— 7 min read
Building a Culture of Quality in Construction: How Safety Approaches Can Transform Quality
Last Updated Jan 27, 2025
Last Updated Jan 27, 2025
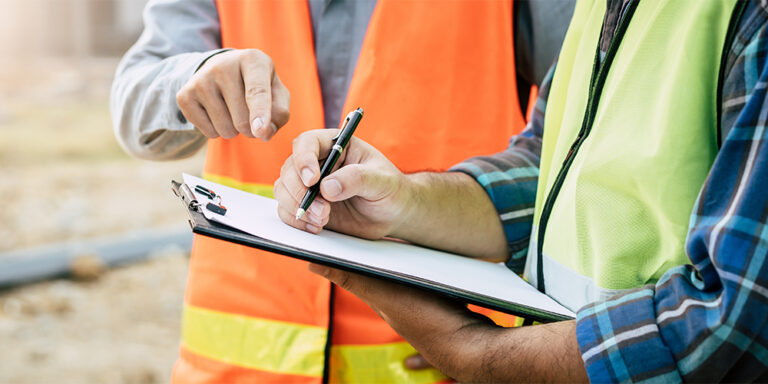
The Australian construction industry faces persistent quality issues that compromise safety, inflate costs, and erode trust. Despite a universal pursuit of excellence, high rates of rework and defects cost billions annually and fail to deliver the value clients deserve. Investigations such as the Royal Commission into non-conforming products, the Grenfell Inquiry in the UK, the Victorian government cladding inquiry, and the Shergold and Weir report repeatedly highlight systemic failures and devastating consequences of poor quality control. Yet meaningful actions often fall short of addressing root causes. These incidents serve as stark reminders of the stakes when quality is neglected.
Reforms like NSW Building Commissioner David Chandler’s compliance improvements and Victoria’s efforts to align with them show promise, but they cannot fully address the industry’s deeper cultural and systemic challenges.
The industry’s success in transforming safety practices over the past two decades offers a valuable blueprint. Focused leadership, robust programs, and cultural shifts have drastically reduced injury and fatality rates. Safety plans, risk registers, toolbox talks, and continuous training have embedded a safety-first mindset on worksites. By applying similar strategies, the industry can achieve a culture of quality that delivers safer, more reliable, and higher-value projects.
We've made incredible strides in construction safety by embracing a culture of documentation and proactivity. Think SWMS, risk assessments, near-miss reporting – it's all about anticipating problems before they happen. Why not apply that same rigor to quality? Detailed building methodologies, quality risk registers, and a system for tracking and analysing defects – these are the tools that can shift the industry from fixing problems after the fact to building quality in from day one.
Tom Proctor
Solutions Engineer, Enterprise
Procore
Table of contents
Learning from Safety: Quality as a Shared Responsibility
The cornerstone of a robust quality culture is shared responsibility. Unfortunately, the construction industry often operates with a "pass-the-blame" mindset, where responsibility is shifted down the chain, leaving subcontractors vulnerable to quality failures. This blame culture hinders collective ownership and continuous improvement. Transforming this mentality requires prioritising quality as rigorously as safety. Every stakeholder—from clients and designers to builders, subcontractors, and suppliers—must champion quality. A holistic approach that integrates quality management into every project stage is key to this transformation.
Quality often suffers from a culture of passing responsibility instead of shared ownership. Many ITPs, including those from owners or developers, are designed to deflect accountability downstream, while imposing unrealistic targets for complex, low-buildability designs.
Tom Proctor
Solutions Engineer, Enterprise
Procore
Strategies and Practical Steps for Improving Quality
1. Take a proactive approach to documentation and reporting.
A key lesson from safety improvements is the power of standardised documentation and reporting. For project managers tasked with identifying and addressing deficiencies, clear and effective processes are essential to initiating corrective actions and preventing rework. What does this look like?
We need to find the sweet spot in quality management – robust enough to drive real improvement, but not so bogged down in paperwork that it cripples smaller firms. We can't let the quest for perfect documentation become the enemy of actual quality on the ground.
