— 7 min read
What is MMC?
Last Updated Mar 26, 2025
Last Updated Mar 26, 2025
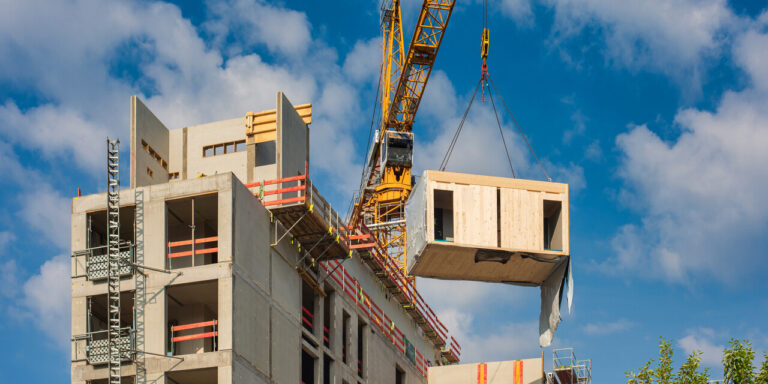
Modern methods of construction (MMC) are construction’s new solutions to age-old problems. By embracing technology, innovation and new ways of working, MMC represent brand-new benefits and opportunities for the construction sector.
MMC are new ways of building that help construction professionals to work more efficiently and effectively compared to traditional methods. There are lots of types of MMC, each with their own benefits and learning curves.
Table of contents
Types of MMC
The following list of modern methods of construction is just a handful of the methods available to construction professionals. More methods arise as technology and innovative thinking continue to progress, but these are some of the types of MMC that we see active today.
Off-site fabrication
Off-site fabrication is the process by which construction teams assemble or manufacture parts for a project away from the building site. This generally takes place in large warehouses or factory environments. There are many benefits to this process, including needing fewer people on site, which creates a safer environment, and time savings thanks to the ability to work on multiple processes in parallel. Off-site fabrication requires proactive project and logistics management to make sure that all deliveries are properly scheduled.
Modular construction
The development of off-site fabrication has paved the way for modular building, which is a technique that enables construction teams to build a prefabricated structure in sections called ‘modules’, that can then be fitted together once on site.
Modular construction, particularly in residential sectors, offers massive opportunities. It allows for buildings to be prefabricated in parts and assembled on site, significantly speeding up construction and improving quality thanks to the factory conditions.
Daniel Kavanagh
Solution Specialist, Industry Compliance
Procore Technologies
With this method, houses can be built, for example, in two separate pieces then fitted together on site. Modular building is quicker than traditional building methods, with production line fabrication supporting consistency and high quality.
Precast panels
Precast panels are another factory-based innovation that help to speed up construction and reduce the amount of work done on site. They are concrete panels which are cast in a mould and cured, and can be used for walls and floors, among other components. Many companies are using precast panels to speed up construction timelines. Since they are made in a factory, their production is not impacted by adverse weather conditions.
Building Information Modelling
Building Information Modelling (BIM) is a technology which allows you to create a 3D model of a construction project collaboratively, as well as integrating data such as project schedules, budget information, project management, and more. It essentially acts as a shared platform which allows construction professionals to work together on an up-to-date digital twin of a build in real time. You can learn more in our article about BIM.
Shape the Future of the Built Environment at Procore's Construction Summit
Engage with construction leaders and discover the latest technology and best practices that are driving change across the industry.
