— 9 min read
4D BIM: Combining BIM & Scheduling
Last Updated Mar 25, 2025
Last Updated Mar 25, 2025
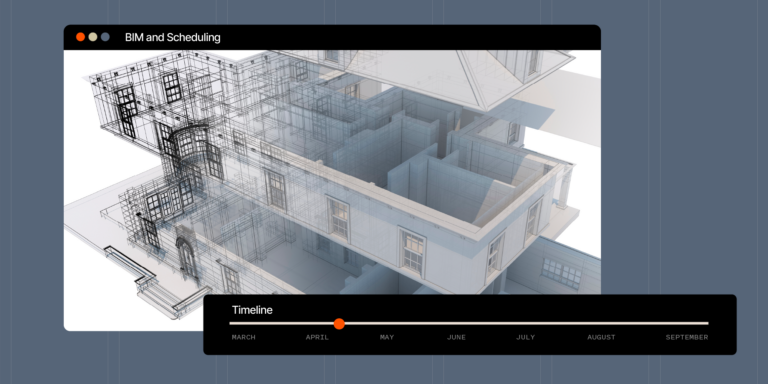
Humans have long speculated about the fourth dimension — but the architecture, engineering and construction (AEC) industry is taking 4D from theoretical to practical. Specifically, as the industry continues to adopt building information modeling (BIM), adding temporal dimensions to our 3D models makes them even more robust and useful.
With 4D BIM, BIM managers and virtual design and construction (VDC) specialists layer the element of time on top of the model. In this way, they aim to create a data-informed schedule that all parties can visualize and, consequently, better understand. Ideally, this allows for more efficiency both in the office and in the field while simultaneously mitigating risk and encouraging collaboration.
Table of contents
4D BIM 101
Simply speaking, 4D BIM is an animated construction schedule. This could be a video or a series of stills that show the project moving forward step by step.
By adding time, scheduling and logistics data to the model, this added BIM dimension allows people to see and engage with the schedule in a new way.
This can support more efficient construction sequencing than looking at “flat” data in a spreadsheet or project management software. Usually, a BIM manager or someone else in the VDC team at the general contractor (GC) helps facilitate the creation of the 4D model. They do this by linking objects in the model to items in the schedule. That results in a simulation that allows users to see construction progress over time.
Creating 4D Models: Layering Time Over BIM
Creating 4D BIM — namely, manually assigning schedule line items to model elements — can be labor intensive. As a result, a lot of teams look for ways to streamline the process as much as possible.
That usually means waiting until two assets are created: the construction schedule and the model(s).
With the schedule in hand, teams have all the information they need about the proper sequencing of events on the project.
They then add that to a model their firm has already compiled(this is most common when the GC has its own VDC department), one developed by the design team and/or one that pulls in modeling work performed by subcontractors. Oftentimes, this combination of the model and the schedule happens in the GC’s 4D scheduling software.
By leveraging 4D BIM when it’s most needed, teams can see what needs to be installed, where to put it and when. This drives efficiency and quality assurance.
Determining What to Model
Once they’re armed with the schedule and the applicable modeled elements, the 4D BIM team decides what to animate. Currently, it’s relatively rare for teams to model everything from the first shovelful of dirt to the last detail of the tile. More frequently, the BIM management team identifies key moments that will have a big impact on the project’s outcome.
In other words, what gets created as a 4D model depends on the project. A fragment of the project — or the project as a whole — might get the element of time layered on the model when:
- The owner requires it
- The GC’s team determines it could help manage the complexity of an area or project
- The scheduling team calls out a potentially difficult area for sequencing
Sometimes, the BIM team might create a massing schedule, which lays out the project in broad strokes. More frequently, though, the scheduling team, the project site team and the BIM team work hand-in-hand to decide what to model — considering owner requirements as they make these decisions.
