— 4 min read
Strategies to Prevent Rework: The Importance of Clear Instructions
Last Updated Mar 31, 2025
Last Updated Mar 31, 2025

In construction, “rework” is the dreaded process of redoing tasks due to mistakes, quality issues, or safety concerns. This unnecessary work drains budgets through wasted materials and labour while causing frustrating project delays.
Both clients and contractors benefit when teams prevent rework. The most effective prevention starts with clear instructions to teams. When you provide clear, comprehensive guidance, your team can deliver results that align perfectly with client expectations.
We try to preach the gospel of getting it right first time, but it’s almost impossible not to have any rework. The way you give instructions has a massive impact on how much rework you have to do.
Emmanuel Sinteh
Construction Quality Manager
BakerHicks
Table of contents
How Unclear Instructions Derail Construction Projects
Vague instructions create problems in three critical areas clients prioritise: budget, timelines, and quality. These issues can seriously damage client-contractor relationships.
Remember the responsibility for clear instructions mainly falls on designers and contractors, not clients. The client provides the scope and vision, while your team must develop the methodology and direct the work.
Construction projects typically involve various contractors with different experience levels. Everyone benefits from well-structured, detailed instructions tailored to their specific needs.
In my role, I have to review quality plans and inspection and test plans and give feedback. It’s almost like marking an exam script: you can tell who has more experience, and who you need to give more detailed or granular instructions.
Emmanuel Sinteh
Construction Quality Manager
BakerHicks
When instructions lack detail and structure, less experienced teams often miss key design elements. These seemingly minor oversights inevitably lead to rework - and sometimes require completely redoing completed work.
How to Create Instructions that Prevent Mistakes
Effective instruction begins with understanding your audience. Consider their experience level, communication style, cultural background, and specialisation. Tailored guidance works far better than generic instructions. As you collaborate over weeks and months, identify where specific teams need additional detail and adjust your approach accordingly.
Hold weekly meetings where everyone feels comfortable asking questions. Create an environment where every question is valid and welcomed. When multiple team members question the same instruction, you've identified an area needing more clarity. Encourage open questioning and even challenging of instructions to uncover potential problems before they materialise into costly rework.
Hidden Factors that Lead to Rework
While detailed instructions help prevent misunderstandings, watch out for these often-overlooked factors:
Unclear Scope and Specifications
A poorly defined scope leaves too much room for interpretation. Contractors may make assumptions that contradict client expectations. Always seek clarification when scope or specifications seem ambiguous.
Insufficient Resources
Large construction projects require adequate quality teams.
I've been on jobs that were worth over £60 million and I was the only quality personnel. I was expected to do QA, QC, and completions on handover. For the best results, you need a team.
Emmanuel Sinteh
Construction Quality Manager
BakerHicks
When project managers recognise they lack internal resources, they should engage recruiters to ensure sufficient personnel to maintain project standards. This proactive approach prevents quality issues from slipping through during construction and requiring rework.
Poor Document Management
Many construction projects overlook effective document control. Technical documents require skilled personnel who can translate intricate designs into clear contractor instructions. Position a design manager on-site to answer technical questions promptly, preventing delays. Implement a common data environment where everyone can access documentation, eliminating guesswork and forgotten details.
Quality Inductions
Safety inductions are an expected part of working on site, but quality inductions are just as important. These induction sessions are the perfect environment to help people understand everyone’s responsibilities, and to remind them that everyone is responsible for quality - not just the QA team. When people understand this, they’re more likely to take steps to avoid situations that require rework.
While safety inductions are standard on site, quality inductions deserve equal importance. Use these sessions to clarify responsibilities and emphasise that quality belongs to everyone - not just the QA team. When everyone understands their role in quality assurance, they actively work to prevent scenarios requiring rework.
Build It Right the First Time
Everyone benefits when construction projects avoid rework. Clear, detailed instructions provide the foundation for success. Also consider scope clarity, resource allocation, document management, and team inductions to enhance communication. With the right emphasis on quality, communication and culture you'll save your team significant headaches during final project phases.
Categories:
Tags:
Written by
Emmanuel Sinteh
View profileReviewed by
Zoe Mullan
Zoe Mullan is an experienced content writer and editor with a background in marketing and communications in the e-learning sector. Zoe holds an MA in English Literature and History from the University of Glasgow and a PGDip in Journalism from the University of Strathclyde and lives in Northern Ireland.
View profileExplore more helpful resources
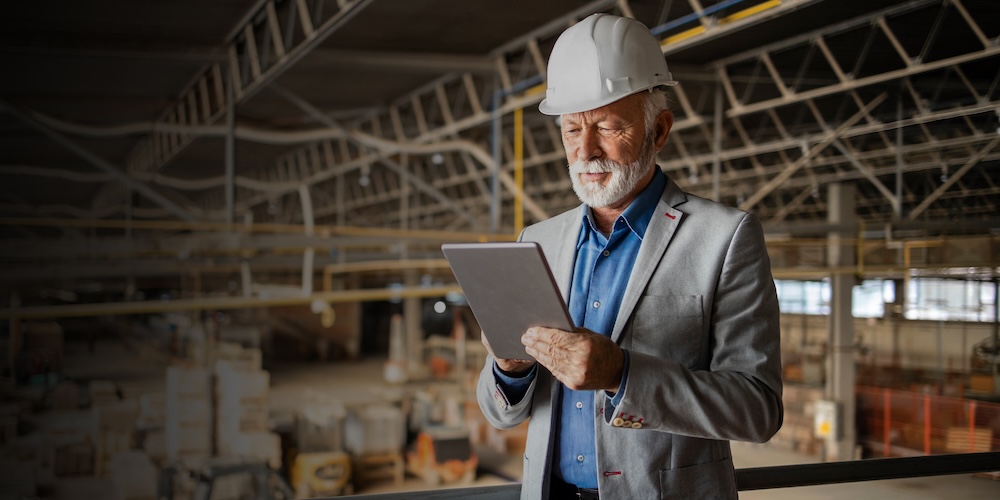
Ensuring Financial Transparency with Centralised Data Management in Construction
Financial transparency is a core part of a healthy business culture and means that there is clear, accurate and accessible financial information available for everyone who needs it. This can...