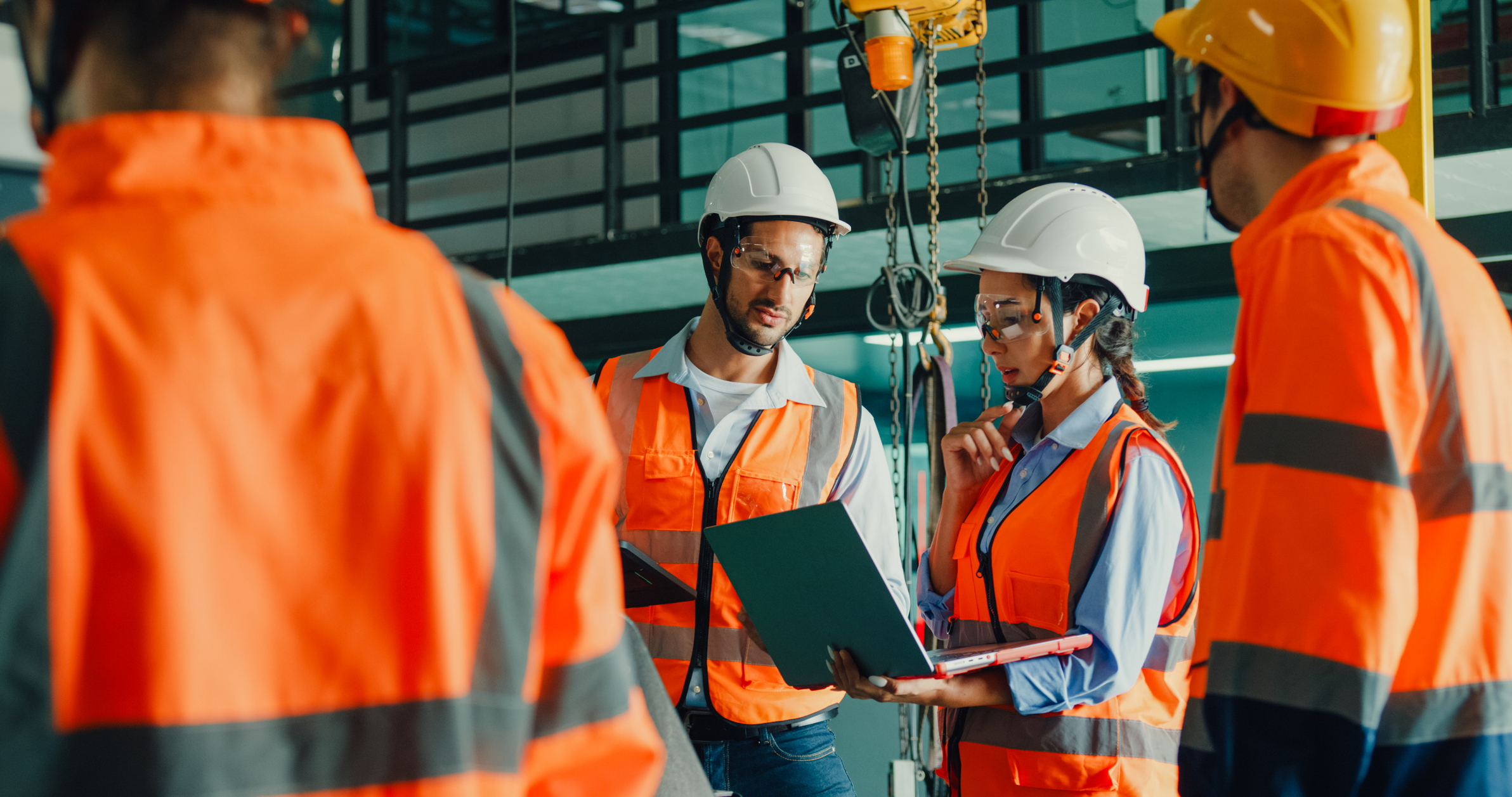
Benefits of Modern Methods of Construction
MMC usher in a whole host of benefits for construction professionals and clients, which makes them attractive for both sides of the construction project equation. Here are some of the key benefits that they unlock:
Enhanced efficiency and speed
Most of the MMC we have discussed in this article involve fabricating elements in a factory or warehouse setting instead of on the building site. This brings with it the benefits of a production line-style of working, which is faster than building on site. There are fewer, if any, distractions or delays caused by unforeseen site conditions, as the environment is controlled and purpose-built. Many MMCs also speed up site construction work, too, as components arrive prefabricated and need less set-up time.
Using MMC, combined with just-in-time deliveries, dramatically enhances project efficiency. This method requires meticulous planning but offers massive benefits, allowing projects to proceed faster by resolving potential on-site construction clashes beforehand.
Daniel Kavanagh
Solution Specialist, Industry Compliance
Procore Technologies
Improved quality and consistency
The factory environment, in which many MMC processes take place, also benefits quality and consistency. The factory setting reduces the likelihood of accidents or negative effects of bad weather. The precision engineering and advanced technology, such as automation used to construct components, enables a level of standardisation that is not easy to maintain with traditional methods. There is also extensive quality assurance that helps ensure that all components are up to standard before they leave the fabrication environment.
The quality assurance from MMC is unparalleled. Prefabrication in controlled factory settings ensures consistent high quality, free from the unpredictability of on-site construction.
Daniel Kavanagh
Solution Specialist, Industry Compliance
Procore Technologies
Environmental benefits
Modern methods of construction are often more sustainable than traditional methods. MMC creates less waste because the precision of cutting and assembly mean that it’s easier to use the exact quantity of materials, with no need for generous allowances, to make sure sizing is correct. Often, there are more opportunities to reuse surplus materials and better recycling facilities in a factory or warehouse environment.
MMC also typically mean fewer deliveries are made to the site as all materials are kept in one place until the delivery of the larger completed component, rather than needing lots of separate trips to deliver materials when constructing a component on site.
