— 6 min read
Bridging the Gap Between Promised and Delivered Quality with AI
Last Updated Feb 17, 2025
Last Updated Feb 17, 2025

One of the biggest challenges in construction is the gap between promised quality and actual delivery. Rework, defects, and warranty callbacks continue to erode already slim margins—damaging reputations and creating costly disputes.
For decades, construction firms have collected massive amounts of project data—on budgets, timelines, materials, workmanship, and defects. But most of this data is only reviewed in hindsight, meaning valuable lessons are often lost once a project is completed. Without full visibility into patterns, risks, and improvement opportunities, the same issues resurface, driving higher costs and lower quality.
What if past project data could be used to predict and prevent defects before they occur? What if construction teams could pinpoint risks in real time, ensuring fewer callbacks, lower costs, and stronger financial performance?
This is where Artificial Intelligence (AI) is changing the game. By analysing vast amounts of construction data, AI can identify risks before they become costly problems, helping teams improve quality, safety, and environmental performance—all at once. AI-powered tools are already proving valuable in tackling some of Australia’s biggest construction challenges, such as waterproofing defects, which often emerge long after project completion but carry severe financial and reputational consequences. As AI-driven analytics become more accessible, firms that adopt them will gain a competitive edge, using real-time insights to win more bids, reduce risk, and strengthen client relationships. Those that don’t will find themselves competing against builders who can prove their quality through data-driven evidence.
Selecting a builder is no longer just about experience—it's about verifiable quality. Look for construction firms that embrace AI-driven analytics to prove their commitment to excellence. The right builder should be able to demonstrate their capabilities through data, showing how they predict and prevent defects, reduce rework, and maintain high safety standards. By choosing a builder who leverages AI, you're investing in a project that benefits from foresight, data-driven decisions, and a dedication to superior outcomes.
Tom Proctor
Solutions Engineer, Enterprise
Procore
Table of contents
Measuring and Managing Quality More Effectively
For AI to truly enhance quality and reputation in construction, it must be grounded in data-driven decision-making. Yet, many firms still rely on outdated measurement methods that only highlight issues after they’ve become costly. Traditional quality management is reactive rather than proactive, meaning defects, rework, and safety concerns aren’t addressed until after they’ve impacted timelines, budgets, and client relationships.
AI changes this by shifting quality control from hindsight to foresight. By analysing vast amounts of project data, AI can connect leading indicators (predictive measures) and lagging indicators (historical performance) to spot risks before they escalate.
- Leading indicators help predict and prevent problems, tracking rework rates, budget adherence, and safety benchmarks.
- Lagging indicators—such as defect claims, project profitability, and lost-time injury rates—are often reviewed too late to influence ongoing projects.
AI fundamentally changes how we approach quality in construction. Instead of relying on lagging indicators like defect claims and project profitability, which tell us about problems after they've already impacted the project, AI empowers us to focus on leading indicators. Imagine AI analysing real-time data on rework rates, budget adherence, and safety benchmarks to predict and prevent defects before they occur.
Tom Proctor
Solutions Engineer, Enterprise
Procore
AI doesn’t just analyse these metrics individually—it connects the dots, uncovering patterns that would otherwise be missed. Instead of reacting after defects arise, construction teams can forecast risks, adjust workflows, and improve long-term performance.
Breaking Down Silos: Integrating Quality, Safety, and Environmental Performance
Even firms with Integrated Management Systems (IMS) for Health, Safety, Environment, and Quality (HSEQ) often struggle with siloed reporting. These divisions make it harder to see the connections between safety, quality, and environmental outcomes.
This fragmented approach creates inefficiencies and blinds teams to key insights, such as:
- How safety incidents correlate with quality defects (e.g., rushed work leading to mistakes).
- How environmental risks align with rework issues (e.g., material degradation due to weather exposure).
- How quality failures impact long-term financial performance (e.g., callbacks and liability claims).
By integrating these datasets, AI helps construction teams make smarter, more holistic decisions about project execution.
AI in Action: How Transferable Analytics Improve Project Outcomes
AI’s ability to recognise patterns and predict trends is transforming construction quality. Consider how this applies to health and safety data:
- Traditional safety reports capture near-misses and Safe Work Method Statements (SWMS)—but they often aren’t analysed across projects.
- AI can identify recurring safety risks and benchmark trends across multiple sites.
These same analytics can be applied to quality management, pinpointing where poor workmanship, materials, or methods lead to costly rework and defects.
By structuring and analysing vast amounts of project data, AI provides clear, evidence-based recommendations for improving quality control.
Waterproofing Defects and AI-Driven Prevention
Post-construction data is invaluable, especially for issues that only surface well after completion—such as waterproofing failures.
Water leaks are one of the most common defects in Australian residential construction. They often lead to:
Mould growth (a safety hazard)
Structural damage (a quality issue)
Costly rectifications (a financial burden)
AI can help by:
- Tracking patterns in waterproofing failures across projects.
- Analysing correlations between construction methods, material choices, and defect rates.
