Procore set out to find the companies, projects and individuals that stood out for their bold achievements in construction. Among the 24 outstanding finalists selected, eight were named winners of the 2021 Groundbreaker Awards. This article is the third in an eight-part series spotlighting each winner.
Technology is foundational to construction, and not just in terms of better batteries and digital design processes. For Mike Maierle, founder and principal of the 2021 Groundbreaker Winner of Excellence in Innovation, ETRO Construction, technology is a way to help construction professionals return to their roots, allowing them to spend more time building and less time managing redundant processes.
“I left my previous position six years ago today,” said Maierle. “I started this company because I wanted to build something of my own, something innovative and fresh. I wanted to bring together the best and brightest, people who’ve come from different avenues, and focus on creating and mentoring a generation of construction professionals who will do things differently. I want to focus on being a builder—that’s something that has gotten lost in the world of construction management.”
Growing pains
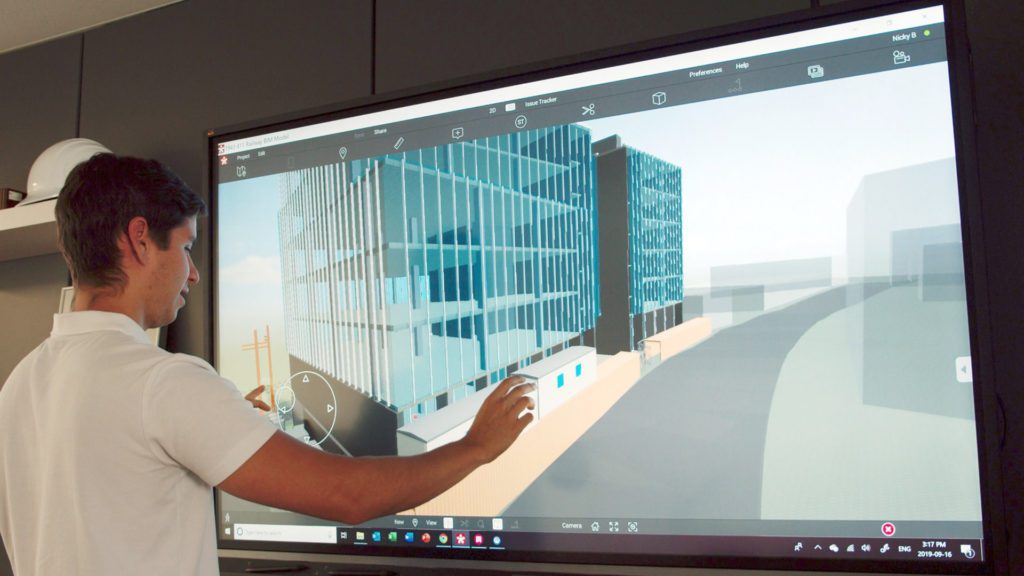
Like any startup, the Vancouver-based ETRO started small, taking on projects with budgets under $5 million. Soon, however, “that five turned to 20 and then to 40. Our largest project is $75M, but we’re working on proposals in the $100-200M range. We’re really scaling up,” he said.
Growth really took off in 2018. That’s when Maierle decided that if he was going to build a next-generation construction company, some of the old ways simply had to go.
“When I grew up working in this industry in a job site trailer, it was normal to go home at 7:00 or 7:30. You’d be fighting all the paper and the checklists, doing the same work multiple times due to repetitive data entry and really, really poor technology tools. Back then, Contech just hadn’t ramped up in the same way other industries had,” he said.
“We wanted to create a business that was focused on getting people home to their families, not only safely, but at a reasonable time—cutting out all the nonsense work. If your whole day is spent filing through paper and documents and drawings, you’re not going to really understand how to build,” Maierle emphasized. “People are forgetting about the root of who we are—we’re builders; we’re craftspeople.”
Perhaps the most important tool the company built to make this happen is the ETRO Milestone Tracker, or EMT.
To meet major and mini-milestones
Maierle recalled frankly that their custom built solution stemmed in part from challenging project experiences.
“We had a tough year—a couple of projects didn’t go perfectly,” he said. “We needed to find a way to track what I call ‘mini-milestones.’ We were missing some, which caused us to miss the larger contractual milestones. We needed a tool that created accountability and transparency. So, we put our heads together and built one, and it launched late last year.”
Easily accessible to managers, designers, on-site workers and supervisors, even clients passing through the lobby or job site, EMT shows an up-to-the-minute accounting of major and minor tasks in unsparing detail. These “mini-milestones” can be something as simple as the delivery of specific materials, without which prevents the project from moving forward.
All the data is collected through a single web tool that can be accessed or updated at any time, from anywhere. It also integrates closely with other platforms ETRO uses regularly, such as Procore, Slack, Google Calendar, and Microsoft Project.
With EMT, you can easily see and contextualize issues not only separately but also as trends. If there’s a growing delay on the concrete cycle, the data is there to look back over the week, find the problem, and take action. If a team’s missed a milestone, but EMT shows 95 percent completion, knowing it’s just a minor slip can ease everyone’s minds. Of course, being ahead of schedule also shows up—something that’s happening increasingly as technology advances.
Maierle estimates that the development of EMT cost the company $100K, but it has already paid for itself in various ways. Most importantly, it saves time and gives people a better sense of the status of multiple projects.
“You have someone with 35 years of experience sitting in a trailer on a single job—I don’t think that’s the right model anymore,” Maierle said. “We need those people being able to mentor three teams, but not spending four hours in traffic, right? What a waste of a valuable resource.”
Toward digital twins
Advantages are already trickling down to trade subcontractors, who are generally still in the Excel era, showing better project management can be far more effective and efficient. However, Maierle is nowhere near finished innovating.
“We started experimenting with lidar and laser scanning, giving us a tremendous amount of data which provides our clients not only with quality assurance but precise as-built documentation,” he said. “We still need boots on the ground there, but these scans are great for transparency. I can do a full walkthrough of a project from my office, so digital twins are definitely where we’re headed next.”
Meanwhile, it all takes place under a lean management style that emphasizes sharing information, lessons, and staying as agile as possible. “It has all paid off as we are able to attract world-class talent to our forward thinking organization,” Maierle said with pride.
“This industry has been struggling to innovate for years, and we want to be the example that everyone strives to be. I’ve got four young children, and I want them to be builders. However, if the industry hasn’t evolved by the time they’re ready to start their careers, I’d much rather them focus on an industry that is more progressive.”
Leave a Reply