— 5 min read
Dodging Delays & Disruptions: A Smarter Approach to Construction Procurement
Last Updated Jan 30, 2025
Last Updated Jan 30, 2025
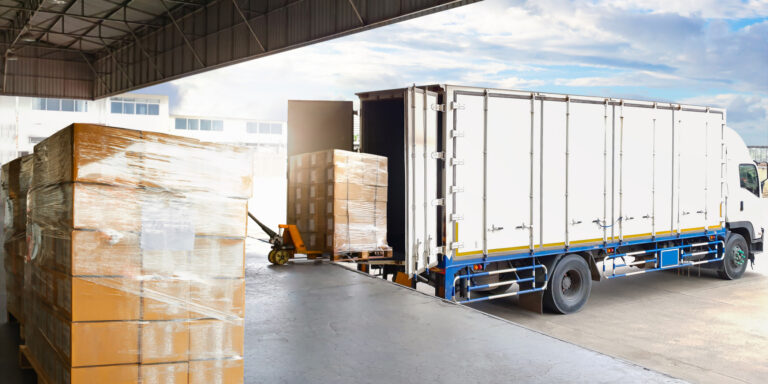
For developers, builders, and project managers, the construction supply chain can either be a project’s greatest asset or its Achilles heel. Procurement connects project goals with the talent, labour, and materials required to deliver a project while balancing factors such as time, cost, quality, compliance, and regulations. As projects evolve, shifting conditions can add further complexity.
Table of contents
Navigating Market Volatility
The pandemic exposed vulnerabilities in global supply chains, with border closures disrupting labour availability and material costs surging due to shipping constraints. Even beyond pandemic-related disruptions, systemic shortages persist, creating chaos in the supply chain of both commercial construction and infrastructure projects. Australia's 2024 Infrastructure Market Capacity report highlights ongoing deficits in key materials such as concrete, steel, and timber, alongside a critical shortage of project managers and skilled trades.
These supply constraints are compounded by the industry’s reliance on outsourced services. An estimated 47% of an average Australian construction project budget is allocated to external expertise—including design, engineering, building services, plant operations, and material installation—making procurement efficiency essential.
Having subcontractors on the ground means you're building, which means you're making money. The mission is to get as many boots on the ground as you can every day.
Michelle Stack
Senior Strategic Product Consultant
Procore
Logistics and Supply Chain Risks
Procurement extends beyond material costs—logistics complexity can result in costly delays. Port congestion, international shipping disruptions, and geopolitical events can all impact project timelines. Optimising procurement strategies reduces waste and mitigates these risks.
A Circular Economy Approach
Integrating material reuse into procurement strategies can minimise reliance on volatile supply chains. Establishing platforms that connect surplus materials with projects in need—potentially through a tender system—promotes efficiency and sustainability. Since this approach is typically localised, it also reduces exposure to overseas shipping risks.
Laying the Groundwork in the Design Stage
Successful procurement and supply chain management begin during early project feasibility and design. Decisions regarding building form, material selections, sustainability targets, timeframes, and budget set the foundation for project execution.
Modern Methods of Construction (MMC), such as prefabrication, modularisation, and Design for Manufacture and Assembly (DfMA), can streamline procurement by reducing on-site labour and material waste. Since MMC requires different procurement timelines than traditional methods, early integration is crucial.
As soon as you win a project, identify long lead-time items and those with high price volatility, locking in prices early to manage risk.
Michelle Stack
Senior Strategic Product Consultant
Procore
In New South Wales, new regulations in the Design and Building Practitioners Act mandate full, detailed design drawings for all major building systems—structure, facade, services, civils, and waterproofing—before obtaining a building permit. This reduces procurement risks by minimising design changes, rework, and budget overruns.
Bridging the Gap Between Design and Buildability
A disconnect between architectural vision and practical feasibility can lead to procurement and construction challenges. Assessing designs for practicality and buildability early in the process helps avoid costly missteps.
The Value of Early Team Involvement
Pro Tip
A design manager can coordinate across disciplines, ensuring that design intent aligns with constructability. In high-rise construction, for instance, early involvement of vertical transportation subcontractors is essential, as lift cores are central to the building structure. Similarly, crane providers and operators should be considered early due to ongoing labor and equipment shortages.
