— 8 min read
Exploring BIM’s Potential in Manufacturing Construction
Last Updated Apr 3, 2025
Last Updated Apr 3, 2025
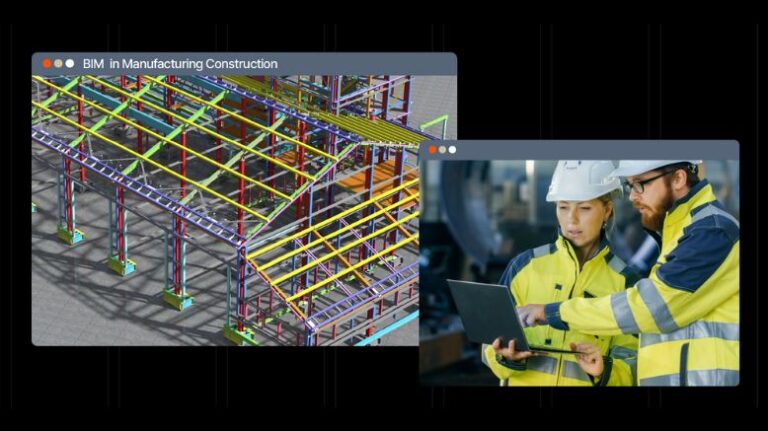
As building information modeling (BIM) improves, project owners can build more sophisticated facilities faster. And as consumers increasingly demand what they want delivered to them faster, brands need smarter manufacturing spaces to keep up.
Enter: BIM. With this kind of virtual design and construction (VDC) technology, owners can build more strategic manufacturing facilities in a more streamlined way.
Table of contents
6 Ways to Use BIM During Manufacturing Construction
BIM can deliver advantages on any construction project. By creating the project in a virtual 3D environment, teams can plan better and more accurately execute on that plan. When it comes to manufacturing construction, BIM delivers a few vertical-specific advantages, too.
1. Clash Detection
Clash detection is one of the most widely applied uses for a BIM model. When the project is “built” virtually, it gets easy to see if, say, that door can actually fit in that hallway, or if that system has sufficient space around it for maintenance.
With manufacturing construction, BIM becomes particularly useful here. Stakeholders can use it to plan for the equipment the project requires. In the model, for example, they can determine the best placement for the drying equipment or the palletizer. They might see that a robotic arm has a 72-inch turn radius on it, and widen the neighboring aisle so it can function properly.
BIM can also be used to make sure the appropriate mechanical, electrical and plumbing (MEP) hookups feed to any equipment that will require them — and don’t have any clashes as they make their way throughout the facility.
2. 4D BIM (Scheduling)
BIM doesn’t have to stay confined to 3D. Teams can expand its uses and benefits by adding the fourth dimension of time. When the model is used in this way — i.e., as 4D BIM — it lets them play out how installation will go over time.
Say, for example, that a major brewer is building a new facility that will house a 240-bottle filler, which weighs eight tons and is too large to fit through any doorway. The team knows that filler can’t come in until the floor is prepared, but it needs to be placed before a certain wall is closed up.
Historically, to find the optimal window for bringing in the filler, the team tasked with construction sequencing would need to do drawings that map the project’s progress over time. With 4D BIM, this aspect of manufacturing construction gets a lot easier because that work gets automated. Some solutions can even use artificial intelligence (AI) agents to identify the best day for installation.
3. Seamless MEP Integration
In manufacturing construction, subcontractors get tasked with creating specialized and oftentimes sophisticated systems. With a finite amount of space in the facility, they may feel they need to fight for their share of the real estate.
Historically, these decisions were often made based on which trade was the highest priority for that specific project. The electrical contractors’ decisions might hold bigger sway at a data center, for example, while a beverage facility bows to the plumbing contractor’s preferences. The prioritized contractor would rough everything in, and then other specialty contractors would need to come in behind and find a way to make it work.
