— 7 min read
Leveraging BIM for Quality Control
Last Updated Feb 25, 2025
Last Updated Feb 25, 2025
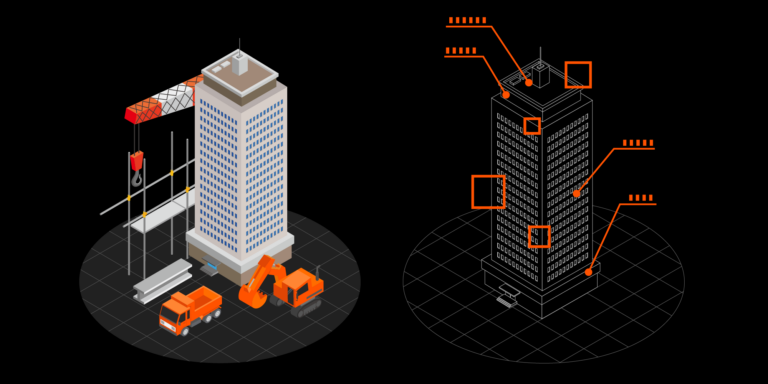
Anyone working on a construction project has a few priorities in play: delivering work per the drawings and specifications, doing so on time and on budget, and keeping everyone on the jobsite safe. Meeting all of those expectations requires a lot of consideration at all times. As a result, it could be easy for things to slip through the cracks. Fortunately, quality control (QC) tools can help here.
As construction technology advances — particularly in the field of virtual design and construction (VDC) — those QC aides have evolved, too. Plenty of construction professionals still use checklists and manual inspections, but building information modeling (BIM) can also come into play.
Specifically, BIM can be an additional tool leveraged as part of a project’s quality control processes.
Table of contents
BIM: A Quality Control Tool
The model developed through BIM serves as a highly useful quality control tool. When leveraged for construction activities, the model gives everyone a way to see key information from various partners (e.g., the architecture and design team, the general contractor’s BIM manager, the trades) aggregated into one place. That includes:
- Design drawings
- Shop drawings
- Installation drawings
- Drawings from specialty contractors
When anything various partners have modeled gets married into one federated model, each person on the project can see how components and systems interplay. They’re able to more accurately visualize what needs to be installed where and when, and then deliver on that.
In short, the BIM model can be leveraged so that everyone does it right the first time and in the proper sequence.
So that BIM can be most effective as a quality control tool, it’s important that the project has a BIM execution plan, or BEP. This aligns everyone on the details of the model (e.g., the level of granularity, the required tolerances) so everyone can use it in the same way.
Specific QC Use Cases for BIM
Construction professionals can leverage BIM to drive quality control in a handful of ways.
Visualization
When people think about using BIM for visualization, they often imagine a beautiful rendering. But the model has QC impact because it’s more than just a pretty picture. It allows all parties involved to see the intention of a space and how components and systems will work together. In fact, the model can make it possible to visualize what’s hidden on the actual jobsite (i.e., what’s above ceilings and behind walls) so people on the job can best plan and install in line with the overall goal for the space.
Spatial Coordination
sed alongside the drawings, specifications, and submittals, the model allows everyone to make sure things fit together properly. Because the model enables clash detection, it’s a powerful tool to identify and correct problems in the virtual space. This means teams can adjust as needed before changes cost labor and materials.
Prefabrication
A strong model allows systems and components to be prefabricated, then brought to the project and installed with a precise fit. In this way, components and systems can be created in environments where it’s easier to control quality.
Sequencing
The model allows teams to see not just where things are supposed to be, but how they relate to other pieces in the space. This enables appropriate sequencing of the installation. The person coordinating the project might realize, for example, that an entire system can’t be put in place all at once because its installation would limit access to a nearby component that requires room to work. With BIM, teams can better sequence the project in an effort to install the various pieces in the most efficient way.
Full Lifecycle Quality
If the model gets turned over to the owners — and particularly if it’s input into their computerized maintenance management system (CMMS) — it helps the owner maintain the building throughout the years. There’s no need to poke various holes in the walls to find a system that requires service, for example, because the model pinpoints that location.
Case Studies
To further illustrate how BIM can serve as a quality control tool on construction projects, a couple of healthcare examples help.