Each trade brings specialised expertise to the project. Engaging lead consultants, construction managers and subcontractors in early design reviews enhances efficiency. For example, while architects focus on aesthetics and user experience, they may overlook opportunities for cost and time savings in service risers, electrical layouts, and civil works.
Engaging subcontractors early fosters constructability input and prevents issues before they become costly.
Ensuring Rigorous Design Reviews
Thorough design reviews reduce procurement risks by addressing:
- Safety – Identifying design elements that pose site safety challenges or require costly safety measures.
- Materials – Ensuring specifications align with project timeframes, budgets, and performance requirements.
- Compliance – Confirming materials and construction methods meet regulatory standards, client objectives, and third-party rating systems.
Material Procurement: Get Ordering in Order
While contractors are adept at estimating large-volume materials like concrete and steel, smaller items such as plasterboard, glazing, tiling, and feature bricks are prone to miscalculations. These issues often stem from:
- Outdated drawings used for subcontractor estimates.
- Client-driven design variations.
- Errors in the original detailed design.
Such miscalculations lead to rework, material waste, and project delays. A critical aspect of good procurement is sequencing material deliveries to match project timelines, reducing the need for on-site storage and mitigating risks like damage, theft, and excess inventory.
Over-ordering results in waste, while under-ordering is even more detrimental, causing project disruptions and increased costs.
You want materials arriving just in time—too early, and you're stuck managing storage and protection. The longer they sit, the greater the risk of theft or damage.
Michelle Stack
Senior Strategic Product Consultant
Procore
Building Strong Industry Relationships
Most commercial builders develop long-term relationships with consultants and subcontractors. While familiarity offers advantages—such as streamlined processes and mutual understanding of expectations—subcontractors must also manage multiple projects, fluctuating material costs, and labor constraints.
A tender price set in 2024 may not be viable in 2025 or 2026, requiring realistic budgeting that reflects market conditions. Additionally, subcontractors may lack resources to invest in supply chain enhancements, procurement efficiency, digitisation, or sustainability initiatives.
If a client requires low-carbon construction, for instance, the head contractor may need to support subcontractors in meeting these new requirements or diversify their service providers.
As client expectations evolve, you may need to seek new subcontractors with broader capabilities. Vetting and integrating them takes time, so planning ahead is essential.
Michelle Stack
Senior Strategic Product Consultant
Procore
Leveraging Digital Tools for Procurement Success
Managing procurement and supply chain complexities requires clear communication, meticulous detail management, and cross-team collaboration. Digital platforms play a critical role in streamlining these processes—from design coordination to materials tracking and workforce management.
Technologies such as construction project management software, BIM (Building Information Modelling), and cloud-based communication tools significantly enhance efficiency. However, adoption barriers—such as cost and consultant buy-in—remain challenges for some companies.
No matter the project type, there are countless moving parts. Coordinating material flow, workforce availability, and site logistics is always a challenge.
Michelle Stack
Senior Strategic Product Consultant
Procore
Seamless procurement leads to smoother projects.
By adopting these strategic procurement and supply chain management practices, developers, builders, and project managers can minimise risk, improve efficiency, and enhance project outcomes. From early design integration and digital transformation to fostering strong industry relationships, success hinges on proactive planning, collaboration, and adaptability in an ever-changing construction landscape.
Categories:
Tags:
Written by
Michelle Stack
10 articles
Michelle Stack is a Senior Strategic Product Consultant at Procore, bringing over 20 years of experience in project management, IT solutions, and change transformation. For 7 years, she has led technology change in the construction industry working closely with teams in design and construction through to post completion. Throughout her career, Michelle has successfully aligned operations with organisational strategies, ensuring changes are implemented through clear communication, training, and evaluation. Her extensive expertise has made her a trusted leader in driving effective, sustainable transformations.
