— 9 min read
Value Engineering in Construction: A 6 Step Guide
Last Updated Dec 18, 2024
Last Updated Dec 18, 2024

In an industry under constant pressure to deliver on budgets, timelines and performance, Value Engineering (VE) has become a critical tool. More than simply cost-cutting, VE focuses on delivering smarter, innovative solutions that balance cost, utility and performance.
From early brainstorming to technologies like Building Information Modeling (BIM) and artificial intelligence, VE fosters collaboration and problem-solving to optimise resources without sacrificing quality.
Table of contents
The Basics of Value Engineering
Value Engineering isn’t just about saving money. First and foremost, it’s about standing back and asking what value means to your project both in the short and long-term. It then involves formulating a plan for achieving this in the smartest way possible, without cutting corners.
What is Value Engineering?
Value engineering (VE) is a systematic approach to balancing cost, utility and performance to maximise project value. Unlike cost-cutting, which sacrifices quality, VE ensures better outcomes by optimising resources, design and materials.
Components of Value Engineering: Cost, Utility, and Performance
Cost
Rather than focusing solely on upfront expenses, VE considers lifecycle costs—how much materials will cost to maintain and operate over time. For example, a slightly pricier, durable material might save significant maintenance costs long-term.
Utility
Utility ensures functionality without excess. Teams reassess project requirements to eliminate inefficiencies. For instance, redesigning slope stabilisation could prevent costly overengineering while delivering the same performance.
Performance
Performance ensures quality outcomes. VE helps projects meet safety and reliability standards efficiently without inflating costs.
Read more about Time Cost & Quality in Construction
The Value Engineering Process
Value Engineering follows a structured six phased approach.
1. Pre-Study Phase
Teams define the project’s scope, goals, and constraints. VE works best when there are strict parameters, so clear objectives at this early stage - whether that’s cost limits, performance needs, or timelines - will prevent wasted effort down the track
2. Information Phase
Gathering data, analysing project requirements and identifying where improvements are possible. Teams evaluate project components to uncover opportunities for optimisation. An example might include reviewing a project’s energy systems to identify more efficient alternatives.
3. Creative Phase
Here’s where the real brainstorming happens. The team generates alternative solutions to achieve the same (or better) performance at a lower cost. This phase encourages outside-the-box thinking, and requires the right mix of expertise. For instance, a structural engineer might see a smart design option that an architect working alone would miss.
4. Evaluation Phase
Each idea is assessed based on feasibility, cost savings and overall value. Again, collaboration is critical because you’re not just looking for savings—you’re weighing trade-offs across utility and performance, too.
5. Development Phase
Solutions are developed into actionable plans with detailed estimates, schedules and specifications. Teams present clear justifications for each recommendation.
6. Presentation Phase
Recommendations are presented to stakeholders, often as a detailed VE report. This ensures all parties understand the changes, benefits and rationale behind them
Roles and Responsibilities in Value Engineering
Value engineering (VE) is a collaborative effort requiring input from multiple stakeholders and construction teams, each of whom plays a distinct role.
Pro Tip
Communication breakdowns lead to half-baked solutions. Get everyone on the same page early on in the process, to keep VE focused and effective. This will also lead to:
- Better decisions: Teams align on goals and share insights.
- Fewer errors: Early communication prevents costly rework.
- Smarter solutions: Collaboration sparks creative, value-driven ideas.
Clients/Owners
- Role: Define the project's objectives, budget and constraints.
- Responsibilities: Provide a clear vision of what the project must achieve. Clients need to remain engaged throughout the VE process to review and approve recommendations.
- Why they matter: Owners ultimately determine the project’s priorities, such as whether to focus on upfront savings, lifecycle value or sustainability.
Designers/Architects
- Role: Develop the project’s conceptual design and technical plans.
- Responsibilities: Collaborate with other stakeholders to adjust designs based on VE recommendations, ensuring no compromise on the project’s vision or functionality.
- Why they matter: Designers ensure the project retains its integrity while incorporating cost-effective and innovative solutions.
Head contractors
- Role: Provide practical, construction-focused insights.
- Responsibilities: Evaluate material and method recommendations, assess feasibility and ensure the VE changes can be executed efficiently on-site.
- Why they matter: Contractors bring a boots-on-the-ground perspective, identifying practical opportunities for savings without sacrificing quality.
Value Engineering specialists
- Role: Lead the VE process and provide expertise in cost analysis, performance evaluation and alternative design solutions.
- Responsibilities: Analyse project components, suggest optimisations and ensure the team follows the VE methodology. Specialists often coordinate the brainstorming, evaluation and final reporting phases.
- Why they matter: Specialists drive the systematic approach needed to identify and prioritise value-enhancing opportunities.
Engineers (Structural, Civil, Mechanical, etc.)
- Role: Contribute technical expertise to assess the performance and feasibility of proposed solutions.