Many BIM teams create 4D models for structural steel sequencing, for example. While this is just one fragment of the overall schedule, it’s a complicated and important step in the project. Plus, it often represents a costly portion of the schedule because it requires a crane on site.
In some instances, the GC will even undertake a 4D massing schedule or 4D modeling of a fragment of the project before the firm has landed the contract. Modeling the project or its most challenging areas in 4D can show the owner the GC’s capabilities, helping with project pursuits or preconstruction.
Using 4D BIM
Once the 4D model has been developed, users can move through time to see installation sequencing. This might function like a slider in the BIM viewer that allows them to move forward and backward in time. Or it could be a video simulating the construction. Alternatively, it might result in a PDF flipbook or storyboard that lets them move through the schedule to visualize how it will progress.
In this way, stakeholders can interact with and even interrogate the schedule: Will the sequencing work as planned? Can, for example, the crane access what it needs to once other components are installed? The model enables clash analysis, checking that the planned sequencing won’t create issues. It also supports logistics planning and clarifies deadlines for individual parties’ work.
4D BIM also helps the project stay on track throughout construction. The BIM and scheduling team might hold monthly meetings to compare the 4D model to the actuals. By updating the model with what’s been installed on specific dates and comparing that to the planned work, teams stay informed. The scheduler, BIM manager, the superintendent and subcontractors can all use the model to measure progress and collaborate to solve challenges as they arise.
Benefits of 4D BIM
Using a model enriched with scheduling data unlocks some notable advantages for projects.
Better Communication for Data-Informed Decision-Making
Many people are visual learners and have an easier time understanding things when they’re presented visually. Taking the project from the 2D space of flat drawings and line-by-line schedules can transform their understanding of what’s required. It can make it easier to identify problems and to talk through them, too.
This facilitates easier communication with all stakeholders. It helps the owner visualize the project over time so they can feel connected to it and informed about it.
It also supports collaboration in the GC’s office, connecting the scheduling, project teams and VDC teams in ways that help them build efficiency and productivity into the project.
When done well, it extends that spirit of collaboration out to the field (particularly to the superintendent) and subcontractors. It helps everyone align as a team, helping them make data-driven decisions.
Risk Mitigation With 4D BIM
A model enriched with 4D data becomes a tool stakeholders can use to push the project forward in a way that’s both proactive and safe. It identifies areas for schedule improvement while also helping to illuminate risk. This allows for refined, strategic sequencing.
Having a crane on site represents a certain dollar amount each day, for example. By helping teams visualize the work for which that crane is needed, 4D BIM enables the optimization of its usage. Teams can develop a schedule that maximizes the daily use of the crane, ensuring it leaves the site as quickly as possible.
By helping to align all stakeholders to the schedule, 4D BIM also directly reduces the risk of delays and their inherent cost burden.
This kind of modeling reduces safety risks, too. When planning the structural steel fragment of the schedule, for example, teams can engage with the model environment. Seeing the work sequenced in 3D helps them pinpoint where they need safety features like tie-offs and railings.
By moving the model through time, 4D BIM makes it easier to spot hazards at each phase of the project. This way, they can be best managed.
Challenges With 4D BIM — and How to Overcome Them
4D modeling introduces some potential pitfalls. Fortunately, the AEC industry has already started developing ways to work around and through them.
Siloed Information: Counter With Regular Meetings
While the 4D model gives teams a tool to collaborate, participation from all stakeholders can also be a challenge. To be effective, 4D BIM needs buy-in from the scheduling team, the VDC team, the superintendent and subcontractors. Data needs to flow from all of these parties into the model to keep it updated.
As a best practice, these groups should have regular meetings (e.g., weekly or monthly). If they don’t, data could get siloed in one person’s software or other recordkeeping repository. Once the model is outdated, it becomes an ineffective planning and problem-prevention tool.
Lack of Technical Skills: Counter With Company-Led Learning
Technical difficulties also introduce some hurdles when it comes to 4D BIM. People on the scheduling team or the superintendent might not have the skillset to interact with the model, for example.