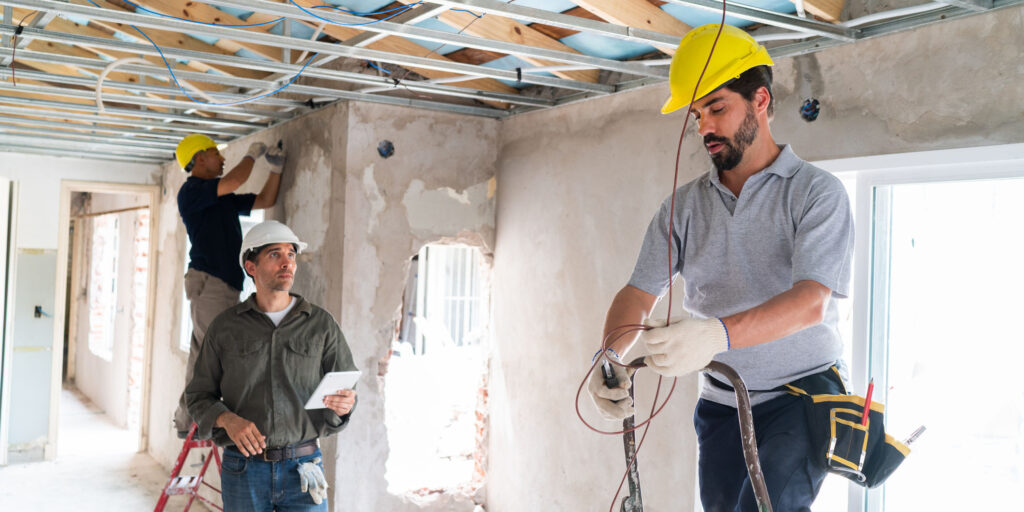
Enhancing Operational Efficiency Through Real-Time Construction Data Insights
Construction companies are forced to juggle a complex mix of challenges, including frequent cost overruns, schedule delays and limited visibility across multiple projects. These challenges can lead to a balancing...
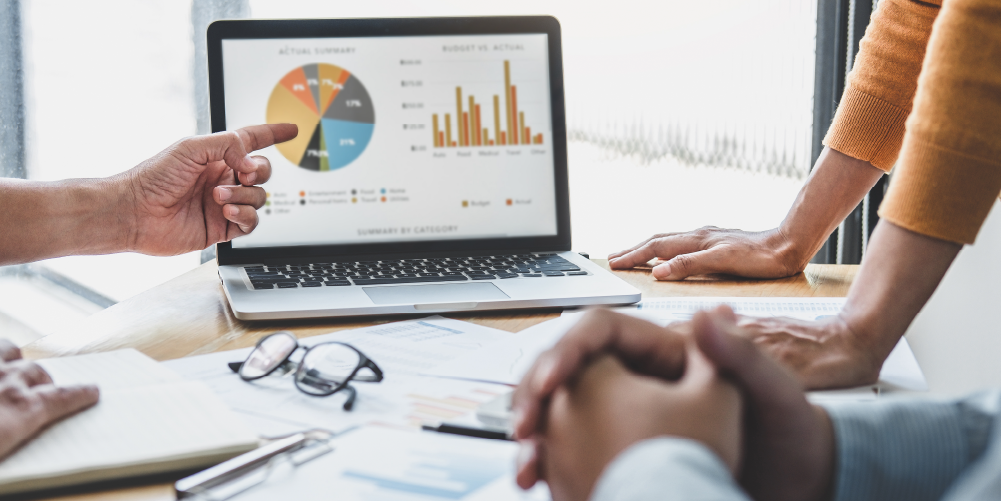
Monitoring Project Schedules and Resources in Construction
Construction projects have many moving parts: the materials, equipment, teams, deliveries, contracts, schedules — this list just scratches the surface. With so many elements to factor in, it takes the...
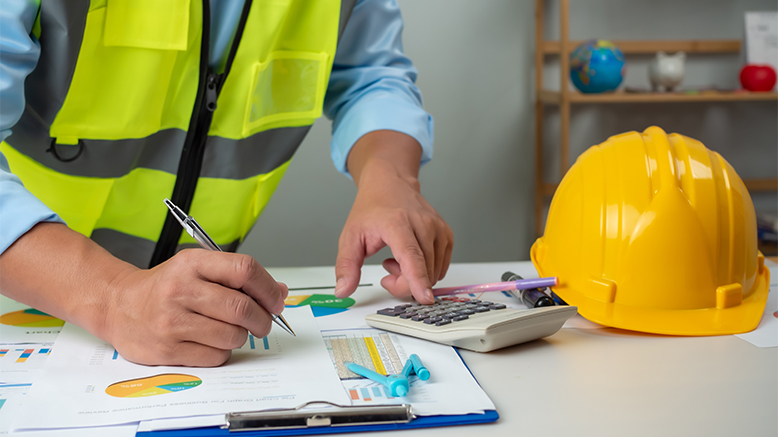
Mastering Construction Cost Management
Labour, materials, equipment, overheads – costs add up quickly in construction. With the constant pressure to deliver projects on time and within budget, tracking expenditure is crucial. This is where...