- To prevent employee falls and injury, the owner of a pharmaceutical project had a strict “no ladders” policy. As a result, the project required that all major service equipment be accessible via scissor lift. By inputting a high level of detail into the model — including furniture like desks — the team could coordinate spatially to build in the required footprint at each potential service point.
- A hospital project leveraged the BIM model to improve quality control for its piping. The model made it possible for the mechanical contractor to prefabricate 20-foot racks of water, hot water, and gas piping, complete with the required valves, in a safe and controlled shop environment. Plus, the racks could be built on the floor rather than at their to-be-installed ceiling height, making the work safer and easier for the team — which supports quality workmanship. The contractor capped the ends to pressure-test the racks as a QC measure before shipping them to the jobsite. This resulted in the streamlined install of piping in which everyone could have a high level of confidence.
Using BIM to Avoid Rework
There’s one area where BIM is such an effective QC tool that it’s worth calling out specifically: the avoidance of rework. Rework diminishes the quality on a project in a number of ways:
Safety
Per research published in the Journal of Construction Engineering and Management, “Rework is positively linked with increased safety risks.” When a project requires rework, there’s a one-in-four chance that the rework will result in an accident. Jobsite injuries hurt the individual worker, of course, and are worth avoiding for that reason alone. But because they can cause delays and incur additional costs, they hamper overall project quality, too.
Efficiency
Rework has a direct — and negative — impact on the project’s budget and timeline, both of which make up a big share of the project’s overall perceived quality. That assumes, too, that identifying who caused the rework and who’s consequently responsible for fixing it goes smoothly. It’s not uncommon for finger-pointing to cause further delays. In short, when work has to be reperformed, it lessens the job’s cost and schedule efficiency, often in significant ways.
End Project Result
It’s very rare for rework to be performed with the same quality as the original work. Trade partners often lose their initial pride in the craftsmanship they delivered the first time around. From the patch in the drywall to the fixture that doesn’t match the original finishes, rework can have lasting effects on the project’s quality.
In short, when teams can install things right the first time and avoid rework, it goes a long way toward controlling quality on the project. Since BIM provides such an asset for placing, sizing and otherwise specifying installation, it serves as a valuable QC tool.
Courses about construction.
For construction.
Unlock your career potential with our free educational courses on Health & Safety, Data in Construction, and more.
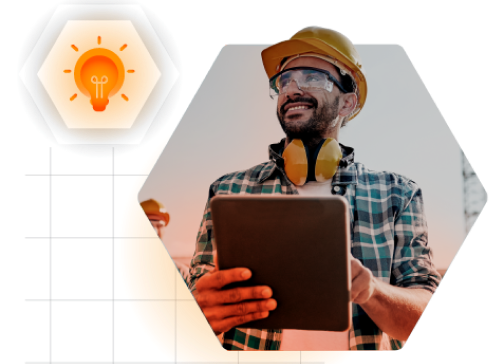
The Evolving World of BIM and Quality Control
As companies build their tech-powered arsenal of quality control tools, BIM represents a valuable addition. And as teams deploy more technology, it becomes even more effective. If trade partners use robotic total stations, for example, the model can power ultra-precise placement. Teams no longer have to pull measuring tape and, consequently, introduce the risk of quality loss due to human error.
One caveat here: BIM isn’t a be-all-end-all QC tool (yet) because not everything represented in the contract documents is modeled (again, yet). The more accurate and complete the model is, the more valuable the model becomes as a quality control tool. It’s important for stakeholders to be aware of gaps in the model — or differences in level of detail — that could impact quality control processes.
Field accessibility represents another important factor in the effectiveness of BIM for QC. The team in the office can create a robust model, but if it’s not useful on the jobsite, it’s only effective for quality control up until a point. Building faith in the model and making it easy to use in the field makes it a powerful tool for avoiding rework. As a result, BIM has the potential to notably and positively impact the project’s quality.
As BIM usage grows, particularly in the field, and new technologies expand its use cases, models should become an increasingly valuable tool in any company’s quality control arsenal.
Was this article helpful?
Thank you for your submission.
0%
0%
You voted that this article was . Was this a mistake? If so, change your vote here.
Scroll less, learn more about construction.
Subscribe to The Blueprint, Procore’s construction newsletter, to get content from industry experts delivered straight to your inbox.
