— 9 min read
Cold Storage Construction: Building for Below Zero
Last Updated Mar 21, 2025
Last Updated Mar 21, 2025

Food is necessary to human life, and society has evolved to rely on a massive food system and supply chain, which depends in turn on the ability to store large amounts of goods at refrigerated, sometimes freezing temperatures.
These places, called cold storage or controlled environment buildings, are a marvel of modern engineering — and building them has unique challenges and considerations that differ from typical commercial projects.
This article explores how cold storage construction works, including the process from preconstruction to closeout, its distinctive safety features, the complexities of material and equipment selection, and the importance of specialized contractor expertise.
Table of contents
Sealing the Cold Storage Envelope
At the core of cold storage construction is the management of extreme temperatures, ranging from a cool 50 degrees to a frigid negative 70 degrees Fahrenheit. These conditions demand a well-designed envelope—the barrier between the controlled interior environment and the external climate.
Choosing the right envelope system is vital to cold storage design and takes up a major part of the planning and design phase, which will be discussed below.
Some clients with smaller cold storage needs may opt for a bespoke box — like a walk-in freezer in a restaurant, for example. Some cold storage boxes, like this 30-foot-long cube that’s built for special events, are essentially refrigerated shipping containers.
Many cold storage clients, however, need to store massive amounts of food in transit to grocery stores and markets. This is part of securing the cold supply chain — keeping food items fresh and in shape from the time they’re picked or processed until they reach the hands of consumers. To hold such large amounts of food, many clients will need a proper cold storage facility — essentially a temperature-controlled warehouse. In fact, many of these facilities are existing warehouses that have been retrofitted to regulate temperature with an envelope.
In new developments, though, the building’s design itself can work as part of the envelope, with insulated panels serving as the walls. Though much more costly, this method of building cold storage allows for a crew to essentially build a skyscraper of cold storage, such as the NewCold facility in Idaho, which opened in 2019 and is 14 stories tall. Most new construction in cold storage is 40-50 feet clear, and at those heights costs may be more comparable to retrofits.
Deciding which of these methods to take depends on the client’s budget and needs. Retrofitting, for example, may be faster, but the efficiency and scale of a new building may save costs in the long run — and may have fewer harmful environmental impacts.
The Cold Storage Construction Process
Beyond the envelope, much of the construction process for cold storage is similar to other types of commercial construction — though the materials, technology and safety considerations might differ from other projects.
The following takes a deeper look at how the building and envelope are made throughout the construction process.
Preconstruction
Food is a subsidized but privatized industry in the U.S., and most owner’s reps are going to be coming from commercial food distributors, or otherwise companies that focus on maintaining controlled environment buildings for those food distributors, such as Americold Realty Trust.
Budgets are going to increase depending on the scale and complexity of the project, as well as the type of refrigeration system that’s being implemented.
I generally try to tell my clients that building a new cold storage facility is going to start in the ballpark of three times the cost of a traditional industrial building. That’s your most basic building. If you’re doing anything complicated–multiple temperature zones, processing components, automation — it’s going to go up significantly from there.
Kate Lyle
Principal Architect
Lamar Johnson Collaborative
As a commercial construction project, cold storage construction will require working the appropriate Authorities Having Jurisdictions (AHJs) and securing local building permits, as well as adhering to local regulations — especially fire and life safety protocols, which are important in these facilities and often different than the systems seen in other buildings due to the low temperatures.
Planning and Design
Because of its specialized nature, this type of construction requires working with architects who have experience in cold storage. These architects may be more involved with the build than in other projects, keeping in contact with the general contractor (GC) and collaborating on the order of the build.
Some of the warehouses may also include workspaces, with offices and spaces for people to meet. This requires planning for best ways to maximize use of the space — an office worker must have a safe path to the loading dock, preferably without having to walk through sub-zero temperatures in storage spaces.
There are many kinds of refrigeration systems, and choosing the right one is important for the project. These systems are regulated by EPA— some have high global warming potential, and others can be ozone-depleting. Since these regulations can change over time, an architect shouldn’t rely on a refrigeration system that’s worked in the past — it could already be outdated. Another important piece of equipment for cold storage buildings is the loading dock —
the area where items will enter the building. Most cold storage facilities use specialized dock equipment that’s insulated and sealed to maintain the thermal envelope.
