— 15 min read
Mitigating Cost Overruns in Construction
Last Updated Aug 13, 2024
Last Updated Aug 13, 2024

In construction, a cost overrun is when the amount spent exceeds the intended or budgeted amount. This is not just a minor hiccup in financial planning — it can reshape the entire project. Unfortunately, cost overruns in the construction industry are quite common, affecting projects of all sizes and scopes. From minor tenant improvements to complex multi-phase developments, surpassing the budget has almost become an expected part of the construction narrative.
The reasons for overruns are as varied as the projects themselves, encompassing everything from unforeseen environmental conditions and material cost fluctuations to design changes and project management oversights. However, their impacts are wide-reaching. They not only strain financial resources but also affect the quality and execution of the project. Such impacts may result in legal disputes, delayed project completion, and in some cases, complete abandonment of the project.
Understanding the nuances of cost overruns is crucial for all stakeholders involved in the construction industry, as it sheds light on the importance of meticulous planning, risk management, and adaptive project processes.
In this article, we explore the impacts of cost overruns, as well as common causes and effective strategies to prevent them.
Table of contents
The Impacts of Cost Overruns
The repercussions of cost overruns extend well beyond simple budget discrepancies. They create a complex network of consequences that impact not only the financial stability of stakeholders but also influence the punctual completion, overall quality, safety standards, and legal aspects of construction projects.
Project Delays and Disruptions
Cost overruns often lead to significant delays and disruptions in construction projects, prolonging the project timeline and escalating indirect costs such as labor and operational expenses. This chain reaction of cost overruns on project schedules triggers a cascade of disruptions and additional impacts throughout the construction process.Extended timelines — or projects falling behind schedule — are a direct outcome of cost overruns. The need for additional funding and the time it takes to secure these funds can slow or halt project progress.
Also, delays often arise from needing to reevaluate and revise project scopes to fit budget constraints.
These setbacks not only affect resource allocation but can disrupt planned workflows and strain relationships with clients and other project parties. Furthermore, these delays can cause compounding effects on the supply chain and subcontracting, complicating inventory management and scheduling.
Ultimately, cost overruns have a profound impact on every facet of a project, emphasizing the importance of strict budget control and effective execution strategies to ensure project success.
Compromised Project Quality and Safety
Cost overruns can also lead to compromises in project quality and safety. To stay within the revised budget, cheaper materials or less skilled labor might be used, which can negatively affect the durability and functionality of the finished structure.
Safety standards are also often jeopardized when budgets become tight. Essential safety measures, such as adequate scaffolding, proper site maintenance, or the use of quality safety equipment, might be neglected to cut costs or expedite the schedule, increasing the risk of accidents and injuries onsite.
Cost overruns can lead to insufficient testing and quality assurance during the construction phase. This lack of thorough testing can result in undetected defects, posing risks to future occupants and users of the building.
Furthermore, when cost overruns lead to compromises in quality, the long-term consequences include increased maintenance and repair expenses. Projects built with lower-quality materials or subpar workmanship are likely to require more frequent repairs, adding to the overall cost of the project in the long run.
Stay updated on what’s happening in construction.
Subscribe to Blueprint, Procore’s free construction newsletter, to get content from industry experts delivered straight to your inbox.
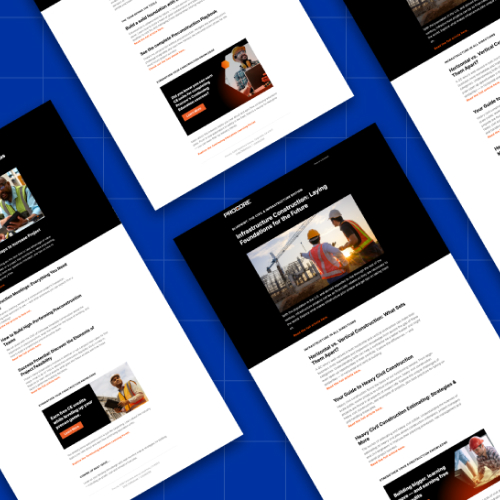
Legal Implications and Brand Impact
If cost overruns result in lower-quality construction, the project may fail to meet regulatory standards and compliance requirements, potentially leading to legal challenges, fines, and the need for costly modifications post-construction. This not only has legal ramifications but also could severely tarnish a company's reputation, particularly among clients. Failure to adhere to the budget can erode trust and credibility, significantly hindering the company's ability to secure future work.
