— 12 min read
Construction Planning: A Guide to Successful Project Execution
Last Updated Apr 16, 2025
Last Updated Apr 16, 2025
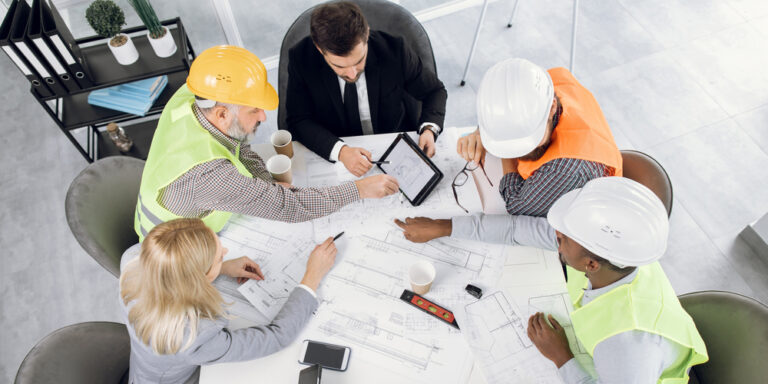
Every successful construction project begins long before the first brick is laid. Indeed, behind each structure - whether a towering skyscraper or complex infrastructure project - lies a carefully crafted construction plan. This construction roadmap outlines resources, timelines, risk management, and compliance requirements. Effective construction planning aligns materials, labour, and schedules, reducing inefficiencies and keeping projects on track.
Table of contents
What is Construction Planning?
Construction planning is the strategic process of defining, organising, and scheduling all project activities for efficient execution. Specifically, it encompasses resource management, budgeting, safety planning, and risk assessment - all necessary for keeping projects on schedule and within budget.
Why Construction Planning Matters
Projects that lack a structured plan often face serious challenges, including disorganised workflows, unexpected costs, and compliance issues. Creating a well-prepared construction plan helps to:
- Improve efficiency: Allocates resources (labour, materials, and equipment) effectively
- Reduce delays: Identifies potential bottlenecks early, preventing escalation
- Streamline safety and compliance: Integrates health and safety regulations, such as the Construction (Design and Management) Regulations CDM 2015, to prevent accidents
- Optimise costs: Prevents overspending through clear budget controls and contingencies
- Enhance risk management: Flags possible risks early, such as supply chain disruptions, labour shortages, or weather-related delays, implementing contingency measures before issues arise
Key Construction Plan Components
Essentially, the construction plan is the project roadmap, outlining everything needed for successful execution. It ensures that schedules, resources, safety protocols, and risk assessments are in place before work begins.
While no two construction plans are identical, core components typically include the following:
Project Overview
A high-level summary of the project's purpose and objectives, providing stakeholders with a clear understanding of what will be accomplished and the key deliverables expected.
Scope of Work
The scope defines what the project includes (and excludes), breaking it down into specific tasks, phases, and deliverables. A clear scope prevents miscommunication and scope creep.
Resource Requirements
Next, the plan identifies all labour, equipment, and material needs to complete the project efficiently, ensuring resources are allocated correctly and available when required.
Construction Schedule
Following resource planning comes a detailed project timeline, often using Gantt charts or scheduling software, that maps out key milestones and deadlines to help project managers anticipate delays and adjust workflows as needed.
Construction Budget
Accompanying the schedule is a comprehensive breakdown of estimated costs, funding sources, and contingency plans; proper budgeting provides financial stability and prevents unexpected expenses from derailing progress.
Architectural Drawings and Visual Plans
These critical documents include blueprints, CAD drawings, 3D renderings, and site layouts to guide project execution and help all teams stay aligned on design specifications.
Construction Specifications
Supporting the visual plans, this component outlines materials and technical requirements, prioritising quality control and compliance with building regulations for all aspects of construction.
Procurement Plan
This element defines the strategy for materials and subcontractors, detailing supplier timelines and contract terms to ensure all necessary resources are secured at the right time.
