— 9 min read
Mastering Airport Construction: From Groundbreak to Takeoff
Last Updated Jun 11, 2024
Last Updated Jun 11, 2024
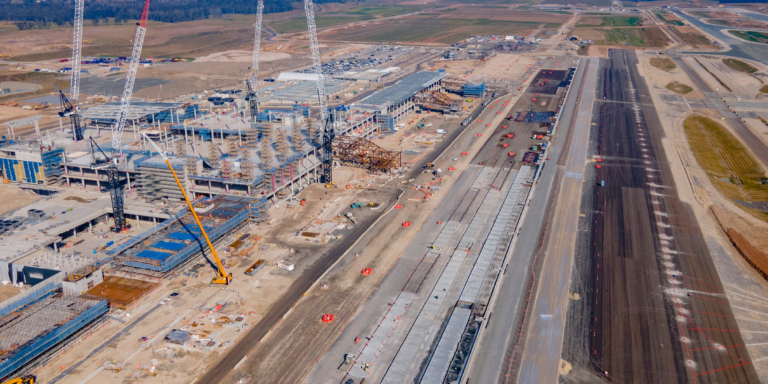
Airports are bustling centers of near-constant activity. Roughly 2.9 million Americans are flying every day — a number that’s only expected to rise. This volume of traffic, from planes to cars to feet, means that infrastructure renovation in airports is almost constantly necessary.
The process of bidding and completing projects at an airport can be particularly tedious, but this kind of construction work is increasingly essential to our interconnected world. So, the ability to navigate an airport’s red tape has never been a more important or valuable skill.
This article explores how construction at airports happens, what makes it different from other types of commercial construction and how to best prepare for the lengthy process of completing a job inside an airport.
Table of contents
The Airport Construction Process
The most important tenet of airport construction is to minimize any disruptions in the flow of business. That’s not an easy task, though, since smaller airports generally close late in the evening — and larger, international airports are landing planes on their runways 24 hours a day.
That means most construction work at airports happens overnight when fewer planes are landing — especially if the project is airside, meaning it’s in the part of the airport beyond security where personnel needs a boarding pass to enter.
Working around security and operational concerns is a unique part of contracting at an airport, and general contractors (GCs) should be prepared to persevere through a long planning process that requires oversight and input from many stakeholders, including the Federal Aviation Administration (FAA). To be successful, they must be both diligent and detail-oriented.
Airport projects can be large and costly, and there are often huge penalties for not completing them on time. Owners may expect contractors to do whatever needs to be done, including working all hours of the day to get the build finished and ready to use.
Also, since even small airports are usually pretty large, many different types of construction might be needed. Airports require maintenance and renovation of runways and taxiways, which are the “streets” planes drive on before and after landing. Many owners are also constantly looking to build new terminals or renovate old ones, and these large-scale projects may last years.
Other types of construction might include working on hangars, aprons, air traffic control towers, gates, baggage claim systems, fuel stations, security infrastructure and in-terminal retail shops, among others. Because there are many different projects a crew could take on at an airport, the following examples represent only some of what could happen during the phases of construction.
Stay updated on what’s happening in construction.
Subscribe to Blueprint, Procore’s free construction newsletter, to get content from industry experts delivered straight to your inbox.
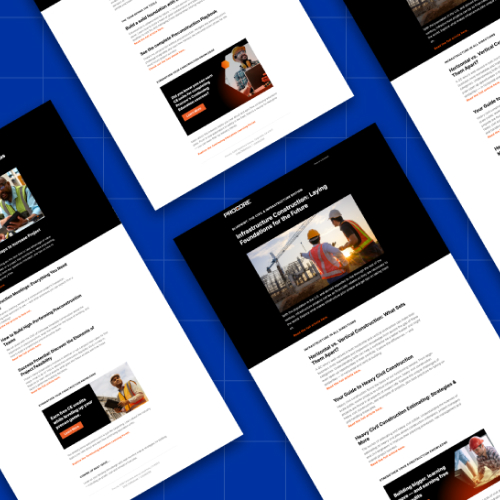
Planning Phase
Airport bids tend to be high. To have the best chance at securing work from a bid, it’s important to understand how much more logistically challenging working at an airport is than other types of construction. The barrier of an airport is like the border of a country. Anything — or anyone — going across that line will need to be approved by the airport authorities and security.
The FAA is the main governing authority for airports, and it lists many Airport Construction Standards on its website. There is no unregulated airspace, which means that even doing a build landside — outside the borders of the security checkpoints — may be subject to regulations, such as how tall a structure can be and what equipment can be used. GCs should also be aware of regional regulations for constructing in and around airports.
