— 5 min read
Construction Quality Control Explained: Avoiding Costly Mistakes
Last Updated Feb 5, 2025
Last Updated Feb 5, 2025
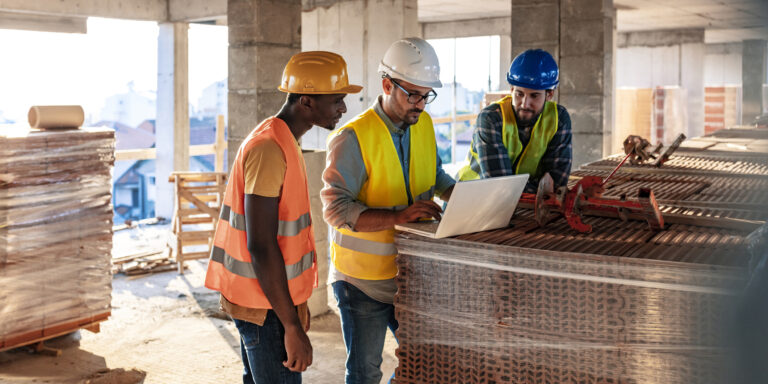
Every construction project begins with the owner's vision, which is translated into drawings and specifications by the design team. A diverse team of contractors, subcontractors, vendors, and suppliers provide materials, equipment, and labour to bring the vision to life. With so many moving pieces and stakeholders involved, ensuring that the end result matches the design — and complies with regulatory requirements — can be a significant challenge.
While we all aspire to achieve quality in the Australian construction industry, it remains a persistent issue, with rework and defect rates both remaining stubbornly high. This is having a major impact on project profits, industry reputation, and the value end clients receive for their budget. Failing to achieve quality control in construction also blows out project timeframes and keeps researchers and regulators busy trying to understand how we can shift the dial.
Table of contents
What is Quality Control in Construction?
Quality control (QC) in construction refers to the processes, procedures, and standards implemented to ensure that the final product meets design specifications, regulatory requirements, and client expectations. QC focuses on preventing and correcting deficiencies in materials, methods, and workmanship to deliver a safe, durable, and functional building. It answers the critical question: "Is the work done correctly?"
Why is Construction Quality Control Important?
Quality control is crucial in construction for several reasons:
- Safety Compliance: Ensuring that buildings meet structural integrity standards reduces the risk of failure or hazards.
- Cost Efficiency: Rework, defects, and non-compliance can significantly inflate project costs.
- Reputation and Trust: High-quality construction enhances a company's reputation and fosters trust among clients and stakeholders.
- Regulatory Compliance: Adhering to codes like the National Construction Code (NCC) and Australian Standards (AS/NZ) is mandatory.
- Client Satisfaction: Delivering a project that meets or exceeds expectations improves long-term relationships and business success.
Difference Between Quality Control and Quality Assurance in Construction
While often used interchangeably, QC and QA (Quality Assurance) are distinct concepts:
Aspect | Quality Control (QC) | Quality Assurance (QA) |
Definition | Inspects and corrects work during construction | Prevents defects through proactive planning |
Focus | Detecting and fixing errors | Developing processes to avoid errors |
Timing | Happens during and after execution | Happens before execution |
Example | Checking concrete strength before pouring | Establishing concrete mix design standards |
Effective quality management requires both QC and QA working together to achieve optimal results.
5 Common Causes of Construction Quality Issues
Despite industry advancements, quality control remains a significant challenge. Several key factors contribute to poor quality in construction:
1. Time Constraints and Rushed Construction
Many projects operate under tight deadlines, leading to rushed work, skipped steps, and overlooked details. Design-build contract models often result in works packages being tendered based on preliminary designs, increasing the risk of poor constructability and quality struggles.
2. Prioritising Cost Over Quality
There has been a noticeable shift in construction practices, where affordability often takes precedence over longevity. Buildings constructed decades ago tend to exhibit superior durability compared to modern lightweight structures, which require precise detailing and high-quality workmanship to match older standards.
3. Material Substitutions and Product Quality Issues
Issues arise such as subcontractors may substitute lower-cost materials to cut expenses, impacting the overall quality, imported materials may lack proper certification or testing, leading to compliance risks. Or, poor documentation or unverified offshore engineering approvals can compromise safety and durability.
4. Lack of Attention to Detail in Construction Execution
Quality issues often arise due to: improper waterproofing and fire system installations, poorly sealed buildings, leading to inefficiencies in insulation and weatherproofing. Or, inconsistent quality in finishes and cabinetry.
