— 9 min read
Equipped for Success: The Risks and Rewards of Construction Equipment
Last Updated Sep 1, 2024
Last Updated Sep 1, 2024
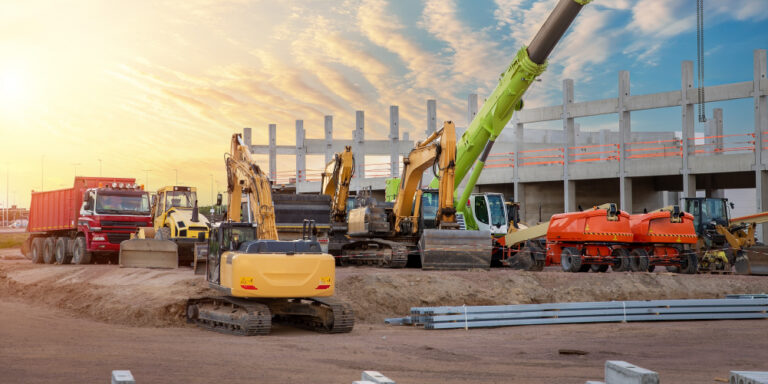
Even before written language, mankind used tools to build. Contractors couldn’t have built the amazing feats seen and used in everyday life without machinery. From handheld tools to multi-story tower cranes, using construction equipment balances safety, efficiency, quality and the many dangers associated with misuse.
This article will discuss the benefits construction equipment brings to the industry, the cost of using new equipment and technologies versus the labor hours it may replace and the risks and rewards of using more construction equipment on the jobsite.
Table of contents
What comprises construction equipment?
Construction equipment makes life easier for construction workers by allowing them to complete tasks more safely using less manual effort, representing significant savings on the overall project. This can include anything from backhoes and cranes to the smaller tools carried around in pockets, like a knife or even a tablet.
Take, for instance, a jobsite that has a single crane. That single piece of equipment saves an incredible amount of labor compared to people manually carrying things around the site. Further, machinery can provide better precision than most people can manage — on tasks like hole digging, GPS-controlled machinery can achieve millimeter precision. On safety forms and during risk assessments, machinery is generally always considered safer than manual labor.
For example, if current processes involve laborers carrying drywall sheets across a construction site, putting those materials on a pallet truck should be considered safer.
The construction industry is currently grappling with a unique intersection between traditional mechanic-only machinery and those equipped with newer technology. Some construction companies are using older, less automated machinery, while others are using high-tech, completely remote-controlled, or unmanned GPS-enabled equipment.
The Cost of Equipment
When considering the cost of equipment, contractors are determining more than just the cash value of a tool. Contractors will have to answer a number of questions revolving around the tool’s cost, the labor costs, and the cost of safety risk.
Is this specific tool necessary for performing the job?
Though utilizing construction equipment is usually a net positive for contractors, before leasing or purchasing equipment, contractors should determine if the tool is necessary for the job site. Even if a piece of equipment could save costs in labor and time on the jobsite, using certain equipment may become more costly than performing it manually.
For instance, if contractors are performing work on a three-story building, it would be faster and safer to haul materials to the third floor using a lift or crane than manually carrying them up a stairwell. But it’s possible that city laws only allow contractors to use that machinery during certain hours, and they may need to schedule it out further than they would like. Contractors would have to weigh the options on using tools versus having their workers manually haul materials.
Will this tool save labor costs?
In most cases, construction equipment will save contractors money and safety risk when compared to their fully burdened labor rate. However, some tools require specific training for use — and this can be costly. Consider a certified crane operator, whose wage is higher than your average laborer. Depending on safety laws, GCs may be required to have a certified crane operator present on a job for all working hours while the crane is on the property — whether or not the crane is in use.
Or, having certain equipment present on a job site may require extensive safety training for every employee who works on the site.
Calculate job labor costs for free with the labor cost calculator.
Should contractors own or rent their equipment?
Whether a contractor chooses to add equipment to their inventory or rent the equipment they use on each project may be a case-by-case decision. Many things must be considered when managing equipment, including whether the maintenance costs of owning a machine outweigh the costs of leasing for a limited duration during a project. In many instances, it's actually cheaper to lease because the leasing company will perform the maintenance on the machine.
