Specialised Ellenbrook Solar (Photo: Solgen Energy)
Many of Australia’s construction companies rely on a fleet of subcontractors and installers to help them build. Everyone involved in a construction project needs to understand compliance—and stay ahead of what seems like a never-ending compliance curve.
Paperwork-heavy systems traditionally used for compliance may appear to be effective. In reality, however, they take time, effort and are more often than not inaccurate. Without digital automation, you may struggle to reach and then maintain compliance. For solar-power engineering expert, Solgen Energy Group, resolving the issue of document and version control transformed its compliance capabilities—and introduced new compliance KPIs clients love. General Manager for Project Delivery at Solgen Energy Group, Clayton Eigenmann shares why staying ahead of the compliance curve has been good for business.
How Information Becomes Knowledge
While Solgen relied on digital systems, it still needed to automate its processes. Namely, it needed to change the way information was captured to build an internal compliance knowledge bank. Before Procore, Solgen was effectively acting as a conduit to the hundreds of subcontractors and installers it relied on across Australia. When clients wanted to know the status of a project, the company had to call contractors for updates.
“Previously, relying on emails, shared folders and multiple spreadsheets meant no real-time site updates and ineffective collaboration,” Eigenmann said. “We also had conflict risks around document control and project drawings. Implementing Procore enhances all of our value-adds and gives us real-time updates and access to safety documentation, inspections and observations. We use Procore from tender site inspections to project delivery and post-project delivery.”
Creating New Compliance Behaviours
Solgen found once Procore was implemented, other changes followed. Solgen project managers and project engineers now start their day ensuring site teams have executed daily pre-start forms, risk assessments and documented any site meetings.
“Anytime anyone goes to a site they use Procore for site risk assessments and take photos to make sure they are stored with summary reports,” he said.
Building a Compliant Safety Reputation
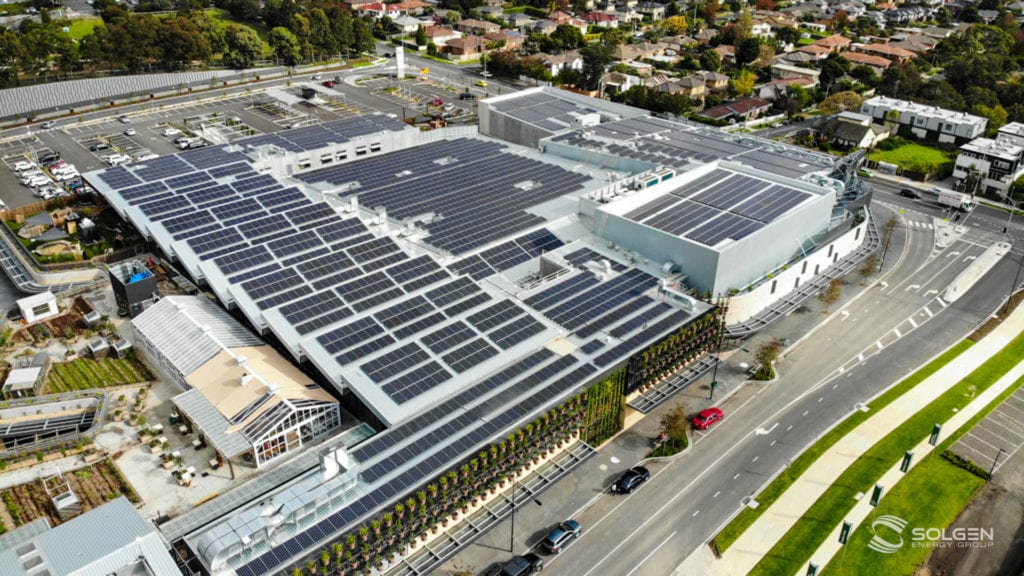
The implementation of Quality & Safety has innovated how the company approaches safety compliance.
Eigenmann explained all site personnel with access to Procore are now part of the new Solgen Safety Collaboration Unit. Anytime an incident occurs, they share safety alerts with all staff, not just the people involved.
“We have 100% confidence that our safety processes are being documented. Everyone has been trained to access and execute safety documentation and understands the impact of ISO compliance for all project stakeholders. This mandate and our on-the-spot audit capability by any project stakeholder have raised the bar on our culture and commitment to safety.”
Extending Procore with the Correspondence Management tool has been key to staying on top of the game. Eigenmann believes precisely this functionality is delivering higher safety standards and better quality projects.
“We have set up an operational KPI report that tracks main project delivery components including cycle times, engineering times and safety KPIs. It frees us up to focus on our compliance benchmarks.”
Improving the Attitude to Compliance
Procore is a hit with Solgen’s client base who appreciate it’s one-stop-shop capabilities for all project-related information. From issuing drawings to product submittals, everything is easy to access. Clients can go on-site, identify a hazard or create an observation, and receive consistent updates until the issue has been fixed.
With safety compliance being a crucial element to Solgen, the company manages compliance with its subcontractors very differently.
“Our subcontractors can’t hide or avoid documenting safety awareness now that we’re using Procore. They must use it, and we have had a 100% improvement in attitude towards the importance of safety,” Eigenmann said.
“It’s natural for project management to focus on completion. However, we believe that it should be compliant completion. We know people may move on from paperwork once it’s submitted, so that is why we verify all safety incidents have been reviewed by site personnel the next day. In essence, they need to be reviewed and signed off before pre-start the next day.
“It’s clear safety awareness has increased, and this supports our Solgen Safe initiative. Our sub-branded program means our safety documentation and alerts are known for being something we take very seriously.”
Leave a Reply