5. Neglecting Post-Completion Quality Considerations
For many contractors, practical completion is the primary milestone, while long-term quality in occupancy is often an afterthought. Poorly executed sealing, inadequate finish work, and undetected defects may not qualify for warranty claims but significantly affect the building's usability and occupant satisfaction.
Everything's being engineered with cost in mind rather than with longevity in mind, short-term cost savings are prioritised over the long-term durability and quality of buildings. If you go back to...the forties, fifties and sixties, brick houses were like bunkers...they're still standing today...But the rate at which newer properties that are being built are effectively becoming defective, or...wearing out is much faster than what it used to be.
Tom Proctor
Solutions Engineer, Enterprise
Procore
The Cost of Quality: An Investment, Not an Expense
Viewing quality control as an unnecessary expense is a common misconception. Instead, understanding the Cost of Quality (COQ) can help companies make informed decisions:
Preventative Costs (Upfront Investments)
- Additional inspections and quality checks
- Enhanced procurement and material vetting
- More time allocated for design coordination and planning
Failure Costs (Consequences of Poor Quality)
- Expensive rework and project delays
- Higher warranty and callback costs
- Increased legal and reputational risks
Industry data suggests that rework alone can account for 2% to 20% of project budgets. Prioritising quality control from the outset can significantly reduce these hidden costs.
Fostering a Culture of Quality in Construction
Achieving better quality in construction requires an industry-wide cultural shift. Just as safety has become a shared responsibility across all stakeholders, quality must also be embedded as a collective priority.
- Clients and Designers should ensure that constructability and durability are factored into designs.
- Builders and Contractors must emphasise stringent quality checks and skilled workmanship.
- Suppliers and Subcontractors should commit to using compliant, high-quality materials.
By integrating quality control into every phase of construction, from design to post-occupancy, the industry can deliver safer, more durable, and higher-value buildings for the future.
Quality is the foundation of long-term success.
Quality control in construction is not just about ticking compliance boxes—it’s about ensuring excellence, reducing costly rework, and improving industry reputation. By investing in robust QC processes, the construction sector can build not only better structures but a stronger foundation for long-term success.
Categories:
Tags:
Written by
Tom Proctor
Before joining the world of technology, Tom worked as a Contract Administrator. This hands-on experience gives him a unique perspective that he leverages in his current role at Procore, where he has been for the past two years. Tom is passionate about helping construction businesses understand best practices in project management solutions. He helps construction businesses understand best practices around project management solutions and the many benefits they can provide.
View profileExplore more helpful resources
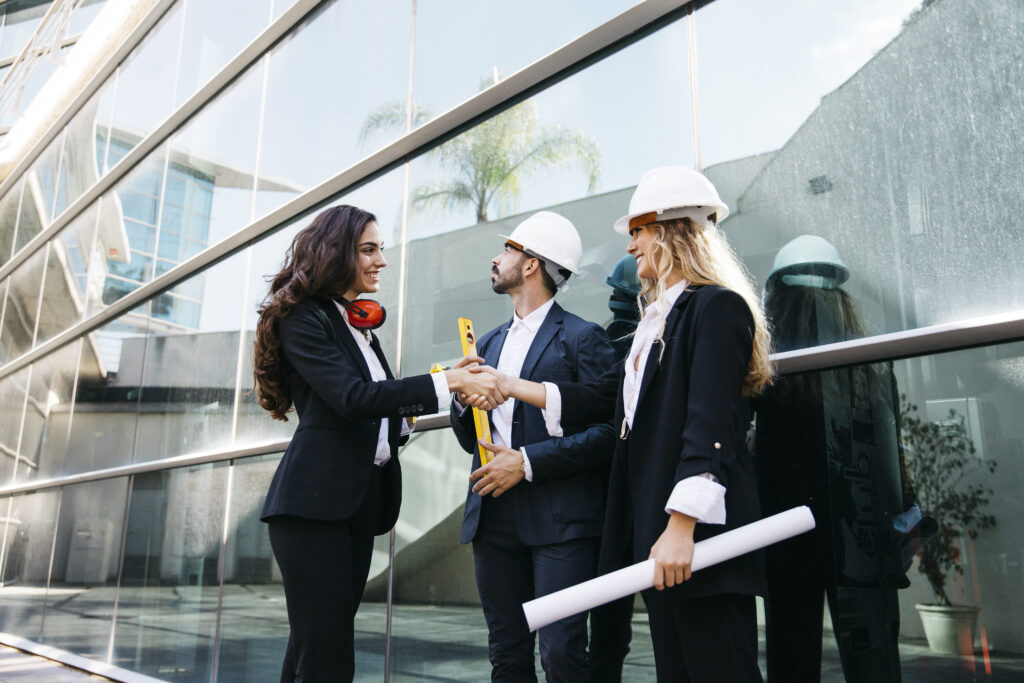
Construction Handover: The Keys to a Smooth and Successful Transition
Project handover should be a seamless transition, but its success is determined long before the last walkthrough. When teams consistently align on design, timelines, and quality, and support that alignment...
