— 7 min read
Understanding Building Specifications – Driving Project Success
Last Updated Feb 20, 2025
Last Updated Feb 20, 2025
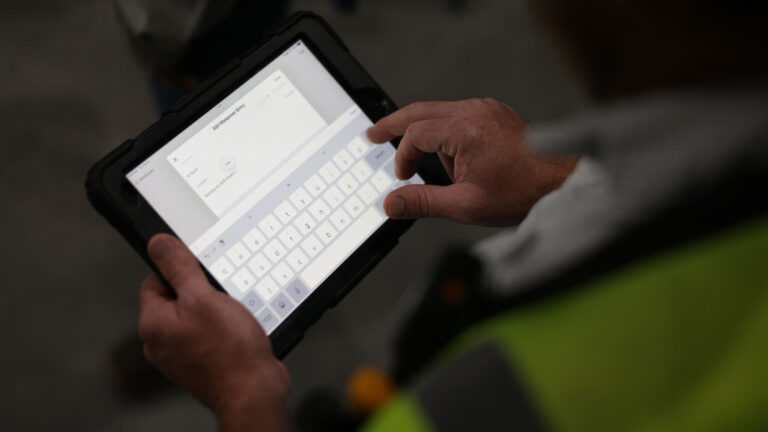
Building specifications are the crux of a construction project, capturing every critical detail and requirement that brings a project to life. As a key component of the initial contract agreement, they describe the materials, manufacturing details, specific processes and standards required to complete a build. Building specifications are used interchangeably with construction specifications and colloquially referred to as building specs.
This article covers the essentials of drafting construction specs, why they are important and expert tips for drafting them effectively.
Table of contents
How Building Specs Are Created
Building specs are drafted by an architect who outlines the materials, finishes, processes and standards required for a build. Once approved by the client, they will be handed to the builder to price it accordingly.
If the building specs are unclear or incomplete, the builder may submit a request for information (RFI) before pricing the labour and materials required to complete the job. This clears up any ambiguity and helps the builder correctly price the project.
Building specs focus on the materials, labour and methods required for a project while a bill of quantities (BOQ), lists the quantities and costs of the materials and labour. Together, they supply the blueprint for quality and cost control in any successful project.
Building specs are used across multiple stakeholders at all tiers of a company’s organisation, at varying stages of. Once the project has been signed off, the general contractor (GC) and project manager (PM) will work together to engage each subcontractor and tradesman and pass on the construction specs to them. Throughout the project, the GC will use the building specs to ensure quality checks and that everything is going to plan. If there are any changes to supply or methods, the GC and PM are responsible for keeping the building specs up to date.
Why Detailed Building Specifications Are Important
Increases efficiency in procurement and purchasing.
Access to the specs means that the GC and trades have a document to reference for any specific information they need when buying materials or doing finishes. The specs will lay out the exact requirements for the job and shared access will mean that less delays going back and forth to acquire information and waiting for a response.
Controls quality and compliance.
Detailed building specs help keep every aspect of a project up to regulatory standards, reducing the risk of liability and subpar work. While the specs provide guidelines to follow, they also are useful guardrails and a reference to crosscheck work as it is completed. By specifying exact requirements, there is little room for subcontractors to cut corners or choose a cheaper option as they are legally liable to uphold the agreement.
If the specs list out the material but do not specify how it needs to be installed, this can cause increased cost as installation methods and costs aren’t correctly accounted for.
Reduces risks and costs.
The more detailed building specs are, the more they support a project in reducing delays and cost blowouts. This is because if the building specifications outline the specific materials, processes and standards before beginning the build, they can be priced accordingly. Similarly, it also ensures that there is a document to cross-reference back to, ensuring proper installation. The more detailed the specifications, the clearer the project scope, which helps maintain timelines and budgets.
Enhances communication.
Building specs enhance communication as they see that what the design team and architects developed in the design phase is communicated clearly to the GC and subcontractors. This helps minimise errors and streamline operations as all stakeholders have a central source of information to refer back to.
Building specs provide detail and give everyone something to refer back to. It’s going to continue to have that overview that everyone has agreed to. We use a centralised documentation system to keep everyone on the same page on what materials, finishes, processes and labour are required to complete the job.