Furthermore, a track record of cost overruns can raise red flags for lenders and investors, making financing future projects more difficult. Lenders and investors are likely to be more cautious, leading to higher borrowing costs or difficulty in obtaining funds. Overall, the legal and reputational fallout from cost overruns can put businesses at a competitive disadvantage. It can affect their ability to bid for new projects, negotiate favorable terms, or maintain a strong position in the market.
9 Common Causes of Cost Overruns in Construction and How to Prevent Them
1. Inaccurate Cost Estimates
Accurate cost estimates are crucial as they lay the groundwork for establishing a project's budget and understanding its financial landscape. Cost overruns frequently arise when these initial estimates fail to capture the true financial requirements of the project, leading to significant budgetary discrepancies.
Often, this occurs for a variety of reasons. For example, if the data on which these estimates are based is incomplete or outdated, it can lead to miscalculations. Additionally, there can be a tendency towards overly optimistic assumptions regarding costs, disregarding the real-world complexities and unpredictability of construction projects. Furthermore, initial estimates often fail to adequately consider potential risks and uncertainties, such as unexpected increases in material costs or labor shortages. These omissions and inaccuracies in the initial budgeting phase set the stage for financial discrepancies as the project progresses, culminating in significant cost overruns that can derail the entire project's financial feasibility.
To prevent inaccurate cost estimates that result in cost overruns, employ detailed earned value analysis, leverage historical data for informed decision-making and conduct thorough risk assessments with contingency planning. Utilizing advanced estimation software can also enhance accuracy by providing detailed and dynamic cost predictions.
2. Differing Site Conditions
Differing site conditions — or discrepancies between the project plans and the actual conditions encountered onsite — frequently lead to additional expenses and are a common cause of cost overruns in construction.
These unexpected site conditions can include a variety of issues, such as soil instability, hidden underground structures, archaeological finds more environmental contaminants.
For instance, a construction team might discover that the soil is less stable than anticipated, requiring additional groundwork and reinforcement, which can significantly increase costs. Similarly, encountering buried infrastructure can halt construction, requiring additional surveys and possibly redesigns to accommodate these findings. These surprises not only add additional direct costs but can also lead to delays, further escalating the overall project expense.
Adopting a proactive approach is key in mitigating the effects of unforeseen site conditions.
Firstly, conducting comprehensive site investigations before finalizing the project plan and budget is crucial. This should include detailed geological surveys, soil tests, and environmental assessments to identify potential issues that could arise during construction.
Utilizing advanced technologies such as ground-penetrating radar and 3D mapping can also provide a clearer understanding of what lies beneath the surface. Furthermore, engaging local experts who are familiar with the area's specific characteristics can provide valuable insights.
Incorporating flexibility into the project's design and financial planning is also key. This involves setting aside a specific contingency budget to address unforeseen site conditions and structuring the project design to allow for adaptability, minimizing the financial impact of any necessary changes.
Lastly, transparent and continuous communication with all project stakeholders, including clients, contractors, and local authorities, ensures that everyone is prepared and responsive to potential changes that arise due to unforeseen site conditions.
3. Project Complexity and Technical Challenges
Complex projects often involve intricate designs, sophisticated materials, and advanced construction techniques, which can be challenging to estimate accurately in terms of cost and time. The more complex the project, the greater the likelihood of encountering unforeseen technical challenges that can disrupt the workflow.
For instance, projects that incorporate unique architectural features or require specialized engineering solutions are prone to technical hurdles that may not have been fully anticipated during the planning phase. Additionally, these types of projects typically involve a larger number of stakeholders, including architects, engineers, contractors, and suppliers, each adding layers of coordination and potential for miscommunication. This increased level of coordination can lead to delays and additional costs, especially if changes need to be made during the construction phase.
