— 7 min read
Resource Coordination in Construction
Last Updated Mar 26, 2025
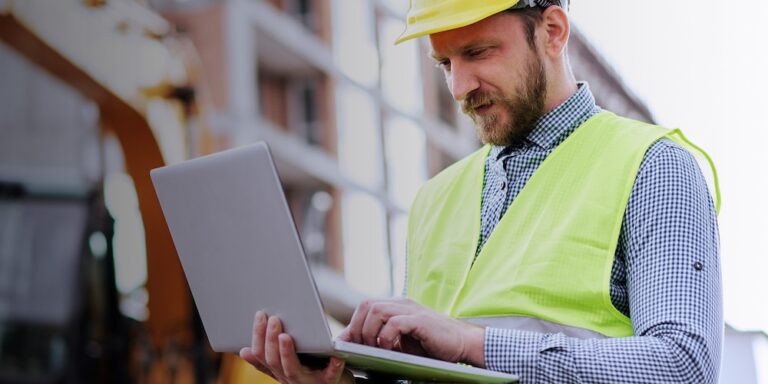
Resource coordination is the process of making sure that all the necessary resources—people, materials, equipment, and more—are ready when and where they’re needed.
This article takes a closer look at how resource coordination works in practice, why it matters, and how effective communication can mitigate the risks when things don’t go as planned.
Table of contents
What is resource coordination?
Resource coordination refers to the process of planning out and making sure that you have all the resources that you need to successfully complete a construction project. There are many different types of resources in construction, including:
- Labour: the people who will do the work
- Materials: the bricks, glass, concrete, timber (and so on)
- Equipment: the machines that workers will use on site
- Designs, drawings and specifications: the plans people work from
- Budget: the money allocated to procure what’s needed for a project
Resource coordination is part of a big picture. To be able to complete a project and hand it over on time, on budget and to the highest level of quality, you need to coordinate the required resources ready for each key milestone of the build. This involves making sure you have the right amounts and types of resources, at the right quality and at the right times.
Say I'm going to procure steel work — these are some of the questions I have to ask: What was the initial design? What was the proposal? Have the design and proposal been verified? Are there approved suppliers? Where are they located? Have we confirmed deliveries and logistics? What are the risks?
Richard Attwell
Power Engineering/Construction Management/Business Strategist
Learn about the future of the built environment - Read Procore's Future State of Construction report
Learn how contractors, subcontractors, and project teams can take advantage of new opportunities to boost efficiency and profitability over the next decade. Download the report to get your roadmap to the future state of construction.
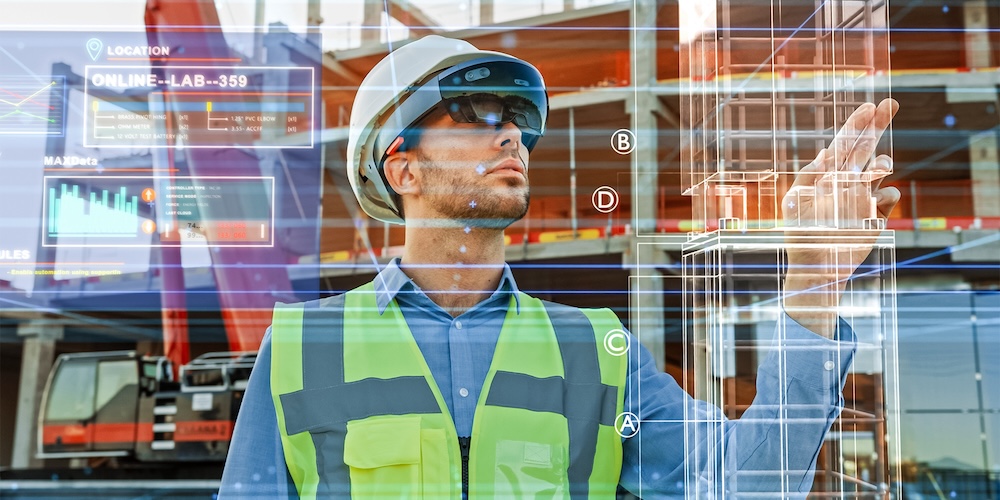
Key Aspects of Resource Coordination
Making sure you’ve got the appropriate resources for a project helps you start the work in an organised, efficient way. You’ve also got to have a full understanding of the scope of works and the responsibilities of your team before you can evaluate whether you’ve got access to the needed resources for a job. Your deliverables (what you will hand over at the end of a project) should align with a predefined schedule or programme of works, the delivery schedule, the Bill of Quantities, technical specifications and a quality plan or Inspection and Test Plan (ITP).
