— 9 min read
Co-ordinating MEP in Construction: A Guide
Last Updated Mar 26, 2025
Last Updated Mar 26, 2025
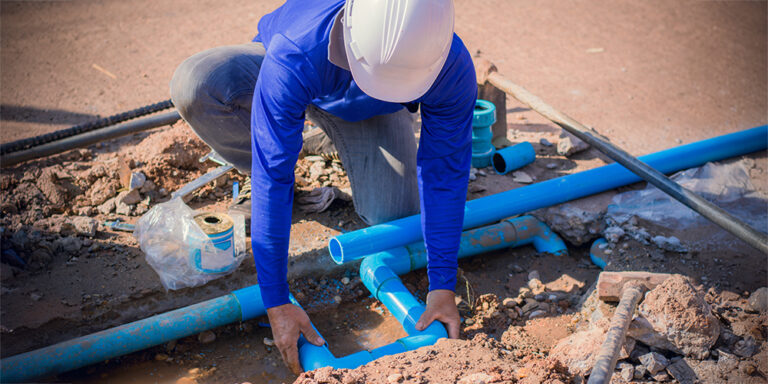
Coordinating MEP systems in construction is a complex and important process that ensures all building systems function together efficiently, safely, and within the project’s timeline and budget. Proper coordination of MEP in construction helps to avoid conflicts, ensure regulatory compliance, and streamline installation and operation.
Table of contents
What is MEP in construction?
MEP in construction stands for Mechanical, Electrical, and Plumbing systems. These are the essential building systems that provide functionality, comfort, and safety to a structure. MEP systems play a significant role in the building of both residential and commercial buildings. Below are the key elements of each component:
1. Mechanical Systems (M):
- HVAC (heating, ventilation, and air-conditioning)
- Fire protection
- Pumps and fans
- Lifts and escalators
2. Electrical Systems (E):
- Power distribution
- Lighting
- Power outlets and switches
- Low-voltage systems
3. Plumbing Systems (P):
- Water supply
- Drainage systems
- Gas systems
- Stormwater systems
Taking an Integrated MEP Approach: The Benefits
An integrated approach to MEP in construction involves the close collaboration and coordination of all MEP systems, from the early stages of design through to installation and operation. This approach brings several significant benefits, enhancing the overall efficiency, sustainability, and effectiveness of a construction project. Here are some of the key advantages of an integrated MEP approach:
Improved Collaboration and Communication
An integrated approach to MEP in construction increases communication and collaboration, reduces conflicts and helps to minimise costly revisions during the construction project. With clear coordination and planning, installation is more straightforward and faster.
Enhanced System Efficiency
When MEP systems are designed and integrated, they can be optimised to drive energy efficiency and performance. For example, HVAC systems can be created to work efficiently with lighting systems, and plumbing can be aligned with electrical systems to minimise energy consumption and improve overall building performance.
Cost Savings
By integrating MEP systems, designers can avoid duplication of systems or elements that would otherwise add to the project’s cost. An integrated design reduces the likelihood of costly change orders that arise from unforeseen conflicts or issues that were not addressed during the design phase.
Faster Project Delivery
Early collaboration and planning help streamline the construction schedule, reducing delays due to late-stage revisions or clashes. MEP systems can be installed concurrently, allowing MEP contractors to work in parallel and in a more organised manner, which can help to avoid disputes and make sure projects are delivered on time.
Sustainability and Environmental Benefits
An integrated approach supports sustainability goals by ensuring that MEP systems are optimised for energy use and minimal environmental impact. For instance, renewable energy sources like solar panels or geothermal systems can be better integrated into the building’s MEP systems. Integrated MEP design plays a key role in meeting green building certifications. The MEP systems can be planned to reduce energy consumption, enhance indoor air quality, and use sustainable materials.
Risk Mitigation
When MEP systems are designed to integrate from the start, there is less chance of system failures that could compromise the building's performance or safety. This is especially important for systems like fire safety, electrical, and plumbing. Integrated MEP systems ensure that all design and installation meet the required UK building codes and standards, reducing the risk of compliance issues during inspections.
Better Lifecycle Management
With well-integrated MEP systems, a building's long-term performance and lifecycle costs can be better managed, ensuring that systems operate efficiently over time and reducing the need for expensive repairs or replacements.