Project managers must proactively prepare for possible technical challenges, particularly in intricate construction projects. This preparation entails extensive offsite testing of new technologies and materials through mockups and ensuring that all systems are expertly designed and implemented by certified professionals.
4. Changes in Project Scope or Design
Often, clients may request additional features or changes to the design during the construction process. While some changes might seem minor, they can accumulate, leading to significant increases in both costs and time. For example, upgrading materials, altering layouts, or adding new functionalities requires additional labor, materials, and time.
To prevent scope creep, collaborate with all project stakeholders to define the project scope clearly and comprehensively at the beginning. This process should involve outlining detailed specifications, creating blueprints, and setting explicit guidelines on what is included in the scope of work and what isn't. It’s important that all parties involved, especially the client, agree on this defined scope and understand the implications of changes.
This shared understanding is crucial for maintaining project alignment and managing expectations.
To safeguard the interests of all involved, incorporate these details regarding the project scope and potential changes into the contract. This serves as a binding guideline, outlining the procedures and consequences of any scope modifications. It provides a clear reference point for decision-making and helps prevent misunderstandings or disputes that might arise from unplanned changes. By formalizing the scope and change order management process in the contract, both the project team and the client are better equipped to handle scope adjustments in a manner that minimizes the risk of cost overruns and project delays.
5. Force Majeure
Unforeseen events, often classified as "force majeure" incidents, can have significant impacts on construction projects, including cost overruns. These events are typically unexpected and beyond the control of the stakeholders involved, such as natural disasters (earthquakes, hurricanes, floods), war, strikes, or pandemics.
Unforeseen events can lead to significant delays on a project. For example, a natural disaster might damage a construction site or impede access, while a pandemic could lead to labor shortages due to health concerns or travel restrictions. These delays extend the project timeline, increasing labor and operational costs. Furthermore, natural disasters can cause physical damage to the construction site or structure, requiring additional funds for repairs and rebuilding.
These events also often cause serious disruptions to the supply chain which can further increase the cost of materials. If suppliers are unable to fulfill orders due to these events, finding alternative vendors usually comes at a higher price.
To mitigate the financial impact of these unforeseen events, including a force majeure clause in the construction contract is key. This clause should explicitly delineate what scenarios qualify as force majeure, encompassing a broad spectrum of potential unexpected incidents.
It’s crucial to clearly dictate how risks and additional costs arising from the force majeure event are allocated among the parties involved. In scenarios where a force majeure event renders the project's completion unfeasible, the clause must specify the conditions under which the contract can be rightfully terminated. This ensures a comprehensive and fair strategy for managing the impacts of these events and safeguards all parties' interests.
6. Project Delays
Project delays are a frequent and challenging reality in the construction industry, with the majority of projects failing to meet their original schedule. A critical aspect of effective construction project management is understanding not only how delays lead to additional expenditures, and consequently, cost overruns, but how to mitigate them.
Delays occur usually due to weather, regulatory approvals, or supply chain issues and prolong the project duration, leading to increased labor and operational costs. Delays often mean that workers are needed on-site for a longer period than initially planned. This results in additional labor costs, especially if workers are paid on an hourly basis or if overtime is required to realign with the project schedule.
The longer a project is delayed, the more likely it is that the prices of materials will increase due to inflation, changes in supply and demand, or other market factors. Furthermore, storing materials for extended periods can lead to additional storage costs or damage to items, requiring them to be replaced.
In some cases, delays result in contractual penalties, further increasing the project costs. Known as liquidated damages, these are the pre-agreed-upon amounts specified in the contract that the contractor must pay to the client for each day the project extends beyond the agreed-upon deadline. These clauses are frequently encountered in projects with stringent deadlines, including commercial or public infrastructure projects.
Realistic project planning and scheduling are crucial to prevent project delays. This involves creating detailed timelines, allocating resources efficiently, and allowing for buffer time to accommodate minor delays that may arise. Proactively identifying potential risks that could cause delays and developing contingency plans can help to quickly address issues and reduce the impact of delays. Lastly, maintaining clear and regular communication with all project stakeholders, including subcontractors, suppliers and clients, helps to quickly resolve any challenges that occur during construction.
