— 8 min read
Shop Drawings: The Blueprint for Accuracy in Construction
Last Updated Dec 15, 2024
Last Updated Dec 15, 2024
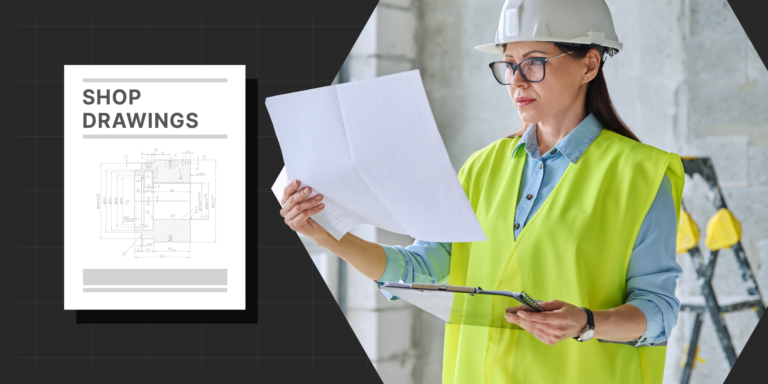
Shop drawings are a blueprint that turns designs into tangible results, acting as a bridge between architects, engineers, consultants and subcontractors. They are essential for upholding quality control, maintaining material specifications and adhering to regulatory standards when constructing a project. Without the detailed guidance shop drawings provide, essential elements can be missed, leading to inefficiencies and errors during a project's build.
Table of contents
What Are Shop Drawings?
Shop drawings are detailed drawings showing how construction components are fabricated, assembled and installed. Shop drawings can be a combination of drawings, 3D models or exploded diagrams combined with text detailing the materials, finishes, dimensions, and installation processes. They act as a visual guide for manufacturers and tradespeople, ensuring sections are buildable and accurately installed.
Who Creates Shop Drawings?
Shop drawings are drawn up by subcontractors, their fabricators and vendors who create specific systems or project components. They are reviewed and approved by the architect and engineer before beginning work on site. Occasionally, the client or building landlord may need to sign off on the shop drawings if they impact the building's systems.
The Role and Importance of Shop Drawings in Construction
Shop drawings inform the fabrication process and ensure all components fit together as intended. They provide the intricate details down to the exact size, installation details and final finishes. Throughout a project, shop drawings are primarily used by subcontractors to guide the installation of the project specific to them.
Without the level of detail shop drawings provide, subcontractors are more vulnerable to errors that can compromise project success. If a high-quality finish is required or the project has complex systems, shop drawings play a pivotal role in the success of a project.
Shop drawings are essentially very detailed drawings of how something will be made, fabricated or installed. It's kind of getting into the nitty gritty of how the finished product will end up on-site. Higher-risk projects are going to have shop drawings because you want to make sure everyone is on the same page and is building towards the same thing.
For example, projects with joinery or complex service requirements such as HVAC, mechanical, cladding or fire suppression systems will require shop drawings to ensure proper installation.
Emma De Francesco
Strategic Product Consultant
Procore
Common Challenges in Creating Shop Drawings
Below are the most common challenges with creation of shop drawings, and their implications:
Pro Tip
Always work with an experienced contractor. They'll know the buildability of a project from the outset, and the availability of equipment or materials, ensuring the design proposed can be built as planned with the intended materials and equipment.
1. Buildability issues
Some designs may not be practical or feasible to construct as initially envisioned. Challenges often emerge when shop drawings fail to account for the physical realities of construction, such as site constraints, material limitations, or assembly methods. If left unaddressed, these issues can lead to costly revisions or project delays.
2. Time Constraints
Shop drawings often need to be developed within tight timelines. Insufficient time for detailed reviews can result in errors or omissions, which can cascade into larger problems during fabrication and installation. Additionally, rushed shop drawings can compromise quality and lead to rework later in the project.
3. Long Lead Times for Materials and Equipment
Delays in sourcing specific materials or equipment can disrupt project schedules. If shop drawings are not aligned with lead times or availability, procurement issues may arise, potentially stalling construction activities.