Preconstruction Phase
As soon as the bid is secured, it’s time to hit the ground running. During preconstruction, the general contractor must submit for materials, hire a crew, and decide who will be airside and who will not.
Airside projects in particular require many approvals from airport authorities, starting with how the crew will get to work. To cross into the airfield, workers need to pass a background check and complete an onboarding for both the contracting company and the airport.
Once inside, though, workers still need escorts to the jobsite — typically at a 1:1 ratio, meaning that if 50 crewmembers need to enter for work, 50 must escort them inside the airfield. But this can be made easier if crew members obtain credentials to escort themselves inside the airfield beforehand. This can be a long process, so it’s important to negotiate how many employees will need badges early on.
In general, workers will need to be flexible with their assignments and should be ready to work any shift to get the job done. Another logistical issue for the workforce is that parking will likely be offsite, far from the actual jobsite, and employees will have to go through security every day. Budgeting time and money reasonably for these issues can reduce the risk of losing workers and getting behind on the project.
In the same vein, it’s also necessary to consider how, where and when building materials and equipment will be delivered to the job site, as everything that enters is subject to TSA and FAA rules, too. All equipment and materials being brought inside must be registered to the airport.
Lastly, airlines may need to be notified if their services are going to be impacted by the production. Also, if the work is out on the tarmac, it might be necessary to shut down some runways at night. But that’s only possible by coordinating with the airport as well as the FAA, which has an in-depth checklist on the procedure, well in advance. For this, a GC will need to be highly organized, with the right equipment at the ready, or else risk wasting valuable time.
Construction Phase
It’s tempting to think that having meetings with an airport’s construction management team would slow up during the actual work, but in fact, the opposite is true. It’s common to meet every day throughout the construction phase.
If the GC is not able to get badges authorizing entry to the airport, they’re likely going to be dependent on having escorts for every member of the crew, no matter how large it is.
But even if that is taken care of, airport construction is still an exercise in patience. For safety reasons, working airside requires adhering to the directions of flaggers, who are the work area’s traffic conductors. They take responsibility for every vehicle — flying or driving — on every runway and taxiway. It’s important to budget time for interruptions from them as they maintain the safety of the airfield.
Post-Construction Phase
Finishing a construction project at an airport is maybe the most similar part of the process to other types of commercial work. Closeout is one of the most important steps in the process to set contractors up for future jobs, so it’s important not to burn out at the finish line.
There will be a series of inspections, including for fire safety and a certificate of cccupancy, and it’ll also be necessary to complete punch lists of any outstanding work that needs to be finished or corrected before handing the project over to the airport authorities to use.
Since many of these projects are publicly funded with grants from the FAA, more meticulous documentation may be necessary than other types of commercial construction. It may seem like a hassle, but it’s important to ensure that taxpayer money is spent correctly and efficiently.
Roles and Responsibilities in Airport Construction
Working at an airport requires a lot of input from many stakeholders, including—but not limited to—the following.
Job Title | Responsibility |
---|---|
General contractor | General contractors are chief of operations at the jobsite. A contractor working in an airport should be able to plan the stickiest logistical details while keeping in communication with the airport authorities. |
Owner and governing body | Airports can be private or publicly owned, so the “owner” might be a business or even a local government. Many airports are owned by one entity and operated by another. For example, New York’s LaGuardia Airport is owned by the city, but operated by the Port Authority of New York and New Jersey. |
Owner’s representative | Often, airport authorities will designate a construction management team, which will meet with the GC throughout the project. |
U.S. Department of Transportation | The Federal Aviation Association is the operating arm of the U.S Department of Transportation, and it does more than set building standards. It is also in charge of air traffic operations, issuing pilot certifications, and developing new technology. Ultimately, the FAA is responsible for all civilian transportation in the US and surrounding international waters, which is why it takes a heavy hand in the construction process. |
Specialty consultants | Airport construction usually requires input from a number of specialized consultants who plan and design the space that will be built, including architects, interior designers, engineers and engineering design experts. |
Common Challenges on Airport Projects
Beyond the logistical issues, airports have a couple of unique problems that a GC should be ready for.
Dangerous Debris
A major part of completing construction in an airport is adhering to an intense environmental regulation that aims to reduce Foreign Object Debris, or FOD. (Sometimes, it’s also referred to as foreign object damage.) FOD isn’t just trash or rubble from the jobsite. It can be anything even the size of a thumbnail that’s leftover on the airfield, including tools and equipment. Most airports do daily sweeps of the airfield to look for FOD, and for good reason. If even a small piece of FOD ends up in a jet engine, it could damage a million-dollar piece of equipment—or worse, pose a hazard to the passengers onboard.