7. Inflation and Market Fluctuations
Inflation is another factor that can increase the costs of construction materials and labor over the course of a project, especially in long-term projects. The prices quoted at the beginning of a project may become outdated as the cost of raw materials, labor wages, and other expenses rise, leading to budget overruns. Market fluctuations also impact the cost and availability of materials and equipment. For example, a sudden increase in demand for specific materials in the market, or supply chain disruptions, result in higher prices or delays in obtaining necessary items.
To safeguard against cost overruns stemming from inflation and market fluctuations, incorporate flexibility within the project budget, typically through a contingency fund, to accommodate potential cost increases. Proactive procurement strategies, such as acquiring materials early in the project or securing price lock agreements with suppliers, are also effective at preventing future price hikes. Monitoring market trends and inflation rates is key to foreseeing economic shifts, which allows for timely adjustments in the project plan and budget. Furthermore, negotiating fixed-price contracts with suppliers and subcontractors serves as a strategic measure to lock in prices, thereby shielding the project from the financial impacts of market and inflation volatility.
8. Regulatory and Legal Challenges
Construction adheres to a wide range of regulations, including building codes, environmental laws, and safety standards. Changes in these regulations during the course of a project can lead to unexpected work, such as redesigns or additional safety measures, thereby increasing costs.
Depending on the project’s location, obtaining the necessary permits and approvals can be a complex and time-consuming process. Permit-related delays can cause project stagnation, leading to prolonged timelines and increased costs, especially if labor and equipment are underutilized.
During the predevelopment phase of a project, it’s important to develop a comprehensive understanding of all relevant regulations and legal requirements, including local zoning laws, building codes, and environmental regulations. Conducting thorough due diligence, including performing environmental assessments, early in the planning stage is crucial to pinpoint potential issues that could delay the project or require additional work.
9. Selecting Subcontractors Based Only on Price
Selecting the right contractor partners is crucial for the financial health of a construction project, and it involves more than just considering the lowest bid. When choosing subcontractors, it's important to prioritize finding the best fit based on their track record, expertise, and reliability. Evaluating their past project experiences, ability to meet deadlines, and quality of work can provide more value in the long run than simply opting for the most cost-effective bid. This approach not only helps in ensuring a high standard of workmanship but also reduces the risk of potential delays and additional costs that might arise from engaging less experienced or less reliable subcontractors.
Selecting the lowest bid without considering these factors can lead to various complications and inefficiencies. Contractors offering substantially lower bids may cut corners by using subpar materials or employing less skilled labor, compromising the project's overall quality and safety. This could potentially result in rework or legal disputes which escalate costs even further.
Learn more: The Importance of Minimizing Construction Rework
The careful selection of subcontractors through a prequalification process involves a balanced consideration of cost, experience, reliability, and the ability to deliver quality results within the project's timeline and budget constraints. By prioritizing these aspects, firms can significantly reduce the risk of cost overruns and ensure the successful completion of their projects.
If a subcontractor is responsible for causing rework or incurring additional costs, the general contractor has the option to issue back charges. These charges are typically levied in scenarios such as delays attributed to the subcontractor, their inability to meet agreed-upon work standards, or when the general contractor must correct errors made by the subcontractor. To compensate for these additional expenses, the general contractor deducts the back charge amount from the payment due to the responsible subcontractor.
It's crucial to clearly outline terms and conditions regarding back charges in the subcontract agreement. This ensures that all parties are aware of the potential financial consequences of non-compliance or poor performance, thereby fostering a mutual understanding of the agreed upon work and reducing the likelihood of disputes.
Stay updated on what’s happening in construction.
Subscribe to Blueprint, Procore’s free construction newsletter, to get content from industry experts delivered straight to your inbox.
