— 10 min read
Constructability Explained: Reviewing Designs for Building Risks
Last Updated Nov 14, 2024
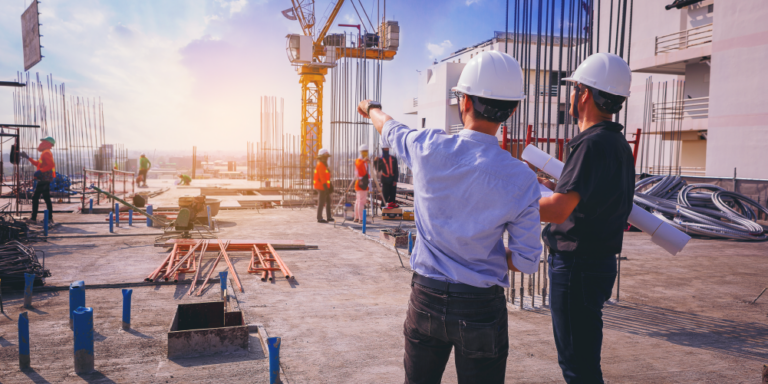
From the Guggenheim in Bilbao, Spain, the Walt Disney Concert Hall in Los Angeles, to 8 Spruce Street in Manhattan, Frank Gehry’s buildings are known for being one-of-a-kind, expensive, and beloved. His projects are also known for being delivered on time and on budget.
It can be challenging to complete even the smallest projects on time and on budget. Gehry’s ability to complete some of the world’s most ambitious and prominent projects as promised is made possible largely through long, precise planning phases where every design decision is scrutinized before construction begins. The process requires input from owners and builders and reviews every choice to determine whether it can be built, how best to do it and exactly how much it will cost. In other words, Gehry is assessing constructability.
Constructability is the extent to which construction designs can be effectively and efficiently executed. Analyzing for constructability is the act of reviewing designs in order to assess the feasibility and risk of constructing them, and finding solutions that better achieve project goals. This article explores constructability, including common issues and an exploration of constructability reviews.
Table of contents
What is constructability?
Design teams are capable of imagining extraordinary buildings. Constructability is where artistry meets reality. Can the designs be built? Are there ways to do them better, safer, more affordably and with less environmental impact?
Constructability is one of the most important considerations of preconstruction. Constructability analysis assesses whether a project can be completed and how to minimize the number of unexpected issues during construction that can lead to delays or increased expenses. Logistical constraints, material availability, site conditions and the efficacy of construction methods all have to be taken into consideration.
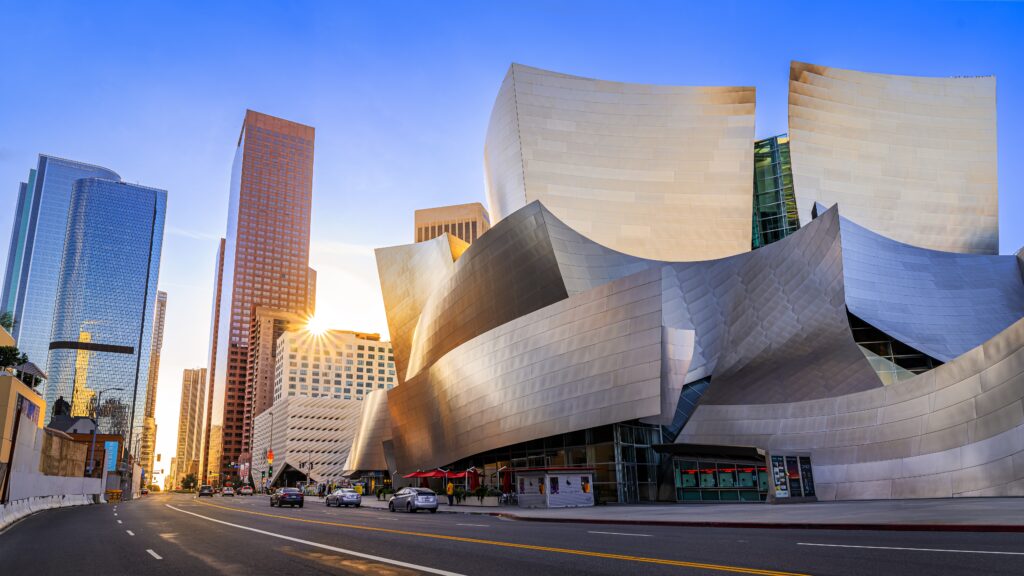
Constructability vs. Value Engineering
Constructability follows a similar process to value engineering. Both methods involve general contractors (GCs) working with the design team to assess and refine construction plans. However, value engineering focuses on increasing a project's value.