Quality Assurance and Control Plan
This component establishes standards, inspections, and testing procedures to ensure the project meets regulatory and contractual obligations throughout the construction process.
Change Management Plan
This section outlines how teams evaluate, approve, and implement project changes, such as design or budget modifications, to avoid delays and disputes.
Site Plan
An essential operational document that provides a detailed layout of site access, storage areas, and work zones, ensuring streamlined operations and minimal disruption to surrounding areas.
Safety Plan
This mandatory component addresses health and safety protocols in line with CDM 2015 (UK regulations), covering hazard identification, worker training, and emergency procedures.
Logistics Plan
Meanwhile, the logistics plan facilitates smooth material deliveries, equipment transport, and worker movement on site.
Traffic Management Plan
Related to logistics, this component outlines vehicle access and pedestrian safety measures to minimise disruption around the site.
Waste Management Plan
This section addresses waste disposal, recycling strategies, and environmental compliance, ensuring sustainability and regulatory adherence.
Communication Plan
This strategic element defines how stakeholders will handle updates, reports, and issue resolution between clients, contractors, and regulatory bodies to maintain transparency and coordination.
Risk Management Plan
This forward-looking component identifies potential risks, contingency measures, and crisis management strategies to secure project continuity should unexpected challenges arise.
Team Overview
Lastly, this overview lists personnel, responsibilities, and reporting structures, ensuring accountability and smooth coordination across all teams.
Effective Construction Planning: Key Steps
A well-structured construction plan also contains multiple interdependent variables. Breaking it down into a step-by-step process helps align all elements, including budgeting, scheduling, resource allocation, and safety planning. Here's a walkthrough of the seven key steps that successful project teams typically use:
Define Goals and Objectives
Before work begins, project stakeholders must establish clear, measurable goals that define what success looks like. These include:
Outlining the project scope - what the plan includes and excludes.
Setting key performance indicators (KPIs) to track project milestones.
Ensuring goals align with stakeholder expectations, licenses, regulations, and contractual obligations.Create Budget and Cost Controls
Next, establish a detailed, well-monitored budget to prevent financial overruns and effectively allocate resources. This step involves:
Estimating total project costs, including labour, materials, equipment, and contingencies.
Implementing cost control strategies, such as real-time expense tracking and financial forecasting tools.
Identifying potential financial risks, such as supply chain price fluctuations or unplanned delays.Develop Timeline and Schedule
Construction projects are notorious for delays, but designing (and following) a schedule helps reduce holdups and prepare for unforeseen disruptions. This involves:
Developing a structured timeline, often using Gantt charts, critical path method (CPM), or scheduling software.
Identifying key project milestones and setting realistic completion dates.
Factoring in potential delays due to weather conditions, inspections, or permit approvals.Plan Resource Management
Effective resource planning ensures everything required - from labour to heavy machinery - is available at the right time. This step requires:
Calculating the exact quantity of materials, workers, and equipment needed for each phase.
Coordinating with suppliers, subcontractors, and equipment rental providers.
Implementing inventory tracking to avoid shortages or excess stock.Define Tasks and Work Breakdown
Next, structuring a project into tasks facilitates better team coordination. This involves:
Creating a Work Breakdown Structure (WBS)- a hierarchical breakdown of all tasks.
Defining dependencies between tasks - which activities must be completed before others begin.
Assigning responsibilities to teams, subcontractors, and site managers.Establish Communication Protocols
With many different teams working on one project, good communication is also paramount. Construction managers should:
Establish formal reporting schedules to keep stakeholders informed.
Use document-sharing platforms and construction project management software to centralise all project updates.
Set up clear escalation procedures to resolve conflicts or unexpected challenges.Implement Safety Planning
Finally, safety is paramount in construction and must be factored into the planning process to protect workers and comply with regulations. This involves:
Conducting risk assessments for potential site hazards, including falls, equipment malfunctions, and fire hazards.
Developing emergency response protocols for on site accidents or environmental risks
Ensuring all workers receive proper safety training before work begins.
