— 5 min read
Reporting Deficiencies in Construction Projects
Last Updated Mar 26, 2025
Last Updated Mar 26, 2025
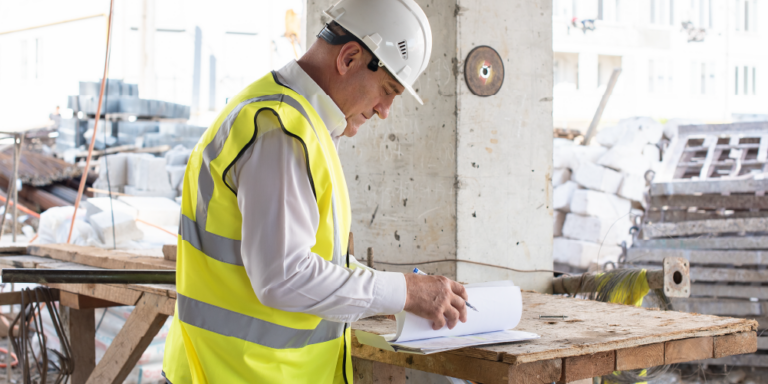
In construction, deficiencies - whether evident in preliminary planning or only after a project's completion - can lead to significant delays, cost overruns, and even safety concerns. This article explores what deficiencies are, why even small oversights can have far-reaching consequences, and how a systematic approach to identification and resolution can save time, money and reputation.
Table of contents
What is a deficiency?
Deficiencies in construction are issues that can be present at both the pre-construction phase or once a build is finished. In the preconstruction phase, a deficiency could be a lack of information or incorrect information. Examples could be quantities or dimensions of materials, like cubic metres of concrete required or the size of steel beams. These kinds of deficiencies would lead to problems down the line if they are not discovered and corrected at an early stage.
Once the build is complete, deficiencies that were not noticed and corrected during the project will have resulted in defects in the build’s finish or quality. These defects will need to be addressed before the project is ready to hand over.
I sat there one day going through bending schedules and the governor said to me ‘You’re wasting your time doing that, we’re paying engineers.’ The thing is, I’d already noticed a problem, and it takes three weeks to get the bars made — so if we didn’t address it then, we’d suffer a bad delay.
Kevin Davenport
Technical Construction Consultant
Risks of Deficiencies
As with the bending schedule example, a deficiency in information can cause major problems for a construction project. Deficiencies in information about materials, like size or quantities, can lead to huge delays because of the long lead times for some materials that can take weeks to get delivered. Or they can require rework if tasks are done incorrectly.
Delays in deliveries are likely to affect the project schedule, which may mean handing over the project past the deadline. This can incur late fees or other penalties as set out in the contract. Contracts will often contain a ‘liquidated damages’ clause for late delivery, which means paying the client a set sum for every day it is late. In addition to penalties, there’s also the cost of reordering the materials.
That’s why it’s so important to go over your schedule, your Bill of Quantities and your contract with a fine-tooth comb before you even start doing the work. Spending two hours looking at documents might feel like a long time that could be better spent getting on with the work, but that time can save you days, weeks or even months of delays. It’s always worth it.
Deficiencies can cause problems besides delays and extra costs too. If deficiencies are not noticed in the information and documentation, they can lead to serious issues with build quality and safety. This can cause structural failures that lead to worker injuries or hazards such as fire risks.
There is also the risk to your reputation — if deficiencies lead to delays or poor quality, it is unlikely that a client will recommend a business or commission more work. Worse still, the client may take legal action.
To summarise, some of the main risks of deficiencies are:
+ Schedule delays
+ Cost overruns
+ Rework
+ Quality and safety issues
+ Reputational damage
+ Client dissatisfaction
+ Legal action
Shape the Future of the Built Environment at Procore's Construction Summit
Engage with construction leaders and discover the latest technology and best practices that are driving change across the industry.
