— 5 min read
Inspection and Test Plans (ITPs): A Comprehensive Guide to Construction Quality Control
Last Updated Mar 20, 2025
Last Updated Mar 20, 2025
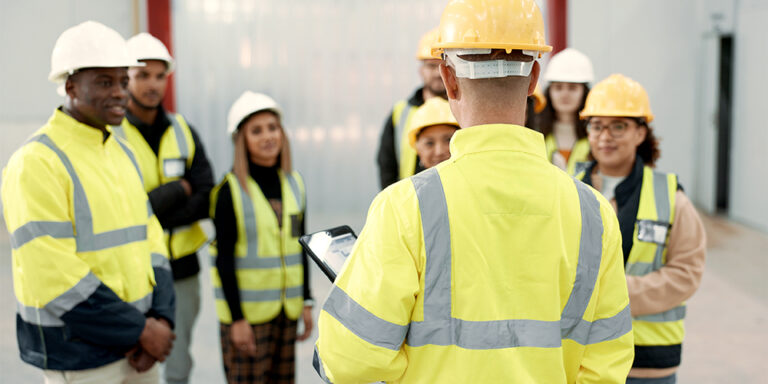
An Inspection and Test Plan (ITP) is more than just a compliance checklist—it’s a proactive quality control strategy that ensures every phase of a construction project meets the required standards. By mapping out inspection and testing checkpoints from start to finish, an ITP helps mitigate risks, prevent costly rework, and streamline regulatory compliance.
In this guide, we’ll break down everything you need to know about ITPs—what they are, why they matter, how to create one, and how they drive efficiency and accountability in construction.
Table of contents
What Is an ITP in Construction?
An ITP is a structured quality assurance document detailing the specific inspections and tests required at different construction stages, such as welding or final building inspections, guiding teams to:
- Ensure each phase meets strict quality benchmarks.
- Identify compliance issues early, preventing costly delays.
- Minimise rework and unexpected project disruptions.
- Support a seamless project closeout.
While ITPs aren’t legally required, they’re often contractually mandated—especially on large-scale projects—because they help builders align with the National Construction Code (NCC) and state regulations. Beyond compliance, they serve as a safeguard for quality, reducing defects and ensuring construction integrity.
How Is an ITP Used in Construction?
ITPs integrate into project workflows to verify that quality and compliance requirements are met at key phases.
Who Creates and Uses an ITP?
Different stakeholders play specific roles throughout the process:
Planning & Development
- Quality Engineers draft the ITP, ensuring all required inspections are covered.
- Construction and Quality Managers refine the plan, oversee its implementation, and track compliance.
- General Contractors & Subcontractors help identify hold points and quality benchmarks.
Pre-Construction Implementation
- The ITP is shared with all stakeholders—contractors, site teams, and inspectors—to ensure alignment.
- Owners & Developers may review the plan to confirm quality control measures are in place.
- Training on inspection procedures and documentation is conducted as needed.
Execution & On-Site Inspections
- Contractors & Engineers perform inspections and tests at key project checkpoints.
- Quality Managers oversee compliance and address any defects before work progresses.
- Regulators or Third-Party Inspectors may conduct audits or witness critical inspections.
Final Verification & Handover
- The general contractor compiles and signs off on the ITP.
- Owners & Developers review documentation to ensure all inspections and tests have been completed before taking possession.
- Digital tracking tools can be used to streamline reporting and record-keeping.
By integrating inspections throughout the project lifecycle, ITPs prevent defects, improve accountability, and ensure regulatory compliance.
The Importance of ITPs in Construction
An effective ITP strengthens quality control, risk management, and compliance:
- Risk mitigation. ITPs help prevent delays, disputes, and cost rework by establishing clear inspection checkpoints and improving accountability.
- Quality assurance. ITPs ensure that materials, workmanship, and installation meet project specifications.
- Regulatory compliance. ITPs help contractors align with NCC guidelines and state-specific regulations, reducing the risk of compliance failures.
- Data-driven decision-making. By tracking inspections and test results, teams can identify trends and adjust quality processes in real time.
- Improved efficiency and collaboration. With standardised inspection processes, teams work more effectively, reducing miscommunication and improving coordination.
How Technology Improves ITP Tracking and Compliance
Traditional paper-based ITPs can be cumbersome, leading to misplaced documents and communication gaps. Digital solutions enhance efficiency by:
- Automating workflows. Cloud-based platforms notify teams of upcoming inspections and flag missed hold points.
- Centralising documentation. Inspection records, photos, and test results are stored in one place for easy access and auditing.
- Providing real-time updates. Mobile apps allow teams to conduct inspections on-site, upload reports instantly, and receive immediate feedback.
- Integrating with project management software. Digital ITPs link to broader construction schedules, ensuring quality checks align with project milestones.
- Enhancing compliance tracking. AI-powered analytics can detect patterns in test results, identifying potential quality issues before they escalate.
What’s Included in an Inspection and Test Plan?