Complying with CDM 2015 regulations(necessary for UK construction projects), which require detailed safety planning before work begins.
Modern Construction Technologies
Technology is also transforming construction planning. As a result, methods like Building Information Modeling (BIM), AI-driven forecasting, and modular construction enhance accuracy and reduce risks throughout the planning process.
Building Information Modelling (BIM)
BIM technology enables construction teams to create 3D digital models of projects, offering a clearer visual representation of structures before construction begins. With BIM, planners can detect clashes, refine designs, and simulate project phases to improve coordination and reduce errors. This improves communication between architects, engineers, and contractors, ensuring accurate translation from design to execution.
AI and Predictive Analytics
Artificial intelligence increasingly integrates into construction planning and risk management. AI-powered tools can make data-driven decisions to predict potential issues - including delays, budget overruns, or material shortages - before they occur. By identifying risks early, teams can adjust schedules and optimise resource distribution in advance.
Drones and Site Monitoring
Drones are also becoming valuable tools for real-time construction site monitoring. Specifically, aerial surveys provide planners with detailed progress tracking, site inspections, and hazard detection. This improves site safety and documentation while helping project managers compare real-time progress with planned schedules.
Construction Management Software
Modern construction management software integrates project planning, document management, scheduling, and cost tracking into a single, centralised platform. Additionally, teams can share real-time updates, monitor budgets, and collaborate more effectively, enabling faster decision-making and reducing miscommunication.
Prefabrication and Modular Construction
Off site manufacturing techniques like prefabrication and modular construction help firms reduce on site delays and material waste. Also, by assembling structures in controlled environments before transporting them to site, project timelines can be optimised and labour costs lowered. This method works particularly well for large-scale infrastructure projects requiring fast deployment without compromising quality.
As construction becomes increasingly data-driven, firms that leverage digital tools gain a significant competitive advantage in the industry.
Planner vs. Project Manager: Roles and Responsibilities
Construction planners and project managers collaborate closely, and their responsibilities often overlap. However, clearly defining their roles from the outset improves accountability and efficiency.
Construction Planner Responsibilities
Construction planners focus on pre-construction, ensuring project schedules, resource allocations, and budgets are fully developed before work begins. Their key responsibilities include:
- Developing project schedules: Creating detailed timelines and Gantt charts to outline work sequences
- Estimating costs and resources: Forecasting labour, equipment, and material needs to prevent shortages or overspending
- Identifying risks and contingencies: Assessing potential delays, budget overruns, and supply chain risks, with backup plans
- Coordinating with architects and engineers: Ensuring design specifications align with scheduling and logistical constraints
- Creating procurement strategies: Managing the timing and sourcing of materials and subcontractor contracts
Project Manager Responsibilities
In contrast, construction project managers are responsible for the execution phase, implementing the plan effectively on site while adapting to real-world challenges. Their role involves:
- Managing day-to-day operations: Overseeing site activities, team coordination, and project milestones
- Solving jobsite challenges: Addressing unexpected delays, supply chain disruptions, or design adjustments
- Handling regulatory compliance: Verifying that health, safety, and environmental standards (such as CDM 2015) are met
- Controlling costs and budgets: Monitoring spending and adjusting financial plans as necessary
- Communicating with stakeholders: Keeping clients, contractors, and regulatory bodies updated on project progress
Key Differences Between Planners and Project Managers
Construction Planner | Project Manager | |
Main focus | Pre-construction strategy and planning | On site execution and project delivery |
Key responsibility | Developing schedules, budgets, and risk assessments | Managing teams, solving on site issues, and maintaining compliance |
Risk management | Identifies and mitigates risks before execution | Reacts to and resolves risks during execution |
Coordinates with | Architects, engineers, and procurement teams | Site supervisors, contractors, and regulatory bodies |
Decision-making | Focused on pre-emptive decisions to reduce risks | Focused on real-time decisions to address site issues |
Effective Risk Management in Construction
Construction projects are also inherently risky, with potential challenges ranging from budget overruns and supply chain delays to safety hazards and regulatory compliance issues.