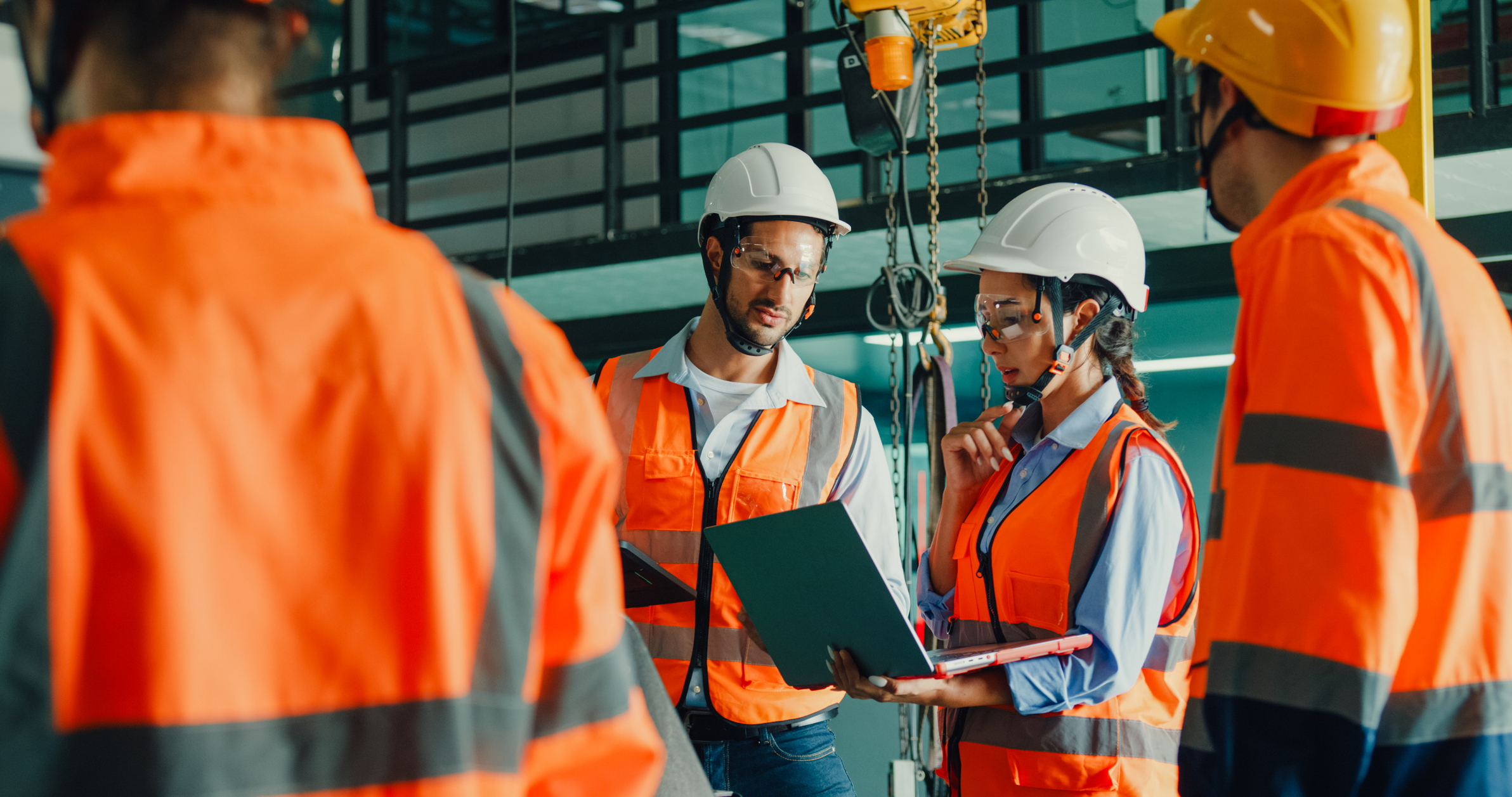
Reporting Deficiencies
Every company has their own way of reporting deficiencies, and there’s not a simple one-size-fits-all process. Everyone has their own IT system which will have different ways of documenting a deficiency, and there will also be conversations and meetings to have where you discuss these issues. It’s really important to understand the system at the company you’re working for, especially if you’re a consultant or sub-contractor. You might have your own way, but you need to know what the accepted process is.