- Identifying early warning signs before issues escalate.
- Providing actionable insights to improve training, quality assurance, and contractor selection.
By proactively addressing these defects, construction teams can significantly reduce warranty callbacks and liability claims—while protecting their reputation.
Imagine using AI to analyse data from past projects to predict waterproofing failures before they happen.. Instead of reacting to leaks and mold growth after construction, AI can identify correlations between construction methods, material choices, and defect rates. This proactive approach not only reduces costly rectifications and liability claims, but also safeguards the builder's reputation by ensuring higher quality outcomes from the start.
Tom Proctor
Solutions Engineer, Enterprise
Procore
AI-Powered Tools for Construction Quality
AI-enabled tools are transforming how construction firms analyse project data, identifying risks and trends across multiple sites. These technologies help centralise quality management and enhance decision-making with key capabilities such as:
- Data Dashboards – Aggregate and visualise quality, safety, and cost data in real time for better reporting and trend analysis.
- AI-Driven Risk Registers – Predict potential quality risks by analysing patterns in project data, similar to how traditional risk registers assess safety and financial concerns.
- Automated Benchmarking – Compare defect rates and project performance against industry standards, ensuring continuous improvement and competitiveness.
To fully realise the potential of AI in construction, the right software is essential to transform raw data into actionable intelligence. With the right tools, AI can identify risks and trends across projects but this involves moving beyond traditional methods of data capture to tools that can predict quality risks, automate benchmarking against industry standards, and centralise quality, safety, and cost data for improved reporting.
Tom Proctor
Solutions Engineer, Enterprise
Procore
Rather than relying on manual reporting, AI continuously scans past and current project data, flagging recurring issues and anticipating risks—offering a more proactive and efficient approach to quality management.
The Future of AI in Construction: A Competitive Advantage
The construction industry is becoming increasingly data-driven, and AI is the key to transforming scattered project insights into meaningful, actionable intelligence. Builders who delay adoption may soon find themselves at a disadvantage, as clients and regulators are already using AI insights to benchmark contractor performance.
Proactive risk management – Identifies quality concerns before they become costly.
Reputation protection – Reduces defects, warranty claims, and negative client experiences.
Competitive advantage – Enables builders to demonstrate superior quality and safety performance. By integrating AI-driven analytics into quality management, construction firms can:
- Reduce rework and defects
- Improve project margins
- Strengthen their reputation for excellence
- Gain a competitive edge in a changing market
The real question is: Will your company use AI to lead the industry—or struggle to keep up?
Categories:
Tags:
Written by
Tom Proctor
Before joining the world of technology, Tom worked as a Contract Administrator. This hands-on experience gives him a unique perspective that he leverages in his current role at Procore, where he has been for the past two years. Tom is passionate about helping construction businesses understand best practices in project management solutions. He helps construction businesses understand best practices around project management solutions and the many benefits they can provide.
View profileReviewed by
Samantha Nemeny
9 articles
Sam—Samantha if she’s feeling particularly academic—has spent a decade in content marketing, with eight years focused on Australia’s construction industry. She has a knack for making complex ideas easy to understand, turning industry jargon into clear, engaging stories. With a background in SEO and marketing, she’s spent the past three years at Procore, helping industry professionals navigate the world of construction with content that’s both insightful and easy to digest.
View profileExplore more helpful resources
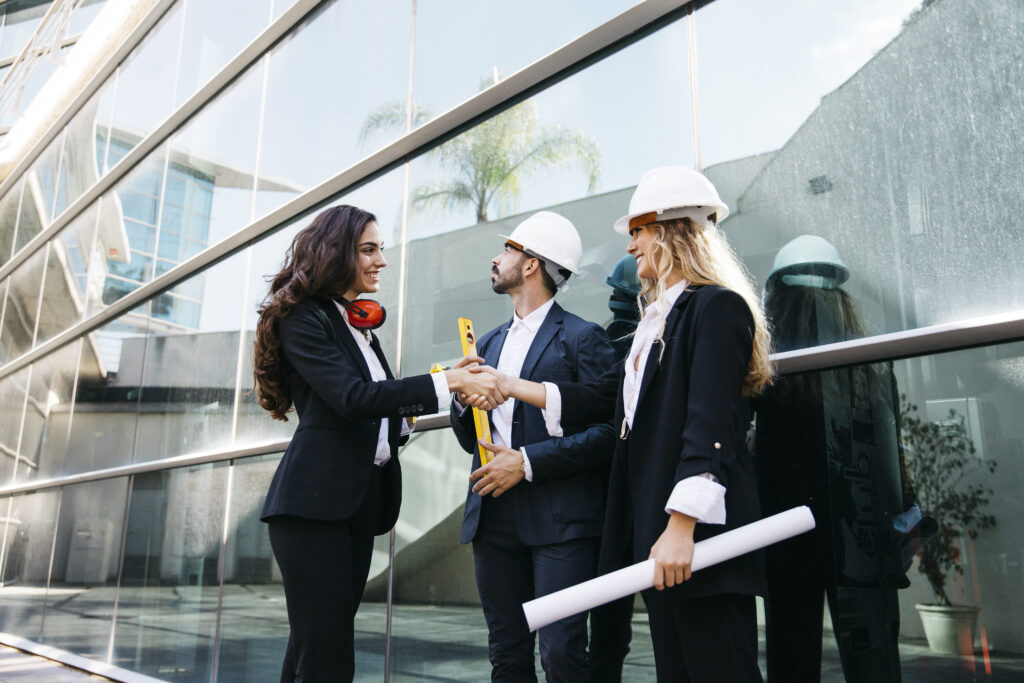
Construction Handover: The Keys to a Smooth and Successful Transition
Project handover should be a seamless transition, but its success is determined long before the last walkthrough. When teams consistently align on design, timelines, and quality, and support that alignment...