A deliverables schedule can help you to coordinate resources in line with key milestones. This is a schedule that helps you visualise when all your milestones and deliverables need to be ready by. It gives you timescales and warnings to keep things on track. With software, you can also link it up with your documents and capture spend, which help you have a full view of the project. This is an area where AI could really help to speed up and simplify things, but it’s worth the upfront time investment regardless.
It’s not just about the procurement — it’s also about the business itself, the management structure, the employees and the network of subcontractors you’re going to use.
Richard Attwell
Power Engineering/Construction Management/Business Strategist
Managing relationships suppliers, stakeholders and expectations is an under looked part of coordinating resources. The coordination of resources, and subsequently the success of a project, can be affected by poor communication and relationships between different parties, whether that’s with subcontractors, suppliers, team members or the client.
Communication and Resource Coordination
As we just touched on, communication has a significant impact on coordinating resources properly. If you’re a project manager, it’s essential that you develop good, ongoing communication with everyone you work with or manage to get a project completed. You will have to delegate some responsibilities when coordinating resources: you can’t do it all on your own. To do this successfully, you need to make sure that you communicate every detail that needs to be understood: don’t leave any room for assumptions.
Regular meetings where you discuss, for example, the status of deliveries and availability of materials and labour are a great way to communicate effectively with the team and keep your coordination efforts on track. It’s also a good idea to ask someone to take minutes at these meetings so you can both focus on the in-person conversation and have a record of any issues that come up or decisions that are made.
Take other opportunities to communicate with your team to check that things are well coordinated, too. One great opportunity for doing this is when people sign in and out of the site. It gives you a chance to build relationships in a less formal situation than a meeting, and to keep tabs on potential issues with resources.
Almost all construction projects will be impacted by variations or changes, and often this is to do with resources. For example, a particular material could be unavailable or there could be unexpected labour shortages. In these situations, it’s important to discuss these challenges as soon as they arise so that you can problem solve and make a decision that will reduce the impact of the change. It’s perhaps even more important to effectively communicate that change with everyone it will impact to make sure that work will continue smoothly.
Early Warning Signs of Resource Coordination Issues
In a perfect world, doing all of the work to prepare and coordinate your resources at the beginning of a project will prevent any chance of issues down the line. However, there are often situations that impact your resources that you can’t necessarily predict. These could be supply chain problems, weather-related issues, equipment failures and any other circumstance outside of your control that you have to troubleshoot.
I once managed a project where on the final day of testing, a test vehicle which had travelled from the Netherlands failed. The supplier estimated repairs would take 6 days, and said they needed to be done in the Netherlands.
Rather than accepting this delay and disappointing the client, I discussed the issue with the contractor, supplier and site team and used my technical knowledge to provide and modify alternative equipment. My positive outlook and the team’s collaboration helped us reach a successful, rewarding outcome.
Richard Attwell
Power Engineering/Construction Management/Business Strategist
It doesn’t have to be a big event like that, however. Less far-reaching circumstances, like issues with measurements or specifications, a company going out of business or a staff member needing sick leave, can also have effects on resources.