By clicking this button, you agree to our Privacy Notice and Terms of Service.
Categories:
Tags:
Written by
DJ Phipps
DJ Phipps has spent over two decades working in the building and design industry. He's dedicated to using technology to make work easier and more efficient, with a focus on project management and improving systems. DJ now plays a key role at Procore as a Senior Principal Strategic Product Consultant.
View profileKacie Goff
54 articles
Kacie Goff is a construction writer who grew up in a construction family — her dad owned a concrete company. Over the last decade, she’s blended that experience with her writing expertise to create content for the Construction Progress Coalition, Newsweek, CNET, and others. She founded and runs her own agency, Jot Content, from her home in Ventura, California.
View profileExplore more helpful resources
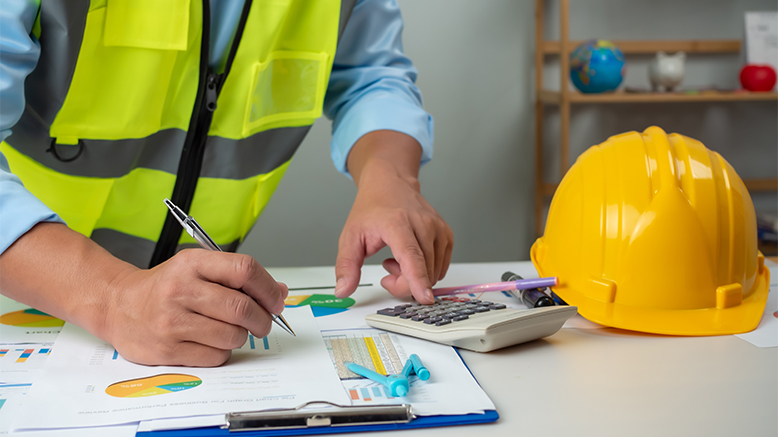
Understanding Subcontractor Bid Packages in Construction
Construction bid packages can have a cascading impact on the success of a construction project. The quality of a bid project may affect the quality of the bids, which in...
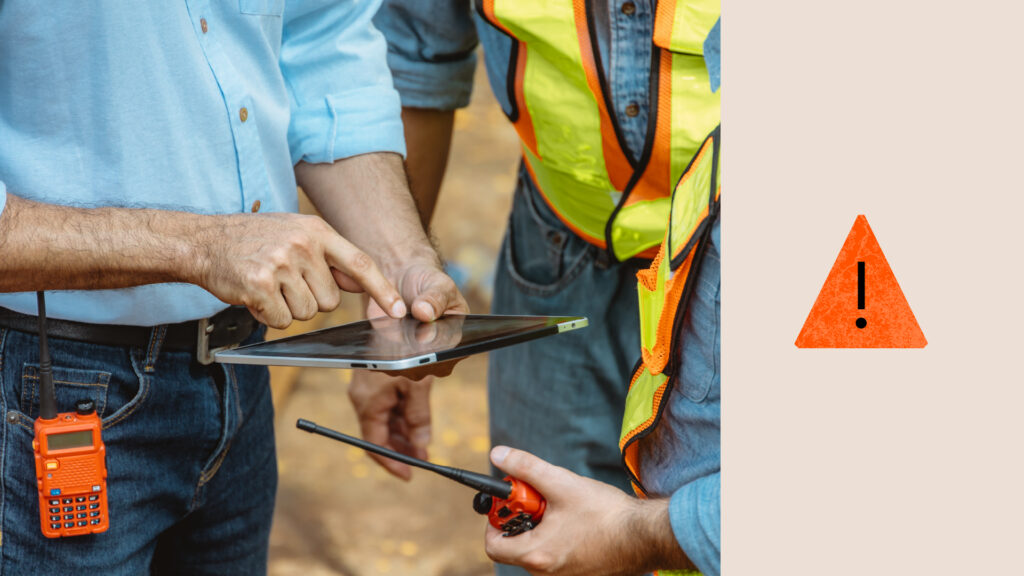
Tackling the Top 10 Construction Industry Issues
The construction industry is constantly evolving, bringing both opportunities and challenges. Companies must navigate an array of construction industry issues — from workforce shortages to integrating new technologies into their...