- Responsibilities: Validate design adjustments and ensure they meet performance and safety standards.
- Why they matter: Engineers ensure the VE recommendations are technically sound and comply with regulations.
Value Engineering Techniques and Tools
Value engineering (VE) uses a mix of proven techniques and modern tools to identify opportunities for improving value. These methods encourage creative solutions, informed decision-making and practical implementation.
Common Techniques
1. Function Analysis System Technique (FAST)
FAST diagrams break a project down into individual functions to clarify how each element contributes to the overall goal. By asking “How does this function work?” and “Why is it needed?” teams can identify where costs can be reduced or performance can be improved.
2. Brainstorming and idea generation
During the creative phase, teams collaborate to explore alternative solutions. Techniques like group brainstorming sessions help uncover opportunities that traditional methods might overlook.
3. Cost-Benefit analysis
This technique weighs the costs of proposed changes against their long-term benefits. VE teams focus not only on initial savings but also on lifecycle value, including maintenance, durability and sustainability.
Software and tools for value engineering
Modern tools play a key role in facilitating the VE process by streamlining analysis and collaboration.
Building Information Modeling (BIM)
BIM software allows teams to visualise designs in 3D and analyse how proposed changes will impact cost, performance and functionality. For instance, BIM can simulate alternative materials or structural adjustments to help identify the most cost-effective solution without compromising quality.
Cost estimation software
Detailed cost analysis is used for helping teams compare options and predict long-term savings.
Collaboration platforms
Platforms like Procore’s project management tools centralise communication, ensuring all stakeholders are aligned when evaluating VE recommendations.
Benefits of Value Engineering
Value engineering (VE) delivers significant benefits to construction projects, balancing cost, utility and performance to achieve better outcomes. These benefits can be both tangible—like cost savings—and intangible, such as improved collaboration and innovation.
Create more cost savings.
VE minimises unnecessary expenses by identifying smarter solutions early in the process. This includes reducing material costs, streamlining designs and lowering long-term maintenance expenses. For example, replacing traditional steel beams with lighter, prefabricated components might reduce costs without impacting structural integrity. VE prioritises long-term benefits over short-term gains. Teams consider lifecycle costs, so that the project remains cost-effective and durable long after completion.
Improve project efficiency.
By eliminating overengineering and optimising resources, VE keeps projects on track and within budget. This efficiency extends to scheduling, material use and workforce allocation.
Enhance collaboration.
VE fosters better communication among stakeholders. Early collaboration ensures that project goals are understood and innovative solutions are explored as a team.
Increase innovation.
By encouraging creative problem-solving, VE helps teams think outside the box and identify solutions that might otherwise be overlooked.
Reduce risk.
Early implementation of VE identifies potential design flaws or inefficiencies before they escalate into costly issues. This proactive approach minimises risks and improves overall project outcomes.
Common Challenges with Value Engineering
While value engineering (VE) offers significant benefits, it’s not without its challenges. Misconceptions, resistance to change and poor timing can limit its effectiveness and even derail a project.
1. Misconceptions about Value Engineering
As already discussed, one of the biggest hurdles for VE is the perception that it’s just another word for cost-cutting. However, when done properly, VE enhances value—it doesn’t just slash costs.
This misunderstanding can lead to resistance from stakeholders who fear compromises in quality, safety or performance. Educating teams on the true purpose of VE—achieving the best outcome for the project—helps overcome this resistance.
2. Integrating VE Into traditional construction processes
In construction, traditional processes can be rigid, with designs locked in early and changes seen as disruptions. Teams may resist revisiting designs, viewing it as an unnecessary delay or added complexity, so VE often requires a shift in mindset and workflow.
Successful VE relies on clear communication and buy-in from all stakeholders to ensure it’s seen as a proactive step, not an afterthought.
3. Late implementation
When VE is introduced late—during or after construction begins—its benefits shrink and challenges grow.
Late-stage VE leaves little room for creative problem-solving or exploring alternatives, and last-minute changes can disrupt schedules, creating frustration for teams and clients alike.
The future of Value Engineering in construction
Emerging trends, innovative technologies, and new approaches are shaping the way VE delivers value across projects
Sustainability and Green Construction
Increasing pressure to meet environmental targets is pushing VE toward sustainable solutions. VE now focuses on materials and designs that lower emissions, reduce waste and improve energy efficiency over a project’s lifecycle.
Modular and prefabricated construction
Prefabrication and modular techniques are revolutionising VE by streamlining processes and reducing both costs and timelines. Teams can identify efficiencies upfront and implement them in controlled factory environments.
Data-driven decision making
With the rise of digital tools, VE now relies heavily on data. Teams can use historical project data, simulations and predictive analytics to make more informed decisions.
Value engineering can shape the future of construction.