Construction
If possible, subcontractors hired on these projects should be familiar with cold storage or food-centered buildings. All contractors and trade workers must understand the design of the envelope and how their tasks affect it. Cutting corners with design might be possible for other types of construction, but it can have really adverse consequences in a controlled environment building.
For example, on these buildings, a roof isn’t just a roof — it’s the cap that traps the air and humidity inside, maintaining the temperature. The juncture where the wall meets the roof is critical, and where many problems might arise. In these parts, insulation must go all the way to the corner, and vapor barriers — sheets that help control the humidity by reducing the amount of vapor that can move across them — have to be wrapped tight around the building.
All materials will need to be proven to work in cold temperatures. While concrete and metals are generally fine in cold conditions, don’t overlook smaller materials — sealant, for example, needs to be certified by its producer to be used in cool and below-freezing temperatures. This type of build will require working with usual subcontractors — mechanical, electrical, plumbing, fire and life safety — as well as a handful of specialized subcontractors.
Thermal contractors must be hired to install insulated panels to secure the envelope, and refrigeration subcontractors will be needed to build and install cooling system parts.
Even though refrigeration is part of the mechanical system of the building, most mechanical subcontractors will focus mostly on HVAC installation. It’s important to note that the two aren’t interchangeable, and the job will require an experienced refrigeration contractor.
Closeout
Toward the end of construction, once the envelope is fully in place and sealed, it’s important to test it by dropping down the temperature. This is a crucial moment for the project — as the temperature lowers, sealant can be broken, cracks can even form, and walls can even start to pull apart.
Small cracks may be fixed with caulk, but big ones threaten the integrity of the envelope. If ice forms, it’s a sign that the envelope is compromised. These issues might require design changes, even to pull down walls and put them back up with proper insulation and vapor barriers.
In terms of inspections, in addition to the usual ones required for every construction project, there may also be air quality inspections as well as visits from the health department, which will check for the risk of food contamination.
Because of the specialized nature and complex systems involved in these buildings, educating the owner and rep about maintenance is a large part of the handover process. Make sure they know how to change temperatures, as well as how to work the loading dock equipment.
Unique Challenges of Cold Storage
All construction sites involve risk, and a cold storage worksite has many of the same safety concerns as other types of construction. The following list contains a few examples of cold storage’s most notable safety challenges and risk of rework, which a GC should be aware of before starting the build.
Indoor rain
When insulation fails, condensation can form and precipitate inside the building, which can damage goods and also present a slip-and-fall hazard to workers or occupants. It’s absolutely necessary to secure and test the envelope to prevent this.
Sprinkler freeze
Goods stored in cold storage can be densely packed and highly flammable, but specialized sprinkler systems might be necessary, given the cold and sometimes sub-zero temperatures. These can be costly, and often fire codes move much slower than the technology of sprinkler systems, so it’s important to work with local fire and life safety regulators to approve the system before it’s installed.
High ceilings
Many cold storage facilities must accommodate high-piled storage and large columns of products. Roofing, insulation, and sprinkler systems must be installed. Taking proper precautions, such as installing safety ties if necessary, can help prevent accidents.
Ground freeze
The point of a cold storage facility is to bring the temperature down, but below the floor is soil and earth that can freeze, which can shift the foundation of the building or heave the slabs. It may sound counterintuitive, but the floors of cold storage buildings must have heating systems to mitigate this risk.
The Path to Success in Cold Storage
The unique demands of building facilities that maintain extreme temperatures can’t be underestimated. A GC must understand the intricacies of the thermal envelope, and prepare for the many challenges that could arise in a cold storage construction site.
By recruiting seasoned architects and subcontractors, a GC can not only meet the goals of the owner and rep, but also bring to life a complex system — half a building, half a machine—that works smoothly to keep food fresh for all of us.
Was this article helpful?
Thank you for your submission.
100%
0%
You voted that this article was . Was this a mistake? If so, change your vote here.
Scroll less, learn more about construction.
Subscribe to The Blueprint, Procore’s construction newsletter, to get content from industry experts delivered straight to your inbox.
By clicking this button, you agree to our Privacy Notice and Terms of Service.
