— 10 min read
The Role of BIM in Sustainable Construction
Last Updated Apr 10, 2025
Last Updated Apr 10, 2025
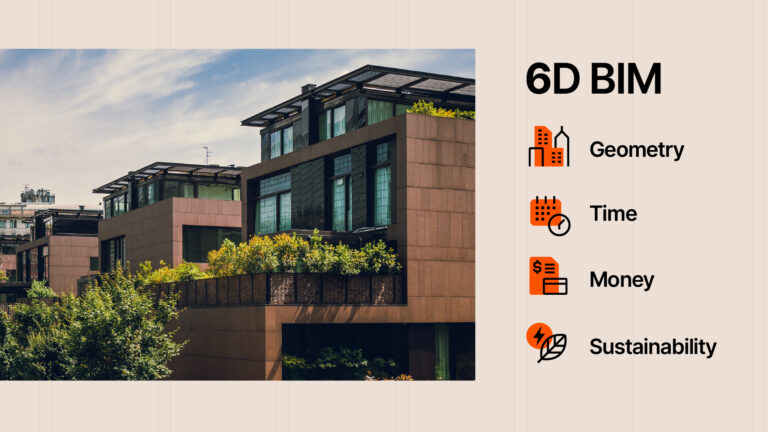
Building information modeling (BIM) is transforming the architecture, engineering, and construction (AEC) industry. With this kind of sophisticated modeling, the industry has shifted from designing in 2D to 3D. This helps teams visualize and optimize the project. The model can, for example, automate material takeoffs and enable clash detection.
It’s a useful tool to make projects more sustainable. While BIM often gets deployed for large-scale projects, research shows that it can enhance sustainability on smaller builds, too. Leveraging the model for better-planned projects that yield more efficient buildings can lead to cost savings for all stakeholders.
Table of contents
Sustainability: The Sixth Dimension of BIM
Sustainability is one of the expanding dimensions of BIM. Teams have started overlaying the schedule on the model to arrive at 4D BIM, and attaching cost to the model to get to 5D BIM.
Why stop there? Some BIM experts have started exploring up to 10 dimensions of BIM — and folks don’t need to go all the way to ten to get to sustainability.
In fact, using BIM for sustainability comes much earlier. This approach has secured its spot as the sixth dimension of BIM.
What, precisely, does that mean? 6D BIM means attaching sustainability-focused data to the model, like data about a material’s carbon footprint or a system’s energy usage. This allows stakeholders to see what environmental impact the project will have during construction and through the building’s lifecycle.
Ways To Use BIM for Sustainable Construction
Because a wide variety of data can be attached to a BIM model, there are a lot of use cases for leveraging BIM for sustainable construction. Here are six key ways to apply 6D BIM.
1. Owner Education
It can be challenging to convey to an owner the impact of the design decisions they make. Modeling the project in 3D makes it easier.
On a very basic level, it can help owners visualize how different choices will affect the space. They can, for example, use the model to make decisions around access to critical areas of the building (i.e., areas with mechanical systems). With the model, they can best position systems for easy access, supporting maintenance that helps the building operate more efficiently and sustainably.
Beyond that, the model makes it possible to run a variety of simulations that can inform the owner’s decision-making. It can be used to perform an energy analysis with different systems in place, for example. That demonstrates to the owner how much money they can save over the building’s lifespan by choosing more sustainable options.
2. Determination of Optimal Building Orientation
BIM becomes useful from a sustainability perspective even in the earliest stages of the design process. Modeling allows the design team to determine how structures should be shaped and positioned to optimize energy efficiency and occupant experience.
For example, shifting the foundation over or rotating the building might prevent direct sunlight through windows on hot summer days. Designers can simulate how the structure will perform based on where the envelope is placed. This allows them to lay a figurative cornerstone that builds sustainability into the project from its earliest planning steps.