Identifying Construction Risks
The first step in risk management is understanding where potential risks exist. This helps project planners develop strategies to minimise or eliminate them. Common construction risks include:
- Budget overruns
- Delays and scheduling issues
- Health and safety hazards
- Regulatory and compliance failures
- Design and engineering errors
Mitigating Construction Risks
Proactive risk mitigation strategies can significantly reduce costly disruptions. Construction planners can:
- Develop contingency plans: Allocate extra budget, secure alternative suppliers, or build buffer time for unexpected changes
- Use technology to predict risks: Apply AI-driven risk analysis to forecast potential budget overruns and scheduling conflicts
- Ensure regulatory compliance: Adhere to health and safety standards (such as CDM 2015) and environmental laws to avoid legal penalties and project shutdowns
- Implement robust contract and change management processes: Clearly define scope changes, contract clauses, and approval procedures to prevent disputes
- Improve communication and reporting: Utilise construction management software for real-time updates on potential risks and quick issue escalation
The Risk Assessment Process
In practice, a structured risk assessment can be broken down into four key steps:
Risk Identification
Documenting all potential risks that could affect the project.
Risk Analysis and Prioritisation
Assessing the likelihood and potential impact of each risk.
Developing Risk Response Strategies
Creating contingency plans and preventive actions.
Ongoing Monitoring and Control
Continuously tracking risks throughout the project lifecycle.
Ultimately, by integrating comprehensive risk management strategies, construction planners can protect their projects from unnecessary disruptions and financial losses.
Sample Construction Plan
While every construction project is unique, an effective construction plan follows a clear format, documenting all essential details. Below is an example of a construction plan layout, including key sections typically found in real-world projects:
Project Name: ABC Commercial Building Project
Project Location: London, UK
Client: ABC Property Group
Project Duration: 18 months
Project Budget: £12 million
Project Overview
This section briefly introduces the project, including its purpose, scope, and key objectives.
- Objective: Construct a 10-storey office building with sustainable design elements
- Key deliverables: Completed structure with full MEP (Mechanical, Electrical & Plumbing) installation and compliance with BREEAM sustainability standards
- Key stakeholders: Client, contractors, subcontractors, architects, regulatory authorities
Scope of Work
After defining the overall project, the scope of work clarifies what the project includes and excludes.
- Included: Site preparation, foundation work, superstructure, MEP systems, interior finishes, landscaping
- Not included: Tenant-specific interior fit-outs, post-completion maintenance
Resource Requirements
This section then outlines what is needed to execute the project successfully.
- Labour: Project manager, site supervisors, civil engineers, electricians, HVAC technicians, safety officers
- Materials: Concrete, steel beams, glass panels, insulation materials, plumbing fixtures
- Equipment: Cranes, excavators, scaffolding, concrete mixers
Construction Schedule (Gantt Chart Overview)
A high-level timeline of project phases and key milestones is essential to track progress.
Phase | Start Date | End Date | Duration |
Site Preparation | June 2025 | Aug 2025 | 3 months |
Foundation Work | Sept 2025 | Nov 2025 | 3 months |
Superstructure | Dec 2025 | May 2026 | 6 months |
MEP Installation | June 2026 | Sept 2026 | 4 months |
Interior Finishes | Oct 2026 | Jan 2027 | 4 months |
Final Inspection | Feb 2027 | March 2027 | 2 months |
Budget Breakdown
An effective construction plan should also include a detailed cost estimation to keep spending under control.
Category | Estimated Cost (£) |
Site Preparation | £1.2M |
Materials | £3.5M |
Labour | £4M |
Equipment Rental | £1.8M |
Compliance and Permits | £500K |
Contingency Fund | £1M |
Risk Management Plan
Following the budget, this section identifies potential risks and contingency measures.