Here’s what you’ll find in a typical ITP document:
- Inspection tasks: Specifies key areas like structural integrity, fire safety, and electrical compliance.
- Quality checkpoints: Establishes acceptance criteria for materials and workmanship.
- Safety and compliance: Outlines adherence to NCC, AS/NZS standards, and contractual requirements.
- Reporting and documentation: Details how inspections are recorded and approved
Most ITPs follow standardised templates and often include visual aids, checklists, or infographics to streamline quality control across multiple projects.
How to Create an Effective ITP
A structured approach ensures an ITP is comprehensive, practical, and compliant.
1. Define the Scope of the ITP
Identify requirements and applicable codes, including:
- AS/NZS standards
- National Construction Code (NCC) guidelines
- State-specific regulations
- Contractual quality standards
2. Identify Inspection and Testing Activities
Break the project into work stages (e.g., material receipt, welding, installation) and specify required inspections at each stage.
For instance, after completing fabrication, you may conduct a fit-up inspection before moving forward to welding.
3. Define Inspection and Test Methods
Specify how inspections will be conducted, such as:
- Visual inspection (e.g., surface defects, alignment)
- Non-Destructive Testing (NDT) (ultrasonic, radiography, magnetic particle testing)
- Destructive testing (tensile strength, impact testing)
- Functional testing (pressure test, load test)
- Dimensional verification (measuring tolerances)
Set pass/fail criteria for each test.
4. Assign Responsibility
Clarify who is responsible for each test and approval, whether it’s the head contractor, a third-party inspector, or a regulatory body.
5. Identify Hold, Witness and Review Points
Determine critical inspection stages:
- Hold Points (H): Work cannot proceed until inspection approval.
- Witness Points (W): The client or inspector is invited to witness but work may continue if they do not attend.
- Review Points (R): Documentation must be reviewed before approval.
6. Define Records and Documentation Requirements
Specify what records are needed, such as:
- Inspection reports
- Test certificates
- Photographic records
- Calibration certificates
7. Develop the ITP Table
A structured table makes ITPs easier to follow. Example:
Activity | Inspection /Test Method | Acceptance Criteria | Responsible | Hold / Witness / Review | Records |
Material Receipt | Visual Inspection | No visible defects | Contractor | H | Report |
Welding | NDT - Ultrasonic Test | AS/NZS 1554 Standard | TPI | W | NDT Report |
Pressure Testing | Hydrostatic Test | 1.5x design pressure | Contractor/TPI | H | Test Certification |
8. Review and Approve the ITP
Finally, the ITP must be reviewed and approved by all stakeholders before it can be implemented.
Maintain quality control with ITPs.
A well-structured ITP is more than a regulatory tool; it ensures quality, reduces risk, and enhances project efficiency. By leveraging digital solutions, construction teams can streamline compliance tracking, improve collaboration, and proactively manage quality across every phase. In an industry where delays and defects can be costly, an effective ITP is essential to delivering projects on time, within budget, and to the highest standards.
Categories:
Tags:
Written by
Samantha Nemeny
9 articles
Sam—Samantha if she’s feeling particularly academic—has spent a decade in content marketing, with eight years focused on Australia’s construction industry. She has a knack for making complex ideas easy to understand, turning industry jargon into clear, engaging stories. With a background in SEO and marketing, she’s spent the past three years at Procore, helping industry professionals navigate the world of construction with content that’s both insightful and easy to digest.
View profileExplore more helpful resources
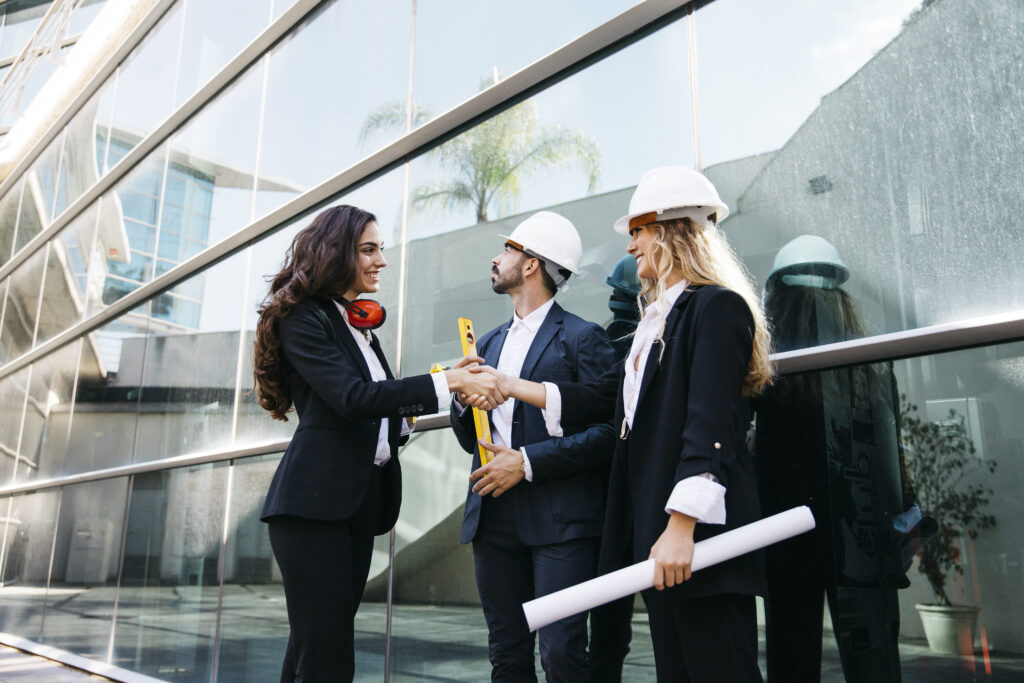
Construction Handover: The Keys to a Smooth and Successful Transition
Project handover should be a seamless transition, but its success is determined long before the last walkthrough. When teams consistently align on design, timelines, and quality, and support that alignment...