Shape the Future of the Built Environment at Procore's Construction Summit
Engage with construction leaders and discover the latest technology and best practices that are driving change across the industry.
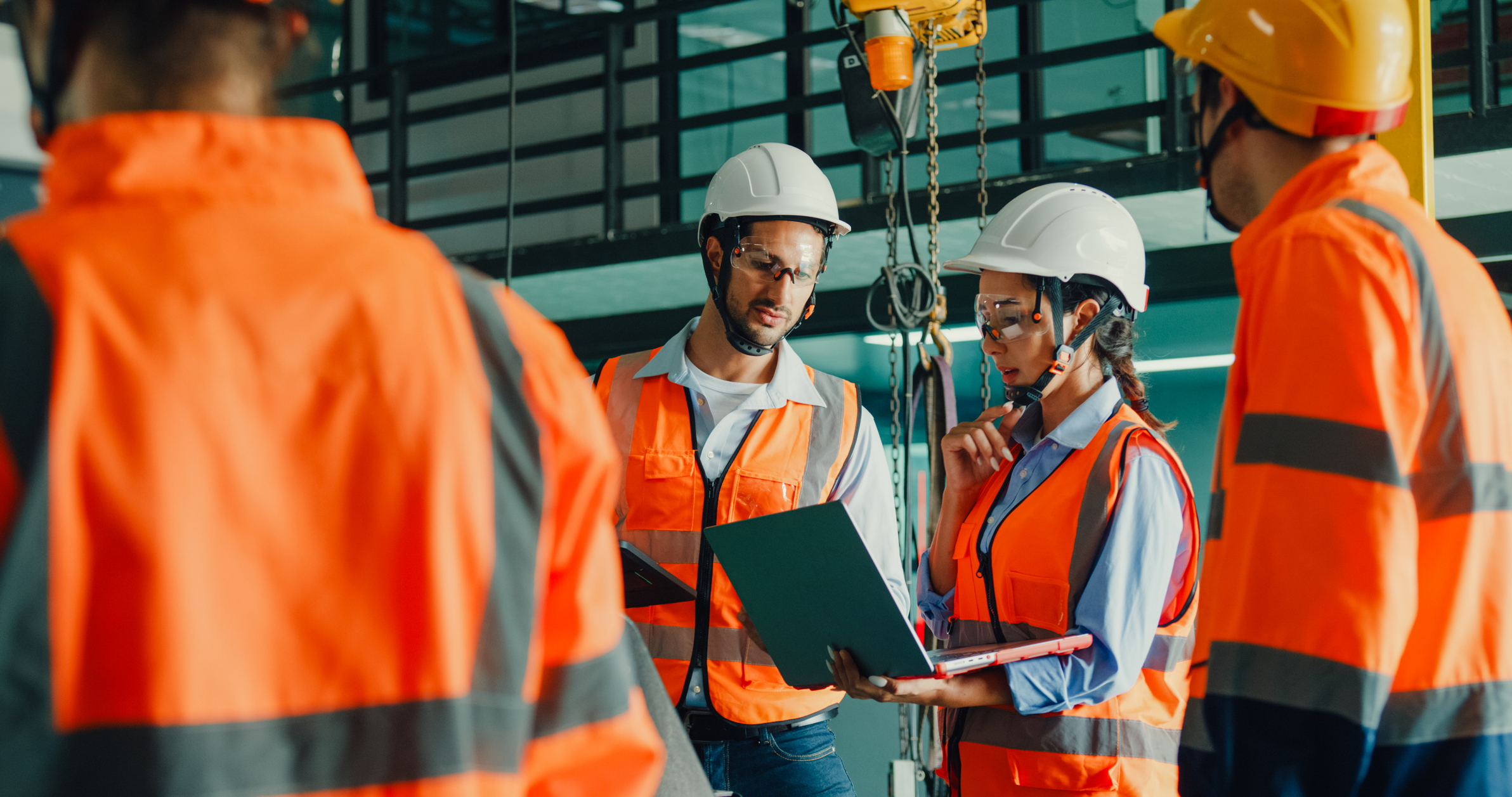
The Challenges of MEP Design and Installation
Designing and installing MEP systems in construction can be complex due to a set of common challenges that can arise during the process. These challenges require careful planning, coordination, and problem-solving to ensure the systems are functional, cost-effective, and compliant with regulations. Here are some of the most common challenges in MEP design and installation:
Lack of Co-ordination Between Trades
MEP systems often need to fit into the same spaces and interact with structural and architectural elements. Coordinating between MEP subcontractors, architects, structural engineers, and other trades is needed to prevent conflict.
