All residential buildings in Australia generally need some form of insulation to meet the National Construction Code requirements for energy efficiency and thermal performance. So which products work best? Is there anything new on the market that will help you score the necessary number of stars?
The most advanced approaches to insulation might not even be about choosing a specific type of batt or foam. According to Jesse Clarke, building science manager for Pro Clima Australia, it is best to consider the whole building in terms of systems, rather than a kit of installed products and parts.
The Three Key Things
Clarke says there are three basic principles of building science at play when thinking about wall systems and insulation: heat, air movement and moisture. The goals are to reduce heat gain in summer, reduce heat loss in winter, control air movement that can cause heat gain or loss, and prevent the build-up of moisture from weather ingress, condensation or water vapour from occupant activities.
The standard formula of treating a wall as a collection of parts can limit the choices a builder has for insulation products. Clarke explains that a conventional brick veneer build, for example, where the brickwork can be erected quickly on the outside of a timber or steel frame, is suited to low-cost fibrous insulation types like batts, which can be installed between the studs. That insulation may not be as effective as you might think, though.
“There are often gaps around cables, or different trades come in like electrical and plumbing and move it,” Clarke said. Unfortunately, any gap in the insulation coverage will translate into lower performance.
An alternative can be a continuous chunk of foam as the insulation. However, Clarke cautions that a petroleum-based foam product can act as a moisture barrier and trap moisture and condensation from inside the home. This can then lead to damage to timber framing.
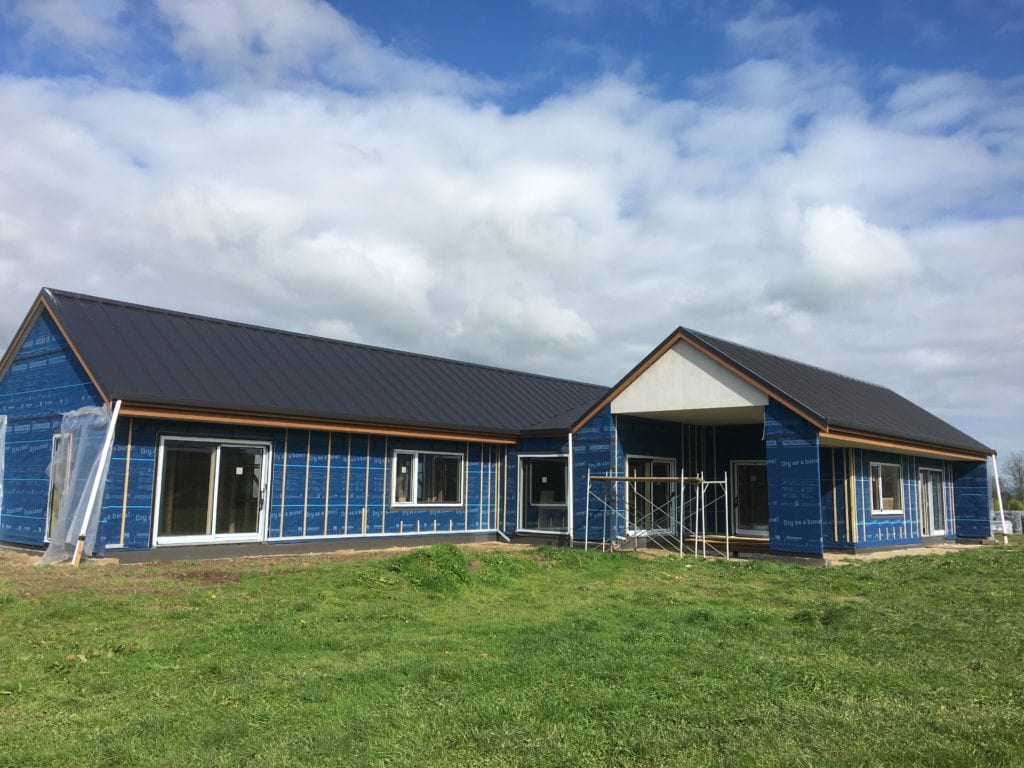
Applying the Latest Thinking
“Where international building science has gone is to make insulation more vapour permeable,” Clarke said.
This is where products like mineral wools and cellulose-fibre products have a benefit, as they are vapour permeable and if they become damp, will naturally dry out.
“Where international building science has gone is to make insulation more vapour permeable.”
Foil-faced sarking is frequently chosen by many builders as part of the weather-proofing solution. Clarke advises against installing it directly against fibrous insulation as that would result in moisture build-up.
An alternative to sarking is a vapour-permeable building wrap, a type of product that is frequently used for Passive House builds and other approaches that aim for an air-tight building envelope.
Get Over Thermal Bridges
Another factor that can compromise insulation performance is the presence of thermal bridges—elements or materials that are effective conductors of heat or cold. The fenestration assembly can be a major weakness, for example, if simple aluminium window frames are installed due to aluminium’s high conductivity. Thermally-broken aluminium frames, uPVC or timber framing are much more effective as part of an insulated wall system.