There’s a learning curve, and companies need to plan for that — and invest in helping their teams overcome it.
Data Loss: Counter With Program Requirements
Each individual’s technical prowess isn’t the only obstacle here. Technical challenges can — and often do — arise when teams use different software platforms. Some data might get lost or degraded as the subcontractor’s or design team’s model gets pulled into the GC’s platform of choice. The same is true if they’re moving a model from their own authoring platform to their scheduling tool to add in the fourth dimension of time.
To counter this, it helps to have a BIM execution plan that’s enforceable (i.e., signed by all parties). The plan can stipulate which authoring tools parties need to use. By choosing tools with pre-built integrations or the required data-sharing functionality, teams can protect data integrity.
Stay updated on what’s happening in construction.
Subscribe to Blueprint, Procore’s free construction newsletter, to get content from industry experts delivered straight to your inbox.
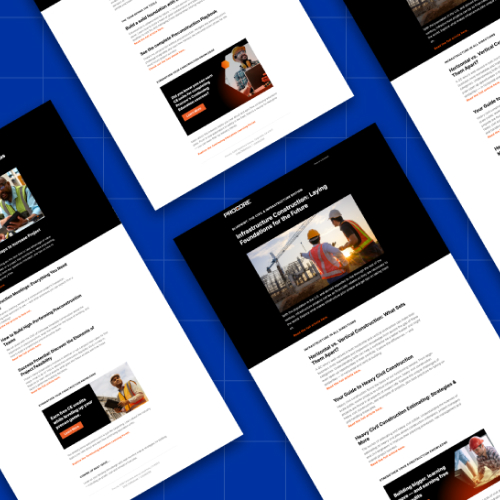
Adding Dimension to BIM: 4D and Beyond
The AEC industry hasn’t stopped at the fourth dimension. It’s also exploring ways to overlay cost (5D BIM), sustainability (6D BIM), facility management (7D BIM) and beyond. In this way, the model becomes increasingly useful. It can power automated 3D takeoffs, for example.
That said, added dimensions of BIM are by no means an industry standard yet. The domestic AEC industry’s current lack of adoption beyond 4D BIM is evidenced by goings-on within the federal government. The U.S. General Services Administration (GSA) has launched a 3D-4D-BIM program(which notably makes no mention of 5D BIM or any other dimensions of building information modeling).
This means there’s room for construction professionals to explore new ways of innovating in this space. Begining to align tools and expectations as soon as possible can help them reap the biggest benefit as they add dimensions of BIM. Implementing new, well-planned processes to further leverage the model can help firms provide additional service and a better finished product.
Was this article helpful?
Thank you for your submission.
100%
0%
You voted that this article was . Was this a mistake? If so, change your vote here.
Scroll less, learn more about construction.
Subscribe to The Blueprint, Procore’s construction newsletter, to get content from industry experts delivered straight to your inbox.
By clicking this button, you agree to our Privacy Notice and Terms of Service.
Categories:
Tags:
Written by
Kacie Goff
54 articles
Kacie Goff is a construction writer who grew up in a construction family — her dad owned a concrete company. Over the last decade, she’s blended that experience with her writing expertise to create content for the Construction Progress Coalition, Newsweek, CNET, and others. She founded and runs her own agency, Jot Content, from her home in Ventura, California.
View profileReviewed by
Benjamin Peek
Benjamin Peek is the Director of Virtual Design & Construction for Gilbane Building Co. Benjamin is a people-leader driving transformation through the collaborative strength of high performing individuals, diversity of thoughts and inclusive practices. Benjamin currently leads a department of individuals across Massachusetts, Rhode Island, and Connecticut business units serving all projects needing Virtual Design & Construction services from preconstruction through construction.