Tom Proctor
Solutions Engineer, Enterprise
Procore
Standardised Reporting Templates
Create industry-standard templates that capture essential details, such as the nature of the deficiency, its location, responsible parties, and the required corrective actions. As it stands, there is no consistency in how quality documentation (Eg. ITPs) looks. Consistency in documentation ensures clarity and accountability.
Real-Time Digital Tools
Leverage construction management software to log deficiencies, upload photos, and tag relevant stakeholders. These tools facilitate transparency, allowing teams to address issues promptly and collaboratively.
Detailed Deficiency Reports
Ensure reports include specific descriptions of deviations, supporting evidence (e.g., annotated photos or drawings), and references to contract documents, standards, or specifications. Comprehensive reporting reduces ambiguity and streamlines corrective actions.
Prioritisation of Issues
Categorise deficiencies by severity and potential impact. High-risk issues, such as those that compromise safety or compliance, should take precedence. Prioritisation helps allocate resources effectively.
Clear Communication Channels
Establish protocols for sharing deficiency reports with relevant stakeholders, ensuring that issues are addressed constructively and collaboratively. Regular follow-ups can prevent delays in corrective actions.
Regular Quality Walks
Similar to safety inspections, these on-site evaluations identify potential issues in real time. Use digital tools to create time-stamped records, which serve as evidence for post-project analysis and continuous improvement.
2. Implement data-driven bidder selection.
Clients and builders should implement data-driven frameworks to evaluate potential partners’ quality performance. This involves:
- Benchmarking historical project data to assess contractors’ ability to deliver high-quality projects on time and within budget.
- Establishing clear quality benchmarks during tendering to ensure subcontractors meet rigorous standards.
- Prioritising contractors and suppliers with proven track records of quality excellence.
Imagine a world where developers can select bidders not just on price, but on a proven track record of quality, efficiency, and collaboration. Data makes that possible. By leveraging the insights from past projects, we can move beyond gut feelings and towards evidence-based decision-making in construction.
Tom Proctor
Solutions Engineer, Enterprise
Procore
This approach ensures that quality performance directly influences project awards, incentivising contractors to uphold high standards.
3. Use a holistic approach to construction management.
The international standard for integrated management systems(ISO 14001), recognises the interconnectedness of quality, safety and the environment. As such, neglecting quality during construction often leads to more significant issues later. A straightforward example is a water leak, which if not addressed, results in mold growth - a direct safety hazard for building occupants.
This example underscores how a lack of focus on quality can negatively impact both safety and the environment. By proactively addressing quality concerns, such as ensuring proper waterproofing during construction, potential hazards and costly rework can be avoided. This, in turn, leads to better buildings, reduced environmental impact, and a more sustainable construction industry.
We need to stop treating safety, environment, and quality like separate boxes to be ticked. It's all connected in the end – a well-run project delivers on all fronts. And with technology, we can finally start using data to understand those connections and make smarter decisions from the design stage all the way through handover.
Tom Proctor
Solutions Engineer, Enterprise
Procore
4. Consider creating a quality risk register.
Just as safety relies on risk registers, quality risk registers can:
- Identify responsibility for specific tasks.
- Link work to relevant Australian Standards, NCC requirements, and other regulations.
- Highlight potential failure points and mitigation measures.
Digital formats ensure seamless information transfer across teams and enable real-time updates, enhancing accountability and efficiency.
5. Implement quality talks and walks.
Toolbox talks—a cornerstone of safety—can be adapted for quality. Before starting work, teams can discuss:
- The day’s tasks and potential quality risks.
- Mitigation strategies to achieve quality success.
Similarly, quality walks—akin to safety walks—could allow site managers to:
- Identify potential issues early.
- Celebrate successes and recognise quality workmanship.
- Capture time-stamped digital records to inform continuous improvement.
6. Adopt industry-wide benchmarking.
Adopting industry-wide benchmarking systems enhances transparency and drives collective improvement. Peer comparisons—similar to Green Star ratings and NABERS assessments for sustainability—can:
- Enable companies to measure their performance against key quality indicators.
- Encourage healthy competition and adoption of best practices.