You’ve got to look out for specifications changing. I once had a product delivered that had a discrepancy in size of only a millimetre because of a change to the specification range, but it was the same product used many times over the years. Checking the specification against the physical product before installation avoided extensive delays and costs.
Richard Attwell
Power Engineering/Construction Management/Business Strategist
There are some metrics that you can track to make sure that you have some idea when you might face a problem and need to course correct to maintain a good level of coordination. Continuously checking work against your ITP and materials list of Bill of Quantities will highlight if there are any materials issues.
It’s really important to focus on what is needed in an ITP or Quality plan. Just using examples from other projects can prove to be catastrophic, time consuming and costly. Understand the full purpose of the ITP and challenge your client or team if you have any doubt. Your regular progress, client and Safety, Health, Environment and Quality (SHEQ) meetings are another opportunity to keep an eye out for any problems that may affect resourcing.
If there are any early warning signs, being organised and able to provide clear facts and suggest solutions is important. You need to react quickly, but also have a thorough and detailed explanation and solution so you can reassure the client you’re on track to resolve any issues. That could mean presenting potential alternative suppliers or subcontractors, revised schedules or alternative materials for them to approve. Don’t just turn up and tell them that you’ve got a resourcing issue without a Plan B.
Categories:
Tags:
Written by
Richard Attwell
Richard Attwell, MIET, is a seasoned technical specialist and senior-level leader with over 40 years of expertise in power distribution, focusing on underground high-voltage cables. He has managed multi-million-pound engineering projects, shaped innovative business strategies, and excelled at staff training and development. Known for his methodical approach and strong leadership, Richard consistently drives operational efficiency, nurtures growth, and delivers high-quality results across the power distribution industry.
View profileExplore more helpful resources
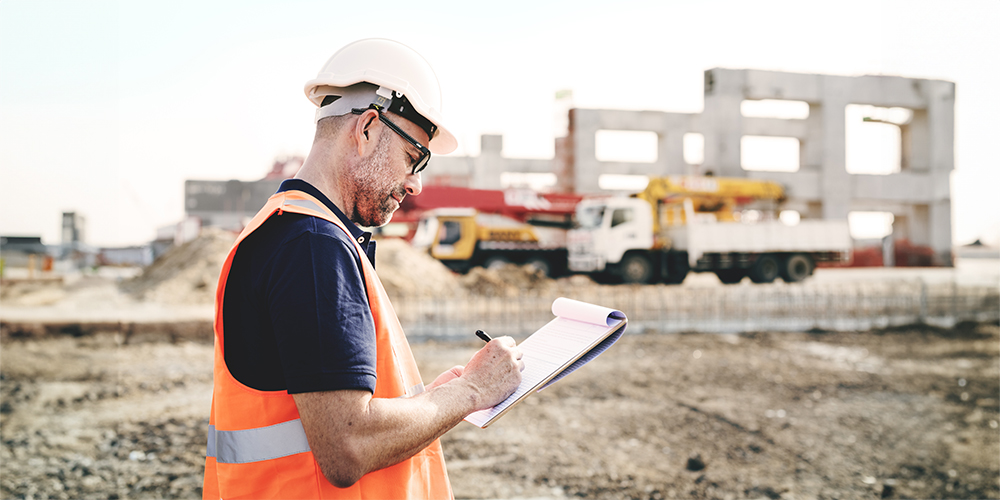
Meeting Industry Standards: Strategies for Enhancing Construction Quality
Like safety, quality is one of the pillars of construction where sacrifices should never be made. In fact, sacrificing quality can ultimately become a safety issue — the two are...

How Unified Data Transforms Construction Projects
Construction teams generate vast amounts of valuable data that reveals critical details about their work. However, many struggle to harness this information effectively. In today’s construction industry, teams face mounting...