Value Engineering (VE) is no longer just a tool for managing costs—it's a forward-thinking approach that blends innovation, collaboration, and technology to maximise project value. By embedding VE early in the project lifecycle, teams can align on objectives, explore creative solutions, and balance cost, utility, and performance without compromising quality. The future of VE lies in sustainability, smarter technologies, and data-driven decision-making, ensuring that construction projects deliver long-term benefits for clients, communities, and the environment. By embracing VE, the construction industry can move beyond traditional cost-cutting and focus on creating smarter, more sustainable, and high-performing solutions.
Categories:
Tags:
Written by
Brendan McGurk
14 articles
"Brendan is a Strategic Product Consultant for Procore Financials, where he enjoys leading and innovating internal company processes to deliver on both public and private projects. He brings 12 years of experience working in various construction roles ranging from builder's hand to quantity surveyor and project manager on both the owner and main contractor side.
Originally studying Accounting, he changed direction to quantity surveying after the Christchurch Earthquake in 2011. He is now qualified and an NZIQS-recognised Quantity Surveyor. He’s since worked on projects from feasibility, concept design, and value engineering right through to construction and post-construction support.
Explore more helpful resources
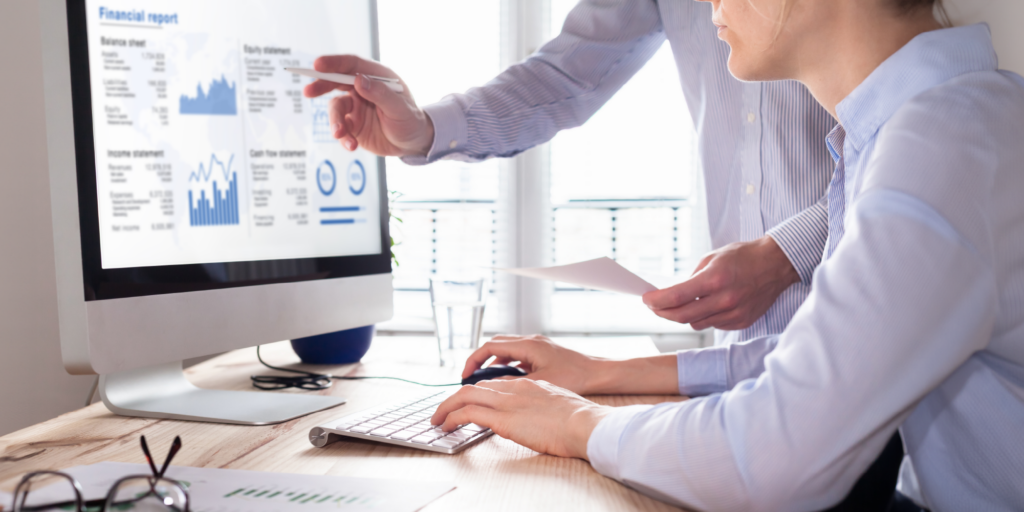
Cash Flow Forecasting in Construction: How to Stay Ahead of Funding Gaps and Protect Project Performance
Cash shortfalls are a leading cause of stalled projects, unpaid contractors, and budget blowouts in construction. Without a clear forecast of how cash will flow in and out over time,...
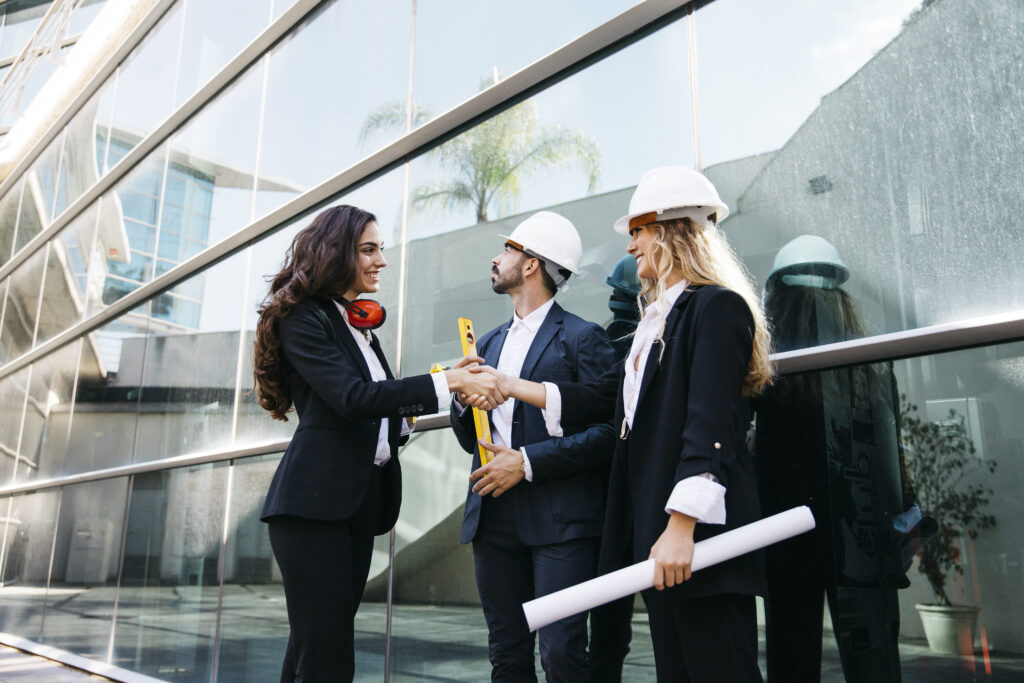
Construction Handover: The Keys to a Smooth and Successful Transition
Project handover should be a seamless transition, but its success is determined long before the last walkthrough. When teams consistently align on design, timelines, and quality, and support that alignment...
