— 6 min read
Construction Specifications: The Blueprint for Project Success
Last Updated Mar 26, 2025
Last Updated Mar 26, 2025
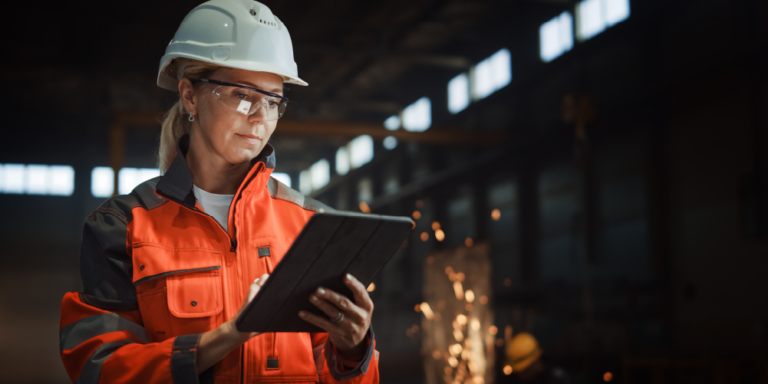
Starting a construction project without a detailed roadmap invites miscommunication and costly mistakes. Construction specifications provide this essential foundation, defining exactly what teams need to deliver. They determine the scope of work, materials, and performance standards, acting as a blueprint to reduce ambiguity and keep projects on track.
Table of contents
What are construction specifications?
Construction specifications (or "specs") outline the materials, methods, and quality standards required for a project. They form part of contract documents and guarantee that every aspect meets agreed standards and industry regulations.
A well-written specification covers:
- Scope of work: The full extent and standards of what needs to be built
- Materials and products: The exact materials, finishes, and components to use
- Installation methods: The correct techniques and procedures for construction
- Quality and performance standards: Requirements for compliance with regulations
Specifications complement construction drawings by clarifying details not visible on plans, from concrete strength to insulation requirements.
Who creates these documents?
Various professionals collaborate in construction projects to create clear and accurate specifications:
- Architects and designers develop design specifications for materials, finishes, and performance expectations.
- Project engineers create technical specifications aligned with structural, mechanical, and electrical requirements.
- Specification writers work closely with other professionals to draft and standardise documents to comply with regulations and project needs.
- Contractors and consultants provide input based on constructability, cost, and material feasibility.
Shape the Future of the Built Environment at Procore's Construction Summit
Engage with construction leaders and discover the latest technology and best practices that are driving change across the industry.
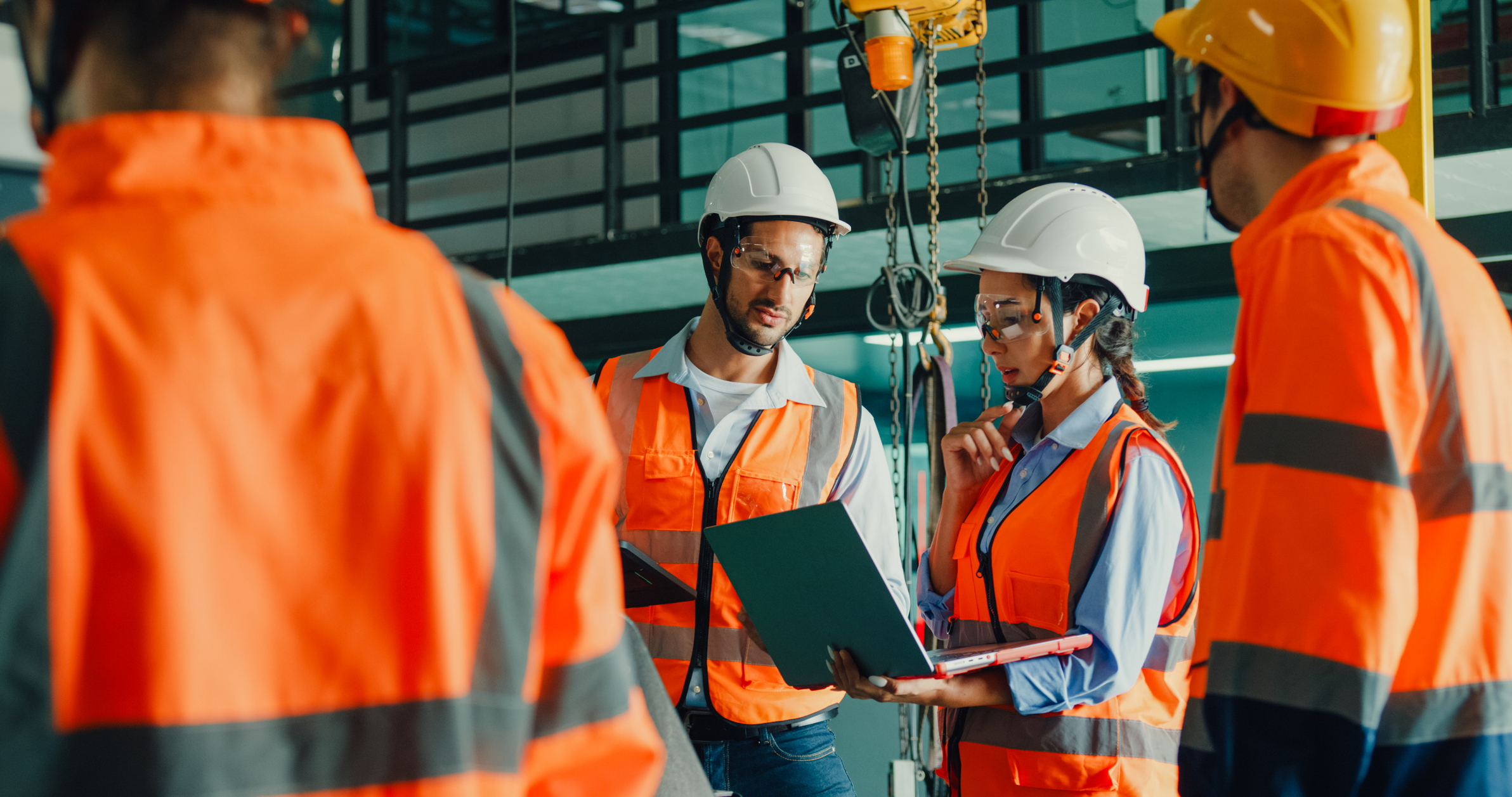
How Teams Use Construction Specifications
Construction specifications are used throughout a project’s lifecycle for compliance, quality, and consistency:
