployment, a modular construction model is adopted:
- Standardised shell: Each facility uses precast concrete panels and prefabricated steel frames, manufactured centrally and trucked to site.
- Plug-and-play mechanical pods: HVAC, cooling and power units arrive as complete modules, craned into place and connected via standard interface kits.
- Digital twin alignment: Every module is tracked and quality-assured in Procore against the same digital model, ensuring consistency across all five builds.
- Commissioning checklists: The team uses identical quality assurance templates at each site, with learnings captured in real time to improve subsequent builds.
The result? Less rework. Faster handover. Lower risk. And a scalable, consistent approach that’s ready to roll out again.
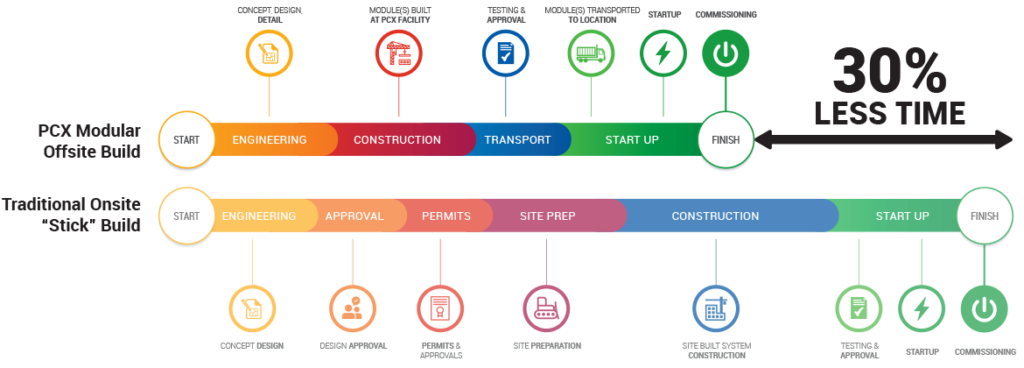
What Data Centre Developers Should Do Next
Every bespoke decision adds complexity. Standardisation reduces risk, cost and time. Procore helps enforce consistency across builds — wherever, and whoever, is on site.
Simon Baker
Procore
Standardisation supports cost predictability – but only if it’s deliberate. Here’s how developers can lead the shift:
- Mandate software in contracts: Require digital tools like Procore for quality assurance, documentation and reporting
- Use consistent templates: Create a standard library of forms, inspection test plans (ITPs), and handover checklists
- Link performance to incentives: Embed rework rates and RFT (right first time) metrics in contracts with builders and subcontractors
- Centralise oversight: Feed quality assurance and commissioning data into real-time dashboards for enterprise-wide transparency
- Insist on digital handover: Structured, digital quality assurance processes ensure nothing gets lost in transition from build to operation.
Categories:
Tags:
Written by
Simon Baker
Simon Baker is a Solutions Engineer at Procore Technologies, where he helps construction businesses across Australia and New Zealand drive efficiency and innovation through technology. Before joining Procore, Simon built a strong foundation in the construction industry, working as a Service Coordinator at Construction Services and Infrastructure, where he was involved in delivering Data Centre projects across Australia. Earlier in his career, Simon spent nearly eight years as an electrician at Castle Electrical & Solar, where he completed his apprenticeship and led residential and commercial projects, including level 2 electrical works and solar and battery installations. With hands-on project management experience and a deep understanding of building services, Simon is passionate about empowering construction teams to deliver better outcomes through smarter processes and technology.
View profileMaryrose Walsh
Maryrose is the Manager of Enterprise Solutions Engineering at Procore and is dedicated to transforming the construction industry through innovative technology solutions. With a life long career in Pre Sales spanning many industries, she has a strong technical foundation in software architecture, integration, and scalable platforms. Bringing this rich experience to Procore, Maryrose excels at aligning complex solutions with the real-world needs of construction businesses through her customer first mindset and strategic approach. With her passion for driving innovation and efficiency, she is dedicated to collaborating with construction organisations to achieve transformative outcomes through technology.