The GC will be contractually obligated to make sure there’s no FOD ever, failure to do so can result in shutting down operations. This might mean having sweepers onsite at all times, or working with a dedicated clean-up crew.
Planning for Pickiness
Many airports prohibit using equipment that’s not environmentally friendly, which rules out using much older equipment. Remember, GCs will have to submit for clearance from the airport authorities on every piece of machinery they’ll use in advance, so it’s important have a detailed plan for how to move through phases of construction. Anything tall, like a crane, will have to be flagged and may have to be boomed down when not in use. GCs need to know the height of all their equipment, as well as when and how they’ll use it, so that planes don’t risk crashing into it.
Planning is the key to successful airport construction projects.
Plan thoroughly. An airport construction project is truly airport-sized, requiring a lot more logistical problem-solving than other jobs. One of the worst-case scenarios for a GC is getting a job they’re not actually prepared to do, and these projects are not typical bids. Getting hired to work on an airport is all about maintaining positive relationships with owners and their reps.
By being open to communicating with stakeholders to meet their needs, along with a little old-fashioned grit, it’s possible to break into this lucrative area of business — and secure future gigs.
Was this article helpful?
Thank you for your submission.
100%
0%
You voted that this article was . Was this a mistake? If so, change your vote here.
Scroll less, learn more about construction.
Subscribe to The Blueprint, Procore’s construction newsletter, to get content from industry experts delivered straight to your inbox.
By clicking this button, you agree to our Privacy Notice and Terms of Service.
Categories:
Tags:
Written by
Alex Six
10 articles
Alex Six is an Enterprise & Strategic Civil & Infrastructure Overlay Account Executive for Procore. Alex has a long background in the construction industry beginning with an internship with one of the biggest contractors in the world, and expanding across projects with teams as small as 4 people and as large as multi-billion dollar budgets with large teams and disciplines. His resume includes Caltrans highways & bridges, Metro light rail & underground, as well as airport runways and utilities.
View profileTrey Strange
26 articles
Trey Strange is a Peabody and Emmy-Award winning writer and producer based in Brooklyn, NY. Throughout his career, Trey has worked for the Huffington Post, Houston Chronicle, Out Magazine, Brooklyn Eagle, CNBC, INTO, and New York Magazine's Bedford + Bowery. He received his Masters in Journalism and Middle East studies from New York University, and Bachelors in the same subjects from the University of Houston.
View profileExplore more helpful resources
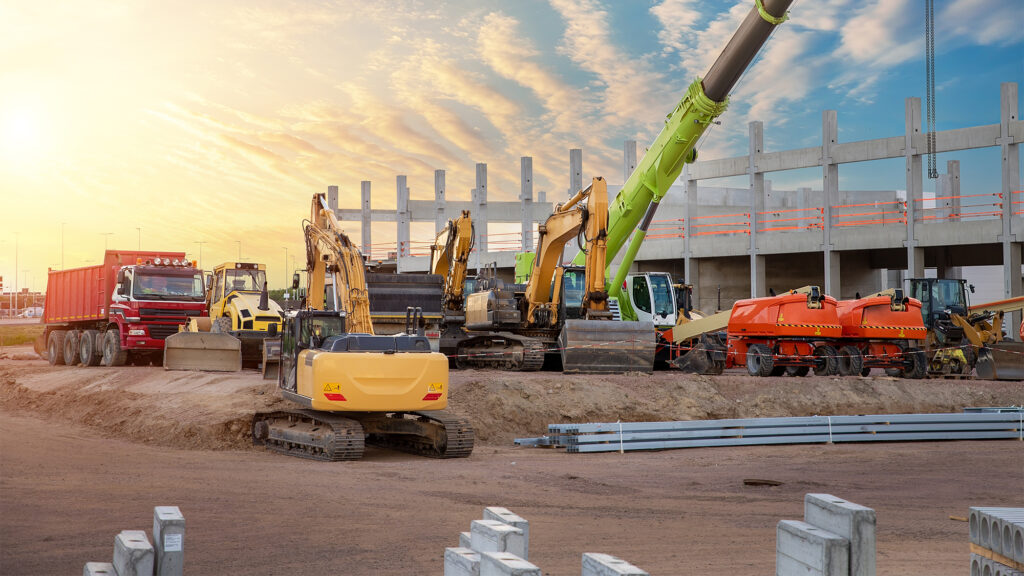
Improving Project Monitoring with Construction Quantity Tracking
Once a construction project is underway, builders need to closely monitor the project’s progress and make sure it’s staying on schedule and within budget. Quantity tracking helps construction leaders manage...