In the case of specialty equipment, contractors will often choose to subcontract that package of work to a company that already owns the equipment and is trained in its use.
Leasing the equipment or subcontracting the labor may be easier when it comes to calculating project costs. If the general contractor (GC) has an agreement with a subcontractor to use two bulldozers on the site, that cost is in the bid package, has been budgeted and accounted for. But, if the contractor owns the bulldozer, it's harder to pinpoint the indirect costs incurred in the process.
Planning for the Best Use of Equipment
Whether a contractor owns or leases a machine, there is a lot of pressure to keep that equipment working once it arrives on site — leaving it idle would be a waste of money in either case. That pressure may be more acute when equipment is being leased, so the contractor pays for each day it spends on site.
Best equipment use comes from good coordination right from the beginning of a project. Contractors should be scheduling, pull planning and coordinating with owners about equipment use as soon as possible. If the project schedule shows that the crew needs to dig one hole today and six holes next week, it makes a lot more sense to find a time that works to dig all seven holes in a single day.
This time constraint is another reason large contractors often choose to mitigate risk by subcontracting out a package of work to another contractor who owns machinery. In that case, it doesn't matter to the GC much whether the machine sits idle for several days—the project costs remain the same regardless.
How far ahead does equipment planning go?
Construction schedules are often set well in advance. However, planning times for each piece of equipment depend somewhat on the size of the machine. While it may be possible to rent a mobile tower scaffold within half an hour, a 90-ton piece of machinery will require far more preplanning. Part of this early planning involves arranging for the equipment to be transported to the job site.
When it comes to a large backhoe or a crane, it's not possible to throw it in the back of a truck and drive to the site. It will require specialized transportation, with permits, road closures, and police escorts.
Common Challenges With Construction Equipment
Though the purpose of construction equipment is to make jobs easier, faster and safer, using it on a job can be challenging.
Lack of Access
Having a lack of access to equipment can happen for a few reasons; such as geography, timing, or poor planning.
Projects that require pieces of large machinery will need to plan to ensure the equipment is available when it's needed. If the equipment is booked far in advance, the team may have to change the schedule to fit that equipment causing delay costs, which could cost much more than the rental cost of the equipment.
Safety
There is a lot more to jobsite safety than wearing personal protective equipment (PPE). The biggest challenge with using construction equipment may be getting workers to take the safety risks seriously. Workplace injuries account for 6-9% of project costs, but good health and safety training accounts for just 2.5% of project costs. Workers who've been around equipment for most of their careers can sometimes get complacent, taking the machinery for granted. Unfortunately, that's how some accidents happen.
Regular, ongoing training can help ward off complacency by reminding workers of all ages about the dangers that can exist and to take time to review all of the risks in any given situation carefully.
People often underestimate the severity of accidents that can happen when they use machinery — misuse of these machines can cause far worse injury than just cuts and scrapes. For example, recent safety advances have introduced the concept of having spotters for large machinery. For most machinery in operation, there need to be workers on the ground, walking around the machinery from a good distance away, ensuring that the machinery is not crossing a pedestrian zone or that there are no other workers going to collide with it.
How to Optimize the Use of Construction Equipment
Any cost/benefit analysis of equipment use has to consider the cost of training, maintenance, and proper use.
Implement training.
For construction equipment to be considered safer to use than manual completion of tasks, it needs considerable maintenance and safety training for every person on-site to make them aware of the dangers it poses.
Use the correct tool for the job.
Using the best possible equipment for each job is critical for both productivity and safety. Of course, not all equipment is available all the time, so workers should consider all options to find the best solution.
For instance, if workers need to access a ceiling panel, a mobile elevated work platform (MEWP) might be the best option. If a MEWP won't fit into the workspace, the next best option might be a mobile scaffold.
Instead, workers often resort to whatever might be handy, like standing on a three-foot ladder to try to reach an eight-foot height. They wind up on the top rung of the ladder and work with no safety barriers. If the ladder goes over during a particularly big reach, the person may fall and be injured.
Prioritize safety.
Safety is a company-wide culture that needs to be carefully cultivated at every opportunity. Regular whiteboard meetings are a great opportunity to go over safety protocols and remind workers to check for risks whenever approaching a new situation. Leaders can reinforce safety protocols by celebrating wins and using near-misses as teaching moments.