Categories:
Tags:
Written by
Kate Lyle
Kate Lyle, NCARB, has 19 years of experience in architecture, specializing in complex project types including cold storage, food processing and food distribution since 2011. Kate has authored many articles, including co-authoring the e-book Best Practices in Cold Storage Facility Development for NAIOP. She has been featured on The Cool Times Podcast, The Beyond Engineering Podcast, and Building Design & Construction’s web series for Horizon TV. In addition, Kate has spoken on the topic of cold buildings at numerous regional and national conferences, including conferences for CEBA, NAIOP and ULI. Kate recently joined The Lamar Johnson Collaborative (LJC) as Principal.
View profileTrey Strange
26 articles
Trey Strange is a Peabody and Emmy-Award winning writer and producer based in Brooklyn, NY. Throughout his career, Trey has worked for the Huffington Post, Houston Chronicle, Out Magazine, Brooklyn Eagle, CNBC, INTO, and New York Magazine's Bedford + Bowery. He received his Masters in Journalism and Middle East studies from New York University, and Bachelors in the same subjects from the University of Houston.
View profileExplore more helpful resources
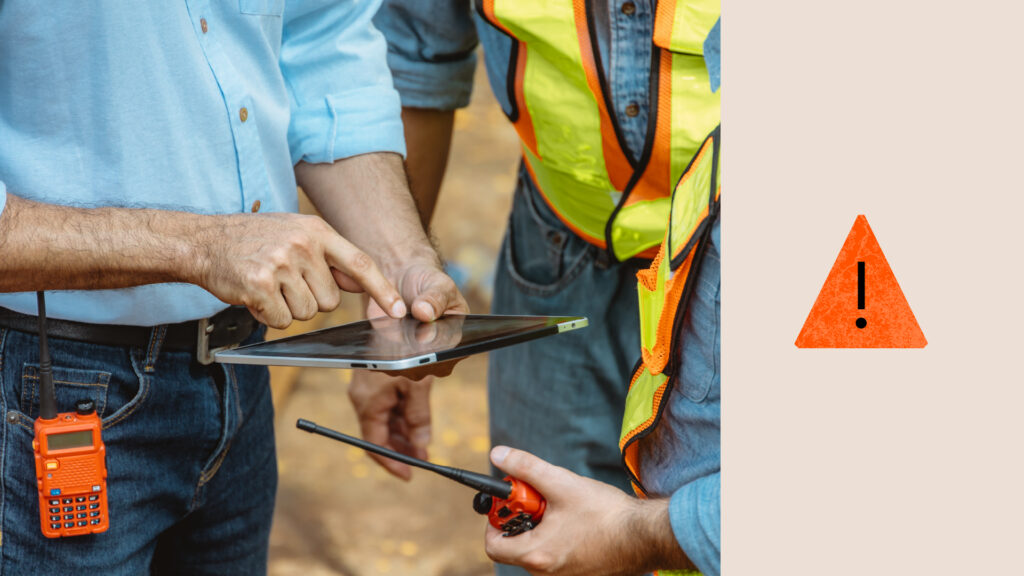
Tackling the Top 10 Construction Industry Issues
The construction industry is constantly evolving, bringing both opportunities and challenges. Companies must navigate an array of construction industry issues — from workforce shortages to integrating new technologies into their...
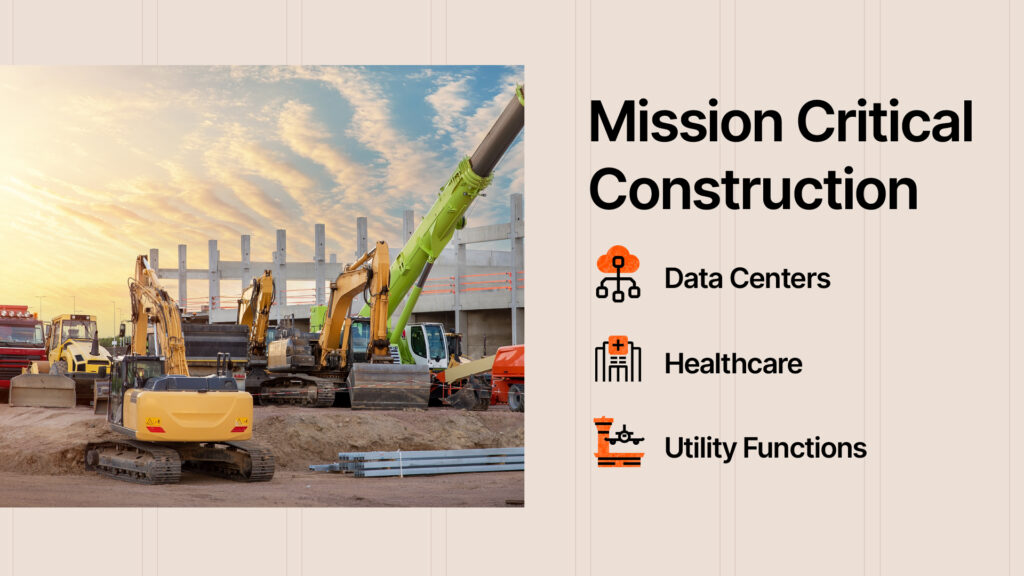
Mission Critical Construction: Strategies for Success
Mission critical construction involves building structures whose functions cannot afford to fail, as any disruptions can lead to significant consequences for society. Keeping data centers, hospitals, power plants and other...