With a 3D model in play, though, planning the facility’s MEP functions differently. Everyone can sit at a table (virtually or in person) and go through the model together. The different trades can voice any needs or issues based on their areas of expertise. Someone might speak up because they know what is or isn’t possible based on the load capacity of the air handler, for example.
With everyone together looking at the same model, planning can happen more strategically and collaboratively. This builds better rapport between all stakeholders while yielding time savings.
4. Just-in-Time (JIT) Material Delivery
BIM can streamline material delivery through 3D takeoffs. But its benefits for logistics planning don’t stop there.
Using BIM on manufacturing construction projects can help optimize logistics on the project and enable JIT delivery. With 4D BIM, it becomes clear what needs to be brought to the site when. If a conveyor comes in pieces, for example, the installation of those pieces can be planned over time in 4D. Teams can then facilitate delivery of those pieces in the order in which they’ll be installed.
By supporting JIT delivery, BIM helps manufacturing construction teams create the smallest laydown yard possible and minimize trucking bottlenecks.
5. Virtual Inspections
Manufacturing facilities usually require extensive and intensive inspections from a variety of authorities having jurisdiction (AHJs). A facility in which DNA test kits are produced, for example, might require clearance from all of the following:
- The Food and Drug Administration (FDA)
- The National Institutes of Health (NIH)
- The Environmental Protection Agency (EPA)
- The state department of health
- The county building inspector
Each AHJ has its own inspection processes. To get the appropriate people to the jobsite to do the required walkthrough often takes quite a bit of time. And that scheduling effort can cause project delays. If a curtain wall is installed but can’t be closed off until it’s inspected, for example, progress halts.
BIM has the potential to streamline some of this process. Some forward-thinking AHJs allow for virtual inspections. By providing them with the model, they can “walk” the space virtually. They may then establish a video call with a team member on the jobsite and instruct them to move the camera to look at specific things.
Backed by the model, remote inspections can enable some sign-offs without ever needing to schedule time for an AHJ stakeholder to physically come to the jobsite.
6. Environmental Health and Safety
The work at a manufacturing facility is often repetitive and can even be dangerous. Combining BIM with an environmental health and safety (EHS) mindset helps to offset some of the risks for the workforce. It makes it possible for teams to build the project in a way that supports the people doing the job.
Say a palletizer will stack a bottled beverage, then a shrink-wrapper will wrap it to prepare it to be loaded onto a truck. The model can make it easier to spatially plan how that prepared pallet will be loaded. Can the forklift safely access it on the conveyor? Are there any steps that can minimize accidents between pickup and loading?
The model can also illuminate unsafe areas, including:
- Pinch points
- Areas that will require workers to be at heights, exposing them to fall risks
- Areas with overly hot or cold temperatures
- Areas with excess noise
In doing so, modeling can show when it might be better to automate a part of the process rather than exposing a human worker to the in-play risks.
Because it allows stakeholders to visualize the project — which helps them picture and plan for how workers will operate in it — BIM is a valuable EHS tool.
Key BIM Uses After Closeout
BIM also has applications for manufacturing construction once the build is complete.
Maintenance Support
Manufacturing construction BIM models can help with planned maintenance. Owners want to make any shutdowns for maintenance purposes as fast and effective as possible. The model enables them to map this process, helping teams make sure they have appropriate access to the to-be-serviced equipment and that they’ll know what they face when they get there.
If the model is handed over to the owner at closeout, it becomes a helpful way to plan strategic maintenance. If the owner deploys the internet of things (IoT) for the facility, an alert from a sensor on say, an air handler, might go off. With proper integration, the model would show precisely which air handler is having the problem and where it’s located based on its IoT address.
Scott Bornman
Principal, Operational Excellence
Procore Technologies
As technology advances, BIM has more and more uses for maintenance support. For example, the model can integrate with augmented reality (AR) devices. This way, once a maintenance worker approaches the equipment they’re servicing, the AR device can show them what needs to happen overlaid onto what they’re seeing in the real world.