Safety
A more people-focussed benefit of MMC is that many of the methods we have looked at help to create a safer environment on building sites. They reduce the number of people and volume of materials needed on site the due to the ability to manufacture components remotely. This in turn reduces the risk of accidents and injuries caused by too much foot traffic and storage issues.
Cost-effectiveness
With less reliance on having people on site, these methods also introduce financial advantages because on-site labour is often more expensive than off-site fabrication. MMC also allows project teams to work to shorter project timelines because of the ability to work on multiple phases of construction at the same time. Reduced waste also means reduced expenses, as it’s easier to pay for the exact amount of materials that you need with these methods — traditional methods often rely on generous estimates for allowances in case of mistakes, which is expensive.
Challenges and Barriers to MMC
Technical and Skill-Related Hurdles
The change from traditional methods to using MMC requires learning and upskilling, as any new development that leads to a change in ways of working does. Some people are more adaptable to change than others, so it’s important that there is enough education around the how and why of introducing MMC to your construction projects.
Initial Cost and Investment Requirements
MMC requires a level of investment before a company will see the return, which is common for a lot of transformation initiatives. However, balancing this with the potential to do work quicker and with less requirement for on-site labour should provide a reassuring evaluation of the potential returns that MMC can bring.
While MMC is often perceived as costly, a detailed return on investment analysis can reveal its economic advantages. These include reduced on-site accidents, lower rework needs due to improved quality, and the efficient use of resources, all contributing to cost savings over time.
Daniel Kavanagh
Solution Specialist, Industry Compliance
Procore Technologies
Lack of awareness
MMC are not yet mainstream and may require some intensive discussions to demonstrate the value of trying them. It can be difficult to go against general practice when mainstream methods of construction have been working well for a long time, so it’s important to show value to get people on board.
Frequently Asked Questions (FAQ)
How can technology help to successfully adopt MMC?
Construction management can help to integrate MMC with current ways of working. It can help with the scheduling aspect of construction projects, as MMC that involve off-site fabrication need very careful logistics and project management to make sure that deliveries happen on time and at the right time.
What successful projects in the UK were built with MMC?
Well known examples of buildings in the UK that were constructed using MMC include:
+ The Shard, London
+ Southmead Hospital, Bristol
+ George Street, the world’s tallest modular building, London
How can the government encourage construction businesses to adopt MMC?
There are a couple of areas that could help modern methods of construction to enter the mainstream. The first is regulation: currently, there aren’t specific regulations or regulatory bodies that deal with MMC. This can mean some companies are reluctant to take the risk of trying them out. Another way that the government can encourage adoption of MMC is to offer tax incentives to companies that use them.
Categories:
Tags:
Written by
Daniel Kavanagh
15 articles
Daniel Kavanagh is a Senior Strategic Product Consultant at Procore, based in Dublin, Ireland. Daniel is a results-oriented project manager with a passion for building relationships and exceeding client and management expectations, with career experience in project management, systems implementation, technical design and architectural finishes. Daniel has been a member of the construction industry since 2014, and graduated from the Carlow Institute of technology.
View profileReviewed by
Nicholas Dunbar
29 articles
Nick Dunbar oversees the creation and management of UK and Ireland educational content at Procore. Previously, he worked as a sustainability writer at the Building Research Establishment and served as a sustainability consultant within the built environment sector. Nick holds degrees in industrial sustainability and environmental sciences and lives in Camden, London.
View profileExplore more helpful resources

Construction Document Software: Essential Tools for Project Success
Construction projects depend on extensive paperwork, including designs, contracts, RFIs, and compliance records. A single misplaced document can trigger delays, disputes, or compliance violations. Despite increasing digital adoption, many teams...
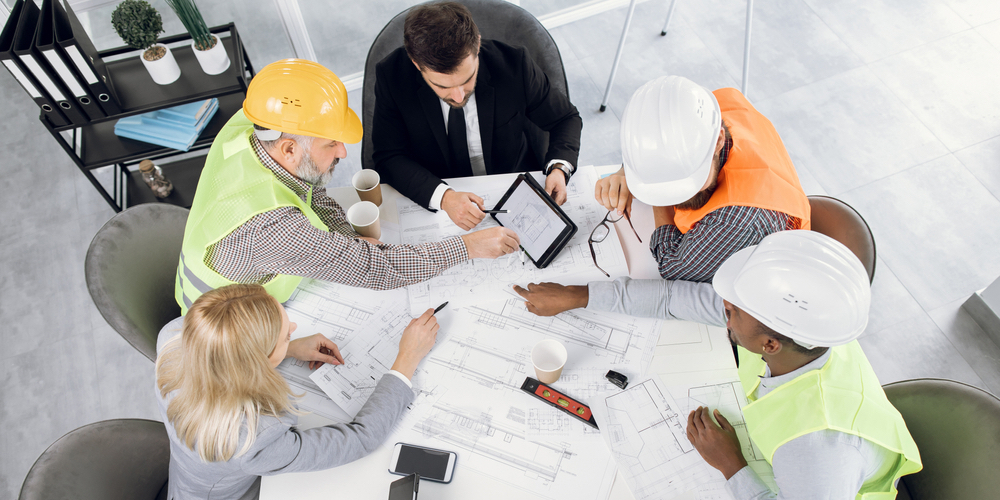
Construction Planning: A Guide to Successful Project Execution
Every successful construction project begins long before the first brick is laid. Indeed, behind each structure – whether a towering skyscraper or complex infrastructure project – lies a carefully crafted...