3. Design of More Efficient Buildings
Once the placement of the building is determined, BIM can continue driving more sustainable decision-making. To illustrate, it can be used to plan the layout of the windows to optimize daylight, minimizing the electricity required to create functional spaces for occupants. Or the model can be leveraged to simulate energy consumption in different seasons, pinpointing the most sustainable HVAC solution.
And as new platforms and plug-ins come onto the scene, it’s becoming even easier to use BIM for sustainable construction. When carbon footprint data is attached to individual model elements, adding those elements immediately informs design teams of their impact. This helps designers choose elements that do minimal environmental damage while still complying with the owner’s design intent.
4. Minimization of Material Waste
On jobsites, 30-yard dumpsters of material that got ripped out because of poor sequencing are not an uncommon sight. Neither are scrap heaps of excess material that didn’t get used.
While it’s early days yet, BIM has the potential to change things here. It can make it easier to see, for example, how trades are stacked above ceilings or in corridors. That helps to prevent specialty contractors from performing work prematurely. By minimizing rework, BIM also minimizes material waste.
In addition to the 4D (scheduling) benefits of BIM, this modeling effort can also refine — and even automate — material takeoffs. This way, the right amount of materials come to the site at the right time. This further reduces waste by preventing materials from getting damaged by the elements or other contractors moving around them.
Here, BIM doesn’t just improve sustainability. It also delivers cost savings for contractors by enabling them to order more precise material quantities — and to best use what they do order.
5. Logistics Optimization To Minimize Transmissions
Because BIM makes it easier to order more precise material quantities and prevents the need to order more due to rework, it impacts a project’s total emissions. By helping to facilitate the delivery of the right amount of materials, it avoids additional transportation — and the resulting emissions. This, in turn, brings the transportation costs on the project down.
6. Achievement of Sustainability Certifications
Today, owners have a variety of green building certifications from which they can choose. Not only do these have the potential to boost positive reception in the community and lure tenants, but they deliver cost savings over the building’s lifecycle, too. Leading certifications in this category include:
Whichever certification owners choose, it can reduce the build’s environmental impact and yield cost-savings. As an example, the U.S. Green Business Council reports that LEED-certified government buildings use 27% less energy and cost 19% less to operate than the national average. A single LEED-certified building — the Department of the Treasury’s headquarters — saves U.S. taxpayers $3.5 million per year.
That said, achieving any of these certifications is usually a sizable undertaking that requires extensive documentation. Fortunately, BIM can make that easier.
If the owner knows they want to achieve a certain certification, for example, teams can tag the required information as they add that data to the model. When everything is organized in the model, it gets much easier to compile and turn over the required data to the certifying agency.
Sustaining Buildings After Closeout
By choosing sustainable materials and systems during design and efficiently installing them during construction, BIM reduces a project’s environmental impact. The sustainability benefits don’t stop there, though.
6D BIM feeds into the next dimension of BIM: using the model for facility management and operations, or 7D BIM. Here are just a few ways the owner might use the model.
Strong Maintenance for Optimal Efficiency
The model can feed into tools the owner uses to maintain the building, like their computerized maintenance management system (CMMS). If they set up notifications overlaid with the model or deploy sensors alongside it, maintenance personnel can see what needs attention when. They might get an alert to change a specific air filter, preventing the cooling system from using excess energy to provide the required air flow and temperature. The model might help them find an access panel they otherwise wouldn’t have known about, too, making their work easier and more efficient.
Minimizing HVAC Energy Consumption
The owner can use the model to simulate how the position of the sun affects the light and temperature in different rooms. They can then use window coverings to offset unwanted effects (like excess air conditioning during summer months).
Identifying and Executing Retrofit Opportunities
Using the model in tandem with other data generated during the building’s lifecycle helps owners identify where the building uses the most energy. To improve its sustainability and yield operational cost-savings, the owner might pursue targeted retrofit projects. And with the model paired with reality capture tools, that work can be tackled more strategically. A wall might not need to be demolished, for example, because teams can see precisely what’s behind it thanks to the model. This minimizes total project cost, and means that the retrofit needs fewer materials, in turn improving sustainability.