Clashes and Conflicts
MEP systems (such as ducts, pipes, and electrical cables) can conflict with structural elements like beams, columns, and walls. Without careful planning, these clashes can lead to costly delays and rework. Using BIM (Building Information Modelling) software can help detect these clashes early in the design phase, but sometimes they may only become apparent during the actual installation, especially if the coordination was not detailed enough in the models.
Difficulty Integrating Modern Systems with Legacy Systems
Integrating new MEP systems with existing, older infrastructure can present difficulties. Legacy systems may have outdated standards, requiring adjustments or modifications to comply with modern codes. Incorporating advanced technologies, such as smart building systems, into existing MEP frameworks can also be a challenge, particularly when dealing with older electrical or HVAC infrastructure.
Non-compliance with Codes and Standards
MEP systems are expected to comply with local, regional, and national codes and standards, which may vary. With a growing emphasis on sustainability, MEP systems also need to meet energy-efficient standards, such as BREEAM (Building Research Establishment Environmental Assessment Method), which can affect system design choices.
Cost Control and Budgeting Issues
More complex MEP designs, especially those involving custom systems or advanced technologies, can increase the cost of installation. Managing these costs while ensuring the systems meet the required performance standards is often a constant challenge.
Scheduling Conflicts
MEP work is typically one of the final stages of construction, and delays in MEP design or installation can impact the overall project timeline. Careful planning and scheduling are needed to ensure the timely completion of systems without other aspects of construction being affected.
Insufficient Quality Control and Testing
Commissioning MEP systems involves verifying that they meet quality expectations, ensuring integration with other building systems, and fine-tuning to optimal performance. This process can be time-consuming and requires careful attention to detail. Once installed, MEP systems need to undergo rigorous testing to make sure they operate efficiently and safely. This testing phase may uncover issues like leaks, electrical faults, or poor airflow, requiring additional work to resolve.
Navigating Environmental Factors
Designing MEP systems that are energy-efficient and environmentally friendly can be challenging, as this may involve the integration of renewable energy sources (like solar panels or geothermal systems) or advanced HVAC systems that require specialised expertise.
Adapting for High Rise and Complex Buildings
The challenges presented by height, large occupancy numbers, and the need for complex, integrated systems require MEP engineers to adopt innovative, scalable, and efficient designs. From HVAC and plumbing to fire safety and energy management, MEP plays a central role in delivering buildings that are more than simply operational; they are sustainable, safe, and comfortable for their users. Effective coordination, advanced technologies like BIM, and adherence to regulations are key to successful MEP design and installation in these types of buildings.
MEP in Construction: How Technology is Building the Future
MEP engineering in the UK has seen significant advancements, driven by technological innovations, sustainability initiatives, and the adoption of BIM. Here is a look at some of the latest developments:
Integration of BIM
A 3D BIM model can simulate how MEP systems will fit into the building structure. It helps in detecting clashes (e.g., pipes running through a beam), allowing for adjustments to be made before actual installation begins. The use of BIM in construction enables real-time sharing and updating of information among teams, improving collaboration, reducing delays and cost overruns, minimising disputes and helping to streamline workflows.
Adoption of Virtual Reality (VR) and Augmented Reality (AR)
MEP design is being transformed by the adoption of VR and AR technology, which allows architects, engineers and clients to ‘see’ the MEP systems in a virtual environment. Using this technology at the design stage helps to improve understanding and aids with key decision-making that can mitigate risk and loss from the very start of the construction project.
Enhanced MEP Software Capabilities
MEP software capabilities continue to be improved, leading to more accurate and efficient designs. Advanced MEP software allows all stakeholders to track the work of MEP systems and check that the installation schedule is aligned with other construction activities, helping to reduce delays and optimise resource management allocation.
Focus on Sustainability and Energy Efficiency
MEP engineering in the UK is increasingly aligned with sustainability goals, like the UK’s Net Zero Strategy. New MEP systems are incorporating energy-efficiency, renewable energy sources, and smart building technologies to reduce carbon footprints and operational costs. This trend is supported by the UK’s stringent building regulations and commitment to environmental responsibility.