For example, a GC might evaluate a particularly expensive light fixture and find an alternative that’s similar but more affordable. On the other hand, a GC assessing a light fixture's constructability would ensure it can actually be installed and will function as expected or designed.
Constructability improves efficiency.
Many projects have formal constructability reviews, which are times when architects, engineers and contractors work together to evaluate and improve designs and plans. Everyone on a project team should be concerned with constructability, as increased constructability usually leads to decreased costs, reduced schedules and improved quality.
However, it’s a particularly important consideration for general contractors (GCs), who are mostly likely to have the construction knowledge and experience needed to truly assess for constructability. GCs are also ultimately responsible for executing what’s in the plans, so they’re invested in ensuring intended outcomes can be achieved, whether that’s a towering skyscraper being able to support itself or ensuring there’s enough space to install individual pipes.
Ideally, constructability concerns are caught and addressed during preconstruction, but, realistically, they will pop up throughout the course of construction. As concerns emerge during the build, GCs might use requests for information (RFIs) to ensure they understand the plans and change orders to define and execute solutions that better serve the final outcome. GCs should also have a good understanding of change management to keep the project as close to on time and on budget as possible as changes are proposed and approved.
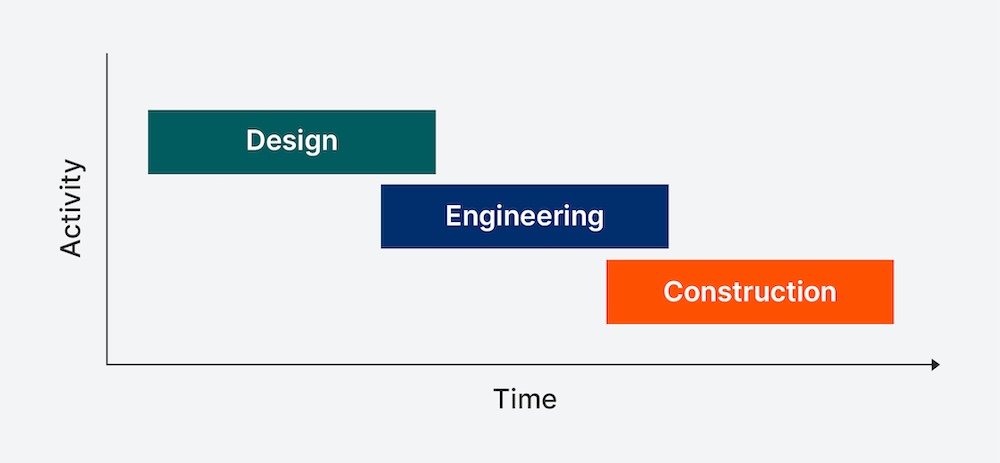
Why Constructability Matters
Constructability analysis assesses whether a project can be completed and how to minimize the number of unexpected issues during construction that can lead to delays or increased expenses, such as logistical constraints, material availability, site conditions and the efficacy of construction methods. This type of analysis should lead to solutions that improve the final outcomes of the project, which might include:
- Reducing cost
- Reducing the project schedule
- Improving the quality of the finished project
- Improving the safety and security of the project
- Decreasing the environmental impact of the project
- Minimizing rework and rescheduling that needs to occur
Common Constructability Considerations
Assessing constructability is almost always about identifying where the plans for a project won’t achieve their desired outcome and finding solutions. However, constructability analysis and concerns change based on a number of factors, including the type of project, the owner’s vision and local building codes and regulations. Constructability concerns often mirror the priority of the project. Concerns about projects with tight timelines or budgets are more likely to be resolved quickly and more conservatively.
There are a few principles that usually help identify, assess and improve constructability on all projects.