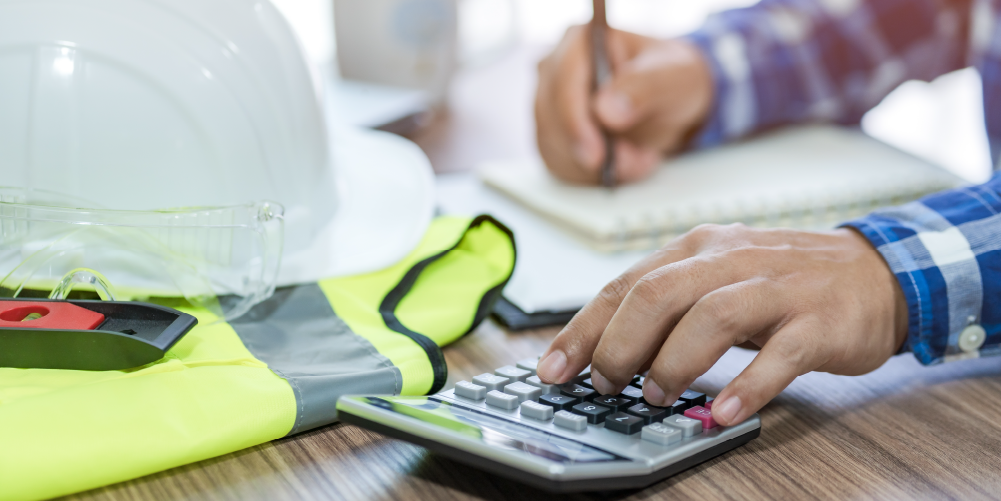
Leveraging Analytics for Better Financial Forecasting in Construction
Financial forecasting is a difficult task in any industry. In construction, where companies need to manage volatile material costs, labour shortages and variation orders on a daily basis, fluctuations in...
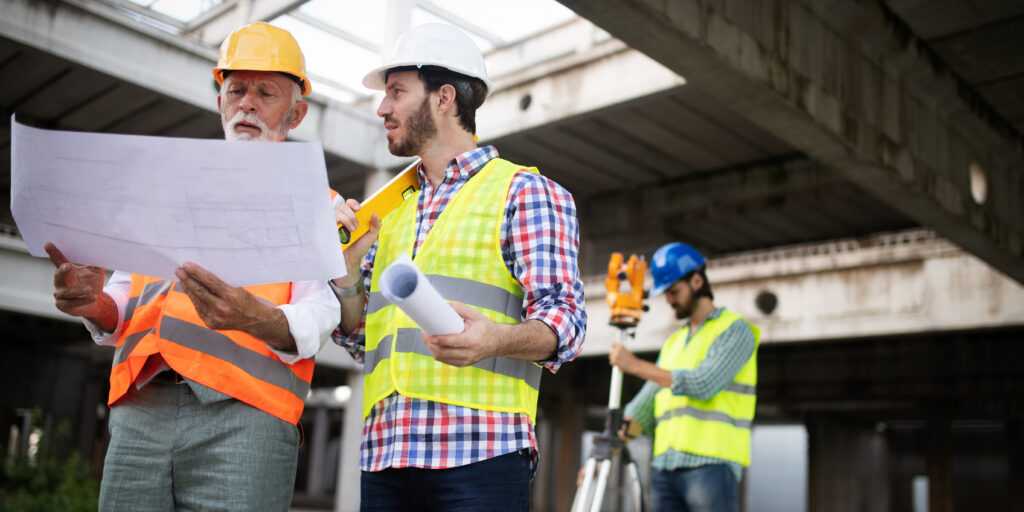
Strategies to Prevent Rework: The Importance of Clear Instructions
In construction, “rework” is the dreaded process of redoing tasks due to mistakes, quality issues, or safety concerns. This unnecessary work drains budgets through wasted materials and labour while causing...