- Potential Risk: Supply chain delays → Solution: Secure multiple suppliers
- Potential Risk: Unpredictable weather → Solution: Include buffer time in the schedule
- Potential Risk: Labour shortages → Solution: Pre-hire subcontractors with flexible scheduling
Safety Compliance Plan (CDM 2015)
This document then outlines the plan for site safety and compliance with regulations, which is mandatory for all construction projects.
- Health and Safety Measures: On site PPE requirements, daily safety briefings
- Emergency Preparedness: Fire escape routes, first-aid stations
- Legal Compliance: Full adherence to UK CDM 2015 regulations
Communication and Reporting Plan
Finally, creating a detailed plan encourages transparency and prevents miscommunication.
- Weekly Site Meetings: Contractors and site managers
- Bi-weekly Stakeholder Reports: Send to client and investors
- Emergency Escalation Contacts: Establish a clear protocol for urgent issues
Final Thoughts
Successful construction planning forms the foundation of every well-executed project. When teams carefully map out budgets, schedules, resources, and risks, they minimise delays and improve overall efficiency.
Technology-driven planning tools, AI forecasting, and BIM modeling give construction firms access to more accurate data and real-time collaboration features than ever before. Additionally, good planning strategies keep projects on schedule and within budget, delivering higher-quality results for clients and stakeholders.
Categories:
Preconstruction, Project Management, Safety and Compliance, Tech and Data
Tags:
Written by
Nicholas Dunbar
29 articles
Nick Dunbar oversees the creation and management of UK and Ireland educational content at Procore. Previously, he worked as a sustainability writer at the Building Research Establishment and served as a sustainability consultant within the built environment sector. Nick holds degrees in industrial sustainability and environmental sciences and lives in Camden, London.
View profileZoe Mullan
Zoe Mullan is an experienced content writer and editor with a background in marketing and communications in the e-learning sector. Zoe holds an MA in English Literature and History from the University of Glasgow and a PGDip in Journalism from the University of Strathclyde and lives in Northern Ireland.
View profileExplore more helpful resources

Construction Document Software: Essential Tools for Project Success
Construction projects depend on extensive paperwork, including designs, contracts, RFIs, and compliance records. A single misplaced document can trigger delays, disputes, or compliance violations. Despite increasing digital adoption, many teams...
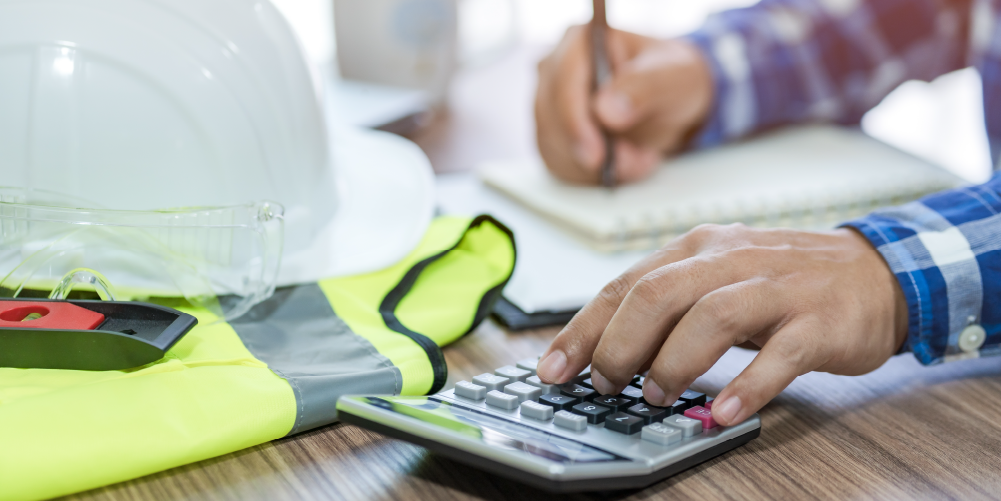
Leveraging Analytics for Better Financial Forecasting in Construction
Financial forecasting is a difficult task in any industry. In construction, where companies need to manage volatile material costs, labour shortages and variation orders on a daily basis, fluctuations in...