Manufacturing Optimization
Most facilities don’t stay static forever. For instance, a clothing manufacturer may have a facility prepped for an entire line dedicated to denim. As fashion trends change, though, they want to allocate space to chinos or corduroy. The denim came with extra requirements as far as the dyeing of the material, the finishing chemicals that were applied afterward and how the fabric was handled throughout the process, while corduroys may require less line space overall.
That means the owner has extra space with which to work, a precious commodity in any manufacturing environment. Leveraging BIM, they can explore different ways to use that space, helping them land at an optimal plan.
Stay updated on what’s happening in construction.
Subscribe to Blueprint, Procore’s free construction newsletter, to get content from industry experts delivered straight to your inbox.
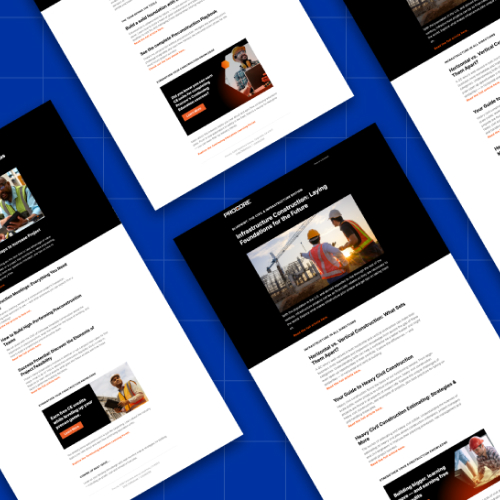
The Future of BIM in Manufacturing Construction
While BIM clearly holds a lot of promise in optimizing manufacturing construction and how facilities are run throughout their lifecycle, it has only scratched the surface. As digital processes like robotic manufacturing become more widely used, making the model interoperable with these technologies can deliver further efficiency wins.
Construction professionals then stand to benefit from starting to develop their BIM capabilities now. Individuals and teams can look to groups that have already successfully adopted BIM for inspiration.
First, start small. Plan a pilot project with a trustworthy team that’s excited about the possibilities of BIM. Document everything on that project and discuss what did and didn’t work with the project team. Ask for feedback and iterate on it.
Next, identify a larger project with the greatest likelihood of success. Scaling up and allowing teams to slowly build BIM proficiency helps with adoption and realizing early wins.
When teams embrace BIM in manufacturing construction, it can help the project move faster and more accurately, minimizing rework and optimizing the facility. Then, it can streamline maintenance and make future improvements easier.
Was this article helpful?
Thank you for your submission.
0%
0%
You voted that this article was . Was this a mistake? If so, change your vote here.
Scroll less, learn more about construction.
Subscribe to The Blueprint, Procore’s construction newsletter, to get content from industry experts delivered straight to your inbox.
By clicking this button, you agree to our Privacy Notice and Terms of Service.
Categories:
Tags:
Written by
Scott Bornman
Scott Bornman is a managing strategic product consultant at Procore Technologies. Scott began his long construction career after a successful 8+ years in the U.S. Army, where he selected to be U.S. Army Recruiter following Desert Shield/Desert Storm. Scott has had many roles in the construction field since then, working his way from a project superintendent, to an owner's rep, to a senior project manager and even Vice President of Construction at Bognet Construction and Director of Construction at Plaza Construction before joining the team at Procore.
View profileKacie Goff
55 articles
Kacie Goff is a construction writer who grew up in a construction family — her dad owned a concrete company. Over the last decade, she’s blended that experience with her writing expertise to create content for the Construction Progress Coalition, Newsweek, CNET, and others. She founded and runs her own agency, Jot Content, from her home in Ventura, California.
