— 5 min read
What Is a Bill of Quantities in Construction?
Last Updated Sep 6, 2024
Last Updated Sep 6, 2024
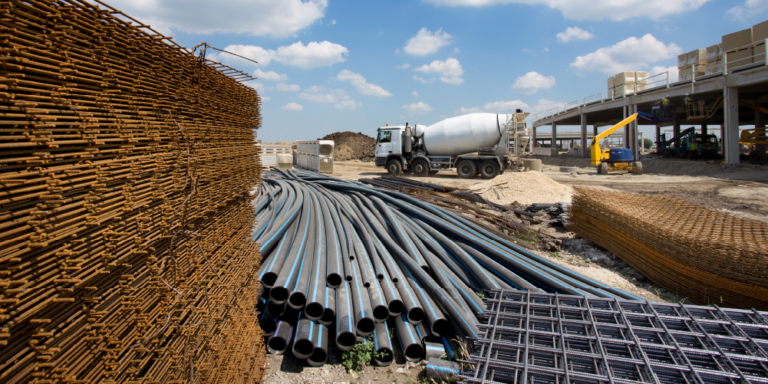
On large, complicated projects, it can be difficult for project owners to compare proposals from contractors: They have to verify that the contractors are bidding on the same scope of work before comparing prices. In construction, a bill of quantities allows owners to control the bidding process because the work and quantities are clearly stated for contractors to price before the project is sent to bid. It takes the guesswork out of bidding and analyzing bids.
Table of contents
What is a bill of quantities?
A bill of quantities (BOQ or BQ) is usually used on larger construction projects and consists of a list of materials and services required to perform a project. The list includes materials, labor, and quantities of each. The engineer or architect typically performs a takeoff to prepare the BOQ after the project design is complete.
On a design-bid-build project, the BOQ is typically provided in the bid package. Because the materials and quantities are already established, contractors may choose to avoid a takeoff, relying on the BOQ instead. But while a BOQ allows contractors to focus on pricing, they often still opt to perform their own takeoff to identify any gaps that the owner or design team missed.
After the contractor prices out the BOQ, it is returned to the owner for review and contractor selection. If discrepancies arise between a contractor’s takeoff and the BOQ, they may submit a request for information (RFI) to the owner for clarification.
After contractor selection and during the project, the bill of quantities can be used when invoicing the project. The BOQ essentially becomes the schedule of values, making scope progress easy to calculate based on the amount of material on the job site and the work completed.
If the project design is not totally complete, or it’s not clear what exact quantities are needed, teams can use what’s called an approximate or notional bill of quantities. In this case, the pricing is estimated based on approximate quantities, and can be revised once the amounts are quantified.
BOQ vs BOM
While a bill of quantities (BOQ) includes an itemized list of all project costs — including materials and labor hours — a bill of materials (BOM) only includes materials. Some general contractors include a BOM in the bid packages for subcontractors, on large and small projects alike. Just like a BOQ, a bill of materials helps to simplify bid comparison from multiple contractors.
Specialty contractors will generally also do their own takeoffs to verify the quantities in the BOM. If they discover any errors or missing information, they can submit an RFI to the general contractor, who would look to the owner for a response.
Courses about construction.
For construction.
Unlock your career potential with our free educational courses on Health & Safety, Data in Construction, and more.
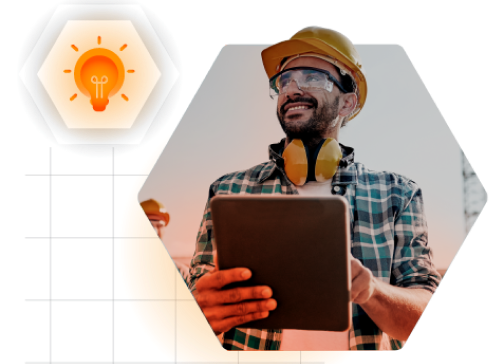
What is the purpose of a bill of quantities?
Bills of quantities in construction allow for quick and easy comparison of contractor proposals. Since every bidder is quoting the same labor and materials, differences in pricing are easy to spot. This gives the owner confidence that each proposal includes all the work shown on the documents, and that they are selecting the most competitive price.
The bill of quantities is also used to clearly define the scope of work on a project. Since quantities and amounts are provided, there’s no room for misinterpretation and less chance of mathematical errors. This helps ensure that contractor pricing is accurate.
A BOQ also helps project owners with cost controls and cost predictions. Based on the project schedule and the breakdown provided, the owner can anticipate the amount of work that will be completed in each billing cycle. This enables them to prepare for their cash flow needs as the project progresses.
How to prepare a bill of quantities
Start preparing a bill of quantities by breaking the work down into items that can be quantified or measured. This breakdown is often based on standard work breakdown structures (WBS), like CSI MasterFormat. The breakdown works best when it’s organized by subcontractor packages, which makes it easier for general contractors to bid on the work.
