Photo: Moriyama & Teshima Architects and Acton Ostry Architects
Wood has long been the material of choice for the construction of houses in Canada. Now, it’s gaining traction for builds of taller structures as well.
In particular, British Columbia has embraced the concept of using mass timber for builds of up to 12 storeys. Architects and builders are increasingly using engineered wood products like cross-laminated timber (CLT) and glue-laminated timber (glulam) for offices, school buildings and warehouses.
Why the Growth?
Mass timber is gaining popularity for tall builds because it’s a relatively clean, cost-effective resource. It’s plentiful in Canada and is reportedly better for the planet as it sequesters or stores carbon.
Growing trees draws carbon dioxide from the atmosphere and releases oxygen. In the process, trees use carbon dioxide to produce wood and lock away large quantities of carbon. When a tree is cut down and used as a building material, the carbon it sequestered is retained within its cellular structure. It is thus placed in a dormant state, removed from the atmosphere. David Wilkinson, principal of LMNTS Project Services Inc., believes these properties are “one of the beauties of mass timber.”
Wilkinson is a consulting project director for a $51.4-million, three-storey RCMP detachment in Fort St. John, B.C., that is being built of wood-stud framing and locally-sourced mass timber.
“We were careful as we evaluated it as an option. We found that some people consider it a fad, but mass timber is a great carbon sequestration strategy,” he said. “You’re hanging onto tons of carbon.”
Another bonus of mass timber, explained Wilkinson, is that it has a lower carbon footprint as the wood is sourced in B.C. and will not have to be trucked over long distances to reach the building site. Large sections of the building are also pre-fabricated in a factory and can be assembled on-site like Lego.
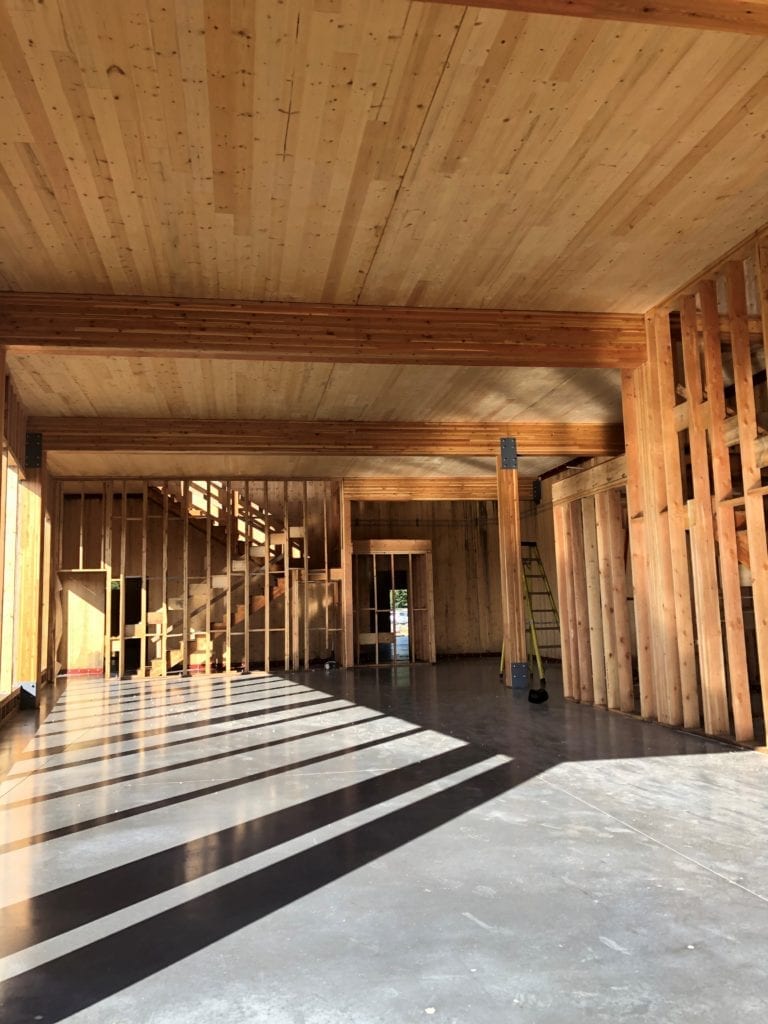
“The thing about mass timber is that it’s an off-site manufacturing product. Because of that, it’s all manufactured using CNC machines to a tolerance of two millimetres and comes together as a kit of parts that get literally screwed and bolted together,” said Tom Moore, founding partner at Studio 531 Architects, lead designer on a distinctive large warehouse made of CLT and glulam in Langford, B.C., on Vancouver Island.