View profileExplore more helpful resources
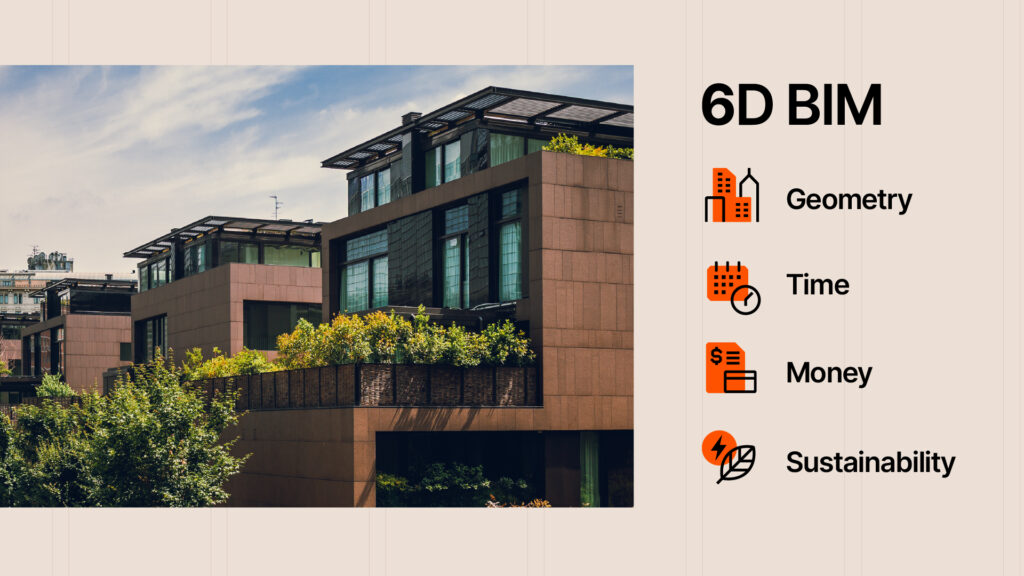
The Role of BIM in Sustainable Construction
Building information modeling (BIM) is transforming the architecture, engineering, and construction (AEC) industry. With this kind of sophisticated modeling, the industry has shifted from designing in 2D to 3D. This helps...
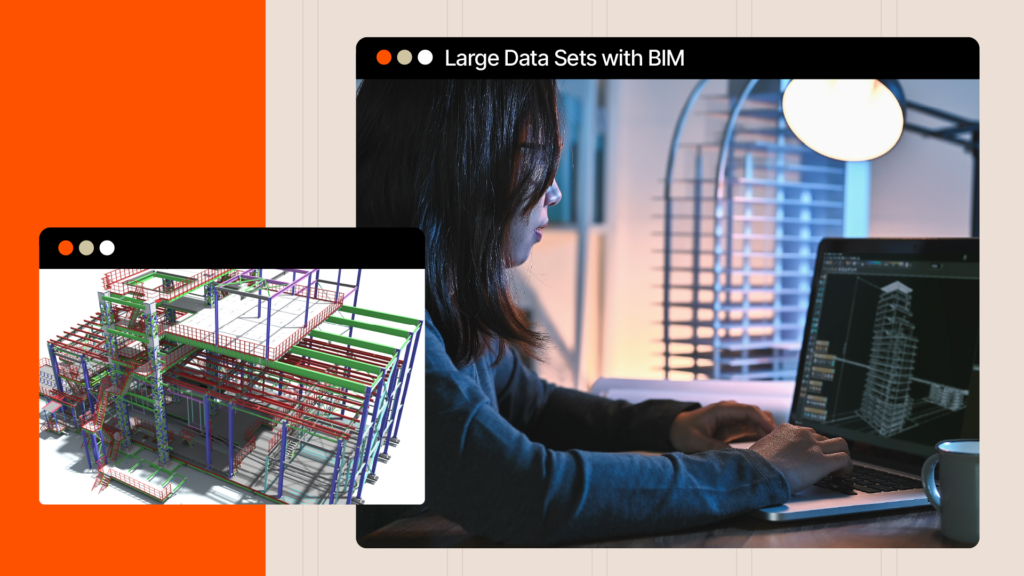
Building and Using Large Data Sets with BIM
In recent years, two technological concepts have exploded, almost in parallel: One, called building information modeling (BIM), makes it possible for stakeholders to “build” construction projects in a 3D virtual...