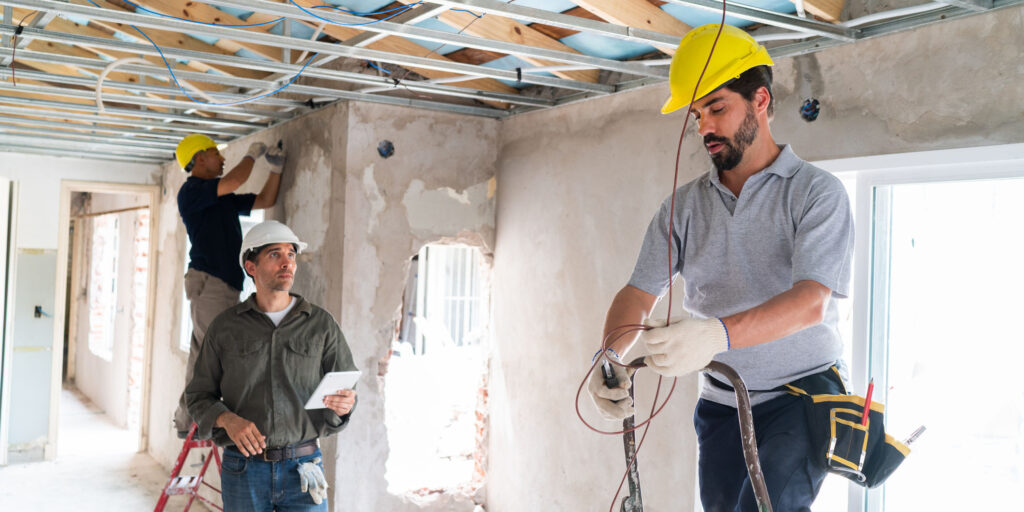
Cutting Delays and Costs: Proven Ways to Boost Construction Site Efficiency
On-site efficiency separates profitable construction projects from those plagued by delays and budget overruns. In Australia’s construction landscape—where supply chain disruptions, skilled labour shortages, and increasingly strict regulations are the...
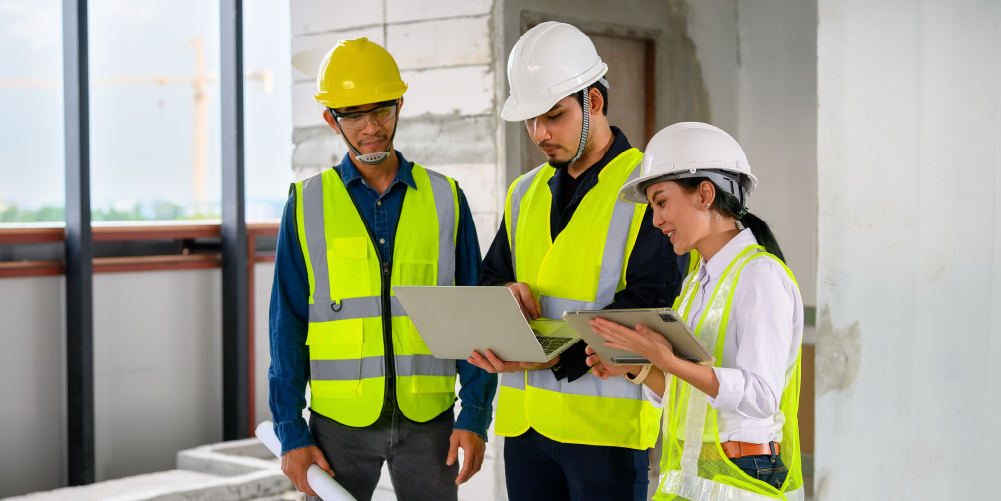
Why Communication is the Hidden Risk Factor in Construction
Construction is a high-risk industry—not just financially, but physically and reputationally. While significant effort goes into mitigating physical hazards, ensuring financial control, and protecting contractual interests, one of the biggest...

Data Centre Construction: Building the Cloud
As the demand for digital data increases, so does the demand for the physical structures and equipment needed to store and process data. Data centres are facilities that house computer systems...