Co-ordinating MEP in Construction, Step-by-Step
By following these steps and utilising technology such as BIM, you can streamline the MEP coordination process, prevent costly mistakes, and ensure that the MEP systems operate effectively and efficiently in the completed building.
1. Embrace Early Planning and Design Integration
Early on, aim to involve MEP engineers in the design discussions with architects and structural engineers. The goal is to create a design where MEP systems are seamlessly integrated into the building layout, without conflicting with each other or with other structural elements.
2. Coordinate with Structural and Architectural Elements
Coordinate with the structural and architectural teams to ensure that space for ducts, pipes, electrical conduits, and mechanical systems is provided early in the design phase.
3. Utilise BIM and 3D Modelling
Implement clash detection software within the BIM model to identify and resolve conflicts between MEP systems and other building components.
4. Hold Regular Co-ordination Meetings
Gather the project’s MEP contractors, architects, and engineers to review progress and discuss any issues or changes.
5. Check Compliance with Codes and Standards
Make sure that the MEP designs and installations comply with local building codes, safety regulations, and industry standards.
6. Conduct Site Co-ordination and Field Verification
Before installation begins, ensure that all MEP routing is verified in the field to confirm that systems fit as planned and meet spatial constraints.
7. Facilitate Communication Between Teams
Maintain thorough documentation of all MEP drawings, revisions, and installation instructions. This keeps everyone on the same page and helps avoid costly mistakes or rework.
8. Carry Out Testing and Commissioning
Once the MEP systems are installed, thorough testing and commissioning should be carried out to check that everything works as expected. After testing, a final inspection of all MEP systems is necessary to ensure compliance with the design, safety standards, and functionality.
9. Manage Documentation for Handover
Create as-built drawings and documentation of all MEP systems that show any changes or modifications made during the construction process. A well-managed Document Management System (DMS) is of importance here. Provide the owner with operation and maintenance (O&M) manuals for all installed MEP systems.
10. Oversee Collaboration Between Subcontractors
Ensure that MEP subcontractors work closely together, sharing information on system design and installation to avoid confusion or delays. Plan the sequence of installation for different MEP systems so that no work interrupts or damages another system.
Strong MEP coordination is the backbone of a successful construction project. By adopting best practices, using the latest technology, and planning ahead, you can avoid delays, reduce costs, and ensure that your building operates efficiently, well into the future.
Categories:
Tags:
Written by
Nicholas Dunbar
29 articles
Nick Dunbar oversees the creation and management of UK and Ireland educational content at Procore. Previously, he worked as a sustainability writer at the Building Research Establishment and served as a sustainability consultant within the built environment sector. Nick holds degrees in industrial sustainability and environmental sciences and lives in Camden, London.
View profileExplore more helpful resources

Construction Document Software: Essential Tools for Project Success
Construction projects depend on extensive paperwork, including designs, contracts, RFIs, and compliance records. A single misplaced document can trigger delays, disputes, or compliance violations. Despite increasing digital adoption, many teams...
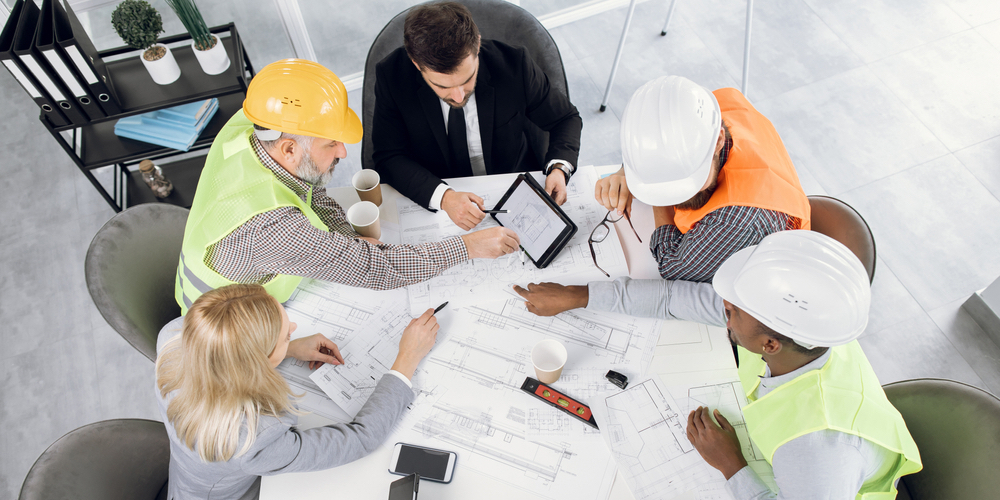
Construction Planning: A Guide to Successful Project Execution
Every successful construction project begins long before the first brick is laid. Indeed, behind each structure – whether a towering skyscraper or complex infrastructure project – lies a carefully crafted...