When you’re a consultant, you get parachuted into an office and everyone runs their own system. So the first thing to do is to talk to people and look at the technology to understand how each company handles their deficiency reporting.
Kevin Davenport
Technical Construction Consultant
Sometimes deficiencies just get reported in meetings — with the technical director, for example — where you will sort out ordering materials or consulting the design team to correct a deficiency before it’s too late. Sometimes companies report these things over email or through a specific software or platform. If a deficiency is going to affect a number of projects, you may even need to alert the MD to make them aware of the potential knock-on effects.
Many sites these days have tablets with construction management platforms where they can easily and quickly report deficiencies by ticking boxes and sending automated messages or forms that contain information about deficiencies. These then get fed back to the appropriate team, who can then call and ask questions about the problem to solve it.
Collaboration and Interpersonal Skills
The human side of working together in a team is important for managing and reporting deficiencies. People have different levels of experience. Some people can spot deficiencies very quickly and easily. Others have to look a bit harder and some need deficiencies shown to them to develop their skills. Whatever the level of experience, there is always something to learn. Done correctly, investigating and reporting deficiencies can be a useful learning opportunity for newer staff.
I had a trainee once who was managing the build of six houses, and I told him to print off the drawing and pin them up in each house. He didn’t do it, for some reason. A couple of weeks passed and I asked him how it was going. He said things were great, until I pointed out a whole load of deficiencies. That was a memorable way to learn that lesson!
Kevin Davenport
Technical Construction Consultant
To err is human. What matters is putting things right when there are deficiencies. The identification of deficiencies can be a good learning opportunity, but it can also be a very stressful situation. Sometimes personalities can get quite heated. It’s important to de-escalate the situation, let people know that everyone makes mistakes, and encourage good communication in these instances. That’s where having a proper, systematic process to identify, document, report and resolve deficiencies can really help.
Categories:
Tags:
Written by
Kevin Davenport
View profileReviewed by
Nicholas Dunbar
29 articles
Nick Dunbar oversees the creation and management of UK and Ireland educational content at Procore. Previously, he worked as a sustainability writer at the Building Research Establishment and served as a sustainability consultant within the built environment sector. Nick holds degrees in industrial sustainability and environmental sciences and lives in Camden, London.
View profileExplore more helpful resources

Construction Document Software: Essential Tools for Project Success
Construction projects depend on extensive paperwork, including designs, contracts, RFIs, and compliance records. A single misplaced document can trigger delays, disputes, or compliance violations. Despite increasing digital adoption, many teams...
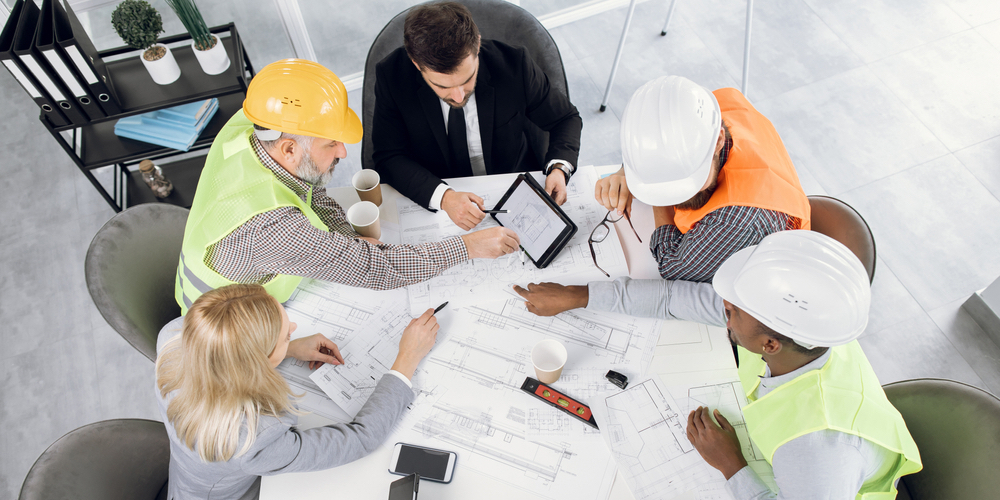
Construction Planning: A Guide to Successful Project Execution
Every successful construction project begins long before the first brick is laid. Indeed, behind each structure – whether a towering skyscraper or complex infrastructure project – lies a carefully crafted...