- Leverage tools like Procore’s benchmarking metrics to revolutionise how the industry evaluates and manages quality.
Transforming the Industry: A Call to Action
Transforming the culture to prioritise quality alongside safety is not just about building better structures; it's about creating a better work environment. Embedding quality in every project phase benefits everyone. Projects are delivered on time and within budget, risks are minimised, reputations are enhanced, and, importantly, construction professionals experience greater job satisfaction and pride in their work.
While numerous investigations have shed light on quality control issues in the Australian construction industry, meaningful change requires a deeper cultural shift. By taking inspiration from the successful transformation of safety practices over the past two decades, the industry can create a similar culture of quality. This involves prioritising quality as rigorously as safety, embracing a holistic approach that integrates quality management across all project stages and stakeholders, and utilising data-driven tools and benchmarking systems to drive continuous improvement. This transformation will lead to better buildings, a more sustainable industry, and a more rewarding work environment for everyone involved.
Categories:
Tags:
Written by
Tom Proctor
Before joining the world of technology, Tom worked as a Contract Administrator. This hands-on experience gives him a unique perspective that he leverages in his current role at Procore, where he has been for the past two years. Tom is passionate about helping construction businesses understand best practices in project management solutions. He helps construction businesses understand best practices around project management solutions and the many benefits they can provide.
View profileExplore more helpful resources

Construction Document Management: The Challenges and Benefits of Embracing a DMS
Every construction project begins, continues, and ends with a mountain of paperwork. From initial bidding documents to contractor agreements, blueprints, variation orders, inspection reports, on and on it goes. And...
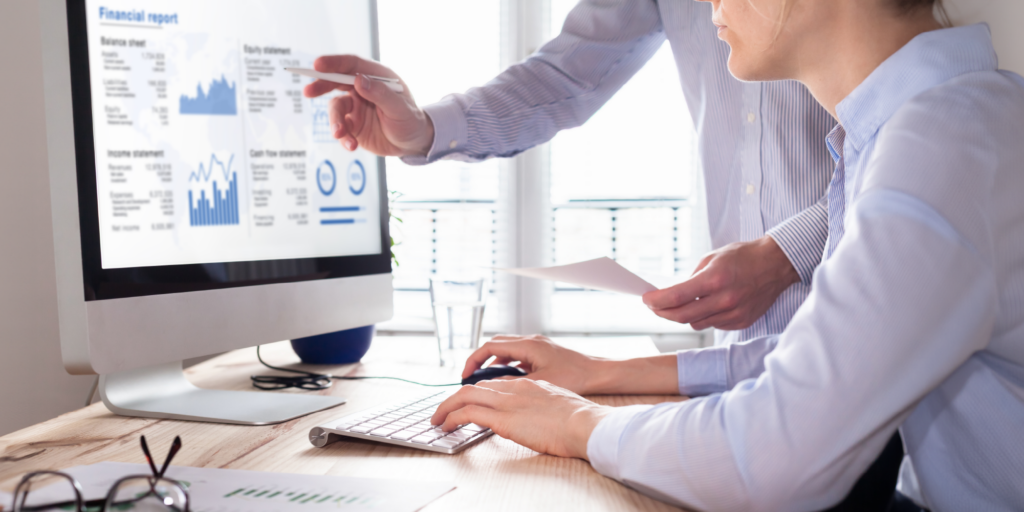
Cash Flow Forecasting in Construction: How to Stay Ahead of Funding Gaps and Protect Project Performance
Cash shortfalls are a leading cause of stalled projects, unpaid contractors, and budget blowouts in construction. Without a clear forecast of how cash will flow in and out over time,...