Principles | What it means | What it could look like |
---|---|---|
Integration of construction knowledge | Bringing construction expertise into the design process can help streamline the build and minimize changes and rework later on. | A GC might identify that the weight of the equipment needed to install steel on an industrial project will exceed the weight limit of the space and pose a significant threat. |
Early involvement | Assessing for constructability as early as possible leaves time for changes to be made without causing delays. | Identifying early on that egress windows can be installed, but they shouldn’t because they don't meet local requirements allows time to find alternatives and update drawings. |
Collaboration | Stakeholders should work to communicate and work together to achieve the best possible outcomes by embracing and engaging with each other’s expertise. | A GC and designer work together to figure out how to install an elaborate, bespoke bar in a downtown restaurant that’s too small for large pieces of the bar to be brought in. |
Safety | Pursue methods that increase the simplicity of the build and ensure the design can be executed safely and effectively. | A design team may decide on a wide, open floor plan in a dense construction area minimizing the number of structural columns needed. |
Standardization | Find ways to standardize elements and processes to increase efficiency and minimize the risk of unexpected issues. | Hospital construction likely has less constructability issues die to certain elements, such as electrical outlets, medical gas connections and door specifications, are standardized and installed repeated throughout the facility. |
Resource availability and suitability | Materials and equipment should be available and have the ideal specifications for the space they will be used. | GCs might use value engineering to find an alternative flooring that is slightly more expensive than the original selection but can be procured in much less time. |
Access | Access points are in place to ensure workers, vehicles, equipment, and deliveries can enter and exit the correct work areas. | A GC works to determine the best way to pour all concrete needed for an underground parking garage on a site with limited access for trucks. |
External variables | Assess and adjust for variables that can cause delays or issues, such as an area’s building requirements, weather or geotechnical characteristics. | Oil and gas companies building plants in Texas and Florida might use similar plans, but should adjust for each area’s respective soil, water and available labor. |
Risk management | Worksites should be safe and secure. | A GC might push for more safety equipment to prepare for the installation of large glass windows on the top floors of a skyscraper. |
Environmental impact | Assess the potential environmental impact during the build process. | Decide whether a potential new road that may cause significant erosion and potentially permanent damage to the area should be built. |
Technology | New techniques and technology can improve the design process and identify problems that might arise during construction. | Building Information Modeling (BIM) would provide a 3D model of an addition to a hospital to help resolve potential issues that would slow the project or cause potential safety concerns for the rest of the facility. |
The Constructability Review
Many projects will have formal constructability reviews, which are times when key stakeholders sit down together to evaluate design plans to ensure they can be built safely, effectively and efficiently. These reviews often happen during the design phase and include architects and engineers sharing their designs with the construction team for feedback. The reviews can take place over multiple days and are often led by someone with a deep knowledge of the project, such as an engineering manager or a construction manager (CM) representing the owner.
Constructability reviews can sometimes feel like they add time to the design phase, but the idea is that they ultimately make the engineering and construction phases smoother and shorter because they bring those teams’ expertises into the process sooner.
The review should take place when the design is complete enough that the construction team isn't commenting on elements that are likely to change, but early enough that the design team is able to implement feedback and find alternatives without delaying the project. Many teams will aim for a time when the design is between 40 to 60% complete. Reviews that take place too late in the process are often minimally helpful, too costly to fix, and force the construction team to overlook potential operational or methodical problems that would require too much time to address.
Stakeholders review every detail of the designs and begin planning the construction process, from the first day to closeout. The construction team assesses the plans to ensure they are feasible while also using their expertise to find areas for improvement. The design team should work to understand any issues or questions and push for solutions that address concerns while preserving their original vision for the project.
Details that are evaluated can range from the big picture to the minute. For example, a review for a hospital might identify that there isn’t room for the required trucks and cranes and lead to a full reimagining of the worksite. On the other hand, it might also have the contractors suggesting small changes around each room, such as the placement of medical gas hookups that would make them easier to install.
After the meeting, the design team will leave and implement the suggestions into the designs. GCs should leave with a better understanding of the project and are sometimes able to begin important planning processes, such as identifying the critical path. The site manager should leave with a better idea of possible challenges, how to best manage the site, and might be able to begin obtaining necessary permits.
If a formal constructability review has not occurred during preconstruction, constructability meetings or discussions might arise during a submittal or shop drawing review cycle.
The Two Keys To Improving Constructability
There is a lot to consider when assessing constructability, from dimensions, material selection and equipment placement to the weather. But there are two things that almost always make it easier to identify constructability and find adjustments: experience and collaboration.
Contractors and designers are able to better identify and address constructability concerns with experience. For contractors, this happens with repeated time spent in the field, learning what parts of a plan are likely to succeed and common mistakes that occur. Designers often have to make a more concerted effort to gain this experience. In some areas, such as heavy industrial, newer members of the design team will be assigned parts of a project to oversee in order to gain experience of what it’s like to work with and interpret drawings.
Constructability reviews and analysis brings the expertise of the stakeholders of a project together with the aim of improving the outcome. Creating deliberate space for the design team to understand how their ideas will be executed and for the construction team to understand the intention behind what they’re building creates a better final product.
Was this article helpful?
Thank you for your submission.
100%
0%
You voted that this article was . Was this a mistake? If so, change your vote here.
Scroll less, learn more about construction.
Subscribe to The Blueprint, Procore’s construction newsletter, to get content from industry experts delivered straight to your inbox.
By clicking this button, you agree to our Privacy Notice and Terms of Service.