View profileExplore more helpful resources
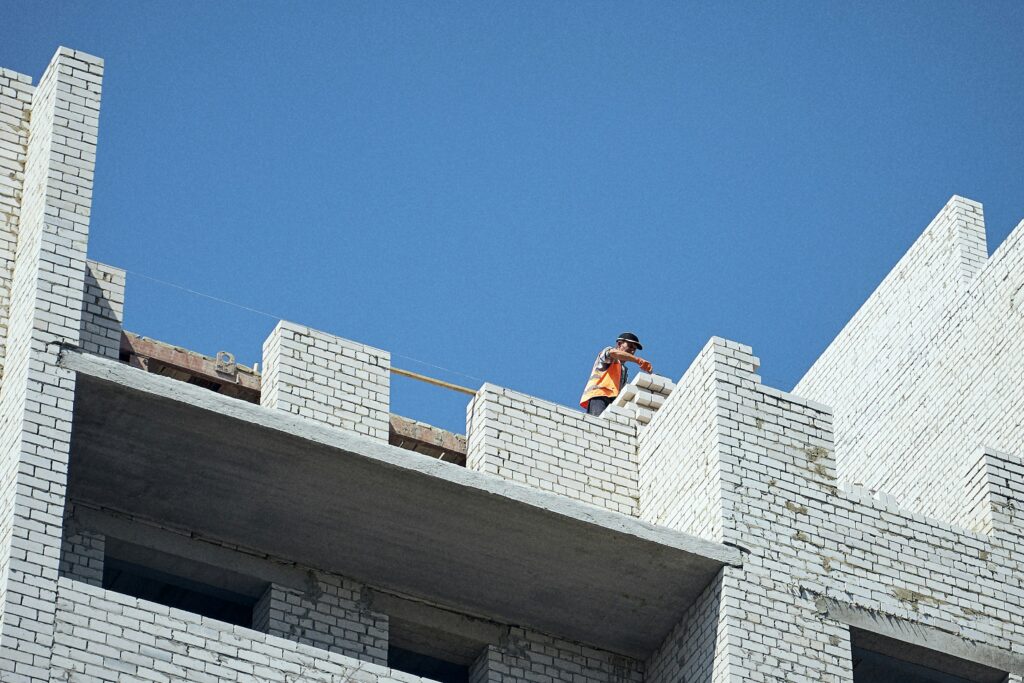
Construction Progress Reports: A Practical Tool for Smarter Site Management
Accurate progress data is essential to managing risk, maintaining control, and keeping stakeholders aligned on site performance. Without it, teams are forced to rely on outdated information, inconsistent updates, and...
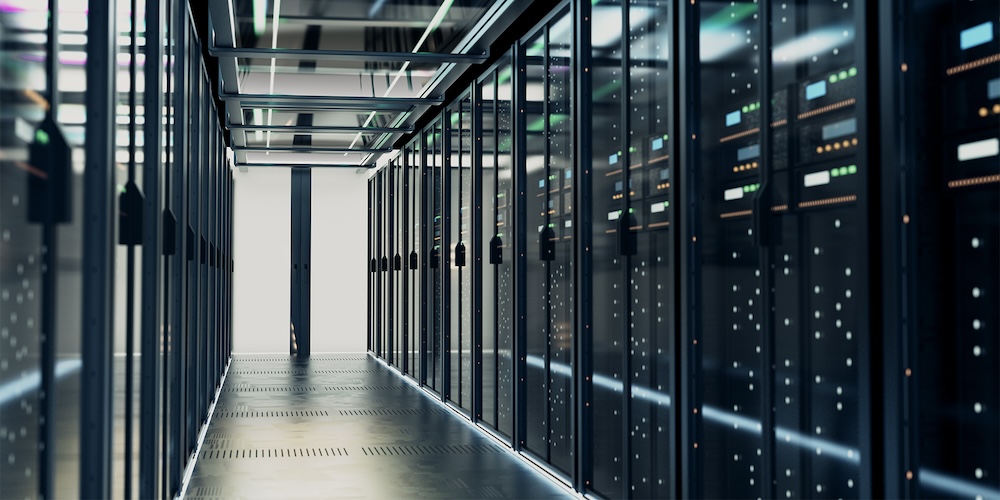
Ctrl + Build: The Data Centre Balancing Act – Why Commissioning Risk is the Biggest Blind Spot in Today’s Builds
This is the first instalment of Ctrl + Build — Procore’s new series exploring the fast, complex, high-stakes world of data centre construction. From commissioning risk to carbon strategy, we’re...
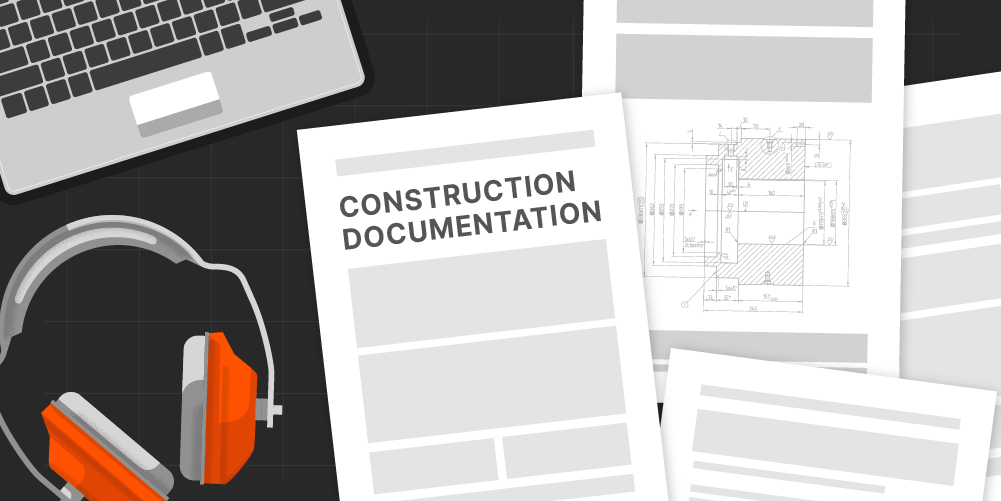
Document Control, Mastered: Blueprints, Binders & the Cloud
In construction, poor document control is more than a hassle—it’s a liability. Mismanaged documents can delay builds, drive up costs, and cause security and compliance issues. It’s a challenge facing...

Construction Progress Claims: Keeping Cash Flowing
In construction, steady cash flow is critical—and progress claims help make that possible. These claims enable staged payments based on work completed, rather than waiting until project completion. In this...