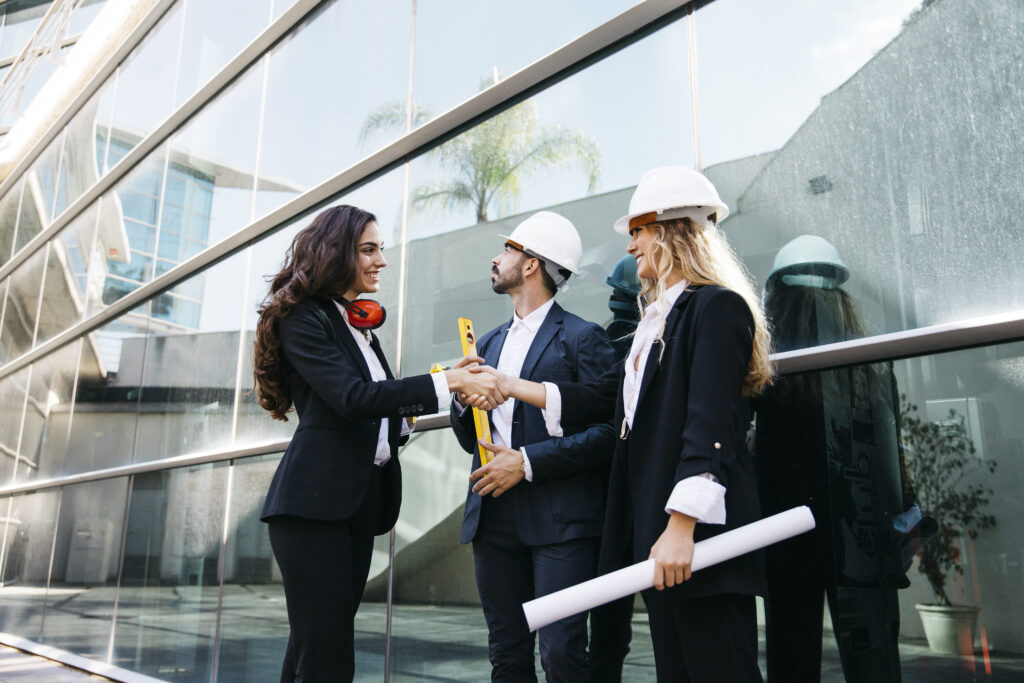
Construction Handover: The Keys to a Smooth and Successful Transition
Project handover should be a seamless transition, but its success is determined long before the last walkthrough. When teams consistently align on design, timelines, and quality, and support that alignment...
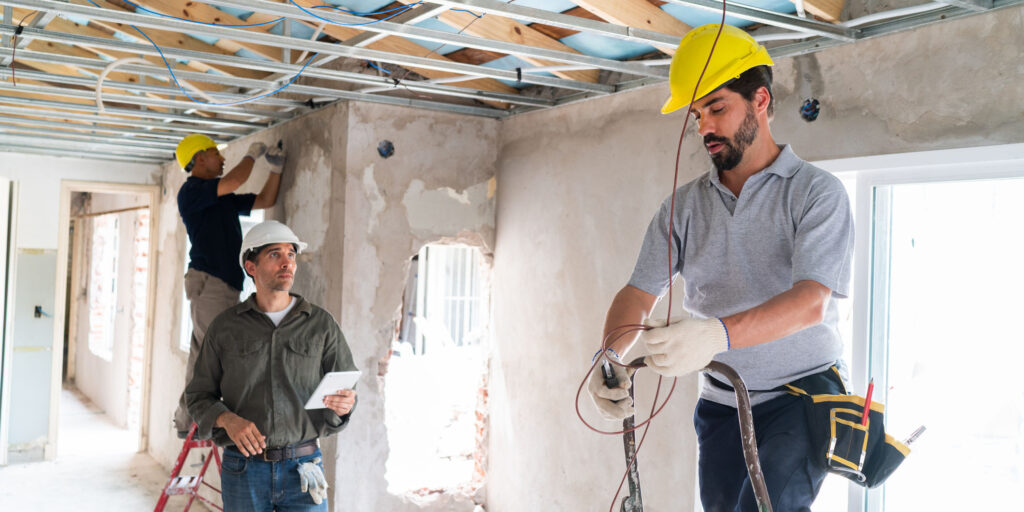
Cutting Delays and Costs: Proven Ways to Boost Construction Site Efficiency
On-site efficiency separates profitable construction projects from those plagued by delays and budget overruns. In Australia’s construction landscape—where supply chain disruptions, skilled labour shortages, and increasingly strict regulations are the...