— 5 min read
Construction Data Automation: The Future of Work
Last Updated Jan 13, 2025
Last Updated Jan 13, 2025
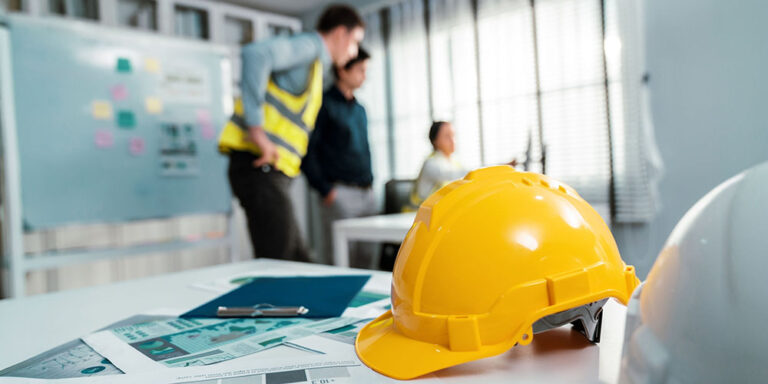
As technology advances, automating tasks in construction is no longer an imaginary concept for the industry.
Construction automation is much more than robotic labor, and even the simplest automated processes can help increase efficiency, reduce errors, and improve overall project management.
In this article, we’ll explore the benefits of the automation of construction data and processes — plus best practices for integrating new technologies effectively.
Table of contents
Automating Administrative Processes
When considering how impactful automation can be for their business, general contractors (GCs) should look at improving their admin teams’ workflows for greater overall efficiency.
Beginning with simple, high-impact tasks on the administrative side can help demonstrate the benefits of automation to employees. Alleviating redundancies of data entry not only makes the lives of employees easier, but assures a higher data integrity and an increase in job efficiency.
At RNGD, we were looking at ways to make our administrative processes more efficient. A lot of time was being spent on mundane tasks like data entry and report generation, which was not only time-consuming but also prone to errors.
So, to start, we automated a monthly safety report which had a lot of data inaccuracies. Now, we can update this data daily, reducing the time taken and potential errors. Automating these reports was a big win, because we showed how quickly and accurately these tasks could be completed, which built a lot of trust in the automation process.
Justin Loehn
Analytics Engineer
RNGD
The Importance of Good Data
Adopting digital tools, including construction management software, allows for real-time updates for projects. Software platforms also help ensure that information shared is accurate and current, enhancing communication between field workers and management by enabling real-time sharing of notes, images, and pins of exact locations on a digital site map, facilitating a quicker resolution of issues. Digital platforms also reduce the risk of losing critical information that could easily be misplaced or damaged on paper.
Real-time data can be analyzed immediately, leading to better decision-making by identifying and addressing problems swiftly.
Data coming from the field should be clear and accurate, allowing for reports to be generated seamlessly from these datasets. This makes it easier to share relevant information both during a project, and once it’s completed.
Capturing and storing good data allows project managers and other leaders to plan more efficiently for future projects. They can analyze which processes work well, from scheduling and sequencing work, to the details of organizing and managing documents, and what strategies need to be tweaked.
Automation in Construction Safety
Another helpful aspect of capturing and integrating data is in building a strong safety culture. Automating safety incident reports and compliance checks, for instance, can be useful safety practices—and can be easily integrated into existing construction software programs. If they’re getting useful data from the worksite, a GC or project management team can ensure that safety standards are consistently met, and that any safety issues are addressed as quickly as possible with the right solution.
Automation can minimize the need for workers to perform high-risk work, like blasting, demolition or even heavy lifting. In this way, embracing automation can have life-saving results, and help minimize the threat of injuries.
Equipment is only as safe as it is managed and handled. Ultimately, it’s the project leadership’s job to assess the safety of new technology, making sure it’s reliable and useful before introducing it widely across crews.
Courses about construction.
For construction.
Unlock your career potential with our free educational courses on Health & Safety, Data in Construction, and more.