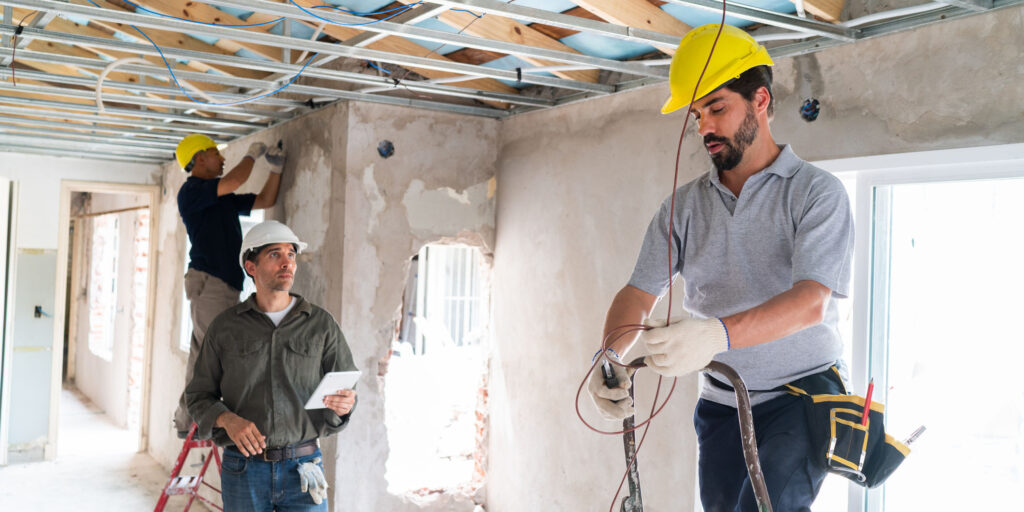
Cutting Delays and Costs: Proven Ways to Boost Construction Site Efficiency
On-site efficiency separates profitable construction projects from those plagued by delays and budget overruns. In Australia’s construction landscape—where supply chain disruptions, skilled labour shortages, and increasingly strict regulations are the...
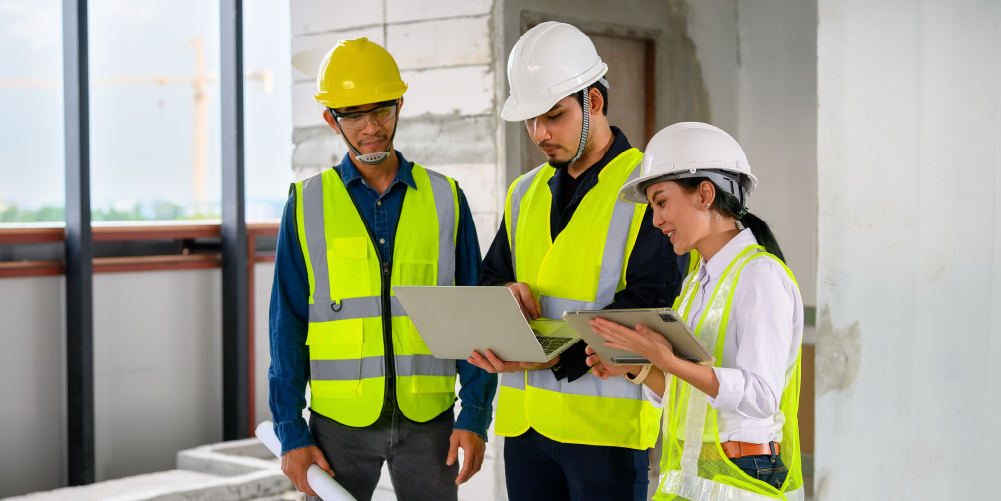
Why Communication is the Hidden Risk Factor in Construction
Construction is a high-risk industry—not just financially, but physically and reputationally. While significant effort goes into mitigating physical hazards, ensuring financial control, and protecting contractual interests, one of the biggest...

Data Centre Construction: Building the Cloud
As the demand for digital data increases, so does the demand for the physical structures and equipment needed to store and process data. Data centres are facilities that house computer systems...