View profileExplore more helpful resources
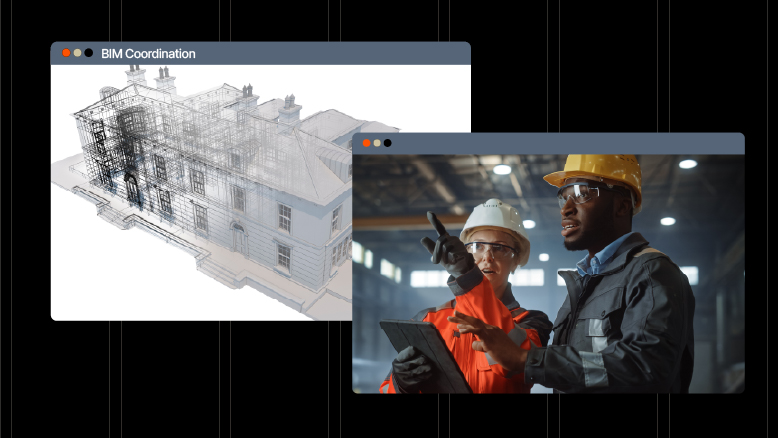
Streamlining Construction Projects with Effective BIM Coordination
The old saying goes: if you fail to plan, you plan to fail. Construction professionals know this better than nearly anyone. To take a project from a vision in an owner’s...
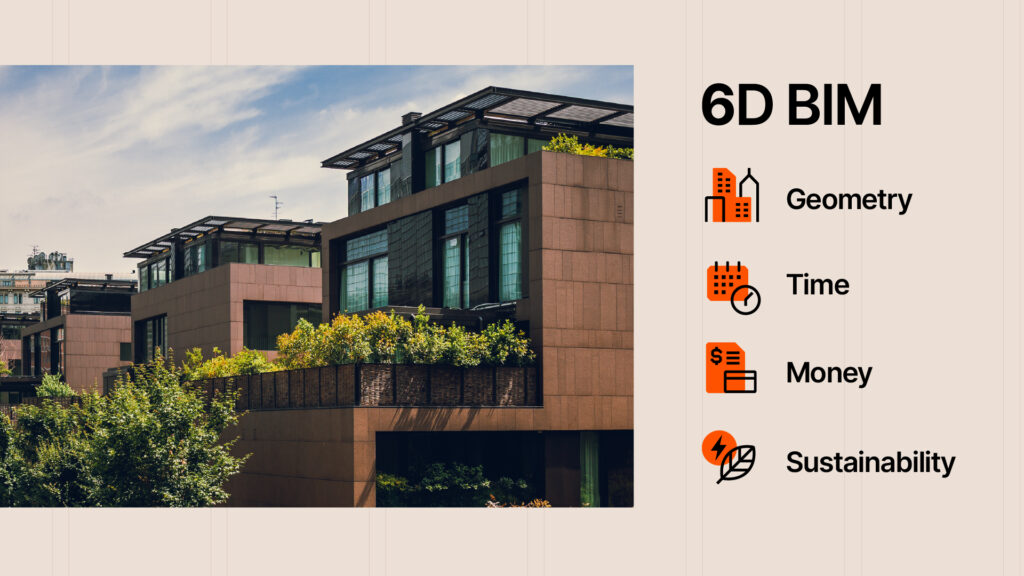
The Role of BIM in Sustainable Construction
Building information modeling (BIM) is transforming the architecture, engineering, and construction (AEC) industry. With this kind of sophisticated modeling, the industry has shifted from designing in 2D to 3D. This helps...