Categories:
Tags:
Written by
Makenna Ryan
Makenna Ryan is a Solutions Engineer at Procore. Prior to joining Procore, he spent seven years at McDermott International Inc. as a construction Manager and Senior Equipment Engineer. He also spent three years as a Project Engineer at Subsea7. Makenna received his B.S. in Mechanical Engineering and Technology from Texas Tech University. He is based in the Houston area.
View profileJames Hamilton
71 articles
James Hamilton is a writer based in Brooklyn, New York with experience in television, documentaries, journalism, comedy, and podcasts. His work has been featured on VICE TV and on The Moth. James was a writer and narrator for the show, VICE News Tonight, where he won an Emmy Award and was nominated for a Peabody Award.
View profileReviewed by
Janine Trinidad
21 articles
Janine Trinidad is a Construction Educational professional for Procore Technologies. In previous roles, Janine managed all phases of construction on hotel, mixed-use, and institutional projects in the San Francisco Bay area. She was responsible for negotiating contract budgets and change orders, managing RFIs and submittals, and overseeing quality control, among other duties. She is also a certified transformational coach with a focus on women-centered and trauma-informed methods. She is passionate about transforming the construction industry to be a healthier, more successful and welcoming place to work and believes technology and education are allies in doing so.
View profileExplore more helpful resources

A Fine Line: Balancing Standardized Construction Processes With Specific Project Needs
When it comes to the construction process, some general contractor (GC) firms formally adopt a mentality of continuous improvement. But even among those that don’t, construction teams know that getting...
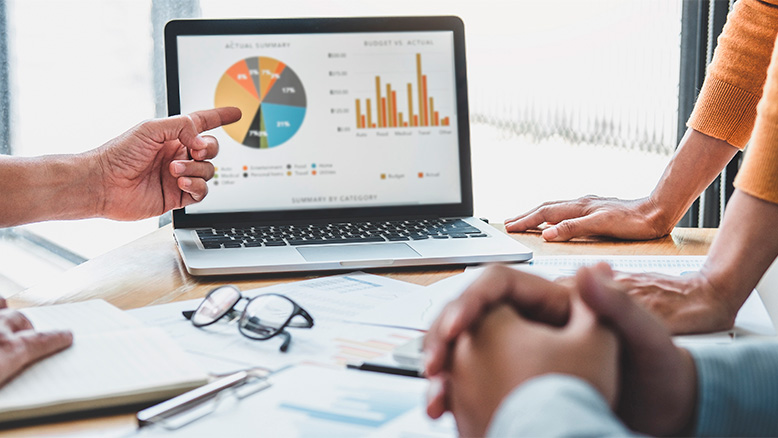
Construction Forecasting Beyond Financials: The Owner’s Guide
Just because a project is large in size, scope or social importance does not mean it will have infinite flexibility and budget. Projects can’t just change their offered service or...
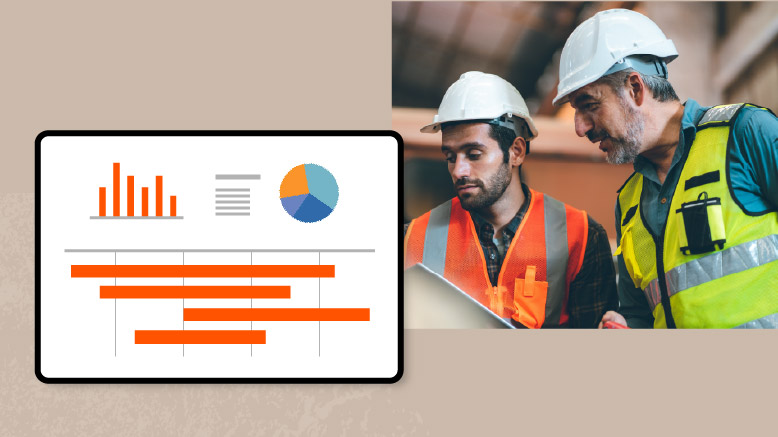
Using Data to Track Subcontractors’ Progress: 5 Keys to Success
Data gives general contractors powerful insights into the progress that subcontractors are — or aren’t —making toward project deadlines. However, the best data isn’t simply there for the taking. Optimizing...

How BIM Software Supports Construction Teams in the Field
Gaps between project design and field execution can cost a lot of money. Architects can create beautiful designs, but if the foreperson and trade crews don’t have access to the...
Free Tools
Calculators
Use our calculators to estimate the cost of construction materials for your next project.
Templates
Find a template to help you with your construction project tasks.
Material Price Tracker
Get the latest U.S. retail prices and view historical trends for common building materials.
Glossary
Explore key terms and phrases used in the industry.