- Contract documentation: Legally binding documents ensure materials, workmanship, and performance meet obligations.
- Companion to drawings and models: Specifications provide technical details that blueprints alone can't capture, such as material grades, installation methods, and tolerances.
- Project handover resources: Documents detail as-built conditions, long-term maintenance requirements, and operational guidelines.
Benefits of Well-Written Specifications
Good specifications balance client expectations, legal compliance, technical feasibility, and aesthetics. They:
- Ensure regulatory compliance by outlining materials and methods that meet building codes and safety laws.
- Translate design vision into precise technical requirements that align with client goals.
- Maintain technical standards for structural integrity, energy efficiency, and durability.
- Reduce risks and prevent disputes by eliminating ambiguity in materials, methods, and quality benchmarks.
Construction Specification Types
Prescriptive Specifications
These provide explicit instructions on materials, products, and construction methods, promising uniformity across projects and leaving little room for interpretation.
Example: "All structural beams must be steel grade S275, manufactured to BS EN 10025 standards, and coated with a C3 corrosion protection system."
Best for: Projects requiring strict compliance with predefined materials and processes, such as government or heritage buildings.
Performance Specifications
These focus on desired outcomes rather than dictating specific materials or methods. They define the required performance criteria, allowing contractors and suppliers to determine the best solutions.
Example: "External wall insulation must achieve a minimum U-value of 0.18 W/m²K."
Best for: Projects prioritising innovation, cost-efficiency, and adaptability, like sustainable building initiatives.
Proprietary Specifications
These require specific brands, products, or manufacturers.
Example: "All windows must be Pilkington Optitherm™ S1 Plus glass units."
Best for: Projects requiring brand-specific materials due to compatibility, warranties, or performance guarantees.
How Specifications Drive Project Success
Reducing Errors and Miscommunication
Ambiguity in construction projects often leads to delays, disputes, and rework. Well-drafted specifications give everyone a shared understanding of project requirements.