View profileExplore more helpful resources
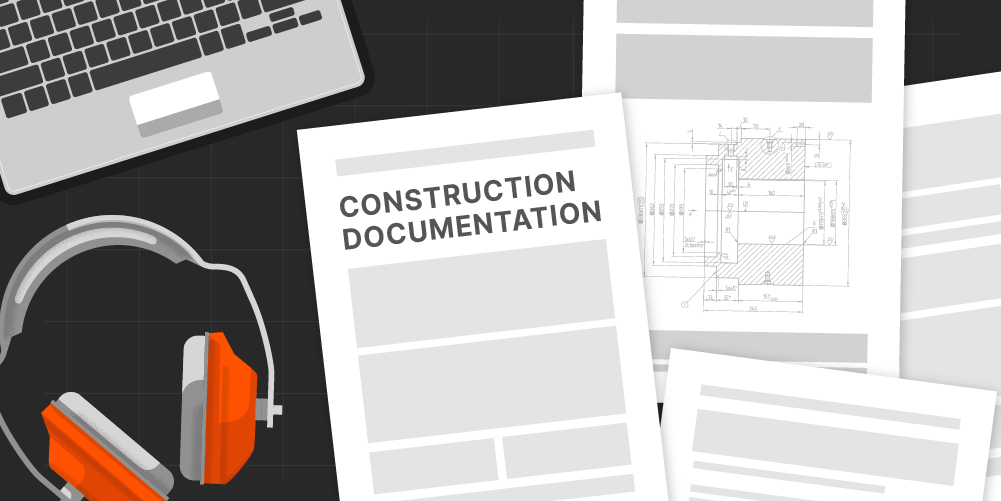
Document Control, Mastered: Blueprints, Binders & the Cloud
In construction, poor document control is more than a hassle—it’s a liability. Mismanaged documents can delay builds, drive up costs, and cause security and compliance issues. It’s a challenge facing...

Construction Progress Claims: Keeping Cash Flowing
In construction, steady cash flow is critical—and progress claims help make that possible. These claims enable staged payments based on work completed, rather than waiting until project completion. In this...
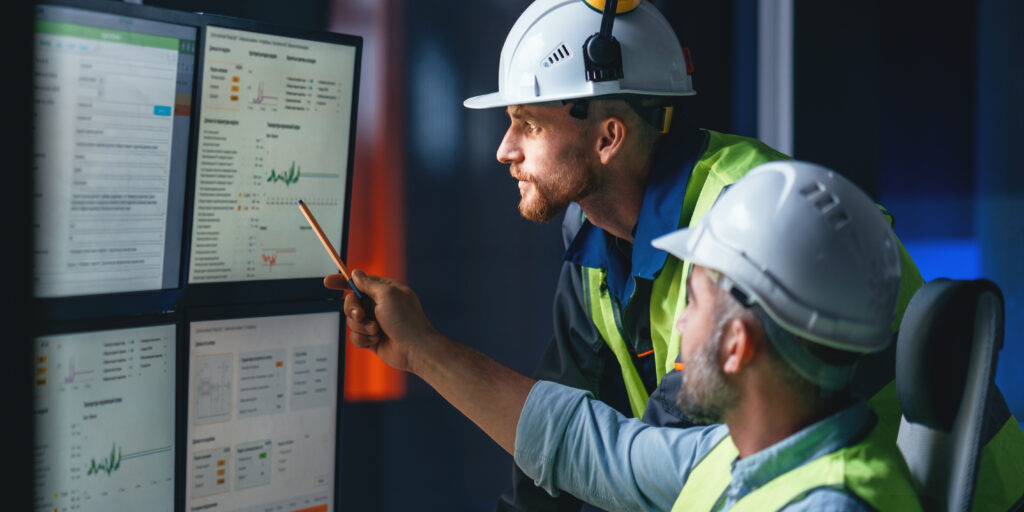
Construction Analytics: The Key to Smarter Decision-Making
Data is everywhere in construction—embedded in schedules, site activity logs, safety reports, and cost tracking tools. Yet despite the abundance of available information, many construction decisions still hinge on gut...

Construction Document Management: The Challenges and Benefits of Embracing a DMS
Every construction project begins, continues, and ends with a mountain of paperwork. From initial bidding documents to contractor agreements, blueprints, variation orders, inspection reports, on and on it goes. And...