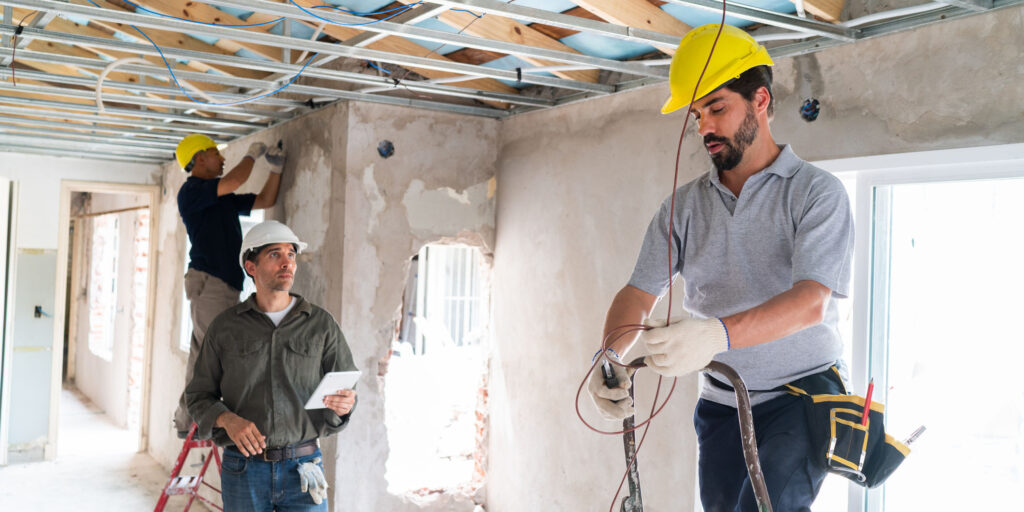
Cutting Delays and Costs: Proven Ways to Boost Construction Site Efficiency
On-site efficiency separates profitable construction projects from those plagued by delays and budget overruns. In Australia’s construction landscape—where supply chain disruptions, skilled labour shortages, and increasingly strict regulations are the...
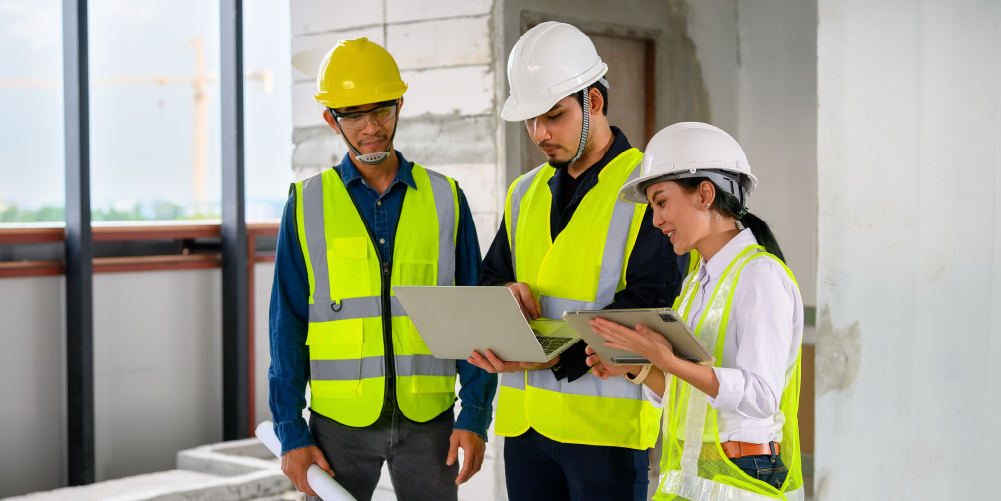
Why Communication is the Hidden Risk Factor in Construction
Construction is a high-risk industry—not just financially, but physically and reputationally. While significant effort goes into mitigating physical hazards, ensuring financial control, and protecting contractual interests, one of the biggest...

Data Centre Construction: Building the Cloud
As the demand for digital data increases, so does the demand for the physical structures and equipment needed to store and process data. Data centres are facilities that house computer systems...