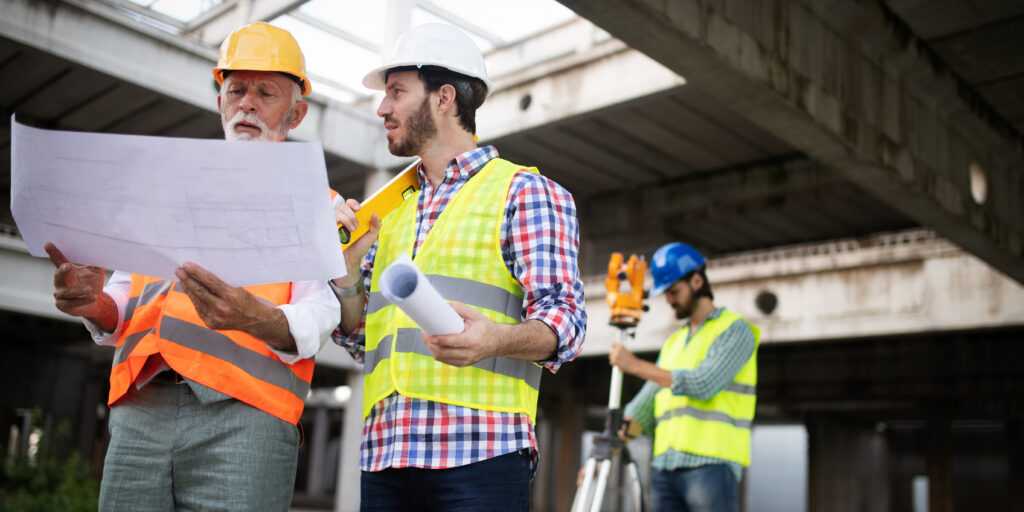
Strategies to Prevent Rework: The Importance of Clear Instructions
In construction, “rework” is the dreaded process of redoing tasks due to mistakes, quality issues, or safety concerns. This unnecessary work drains budgets through wasted materials and labour while causing...
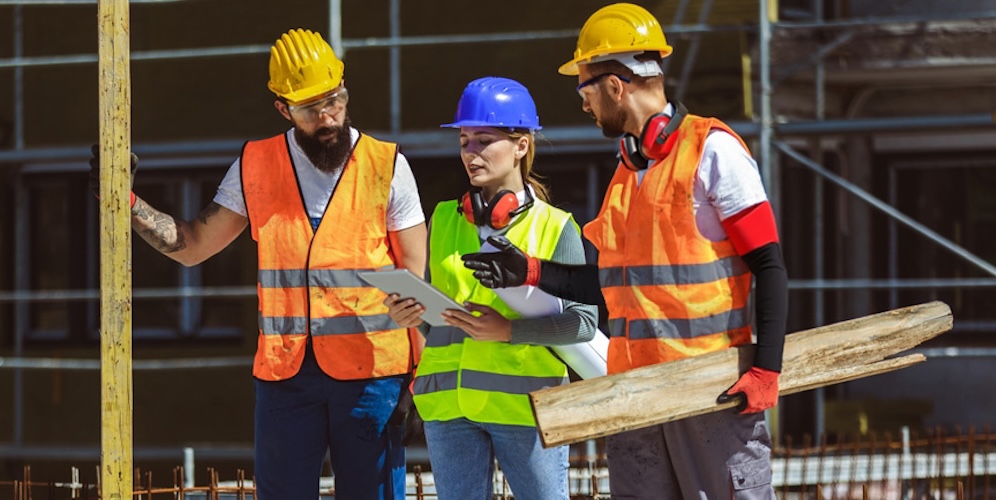
Building a Culture of Quality in Construction: How Safety Approaches Can Transform Quality
The UK construction industry faces persistent quality issues that compromise safety, inflate costs, and erode trust. Despite universal pursuit of excellence, high rates of rework and defects cost billions annually...