Example: A precise specification like "Use C40/50 concrete in accordance with BS EN 206-1" prevents confusion that could arise from vague terms like "Use high-strength concrete."
Ensuring Regulatory Compliance
Specifications help teams meet legal and regulatory requirements, reducing non-compliance risks. They ensure materials and methods align with building codes, health and safety regulations, and sustainability standards.
Example: Fire safety specifications must adhere to Approved Document B (UK Building Regulations), dictating fire resistance ratings for different building elements.
Controlling Costs
Precise specifications prevent material substitutions that could lead to performance issues or costly modifications.
Example: A detailed specification stating "Use mineral wool insulation achieving a minimum R-value of 4.0 m²K/W" prevents last-minute substitutions and scope creep.
Enhancing Quality and Longevity
Clear specifications define performance standards that directly impact building quality and durability.
Example: Specifications for structural steel coatings determine corrosion resistance, directly affecting a building's lifespan.
Writing Effective Specifications
Define Clear Scope
Outline precisely what teams need to build, with what materials, and to what standards. A defined scope prevents contractor disputes and guarantees that materials meet the required standards.
Example: Replace "Install wooden flooring" with "Install 20mm oak hardwood flooring, FSC-certified, with a UV-resistant matte finish, in compliance with BS 8201 standards."
Use Standard Industry Language
Apply consistent terminology and reference recognised standards and regulations. This ensures materials meet regulatory requirements and prevents suppliers from substituting lower-quality products.
Example: Instead of "High-quality steel beams," specify "S355 structural steel, compliant with BS EN 10025-2 standards."
Detail Materials and Methods
Clearly define:
- Materials: Brand, grade, or technical specifications
- Installation methods: Required techniques, tolerances, and workmanship
- Performance criteria: Strength, durability, fire resistance, and insulation values
Example: “Use C40/50 concrete mix with a minimum compressive strength of 40 MPa, compliant with BS EN 206-1."
Align All Documentation
Ensure specifications match drawings, contracts, and other project documents, preventing contractor misalignment.
Example: If drawings show double-glazed windows, specifications should not reference triple-glazing.
Organise for Readability
Structure specifications logically:
- General requirements: Overview, scope, and compliance standards
- Materials: Detailed specifications for each material
- Execution and workmanship: Installation methods and best practices
- Testing and quality control: Inspection procedures and acceptance criteria
Example: A mechanical specification might include:
- Piping materials: Specify material, size, and pressure rating
- Installation requirements: Welding methods and corrosion protection
- Testing: Pressure tests and compliance with BS EN 10255
Collaborate Across Disciplines
Involve engineers, architects, and contractors to verify viability, identify potential conflicts, and prevent procurement delays.
Example: When an architect specifies a complex façade material, contractors can identify sourcing or installation challenges early.
Review and Update Regularly
Keep specifications current with new regulations, material availability, and evolving project needs. Outdated specifications can lead to non-compliance, delays, and unnecessary costs.
Example: A sustainability-driven project may update specifications to incorporate lower-carbon concrete alternatives as technology advances.
Digital Tools for Specification Management
Modern construction software helps teams create more accurate, standardised, and accessible specifications:
Template Automation
Teams can create and reuse pre-approved templates to ensure consistency and compliance. This reduces the risk of missing key details and aligns specifications with industry standards and regulations.
Real-Time Collaboration
Cloud-based platforms enable all stakeholders to work with the latest versions, preventing errors from outdated information.
Integration with Construction Drawings and BIM
Advanced software integrates specifications with project drawings and Building Information Modelling (BIM). This process is often complex but with careful management, specs and designs are synchronised, improving project coordination and efficiency.
Compliance Verification
Digital tools automatically track and verify compliance with regulations, industry standards, and client requirements. For example, a specification management platform automatically flags non-compliant fire-resistant materials needed to meet Approved Document B requirements.
Improved Accessibility
Cloud-based specifications allow teams to search, filter, and access specific details instantly from any device.
The Future of Specification Management
AI-driven tools, BIM integration, and cloud-based collaboration continue to make specification management more efficient and error-free.