“It saves significant time in terms of erection, so you reduce the costs of the general contractor, and you diminish financing and interest costs.”
Provinces Taking on Timber
B.C. has been the standard bearer for the adoption of mass timber and was the first province to raise the height for wood buildings to 12 storeys. The province has created projects like Brock Commons at the University of British Columbia and the Wood Design and Innovation Centre in Prince George. The Province of Alberta also allows wood builds up to 12 storeys.
Both provinces have approved changes allowing taller wood builds ahead of an impending update to the National Building Code which is expected to allow for wood builds of up to 12 storeys.
Ontario Making Strides
Ontario has not yet taken steps to raise its six-storey limit for wood builds. However, the Residential Construction Council of Ontario (RESCON), representing more than 200 residential builders in the province, is urging the government to raise the standard to 12 storeys in line with the national code.
According to a draft Ontario Forest Sector Strategy (FSS) called A Blueprint for Success, the province has been consulting with Indigenous, municipal, and industry leaders and is looking at ways to expand mass timber use in Ontario buildings and open new markets for wood product manufacturers.
The strategy notes that the province has supported four tall-wood demonstration projects: a 12-storey Arbour development by George Brown College; a 14-storey Academic Tower at the University of Toronto; a 12-storey residential condominium building in North Bay; and an eight-storey office building in Toronto.
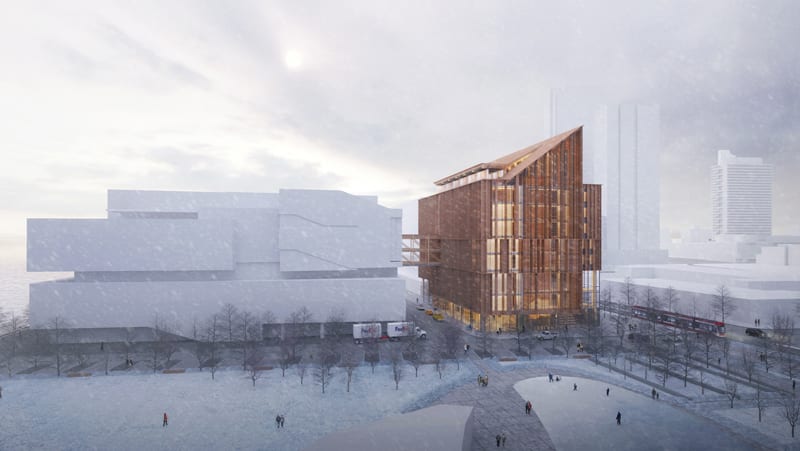
Photo: Moriyama & Teshima Architects and Acton Ostry Architects
While RESCON president Richard Lyall said the organization commends the province for supporting those projects, he noted that Ontario’s building regulatory environment still lags well behind other Canadian and international jurisdictions.
“To that end, more needs to be done to update the Ontario Building Code as well as related code compliance and enforcement systems,” he wrote in a letter sent to staff at the provincial Ministry of Natural Resources and Forestry.
According to Lyall, RESCON strongly supports using more wood in taller residential buildings. The organization believes Ontario should allow for all construction types that meet the very high safety and energy efficiency requirements.
“Introducing the option of using more wood will provide industry-wide benefits as it will increase competition resulting from more choice and more options,” Lyall said. “Should a builder switch from steel or concrete to a wood-structured system for certain types of taller buildings, the (Ontario) Building Code should be aligned with international best practice and should not be an obstacle to safe, energy-efficient construction.”
Benefits of Timber
A study entitled Wood, Well-being and Performance: The Human and Organizational Benefits of Wood written by Labour Market and Policy Consultant Graham Lowe, reports there is mounting evidence that mass timber can contribute to the occupants’ better overall health.
“Research conducted in a wide range of disciplines points to the same evidence-based conclusion: wood is good for the environment, for people and for organizations,” he states in the report.
Leave a Reply