Photo: Form Building Developments Ltd
Historically, the construction sector has faced higher work-related injuries and costs than any other industry. However, the days of building with outdated quality and safety standards and expecting improved outcomes are long gone. If you can understand, predict, and correct quality and safety issues while building, better quality outcomes become possible in a safer environment.
For Form Building Developments Ltd in New Zealand, this approach doubled the efficiency of its safety measurements and benchmarks. Sarah Ross, Business Improvement Manager, explains why Form advocates removing manual project management processes to deliver new efficiencies.
“We implemented Procore to support better document management,” Ross said. “Procore has grown to become the backbone of our project management and quality assurance system. We now have one single digital platform and a streamlined way of operating.”
Project the Outcomes
According to Ross, the implementation of Procore Project Management helped Form resolve its document management challenges, supporting a myriad of best practice outcomes.
“First, we standardised digital processes and provided greater transparency for staff emails. Moving our team away from error-prone manual processes into Procore meant tasks were automated and monitored in real-time, giving us a much clearer indication of what we should be focusing on.”
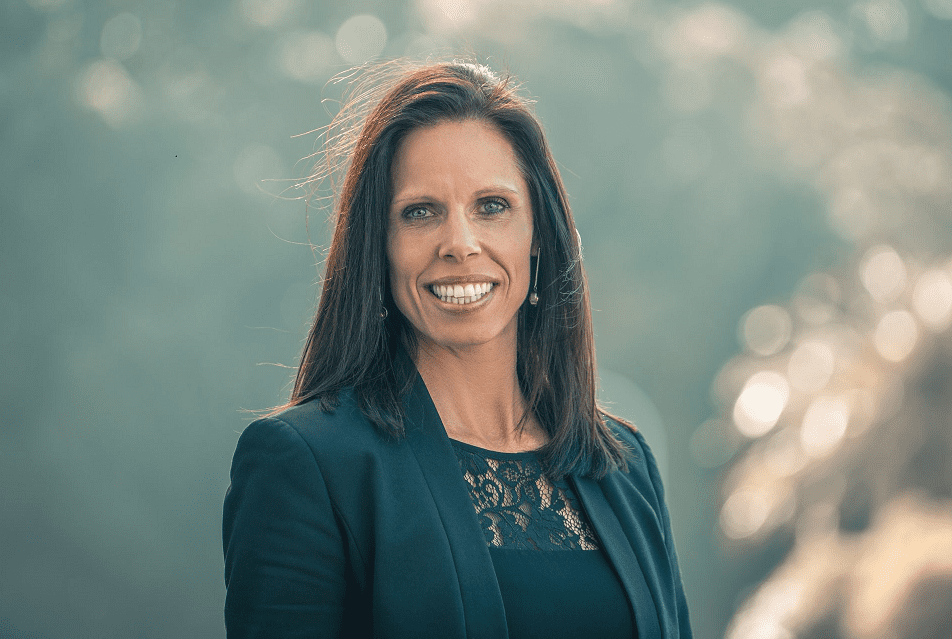
Form’s System and Compliance Advisor Carl Newman explained the company achieved this by setting up Procore to mirror its project management approach. This way Form didn’t have to make too many changes to the way its team worked.
“You could say this was an easy transition. With Quality & Safety today, we automate and measure quality outcomes in real time,” Newman said. “We can react to changes as we need to and measure our quality benchmarks via two different processes.”
Streamlining Options for Maximum Results
Form found offering two options for measuring quality meant the team could choose the monitoring and reporting best suited to their work style—with the same outcomes.
Newman explained the first solution is based on a list of questions guiding the project manager through the physical build—matching the outcomes against the initial design standard.
The second option targets specific jobs. It is a customised Quality Assurance cheat sheet, instructing project managers and asking for evidence to support the recommendations.
“You just have to set up the cheat sheets for these jobs and then get the project underway.”
Better Risk Controls
The implementation of Quality & Safety means it has become easier to track QA across the business on a week-by-week or month-to-month basis. Newman is now able to investigate a drop off in QA and avoid the issue of seeing “the risks on a project increase.” Now the team can see it and act on it straight away.
The company can also improve safety outcomes and get better insights by integrating additional tools with Procore. This is particularly apparent with SignOnSite; this integration, according to Newman, “saves time and provides better insight into incident reporting”.
He believes it is this integration that best supports both the review of incident data and site-by-site reports without having to collate and manipulate underlying information.
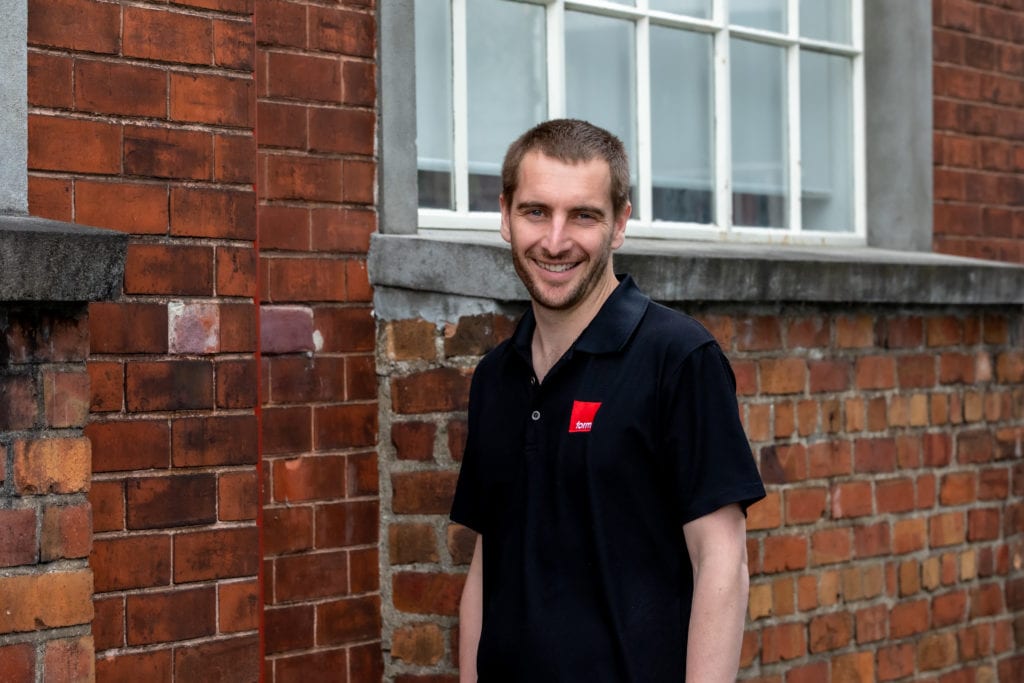
“The days of counting our site staff-hours and submitting them are gone. We know who is where and when, and this saves us a lot of time.”
Form is also now looking at the incident data and investigating the type of incidents and their location. It’s given the team the ability to focus on the improvements that are required and not take a “haphazard approach to safety.”
“At the end of the day, this is why we have been able to increase our safety benchmark by 200%.”
Leave a Reply