Courses about construction.
For construction.
Unlock your career potential with our free educational courses on Health & Safety, Data in Construction, and more.
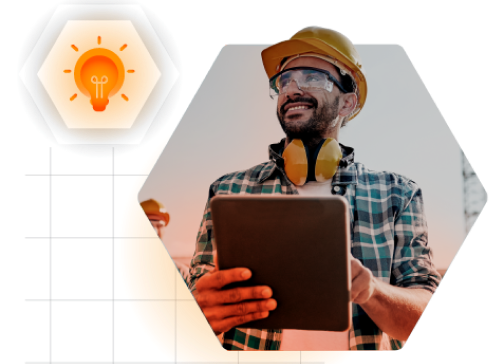
Developing Strong BIM Practices for Sustainability
BIM can support progress toward a wide range of sustainability-focused goals. As a result, there’s no one-size-fits-all application. Instead, companies need to determine how, when, and why to deploy building information modeling. For help there, they can:
Clearly Identify Sustainability Goals
As owners increasingly ask for a turnover model, teams are served by trying to understand both how the owner will use that model and how it aligns with their sustainability goals. For that, ask the owner some targeted questions, including:
- What is the overall objective of the project?
- What’s the intended use of the building?
- Who are the people who will be occupying it?
- How will those people use the space?
- Is the owner trying to meet any efficiency standard (e.g., construct a net-zero building)?
- Do they want to secure a specific green building certification (e.g., LEED, BREEAM)?
Talking with owners about big-picture questions like those help to identify project goals. Then, teams can determine how best to deploy BIM to accomplish those objectives.
If, for example, the owner wants the building to be LEED-certified, the model can be used strategically. If teams attach data that will be needed for certification to the model as they go along, compiling the required documentation gets much easier. The model can also be used to check that the project meets applicable standards, as design and constructability decisions are made.
In other words, meeting or exceeding the certification gets built into the design and construction process. This way, the owner doesn’t have to bring on additional headcount for documentation gathering or retrofit areas that fell short.
Practice Good Data Hygiene
As with all data-related topics, decision-makers need to remember: garbage in, garbage out.
Bad data makes room for rework (material waste) and buildings that function less efficiently. Good data, on the other hand, powers good models that drive good sustainability practices.
As a result, teams with an emphasis on sustainability need to take the extra time to validate data. Make sure the cost catalog matches the model so takeoffs can be automated, for example. Assigning responsibility for good data hygiene to certain team members (e.g., the architect or general contractor’s BIM manager) can help here.
Cultivate the Right Tech Stack
Make sure the team is choosing the right tools for the job. If sustainability will be a primary focus of the project, seek out BIM authoring platforms and plug-ins designed to help. If the project would benefit from a certain type of sustainability simulation or analysis, for example, look for tools that offer that functionality natively or via an application programming interface (API).
It’s also important to create a tech stack that helps to bring the model to the field. If the office team does extensive BIM work to boost the project’s sustainability but that doesn’t reach the jobsite, it loses efficacy.
As BIM technology gets more sophisticated, planning and maintaining more sustainable buildings should get easier. Taking steps to leverage this BIM for sustainability now sets teams up for success.
Was this article helpful?
Thank you for your submission.
0%
0%
You voted that this article was . Was this a mistake? If so, change your vote here.
Scroll less, learn more about construction.
Subscribe to The Blueprint, Procore’s construction newsletter, to get content from industry experts delivered straight to your inbox.
By clicking this button, you agree to our Privacy Notice and Terms of Service.
Categories:
Tags:
Written by
Adam Fairbairn
Adam is a BIM solution specialist and Lead Solutions Engineer at Procore Technologies. He works ollaboratively with company owners, construction managers, general contractors, architects, engineers and specialty contractors to discover their needs and identify solutions to meet those needs.