4. Outdated or Incomplete Drawings
Using outdated or incomplete shop drawings can result in misaligned expectations and installation errors. For example, if site measurements have changed but the drawings do not reflect those updates, the installation may fail or require adjustments. This highlights the importance of maintaining up-to-date information on measurements, materials, and methods.
5. Miscommunication Among Stakeholders
Without clear communication channels, different teams may interpret shop drawings inconsistently. This can result in deviations from the design intent, coordination failures, or project delays. A lack of centralised access to updated drawings exacerbates this problem, leaving stakeholders out of sync.
Addressing these challenges early in the process is critical for maintaining efficiency and avoiding costly disruptions during construction.
Best Practices for Creating Shop Drawings
Implementing effective strategies in the creation of shop drawings can help streamline fabrication and installation. Below are three essential practices to enhance collaboration and project outcomes:
In the past, limited licenses made it hard for everyone to see what was going on, leaving the leading hand to control the workflow. Now, with broader access, everyone can see the drawings, understand what needs to happen, and take more ownership of their work.
Emma De Francesco
Strategic Product Consultant
Procore
Pro Tip
Early contractor engagement helps prevent issues such as delays in procuring equipment or finishes, which are common when insufficient time is allocated for planning and coordination.
Use a centralised system.
A single, centralised system gives stakeholders a unified platform for accessing project information. This ensures everyone is working from the same up-to-date set of drawings, reducing errors and enhancing communication.
Establish a clear approval process.
Define stakeholder responsibilities and timelines for workflow approval. Clear processes ensure that everyone understands their role and avoids delays caused by uncertainty or miscommunication.
Engage contractors early.
Involving contractors early in the design process helps bridge the gap between design intent and practical execution. Contractors can provide valuable insights into buildability, material availability, and lead times. This proactive approach minimises revisions, reduces delays, and ensures the design can be constructed as planned.
Shop Drawing Requirements
In Australia, there are International Organisation for Standardisation (ISO) standards and Australian standards that must be followed. This ensures that buildings and projects are compliant with global and local standards to maintain consistency and safety regulations. The level of detail shop drawings require is dependent on the complexity of the project and its specific compliance regulations. For example, HVAC systems or high-risk projects may require more details to adhere to safety standards and authority requirements.
Examples of Shop Drawings
Shop Drawings vs. Design Drawings
Design drawings, also known as tender drawings or consultant drawings, are visual design drawings of a project. They are initially proposed by the architect and engineer as part of the construction tendering process and serve as a base for shop drawings. The primary difference between shop drawings and design drawings is the level of detail used and its intent.
The level of detail and the intent of the drawing is the key difference between a shop drawing and a design drawing. For example, a design drawing for an HVAC system will show the product specifications and location whereas the shop drawing will detail exactly how equipment connects together, ancillary equipment specification and accommodate specific site measures.
Emma De Francesco
Strategic Product Consultant
Procore
Shop Drawings vs. Construction Drawings
Construction drawings are high-level visual drawings that guide the overall construction project and are approved by a consultant as buildable. They are referenced by all stakeholders. Shop drawings, on the other hand, are used by a specific subcontractor and offer greater detail of individual components.
A construction drawing will never really say how we're going to build something. It's just saying what we're going to build.
Shop Drawings vs. As-Built Drawings
As-built drawings document the final installation and are a record of what has been installed and where it is located. Unlike shop drawings, which guide installation, they are created as part of the final sign-off documentation for the client and contractor once a project is completed. As-built drawings are important for maintenance, future renovations and ensuring the project has been completed according to the proposal.
Type | Creator | Focus | Timing |
Shop Drawings | Fabricators/ Subcontractors | Component-level details. E.g Custom fabrication specs for a metal staircase. | Before Fabrication/ During Construction |
Design Drawings | Architects/Engineers | Conceptual and schematic. E.g. Visualising the building layout. | Pre-construction |
Construction Drawings | Architects/Engineers/Consultants | Execution-level details. E.g. Guiding contractors on overall building steps. | During construction |
As-Built Drawings | Contractors/Building Owners | Actual built structure. E.g. Documenting changes for future use or maintenance. | Post-construction |
How Technology is Improving Shop Drawings
Integrating technology into shop drawings has greatly improved efficiency and accuracy. Tools like building information modelling (BIM) and computer-aided design (CAD) such as AutoCad, Otherbin software or Solowerks offer 3D modelling and exploded diagrams, making it easier to visualise complex projects.