Construction specifications form the backbone of successful projects, by clearly defining materials, methods, and performance standards. By following best practices and leveraging digital tools and data-driven approaches, project teams can enhance collaboration and ensure quality and compliance throughout the construction lifecycle.
Precise, well-structured specifications help deliver projects that meet expectations - on time and within budget.
Categories:
Tags:
Written by
Nicholas Dunbar
27 articles
Nick Dunbar oversees the creation and management of UK and Ireland educational content at Procore. Previously, he worked as a sustainability writer at the Building Research Establishment and served as a sustainability consultant within the built environment sector. Nick holds degrees in industrial sustainability and environmental sciences and lives in Camden, London.
View profileZoe Mullan
Zoe Mullan is an experienced content writer and editor with a background in marketing and communications in the e-learning sector. Zoe holds an MA in English Literature and History from the University of Glasgow and a PGDip in Journalism from the University of Strathclyde and lives in Northern Ireland.
View profileExplore more helpful resources
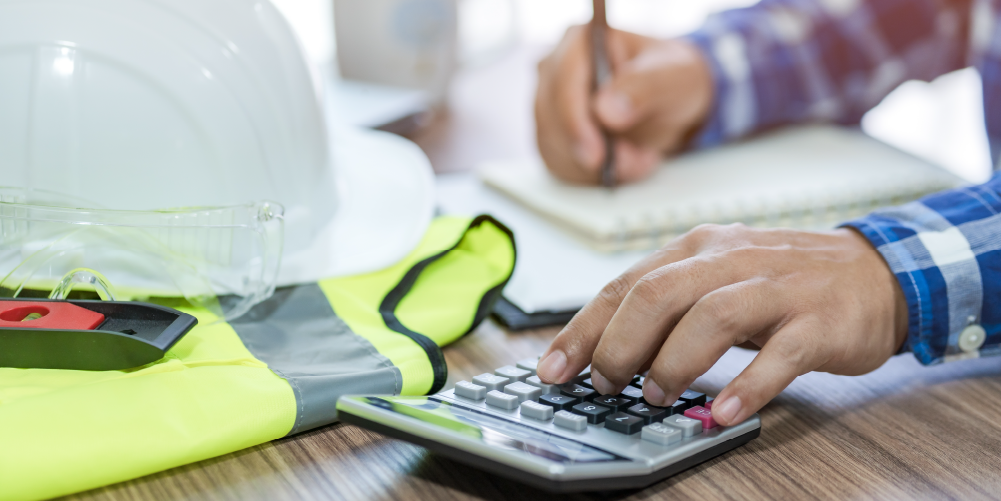
Leveraging Analytics for Better Financial Forecasting in Construction
Financial forecasting is a difficult task in any industry. In construction, where companies need to manage volatile material costs, labour shortages and variation orders on a daily basis, fluctuations in...
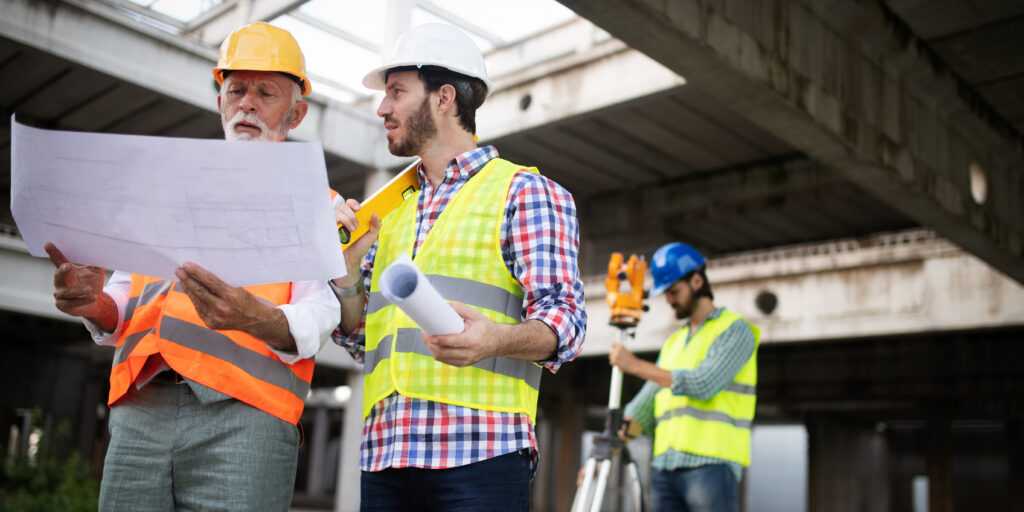
Strategies to Prevent Rework: The Importance of Clear Instructions
In construction, “rework” is the dreaded process of redoing tasks due to mistakes, quality issues, or safety concerns. This unnecessary work drains budgets through wasted materials and labour while causing...