Mike Smith
Strategic Product Consultant
Procore
Types of Specifications
There are three components to building specs and each plays a key role in providing detailed requirements for a project. They are as follows:
Specification | Key Features |
Prescriptive specifications refer to which type of materials, specific material information, installation methods and finishes to use in the plan. | Specifies the materials to be used e.g. timber flooring or oak hardwood. Detailed descriptions of material types. Installation requirements. |
Proprietary specifications detail the specific supplier or material the architect and the client want. | Identifies suppliers or brands. Includes visual aids, such as images or catalogue numbers. Lists exact product names, paint colours, model numbers, or codes. Highlights manufacturer-recommended installation methods |
Performance specifications refer to the required performance and functionality of the end product in a project. | Defines functionality and performance expectations. Outlines performance testing and operational standards. Sets maintenance requirements. Specifies compliance with Australian Standards and/or the Building Code of Australia (BCA). |
Pro Tip
When writing building specs it is important to use clear language and keep it concise, this ensures there is no ambiguity surrounding what needs to be built. Categorising all elements of the build into sections and breaking them down into smaller categories ensures all aspects of the project are covered. It is also best practice to have regular meetings across stakeholders and update the construction specs of any changes that may occur.
It is best practice to use all three types of building specifications per material to help builders give an accurate initial cost proposal, keeping all stakeholders in agreement with the projected budget. E.g. To aid in correctly scoping a project, an architect can list the specific product or catalogue number they have in mind to the proprietary specifications.
The construction spec document must cover all the bases of a project’s materials, methods and installation processes. At a minimum, a material specification should have one type of the above specs. However, using a blend of these building specifications helps build out a comprehensive document that aligns the client's goals with the project capabilities, setting expectations around quality, cost and timelines.
Common Pitfalls when Producing Building Specs
- Using generic, incomplete specifications, or vagueness can lead to miscommunications and mistakes. For example, if an architect specifies marble but does not provide details on the product type or installation methods—such as the correct setting material—there’s a risk of damaging the marble during installation. Providing as much detail as possible is key to ensuring a project runs smoothly from start to finish.
- Relying on a general construction spec document without tailoring it to a specific job. Specs usually need to be tailored to the job. While there are occasions where using a templated, pre-created spec can help, it often results in irrelevant information in the spec document, adding unnecessary bulk. To avoid confusion and improve the process, it's always best to only keep what is relevant to the current project.
If you aren’t specific, you get prices that aren't reflective of the work needing to be done. So if something is unclear, ask! It is better to clarify something in the beginning than to wait till the project has begun.
Mike Smith
Strategic Product Consultant
Procore
Using Technology to Improve Specifications
In Australia, construction projects must adhere to a set of standards. This will be included as part of the performance specs. To ensure compliance across a project, architects can reference Natspec for information on Australian quality and assurance standards. This ensures consistency, safety and standards are upheld throughout a project.
To put the document together, utilising one central document or construction specification software will help stakeholders have a single source of truth to refer back to. This can help track any changes throughout the project, explaining delays or material changes. Additionally, as the building specs have become digitised, it allows teams to immediately access the specs on their phone or tablets-giving real-time updates, reducing errors and avoiding delays.
Detailed specifications drive project success.
Building specifications are the backbone of any successful construction project, providing the guide to what materials, processes and standards are required. When taking the time to provide clear and detailed specifications, construction specs provide a roadmap that aligns all stakeholders, reduces risks and keeps projects within budget. By implementing best practices and utilising the right tools, project teams can ensure quality across a project, minimising delays and having a seamless build from start to finish.
Categories:
Tags:
Written by
Mike Smith
Mike Smith is a Strategic Product Consultant at Procore, where he helps construction teams streamline processes and achieve project success through technology. With a career in construction spanning over 15 years, Mike has held key roles such as Project Manager, Scheduler, Project Controls Manager, and Field Engineer. His experience spans commercial fit-outs, residential projects, and industrial developments, giving him a well-rounded understanding of the industry's complexities. Originally from Florida, Mike has been based in Australia for the past nine years, bringing his expertise to a wide range of construction projects.