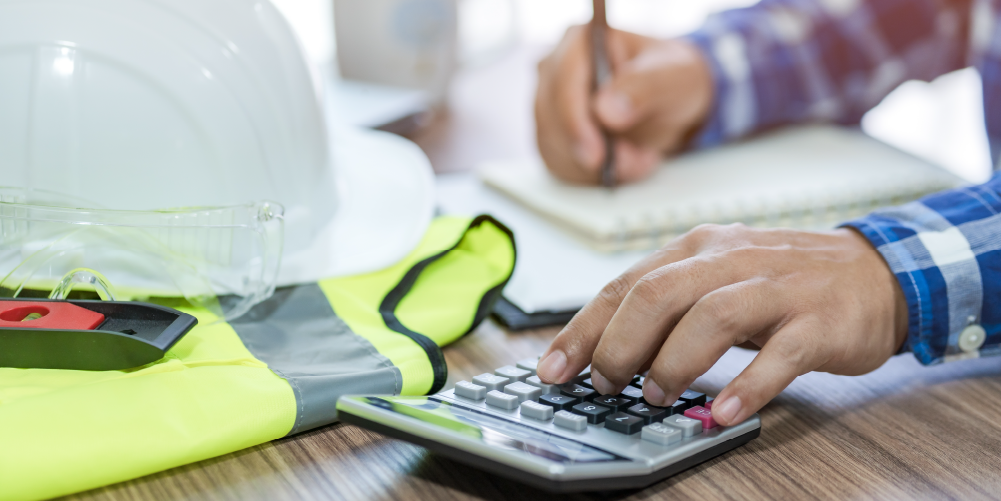
Leveraging Analytics for Better Financial Forecasting in Construction
Financial forecasting is a difficult task in any industry. In construction, where companies need to manage volatile material costs, labour shortages and variation orders on a daily basis, fluctuations in...
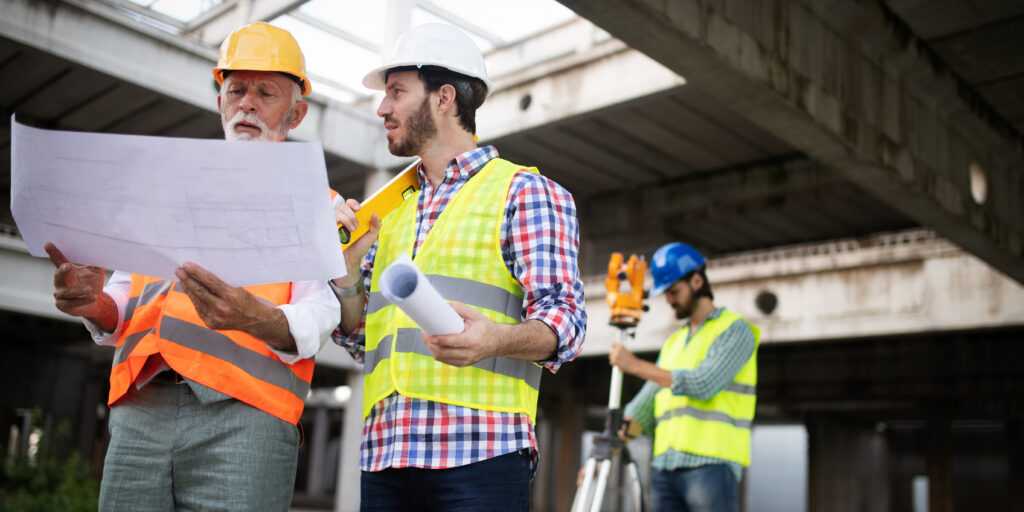
Strategies to Prevent Rework: The Importance of Clear Instructions
In construction, “rework” is the dreaded process of redoing tasks due to mistakes, quality issues, or safety concerns. This unnecessary work drains budgets through wasted materials and labour while causing...