The type of technology used to create shop drawings is dependent on the intricacy and level of detail required. For example, HVAC systems may require 3D modelling or exploded diagrams to depict how each section fits into one another. As a result, the tools or systems used to create the shop drawings will differ depending on the project and the subcontractor's knowledge.
The detail of the shop drawing depends on the project's complexity and the subcontractor's sophistication. More complex projects require more advanced subcontractors, as some may not be familiar with 3D drawings, while others use them daily.
Future Trends in Shop Drawings: Trends Shaping the Industry
As technology advances, how stakeholders collaborate and coordinate across a project will become more efficient and effective. Having one centralised system to view shop drawings and utilising AI-driven solutions for faster design integrations will streamline the creation and use of shop drawings in construction. Integrating automation and VR technologies into shop drawings, the more streamlined the processes will become. As the construction industry evolves, shop drawings will continue to advance with them, improving accuracy, efficiency and collaboration.
Automation will likely increase in these processes, with AI already helping to build layouts. It’s expected to extend to shop drawings, given the repetitive specs, and new tools, like VR visualisations, may emerge, along with new market players.
Categories:
Tags:
Written by
Emma De Francesco
18 articles
Emma is currently Strategic Product Consultant at Procore where she loves partnering with clients to help them achieve the best possible results. She has worked as a Project Manager in previous roles, responsible for overseeing small to medium-sized projects across various sectors including commercial, health and lifestyle, retail, government and hotels. Throughout these projects, she managed everything from project costs, program and quality & safety, to design management, procurement, and authority approvals.
View profileExplore more helpful resources
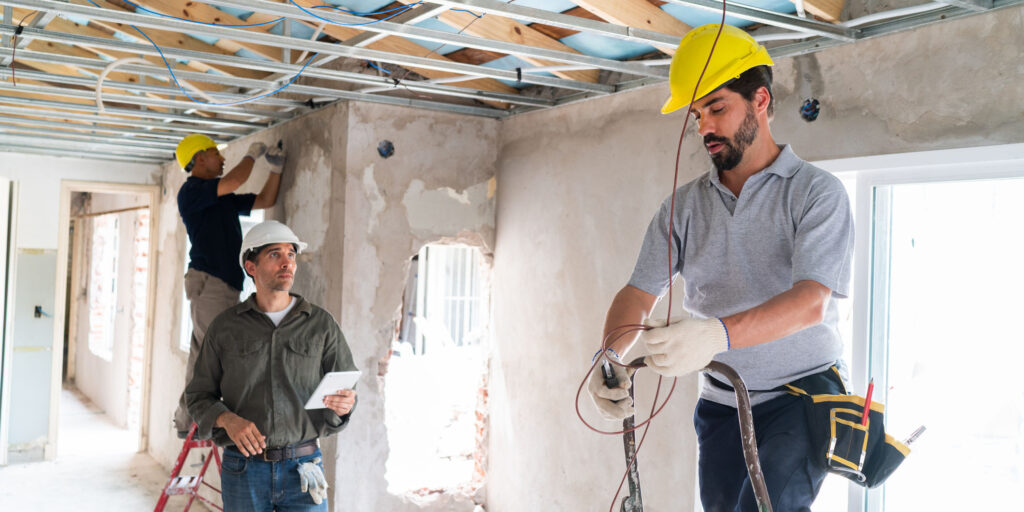
Cutting Delays and Costs: Proven Ways to Boost Construction Site Efficiency
On-site efficiency separates profitable construction projects from those plagued by delays and budget overruns. In Australia’s construction landscape—where supply chain disruptions, skilled labour shortages, and increasingly strict regulations are the...