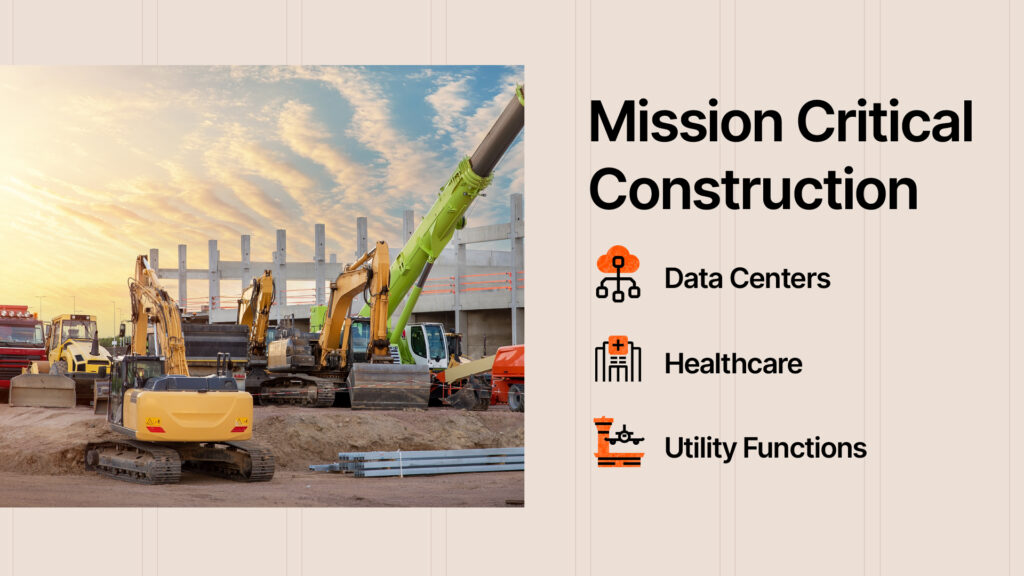
Mission Critical Construction: Strategies for Success
Mission critical construction involves building structures whose functions cannot afford to fail, as any disruptions can lead to significant consequences for society. Keeping data centers, hospitals, power plants and other...
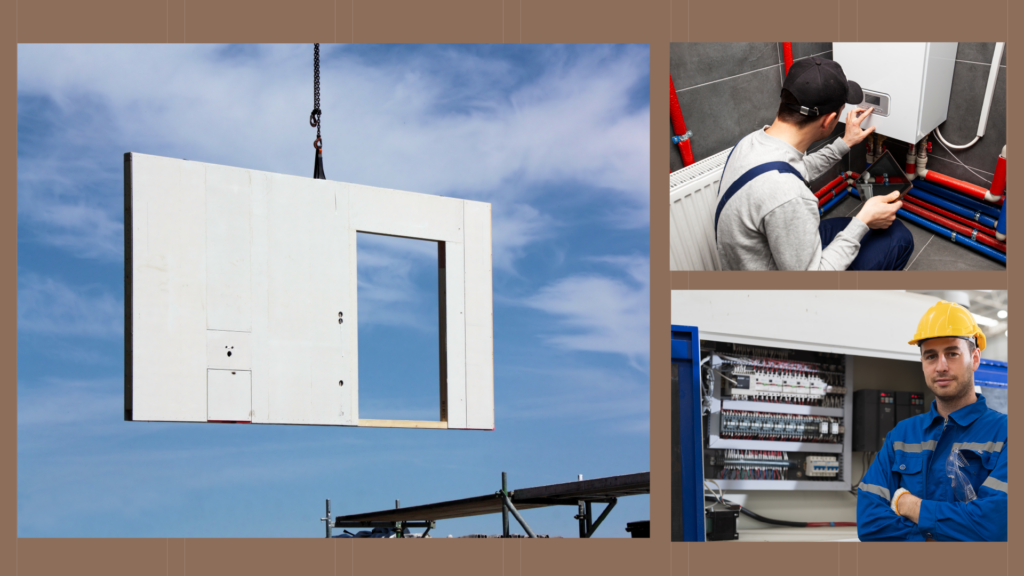
Modular Construction and MEP: A Collaborative Pairing
In an age of supply chain disruptions, workforce shortages, and rising material costs, off-site construction — including modular construction methods and prefabricated materials — is surfacing as a multipurpose solution....