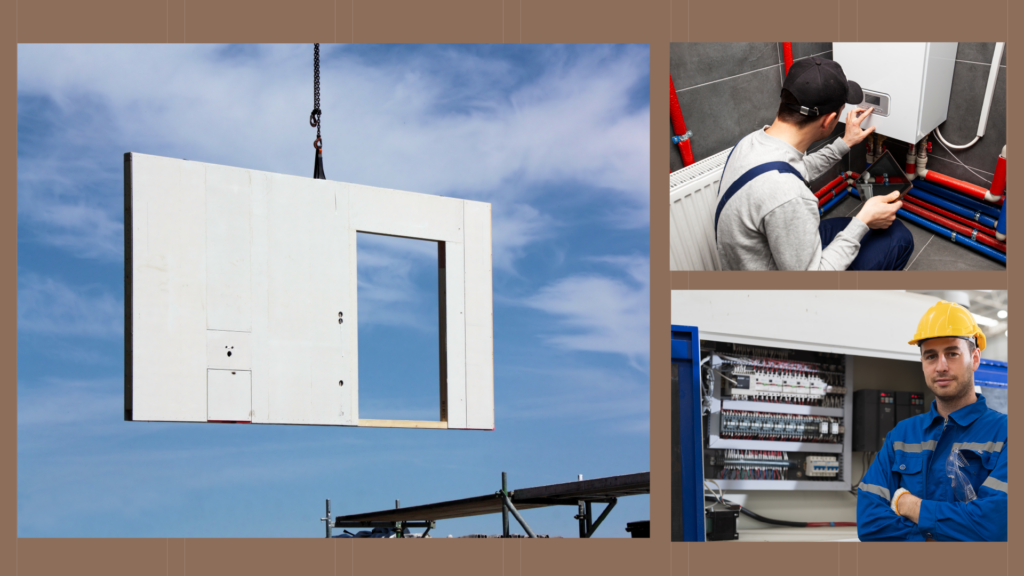
Modular Construction and MEP: A Collaborative Pairing
In an age of supply chain disruptions, workforce shortages, and rising material costs, off-site construction — including modular construction methods and prefabricated materials — is surfacing as a multipurpose solution....
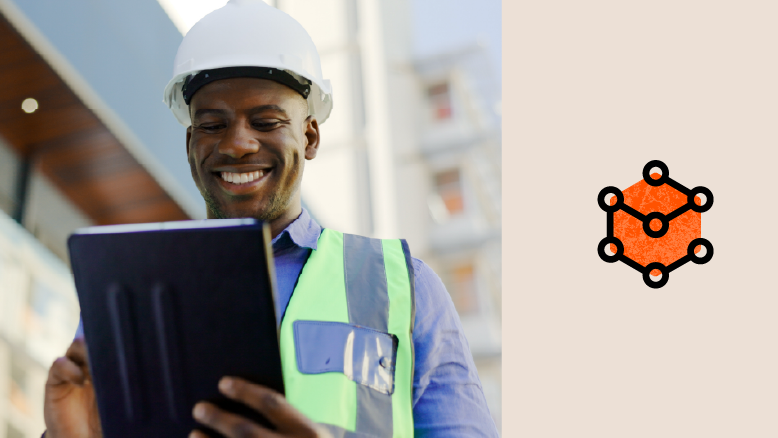
Connected Construction: Transforming the Industry Through Integration
Construction projects are becoming increasingly complex, so companies need to innovate to accurately and profitably complete these modern structures. Connected construction — using technology and data to improve communication, processes...