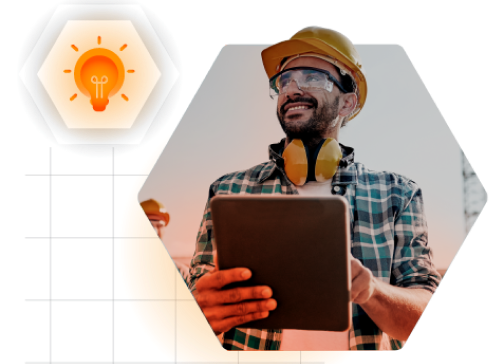
Best Practices for Automating Data in Construction
Adapting to evolving technologies may create challenges for some construction industry leaders, but it also offers an exciting opportunity to be at the forefront of a changing frontier.
Implementing automated technologies can go more smoothly when keeping a few best practices in mind.
Be informed and engage with stakeholders early.
Introducing a new technology should be an informed, rational decision. Selecting the right vendors and technology partners is critical, and research should be done before purchasing any technology. It’s helpful to know what’s on the market—as well as what may be on the market soon.
Another important aspect of automation is that regulation often lags behind technological advancements, so staying updated on the latest requirements is necessary for project success. Project team leads, in particular, should be involved in the decision process for types of automation that will impact the worksite. Engaging them early, and taking the time to explain why the automated process is necessary, can make the transition — and the job — a smoother experience.
Build up slowly.
Consider having dedicated process managers oversee and roll out any automated processes. Train crew members to understand how their tasks translate into data for the management team and how to use any new equipment or software. Define clear objectives and Key Performance Indicators (KPIs) for each automation project.
But there’s no need to reinvent the wheel. Build data systems that are compatible with established platforms and existing software programs, since these programs have been built with onsite reliability in mind.
Allow time for feedback.
Crews are collaborators, and their input on using new technology is as necessary as a GCs or PMs — especially since they’ll be the ones onsite performing the actual labor of construction.
Transparent discussions and regular updates are necessary steps to build trust and acceptance. A vital part of implementing any new change is to communicate expectations clearly and definitively before the change occurs, and being receptive to criticism afterward.
Dedicating time to listen to feedback, whether in regular meetings onsite or via online surveys, can be a useful way to involve all team members in the rollout of automated technology, and is a vital part of fostering a data culture within the organization.
Scaling Your Construction Business with Automation
Automation can play a crucial role in scaling construction businesses by streamlining operations. Successfully integrating automation into construction tasks can lead to increased efficiency, improved safety, and enhanced project management.
Automating scheduling and resource allocation, for instance, can make a significant difference in the amount of time a GC has to perform critical work on or offsite. Automated scheduling processes are improving and may, for example, be able to anticipate weather-related delays, making the entire process more efficient.
By embracing best practices and remaining adaptable, the construction industry can look forward to a future where technology and human expertise work hand in hand.
Was this article helpful?
Thank you for your submission.
0%
0%
You voted that this article was . Was this a mistake? If so, change your vote here.
Scroll less, learn more about construction.
Subscribe to The Blueprint, Procore’s construction newsletter, to get content from industry experts delivered straight to your inbox.
By clicking this button, you agree to our Privacy Notice and Terms of Service.
Categories:
Tags:
Written by
Justin Loehn
Justin Loehn is a dynamic professional with a background in data analytics, data engineering, and process analysis, currently contributing his expertise to RNGD. With over a decade of experience in Business Analytics and Market Research Analytics, Justin brings a wealth of knowledge to his role, having transitioned to the construction industry two years ago. Born and raised in New Orleans, Justin graduated from Brother Martin High School and holds an MBA from Loyola University of New Orleans. His career path has been marked by a commitment to leveraging data-driven insights to revolutionize operational efficiencies and strategic decision-making in a variety of business sectors. At RNGD, Justin applies his fresh perspective and analytical prowess to drive innovation in managerial processes through automation and advanced data techniques. Justin's role is pivotal in transforming how RNGD approaches projects, ensuring that stakeholders benefit from his detailed analytical reports, which enable informed, data-driven decisions. His aspiration is to continue enhancing RNGD's capabilities within the construction sector, pushing the boundaries of what's possible through technology and strategic business solutions. Outside of work, Justin is deeply rooted in the local community, actively engaging in initiatives that contribute to the growth and development of New Orleans. With his blend of analytical acumen and a passion for the construction industry, Justin Loehn embodies the spirit of innovation and progress in his professional journey at RNGD.