The list of work items includes a description, quantity, and unit of measure. From there, the contractor prices the work listed on the bill of quantities, based on the drawings and specifications they have been provided. If an item is shown on the drawings and is missing from the bill of quantities, the contractor should bring this to the owner’s attention. A revised bill of quantities may need to be sent out.
Pricing is sent back to the owner for review, and each contractor’s proposal is compared to other bidders.
Once a contract is signed, the bill of quantities can be used to create payment applications as the work progresses. The contractor notes the quantities completed each month on the form and multiplies it by the price for each item to get the invoice amount.
Although architects and engineers usually create the bill of quantities for a project, more companies are using BIM software to prepare their list of quantities. Software easily creates the list and can modify it quickly if the model is updated.
Creating an even bidding field
Using a bill of quantities to estimate a construction project improves the accuracy of the proposals and ensures that all contractors are bidding for the same work. This makes it easier for project owners to select a contractor because they don’t have to manually level bids to compare different scopes of work or material lists.
And since contractors can submit the BOQ with their payment application, the owner can easily see progress on the project — and anticipate cash flow needs.
Was this article helpful?
Thank you for your submission.
100%
0%
You voted that this article was . Was this a mistake? If so, change your vote here.
Scroll less, learn more about construction.
Subscribe to The Blueprint, Procore’s construction newsletter, to get content from industry experts delivered straight to your inbox.
By clicking this button, you agree to our Privacy Notice and Terms of Service.
Categories:
Tags:
Written by
Dawn Killough
34 articles
Dawn Killough is a writer with over 20 years of experience in construction, having worked as a staff accountant, green building advisor, project assistant, and contract administrator. She holds a BA in Psychology and MS in Conflict Resolution, both from the University of Portland. She shares fundamental green building strategies and techniques in her book, Green Building Design 101. Dawn lives in Portland, Oregon.
View profileBrittney Abell
12 articles
Brittney Abell joined Procore after 6 years as an accounting manager for a commercial general contractor, overseeing accounts payable and receivable. Before that, she worked as a contract administrator for an architecture & design firm for 6 years. She has worked on a variety of building projects, including travel stops, restaurants, hotels, and retail warehouses raging from $2M to $20M. She lives in Louisville, Kentucky
View profileReviewed by
Robert Miller
Robert Miller is a Senior Strategic Product Consultant with Procore. He has worked in construction as a project manager for a variety of private companies and public agencies, including Cambridge Housing Authority and the City of Boston. Robert lives in Brooklyn, New York.
View profileExplore more helpful resources
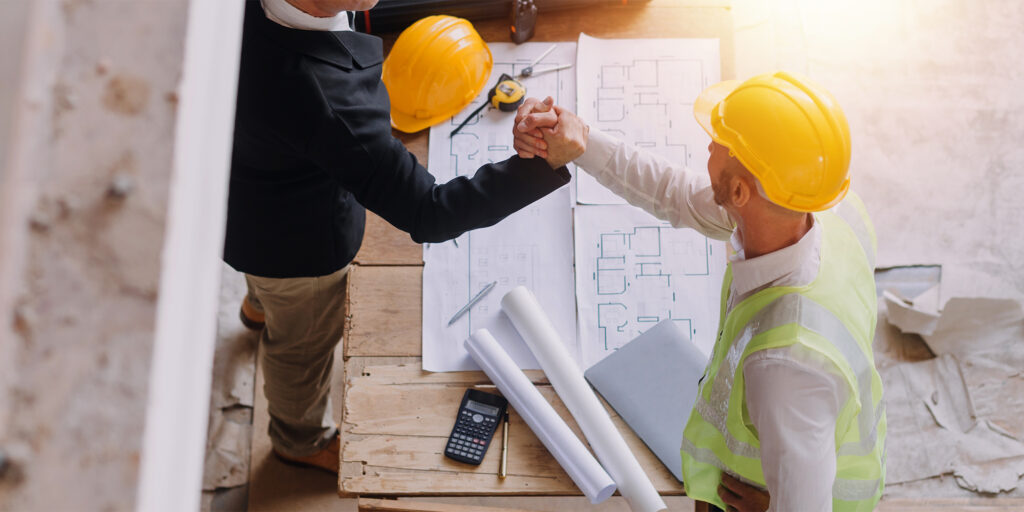
Qualifications-Based Selection: Prioritizing Expertise over Initial Cost
For large or complex construction projects, owners and public agencies often use qualifications-based selection (QBS) to prioritize experience and capability over merely selecting the lowest bid. QBS involves owners choosing...