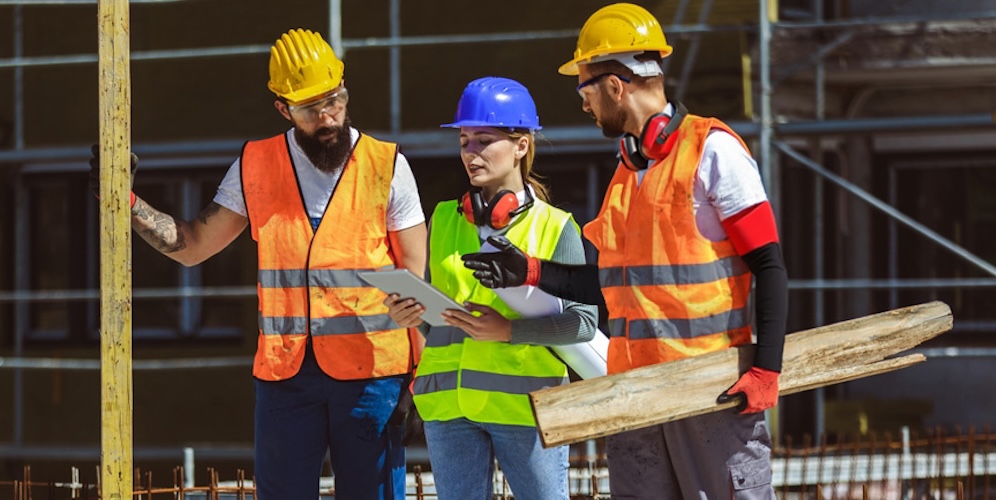
Building a Culture of Quality in Construction: How Safety Approaches Can Transform Quality
The UK construction industry faces persistent quality issues that compromise safety, inflate costs, and erode trust. Despite universal pursuit of excellence, high rates of rework and defects cost billions annually...
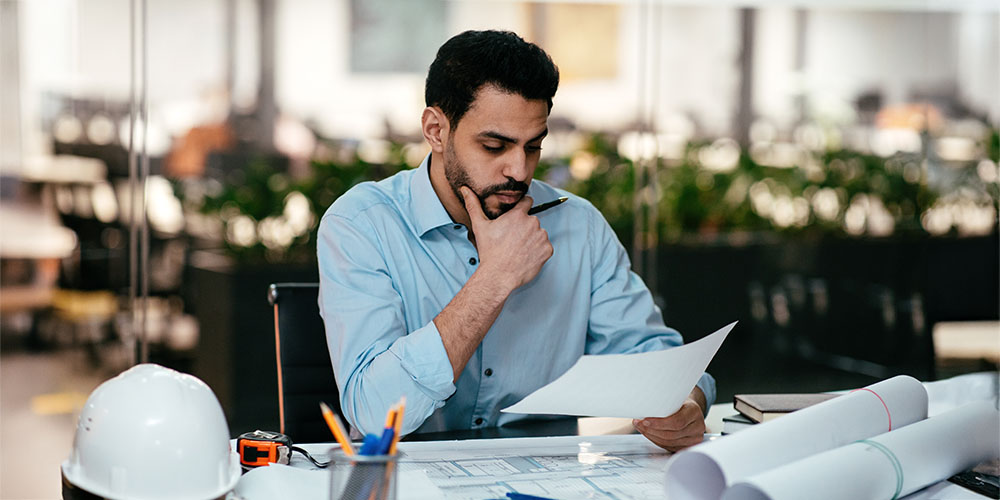
Mastering Document Control in Construction Projects
The construction industry generates enormous volumes of paperwork. A single project can produce countless documents, making organisation, accessibility, and security essential. Construction document control systematically manages project-related documents, giving teams...