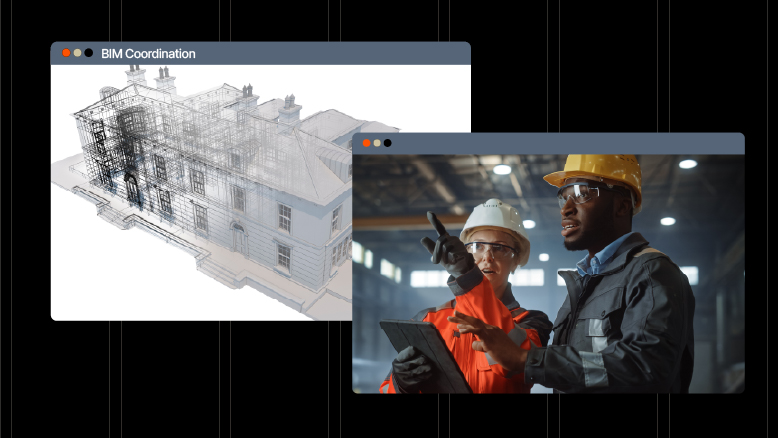
Streamlining Construction Projects with Effective BIM Coordination
The old saying goes: if you fail to plan, you plan to fail. Construction professionals know this better than nearly anyone. To take a project from a vision in an owner’s...
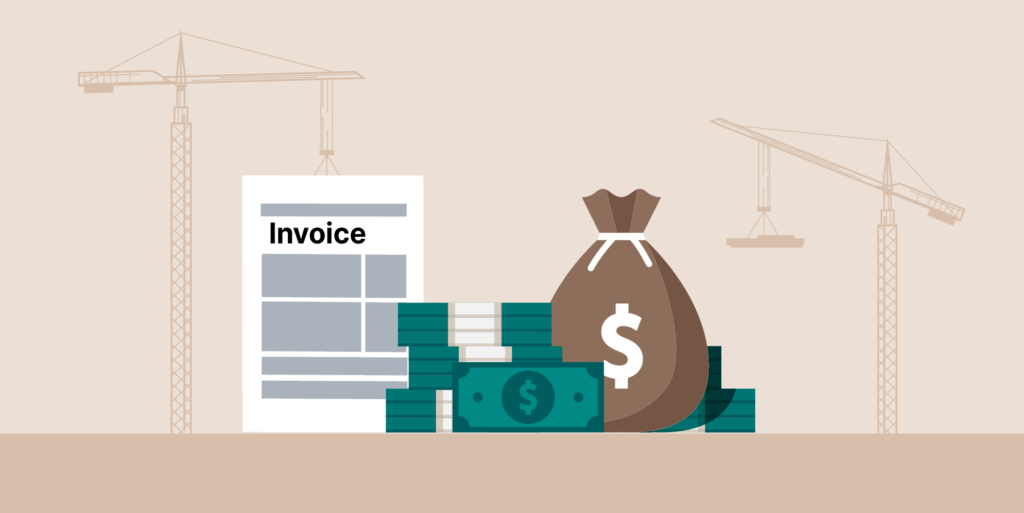
Construction Invoice Factoring: A Quick Guide
Construction companies need to maintain consistent cash flow. Projects can take years to complete, and delays and unforeseen events may keep expenses mounting. Adding to this load are typically high upfront...
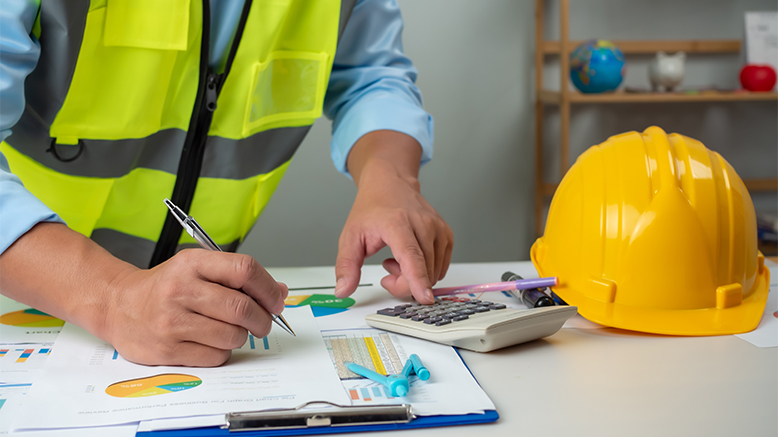
Understanding Subcontractor Bid Packages in Construction
Construction bid packages can have a cascading impact on the success of a construction project. The quality of a bid project may affect the quality of the bids, which in...