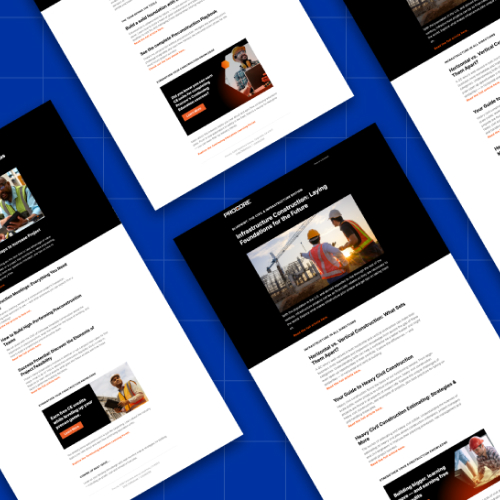
Addressing Cost Overruns in Construction
Effectively managing cost overruns in construction involves not only understanding the root causes, such as scope creep, regulatory changes and market fluctuations — but also implementing robust project management practices and maintaining transparent communication with all project stakeholders.
By proactively addressing these issues through detailed planning, risk assessment, and collaboration, construction firms can significantly reduce the likelihood of overruns and ensure the successful and timely completion of their projects. Ultimately, mastering cost management is key to maintaining financial stability, upholding a strong reputation, and securing long-term success in the construction industry.
Was this article helpful?
Thank you for your submission.
100%
0%
You voted that this article was . Was this a mistake? If so, change your vote here.
Scroll less, learn more about construction.
Subscribe to The Blueprint, Procore’s construction newsletter, to get content from industry experts delivered straight to your inbox.
By clicking this button, you agree to our Privacy Notice and Terms of Service.
Categories:
Tags:
Written by
TJ Forbes
16 articles
TJ Forbes is a Senior Solutions Engineer at Procore, specializing in financials products, analytics, ERP integrations, workflows, reporting and accounting solutions. He previously worked as a financial manager and project accountant for Stiles, a commercial real estate firm in Ft. Lauderdale. TJ holds a Masters in Financial Management from Southern Adventist University.
View profileTaylor Riso
73 articles
Taylor Riso is a marketing professional with more than 10 years of experience in the construction industry. Skilled in content development and marketing strategies, she leverages her diverse experience to help professionals in the built environment. She currently resides in Portland, Oregon.
View profileExplore more helpful resources
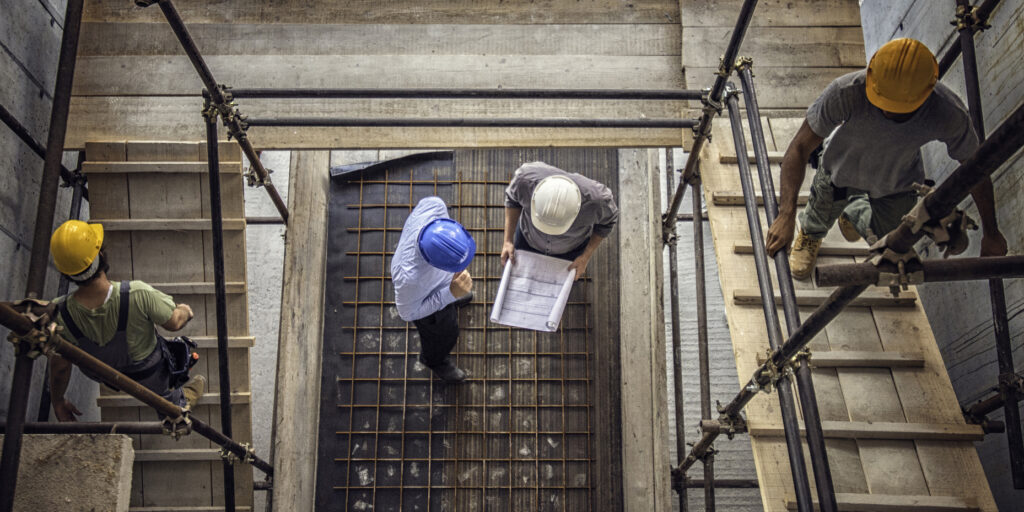
Construction Collaboration: Navigating the Intersection of Project Management and Accounting
Accounting and project teams work together to move the financial aspects of projects through to completion. Data sharing allows for concurrent review to make this possible. Teams need to share...