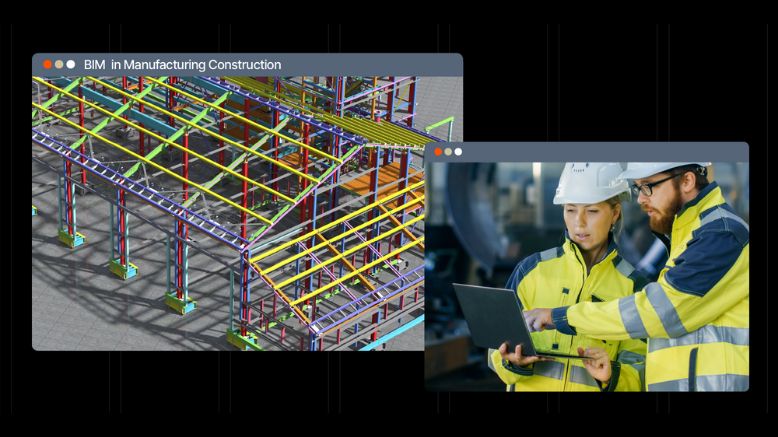
Exploring BIM’s Potential in Manufacturing Construction
As building information modeling (BIM) improves, project owners can build more sophisticated facilities faster. And as consumers increasingly demand what they want delivered to them faster, brands need smarter manufacturing...
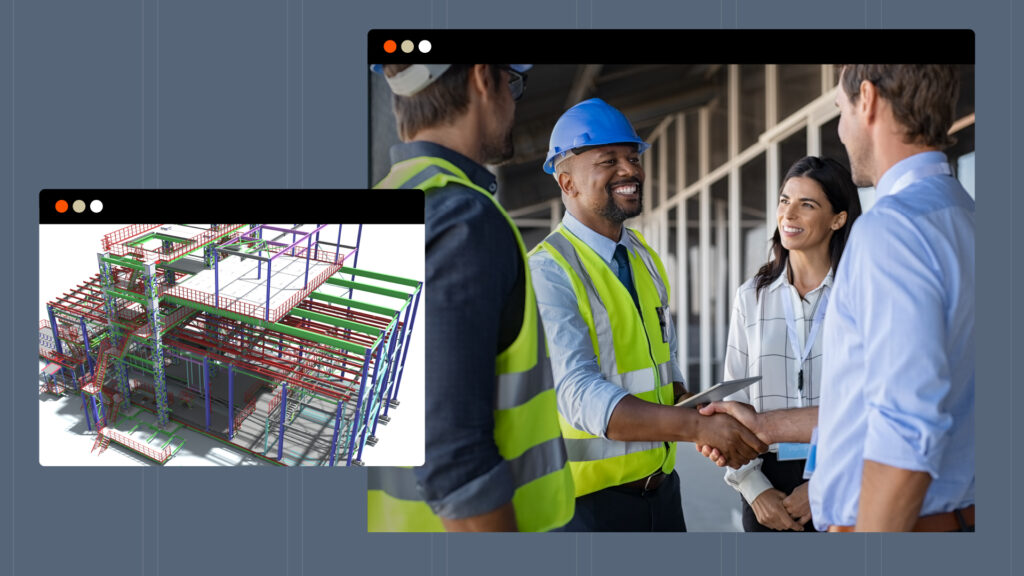
How BIM Enhances Control and Efficiency for Project Owners
Any construction project has a number of stakeholders. With a traditional project delivery method, it moves from designers and engineers in the architectural design process, to the general contractor and...