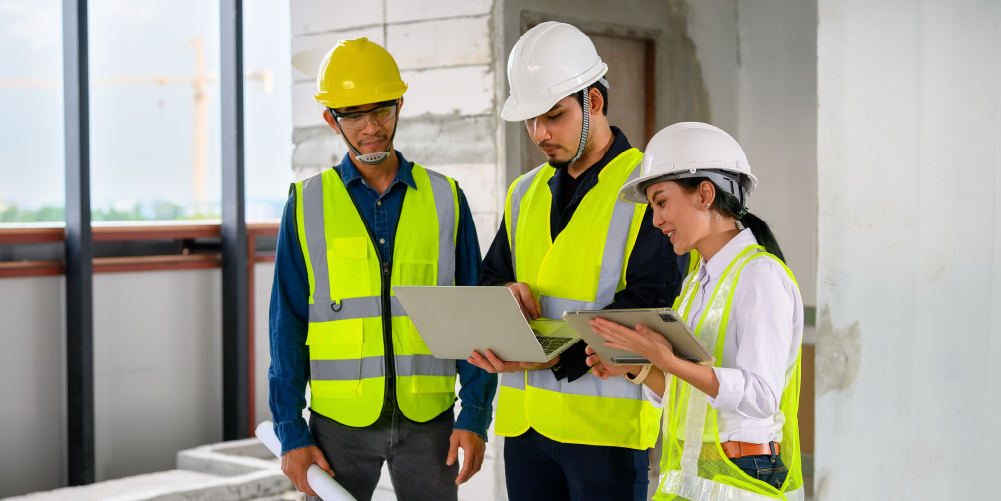
Why Communication is the Hidden Risk Factor in Construction
Construction is a high-risk industry—not just financially, but physically and reputationally. While significant effort goes into mitigating physical hazards, ensuring financial control, and protecting contractual interests, one of the biggest...

Data Centre Construction: Building the Cloud
As the demand for digital data increases, so does the demand for the physical structures and equipment needed to store and process data. Data centres are facilities that house computer systems...
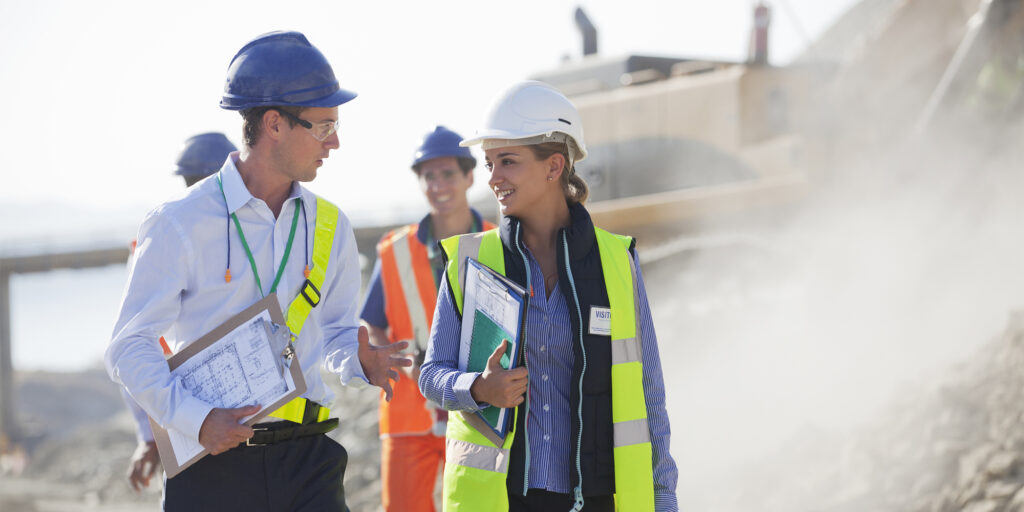
From Forming to Performing: Mastering Communication for a Winning Construction Culture
The way people communicate on a construction site is like the reinforcing steel in a slab—it holds everything together and strengthens the team. Clear, effective communication is essential for building...