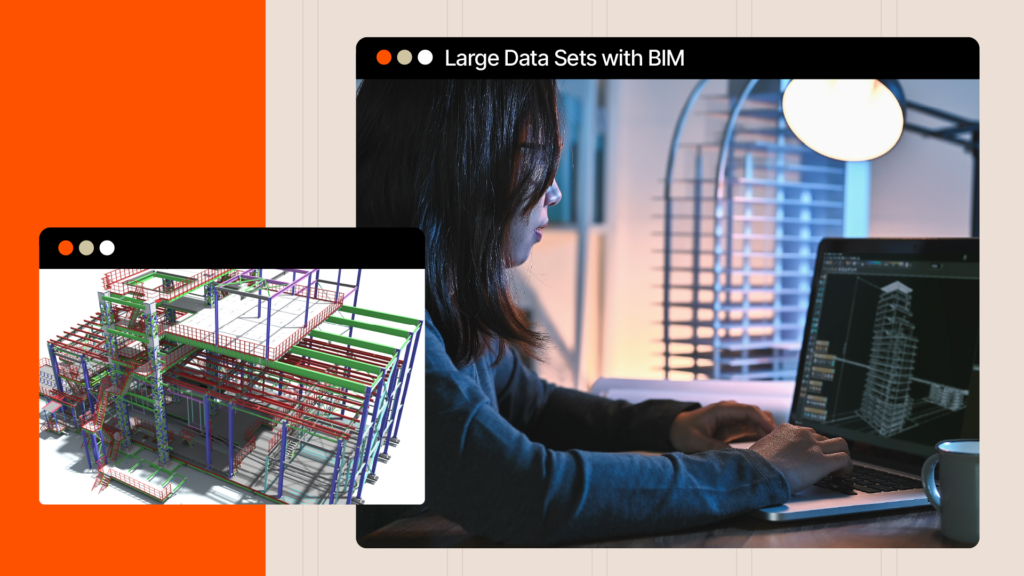
Building and Using Large Data Sets with BIM
In recent years, two technological concepts have exploded, almost in parallel: One, called building information modeling (BIM), makes it possible for stakeholders to “build” construction projects in a 3D virtual...
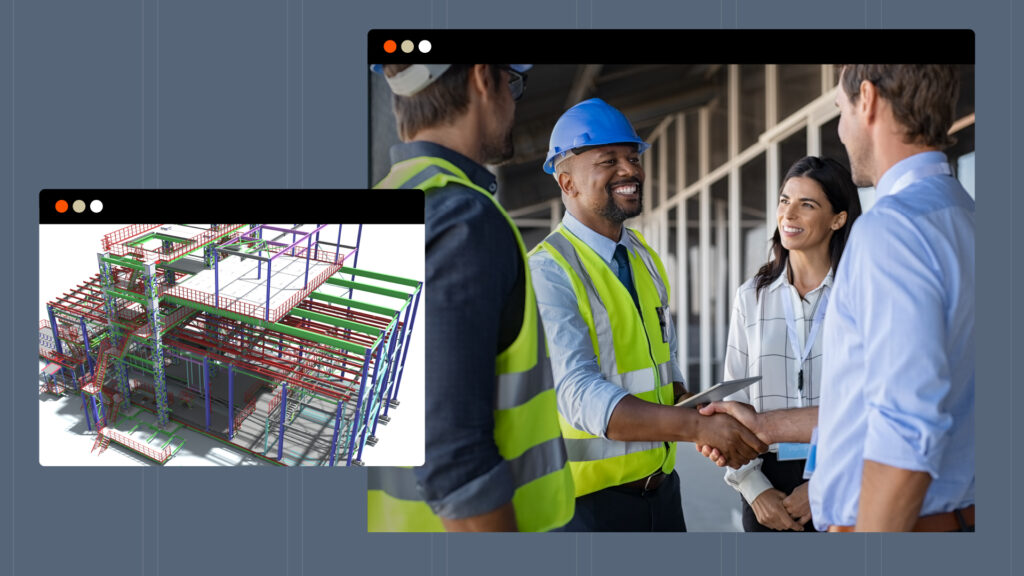
How BIM Enhances Control and Efficiency for Project Owners
Any construction project has a number of stakeholders. With a traditional project delivery method, it moves from designers and engineers in the architectural design process, to the general contractor and...