View profileKacie Goff
54 articles
Kacie Goff is a construction writer who grew up in a construction family — her dad owned a concrete company. Over the last decade, she’s blended that experience with her writing expertise to create content for the Construction Progress Coalition, Newsweek, CNET, and others. She founded and runs her own agency, Jot Content, from her home in Ventura, California.
View profileExplore more helpful resources
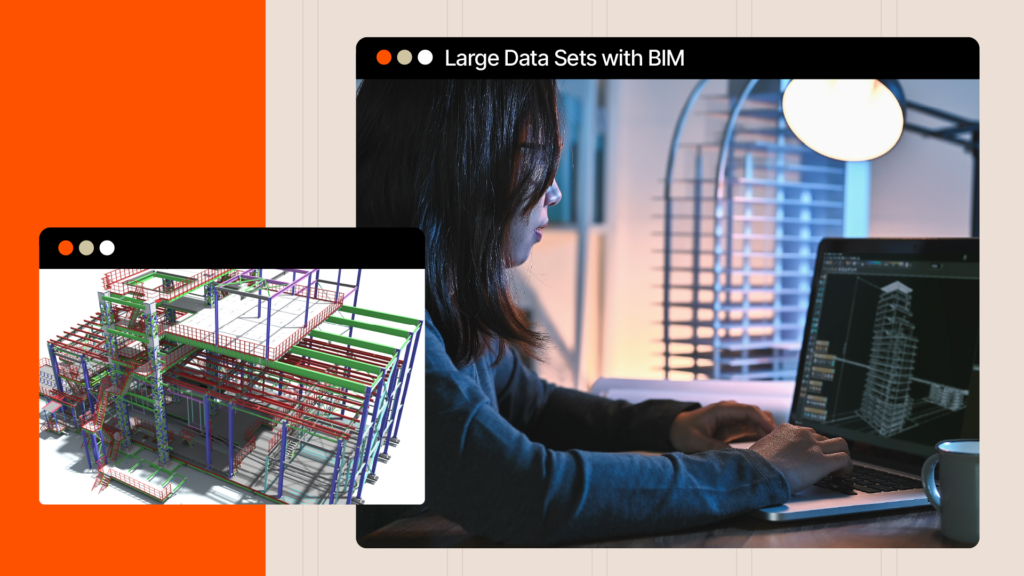
Building and Using Large Data Sets with BIM
In recent years, two technological concepts have exploded, almost in parallel: One, called building information modeling (BIM), makes it possible for stakeholders to “build” construction projects in a 3D virtual...
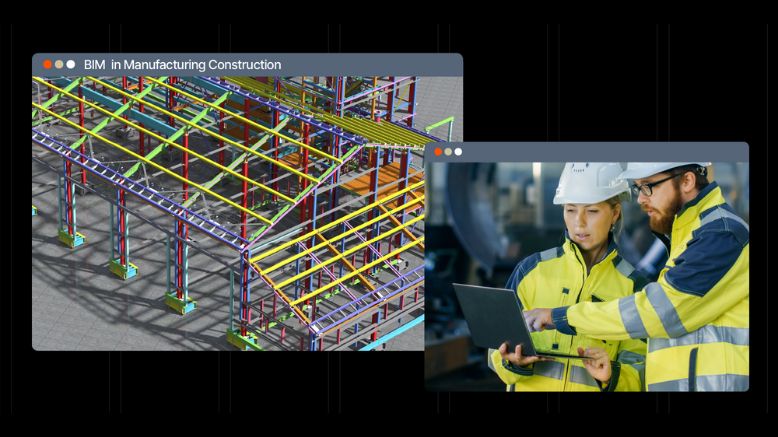
Exploring BIM’s Potential in Manufacturing Construction
As building information modeling (BIM) improves, project owners can build more sophisticated facilities faster. And as consumers increasingly demand what they want delivered to them faster, brands need smarter manufacturing...