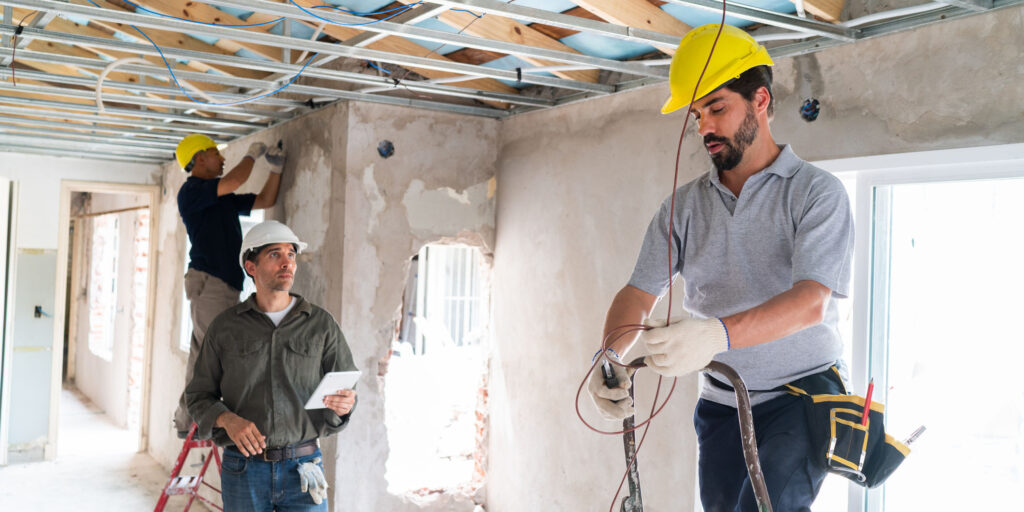
Cutting Delays and Costs: Proven Ways to Boost Construction Site Efficiency
On-site efficiency separates profitable construction projects from those plagued by delays and budget overruns. In Australia’s construction landscape—where supply chain disruptions, skilled labour shortages, and increasingly strict regulations are the...
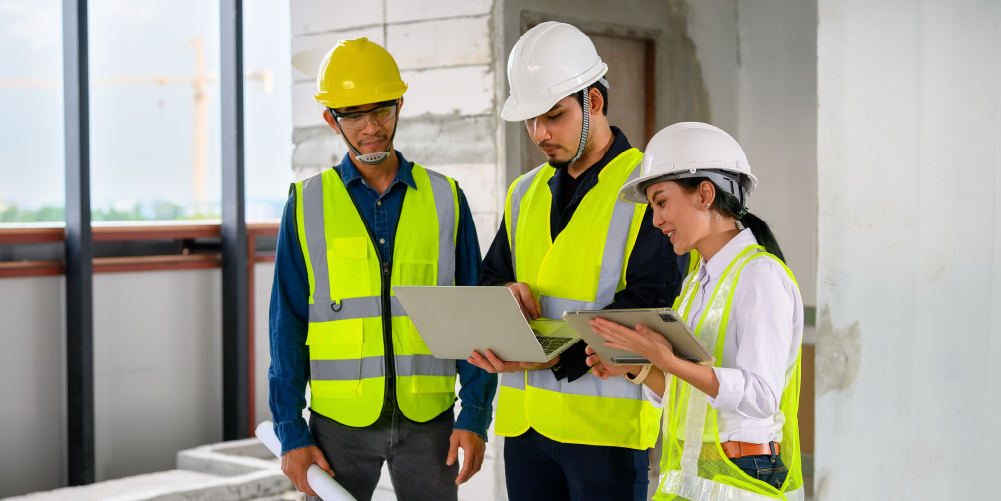
Why Communication is the Hidden Risk Factor in Construction
Construction is a high-risk industry—not just financially, but physically and reputationally. While significant effort goes into mitigating physical hazards, ensuring financial control, and protecting contractual interests, one of the biggest...