View profileTrey Strange
26 articles
Trey Strange is a Peabody and Emmy-Award winning writer and producer based in Brooklyn, NY. Throughout his career, Trey has worked for the Huffington Post, Houston Chronicle, Out Magazine, Brooklyn Eagle, CNBC, INTO, and New York Magazine's Bedford + Bowery. He received his Masters in Journalism and Middle East studies from New York University, and Bachelors in the same subjects from the University of Houston.
View profileExplore more helpful resources
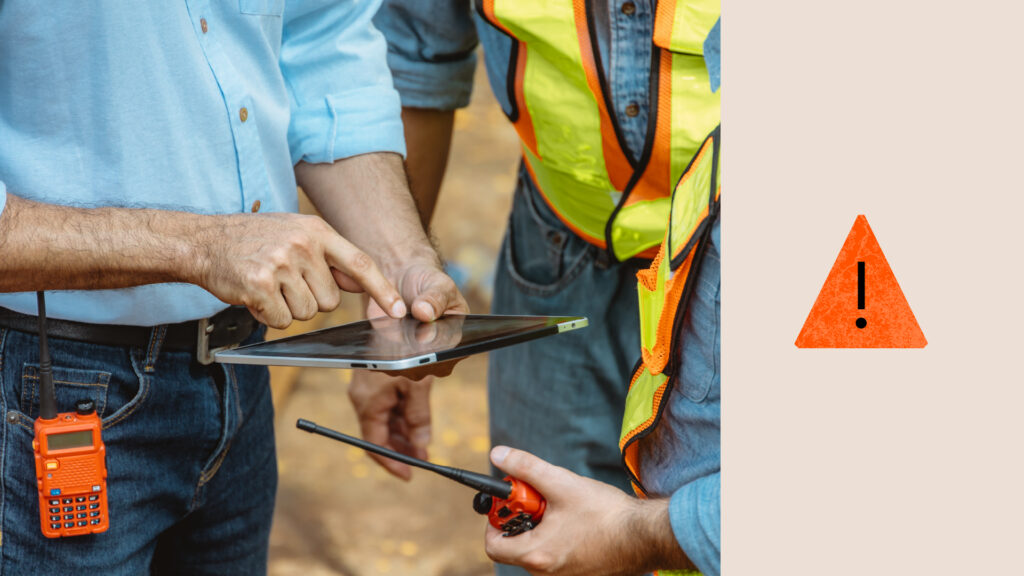
Tackling the Top 10 Construction Industry Issues
The construction industry is constantly evolving, bringing both opportunities and challenges. Companies must navigate an array of construction industry issues — from workforce shortages to integrating new technologies into their...
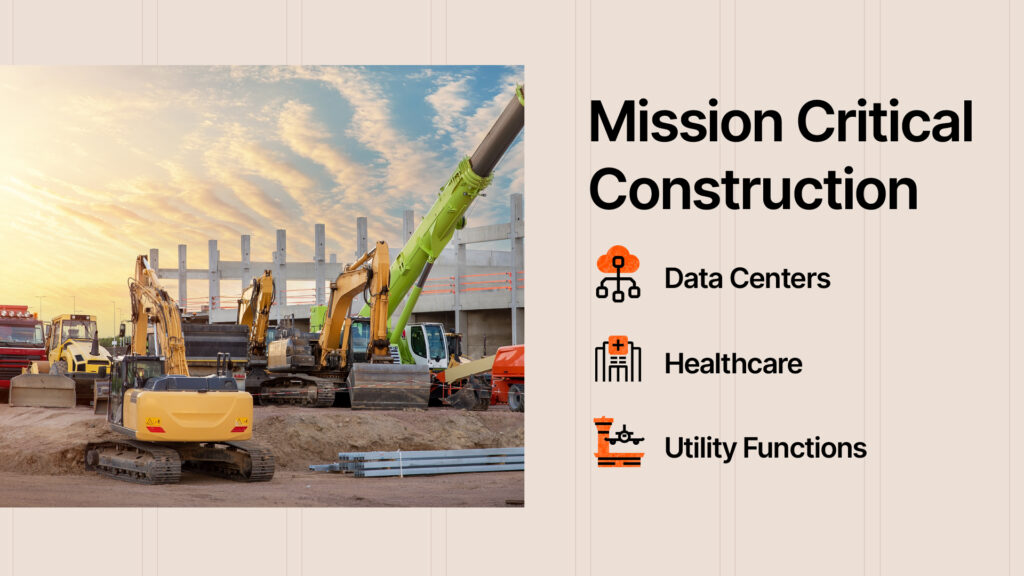
Mission Critical Construction: Strategies for Success
Mission critical construction involves building structures whose functions cannot afford to fail, as any disruptions can lead to significant consequences for society. Keeping data centers, hospitals, power plants and other...