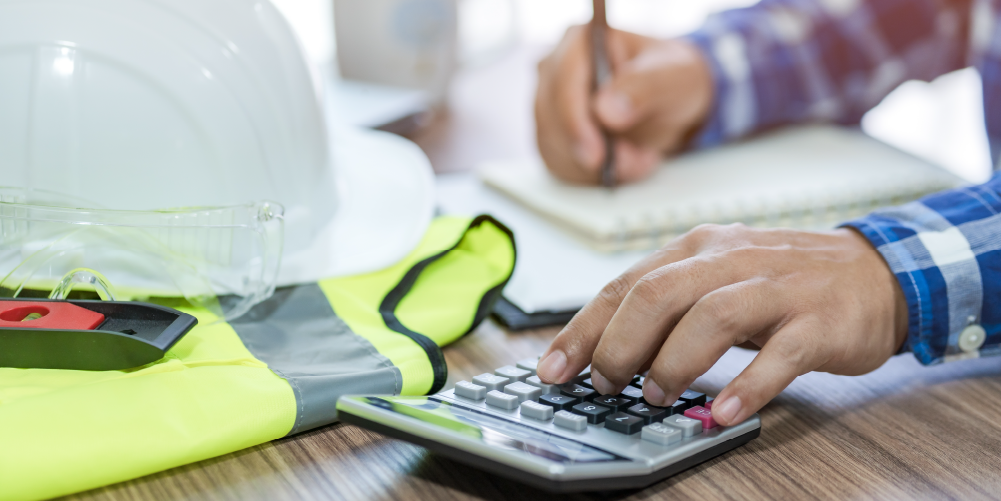
Leveraging Analytics for Better Financial Forecasting in Construction
Financial forecasting is a difficult task in any industry. In construction, where companies need to manage volatile material costs, labour shortages and variation orders on a daily basis, fluctuations in...
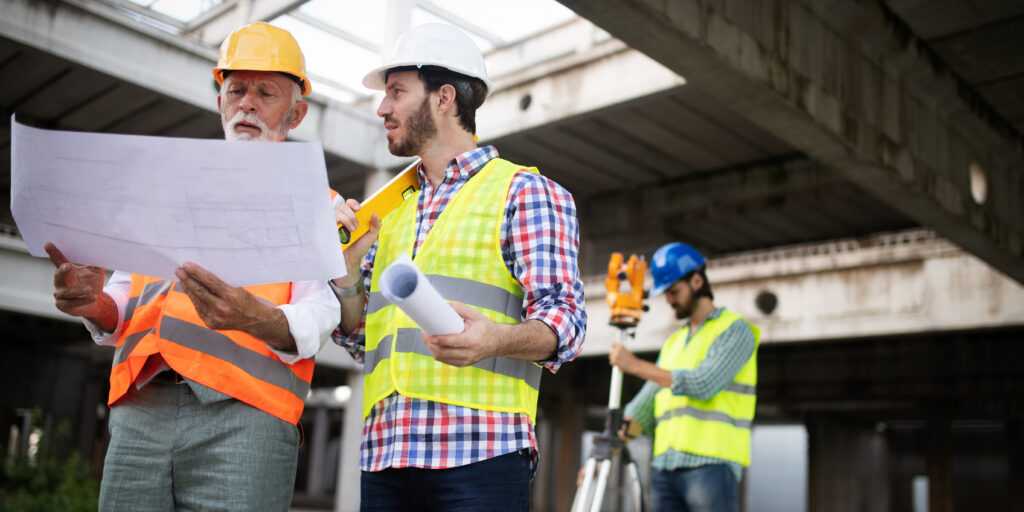
Strategies to Prevent Rework: The Importance of Clear Instructions
In construction, “rework” is the dreaded process of redoing tasks due to mistakes, quality issues, or safety concerns. This unnecessary work drains budgets through wasted materials and labour while causing...