A Robins & Morton construction crew surprises a 10-year-old hospital patient with a birthday banner.
Over the last few months of quarantines, stay-at-home orders, and social distancing, glimmers of good news have been hard to come by. Still, despite the tsunami of economic and operational challenges brought on by the pandemic, many construction companies are going above and beyond to help their communities, from donating N-95 masks to taking on projects to help hospitals overwhelmed by the influx of COVID-19 patients.
One company that knows all about such efforts is Birmingham, Alabama-based Robins & Morton. The construction firm turned to its healthcare clients to find out where and how the company could provide the most help and have the biggest impact.
In The Eye Of The Storm
As states and health systems scrambled to ensure there would be enough rooms to handle a massive spike in admissions due to COVID-19, alternative solutions were devised out of necessity. To help hospitals manage the expected overflow of patients, temporary facilities had to be constructed.
One such project had Robins & Morton erecting temporary tents that provided testing and served as a triage site outside Broward Health North in Pompano Beach, Florida. The setup also served as a place to safely isolate patients awaiting test results.
“It’s not often we’ve been in a pandemic scenario like this,” said Johnathan Peavy, Robins & Morton Senior Project Manager. “We knew our clients needed some help, and we felt as experts in the healthcare construction space we could lend our services to them.”
Another project involved building a 500-bed hospital unit inside the Miami Beach Convention Center for the Army Corps of Engineers. Robins & Morton transformed half of the convention center’s 500,000 square feet into a fully-functional temporary hospital, complete with 400 acute care patient rooms, 50 isolation rooms, nurses stations and support areas.
Far from just a basic setup with room dividers and little else, the convention center hospital included necessities like medical gas lines, plumbing, electrical, and data wiring.
“Even though they’re temporary facilities, you’ve got to give them the technology and capabilities to function like their day-to-day routine. You can’t go back to a field army hospital with limited connectivity,” Peavy explained.
Given the fluidity of the situation and the project’s race against time to beat the pandemic’s curve peak, the team had to stay on their toes.
“A lot was learn-as-you-go because new information was coming out from the medical field on how to best treat these types of patients. It was an ever-evolving situation as we got new information day by day, and we made adjustments based on the changing needs, including finding the resources you need to make those modifications. That was a big challenge in and of itself,” said Peavy.
To ensure the team had the equipment and materials required to complete the job in the time allotted, the company relied on a network of suppliers. They saw everything from locally sourced materials to juggling overnight shipments from as far away as California and Canada. Peavy described it as a “massive logistical challenge,” particularly in a crisis time when everyone is clamoring for many of the same materials.
A True Community Effort
With more than 400 workers on the project, challenges like how to feed and shelter everyone had to be addressed. The company was able to ensure everyone’s needs were met thanks to some help from the local community.
“We contacted some local restaurants that were shut down and tried to utilize them to provide meal services, sort of helping the community stay in business while shut down. Luckily, we found a hotel next to the convention center that could house everyone. It was full community involvement, down to the police force helping us with logistics,” Peavy said.
Growth Through Adversity
As for what the team learned from these extraordinary circumstances, Peavy said everyone took something away from the project.
I think everybody who worked on this will have something to take away that will make them a better builder.
“You always say you’ve got to test yourself to see what you’re made of and if you’re capable of handling those types of situations,” he said. “I think after doing that type of project, when you go back to a normal project you think ‘Hey, I can handle anything thrown at me today.’ I think it’ll make everybody a little bit better.”
A Special Birthday Surprise
On another project at Duke Hospital in Durham, N.C., a Robins & Morton crew was able to pull off a birthday surprise for a young patient.
Reese had spent the last two birthdays in the hospital and was about to turn 10. For weeks he had been staring out his window, watching the construction crews at work, seeing heavy machinery (including a 550-ton hydraulic crane) come and go each day.
Reese’s dad wanted to do something special for Reese, so he approached the Robins & Morton crew and asked if they would help make Reese’s birthday a memorable one.
“He asked if we could put a banner for him on the roof. The next morning he told us that Reese loves cranes, and asked if we could fly a bike he bought Reese up to his window. We got approval from the crane company, and the guys rigged it up,” said Mike Dare, a Robins & Morton superintendent.
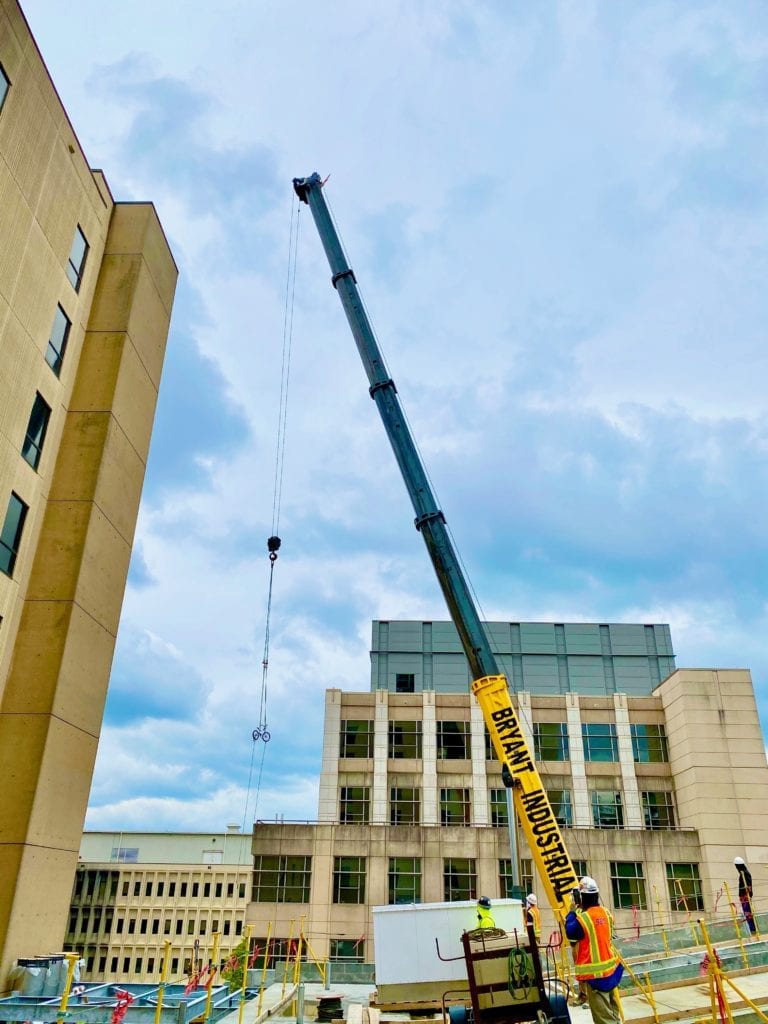
The crew went up to the roof and sang happy birthday to Reese, joined by his father, who was fully decked out in the same safety gear as the workers.
“Everybody on the crew got really excited and involved. We saw a complete shift in the team’s attitude on site. I think getting the team to band together for something like that really helped us get through the whole COVID situation,” said Dare.
Leave a Reply