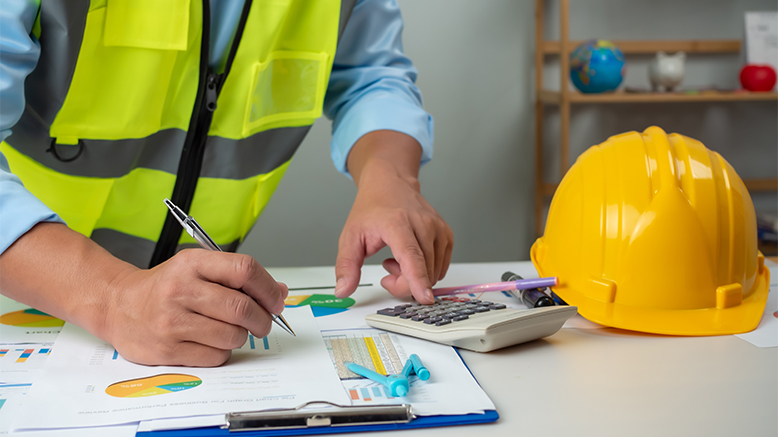
Understanding Subcontractor Bid Packages in Construction
Construction bid packages can have a cascading impact on the success of a construction project. The quality of a bid project may affect the quality of the bids, which in...
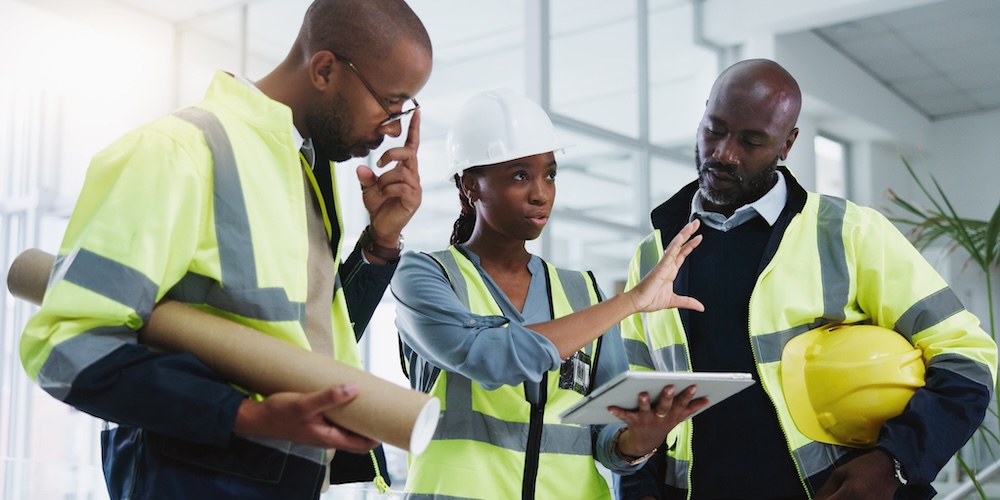
Winning Bids with BIM: Marketing the Benefits to Owners
Creating a 3D model of a construction project is becoming more common but, that doesn’t mean that all projects leverage BIM – or, that all companies are using BIM in the...
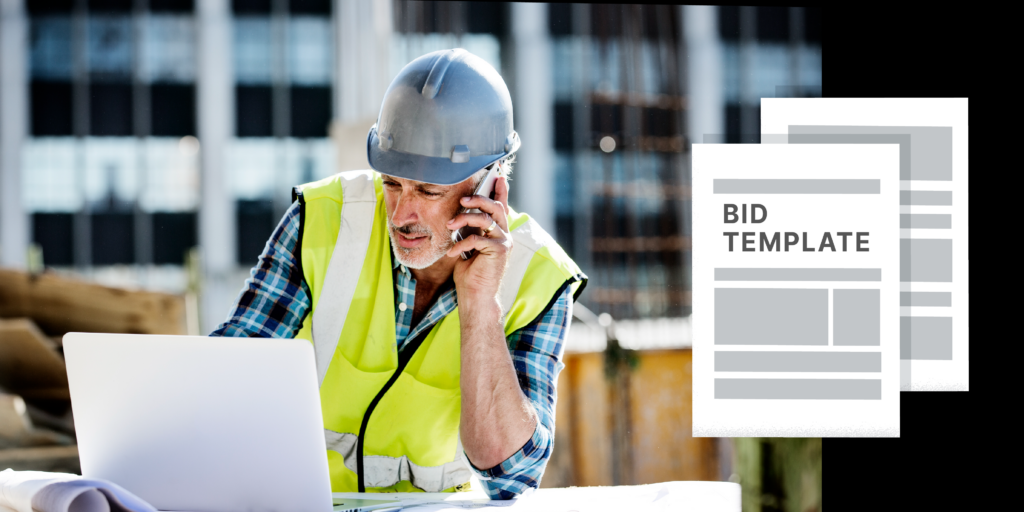
Mastering Construction Bid Templates to Simplify the Process and Win More Work
Every construction project is different. Different set of challenges, timelines, key players, etc. Because every project is different, what project owners need to know from a bid will differ based...