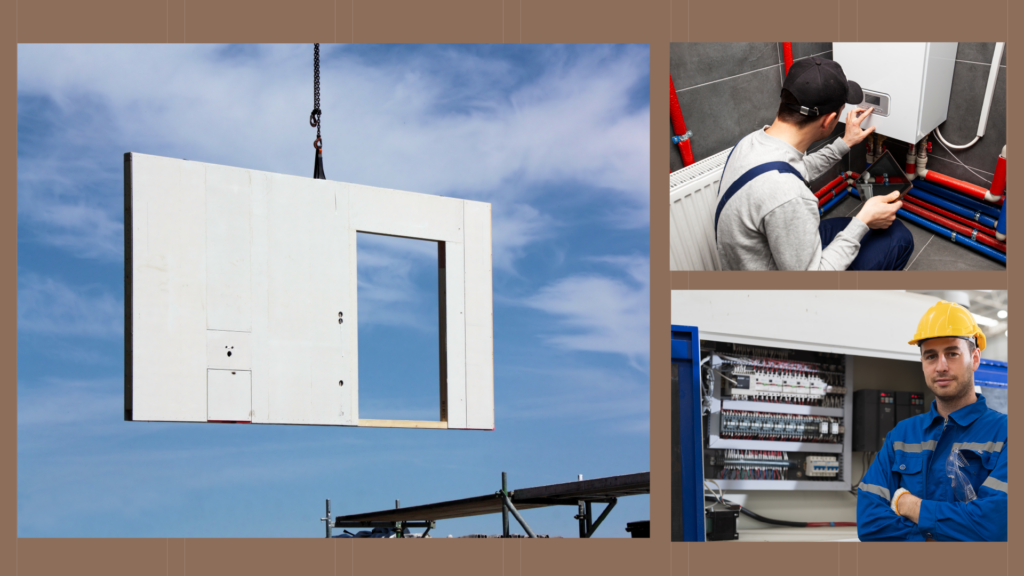
Modular Construction and MEP: A Collaborative Pairing
In an age of supply chain disruptions, workforce shortages, and rising material costs, off-site construction — including modular construction methods and prefabricated materials — is surfacing as a multipurpose solution....
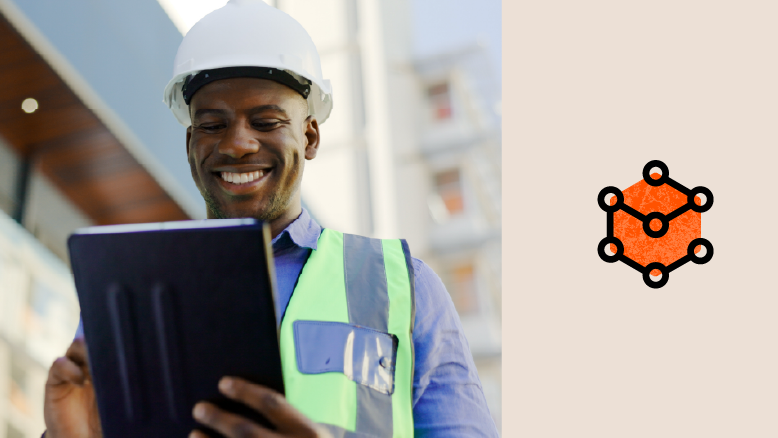
Connected Construction: Transforming the Industry Through Integration
Construction projects are becoming increasingly complex, so companies need to innovate to accurately and profitably complete these modern structures. Connected construction — using technology and data to improve communication, processes...