According to Clarke, a gap of 10–20mm between the window frame and the insulated wall systems can also undermine the window and the insulation systems because of thermal bridging and air leakage. Conduits for cables and pipework can similarly reduce insulation performance by creating a thermal bridge or gap.
The “high-performance end of the industry” is beginning to address this issue by including a dedicated cavity for services cables and pipework. While Clarke said this is a “huge step forward,” it can mean a loss of between 30mm and 50mm in floor area as it increases the thickness of the wall assembly.
Delivering an Overall Better Building
Insulation can even play a role in the overall durability of a wall system.
“This can be greatly enhanced by combining all these systems,” Clarke said. “Water leaks are a big problem for builders—that’s when you will get the kind of call back no one wants to have.
“The more airtight the weather-resistive barriers (WRBs), the more waterproof they are. So waterproofing and energy go and in hand.”
Another building system that should be considered as a whole is the slab and floor system. In some climate zones, especially very cold climates, decoupling the slab from the ground and insulating it is a sound practice. In warmer climates, on the other hand, having the slab on the ground is beneficial—it can make a home cooler in summer due to the relatively cool temperature of the ground.
No matter the climate, the perimeter of a slab should always be treated with some form of insulation, Clarke said. This will be where heat can be gained in summer or lost in winter.
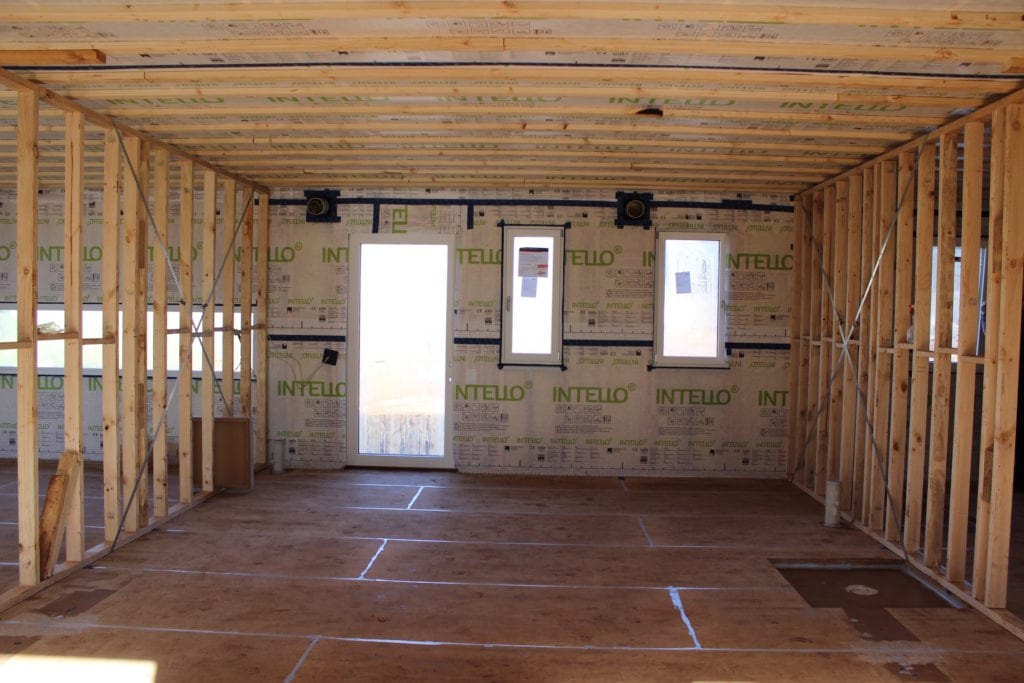
A Quick Guide to Product Types
In terms of specific products, Clarke believes fibrous insulation products are a sound choice when installed correctly within a well-detailed building system. While spray-in foams might look cheap and easy to use, he warns that they can be subject to shrinkage, the thickness is hard to control, they can trap moisture, and they may also off-gas volatile organic compounds.
Another recent innovation, phase change materials, can be used to substitute for thermal mass as part of a solar passive approach. However, Clarke said, it does not generally substitute for all the functions of wall insulations. Made from encapsulated materials like paraffin wax or mineral salt solutions, phase change materials absorb and release thermal energy as they change from solid to liquid form or back again.
The same thermal storage effect, Clarke explained, can be achieved with polished concrete, exposed masonry or reverse brick veneer in conjunction with solar passive design.
“Mass really needs to be used well,” Clarke said.
Structural Insulated Panels (SIPs) are another product gaining popularity, particularly with modular and prefabrication approaches. Clarke said that where they run the whole span of a wall, there is little risk of condensation issues. The detailing matters, however, as some form of insulation and moisture barrier treatment will still be needed and special attention to junctions and joins.
The upside for builders of paying close attention to insulation is gaining a higher home energy efficiency rating for their builds, which Clarke referred to as a possible marketing advantage. Research released earlier this year by the Sustainable Building Research Centre at the University of Wollongong also found that buyers are prepared to pay more for an energy-efficient home.
Leave a Reply