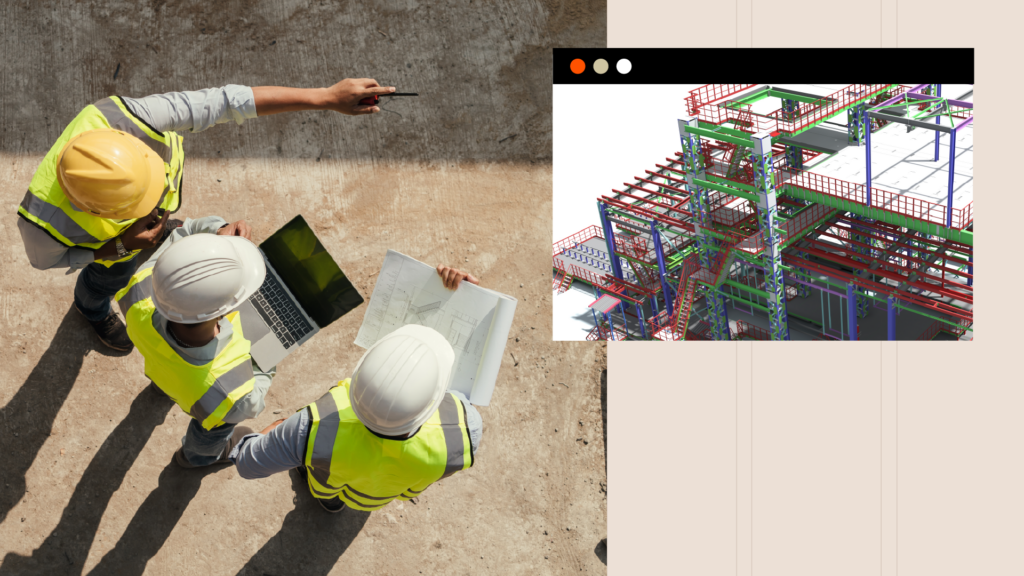
Building a Future-Ready Workforce Strategy
A record £37 billion of publicly funded projects will break ground across the UK in the next three years, yet CITB forecasts a shortfall of 225,000 construction workers by 2027....
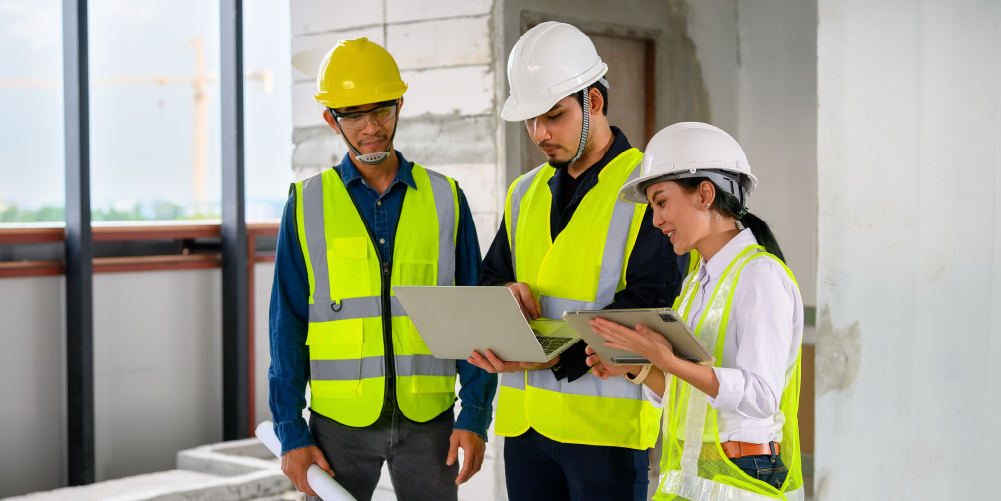
Preventing Construction Disputes with Smart Contract Management
A Strategic Framework for Modern Construction Humans have always built megastructures with pride. From the Pyramids of Giza to Dubai’s Burj Khalifa and Saudi Arabia’s NEOM, there will always be...