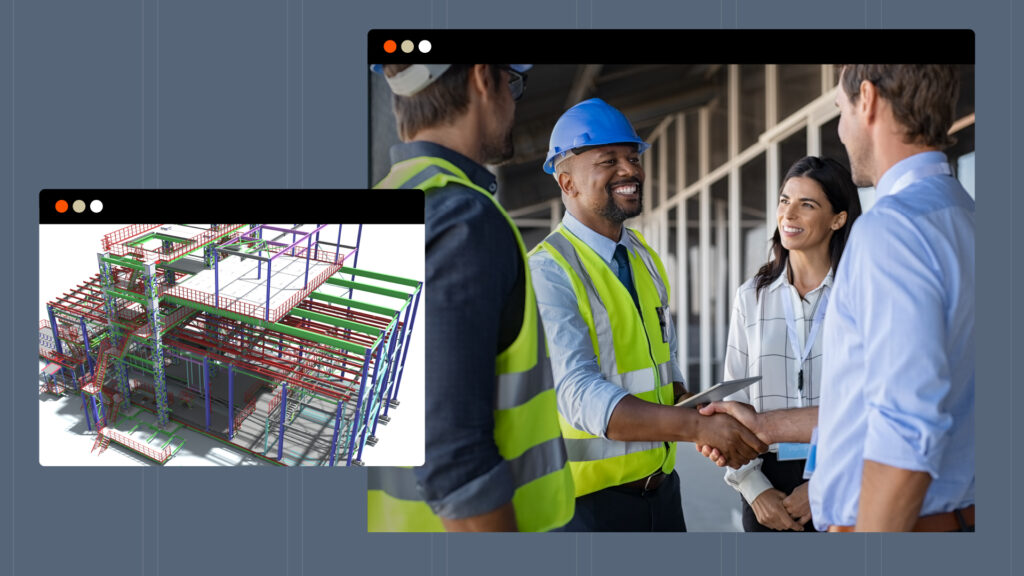
How BIM Enhances Control and Efficiency for Project Owners
Any construction project has a number of stakeholders. With a traditional project delivery method, it moves from designers and engineers in the architectural design process, to the general contractor and...
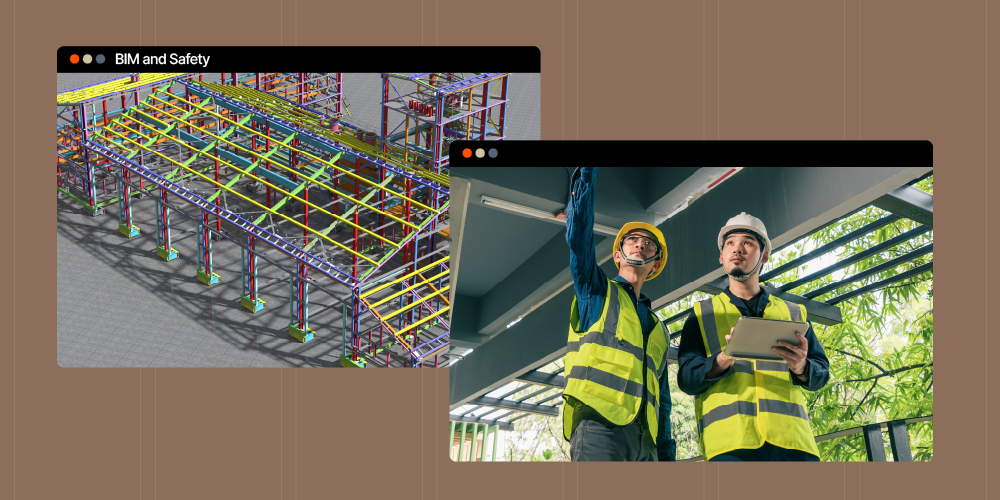
Enhancing Construction Safety with BIM Technologies
The construction industry is no stranger to tools: Even ancient civilizations developed mallets and axes to make their work easier. Today’s latest tools look different, but they can be as instrumental...