What are Committed Costs in Construction Accounting?
In construction projects, managing finances can be a challenging task — but understanding committed costs can simplify the process. Committed costs refer to expenses that are guaranteed through formal agreements,...
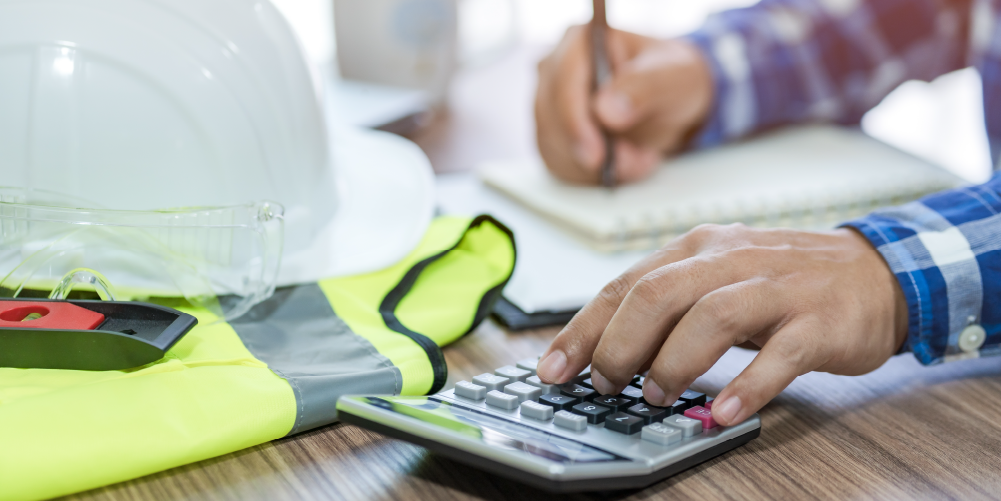
Understanding Construction Financial Statements
For construction firms, effectively managing financial statements is an important building block for success. These documents play a key role in tracking performance, maintaining financial health and securing future projects....
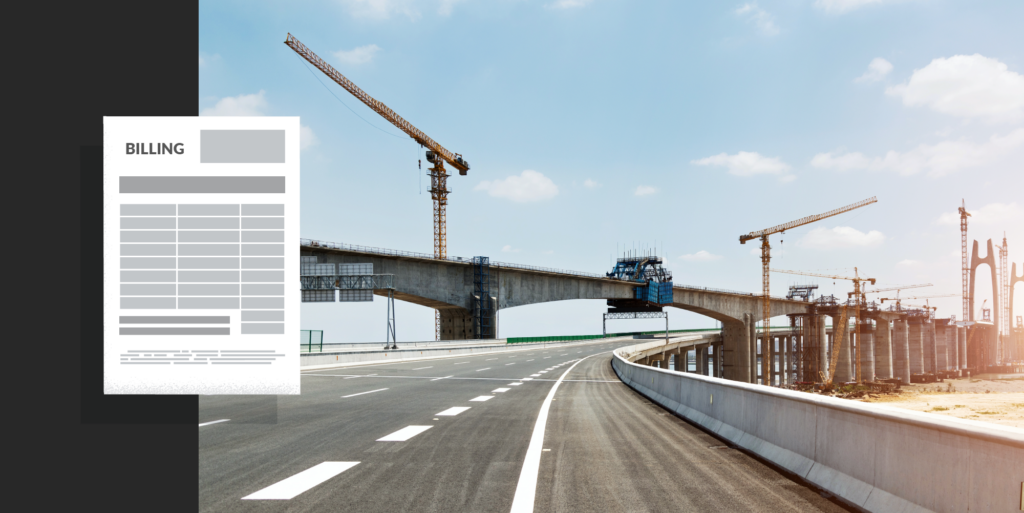
Construction Progress Billing: Keeping the Cash Flowing
Rome wasn’t built in a day, and neither are skyscrapers and bridges. Construction projects take time, and because of that, they require significant upfront costs for labor, materials and equipment....