View profileExplore more helpful resources
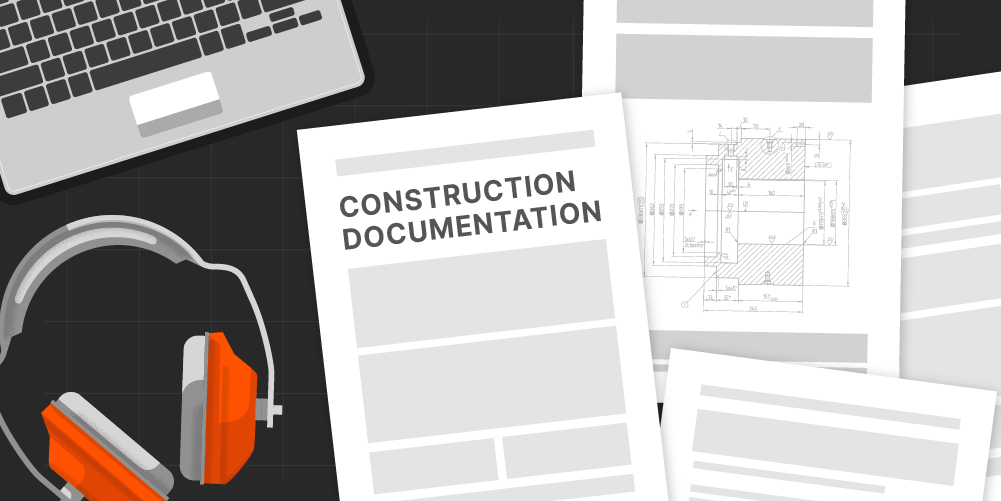
Document Control, Mastered: Blueprints, Binders & the Cloud
In construction, poor document control is more than a hassle—it’s a liability. Mismanaged documents can delay builds, drive up costs, and cause security and compliance issues. It’s a challenge facing...

Construction Progress Claims: Keeping Cash Flowing
In construction, steady cash flow is critical—and progress claims help make that possible. These claims enable staged payments based on work completed, rather than waiting until project completion. In this...
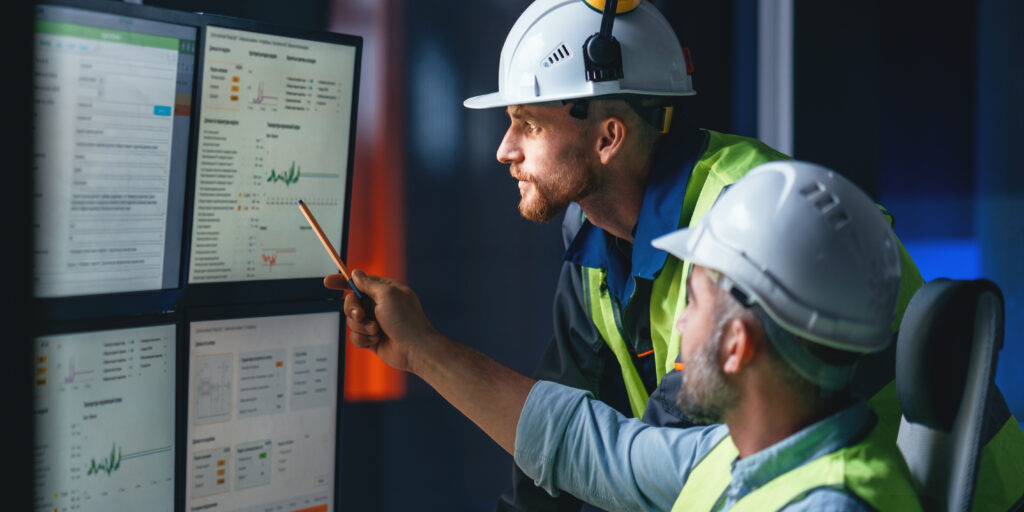
Construction Analytics: The Key to Smarter Decision-Making
Data is everywhere in construction—embedded in schedules, site activity logs, safety reports, and cost tracking tools. Yet despite the abundance of available information, many construction decisions still hinge on gut...

Construction Document Management: The Challenges and Benefits of Embracing a DMS
Every construction project begins, continues, and ends with a mountain of paperwork. From initial bidding documents to contractor agreements, blueprints, variation orders, inspection reports, on and on it goes. And...