Good practice is to take five minutes to stand back and take in each new situation. When entering a room, look at what machinery is there, what sprinklers are there, and what electrical work. Heightened awareness can help improve safety with equipment and across the job site.
The Future of Construction Equipment
As the construction industry continues to evolve, so does the machinery that supports it. The future of construction equipment is bright, with technological advancements driving ever-greater efficiency, precision, and safety. With tools like remote-controlled-AI-integrated robot “dogs,” software-enhanced hardware will likely become the norm, reducing manual labor hours and allowing workers to focus on focused skill sets and analytical tasks.
However, the integration of new technologies must be balanced with comprehensive safety training and rigorous maintenance protocols. By investing in education and embracing innovation, the construction industry can foster a safer, more efficient workforce prepared to tackle the challenges of tomorrow. As we look ahead, the combination of advanced machinery and skilled labor promises to elevate the standards of construction, creating safer job sites and more impressive architectural feats.
Was this article helpful?
Thank you for your submission.
0%
0%
You voted that this article was . Was this a mistake? If so, change your vote here.
Scroll less, learn more about construction.
Subscribe to The Blueprint, Procore’s construction newsletter, to get content from industry experts delivered straight to your inbox.
By clicking this button, you agree to our Privacy Notice and Terms of Service.
Categories:
Tags:
Written by
Daniel Kavanagh
15 articles
Daniel Kavanagh is a Senior Strategic Product Consultant at Procore, based in Dublin, Ireland. Daniel is a results-oriented project manager with a passion for building relationships and exceeding client and management expectations, with career experience in project management, systems implementation, technical design and architectural finishes. Daniel has been a member of the construction industry since 2014, and graduated from the Carlow Institute of technology.
View profileKristen Frisa
67 articles
Kristen Frisa is a contributing writer for Procore. She also contributes to a variety of industry publications as a freelance writer focused on finance and construction technology. Kristen holds a Bachelor of Arts in Philosophy and History from Western University, with a post-graduate certificate in journalism from Sheridan College. She lives in Ontario, Canada.
View profileExplore more helpful resources
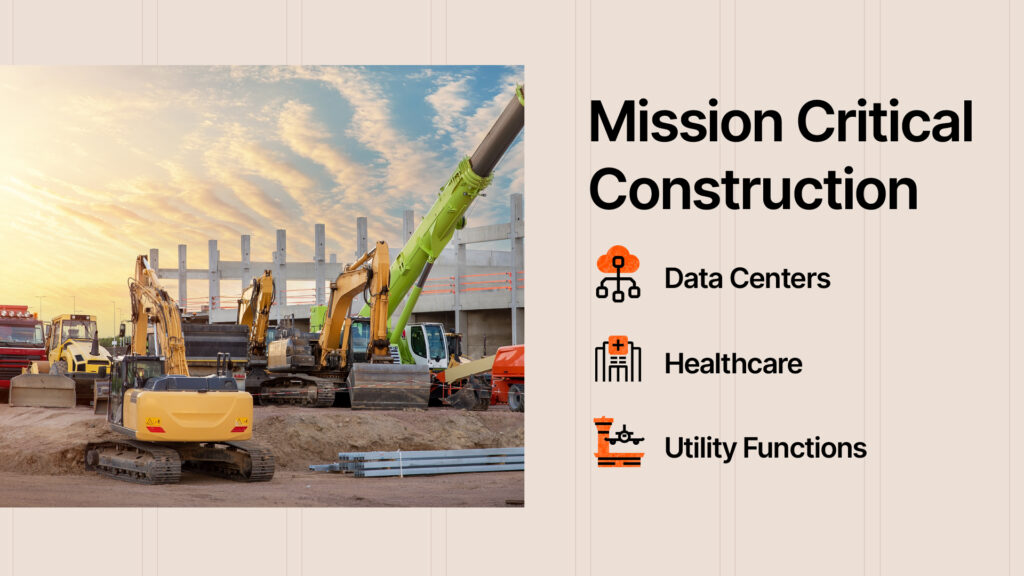
Mission Critical Construction: Strategies for Success
Mission critical construction involves building structures whose functions cannot afford to fail, as any disruptions can lead to significant consequences for society. Keeping data centers, hospitals, power plants and other...
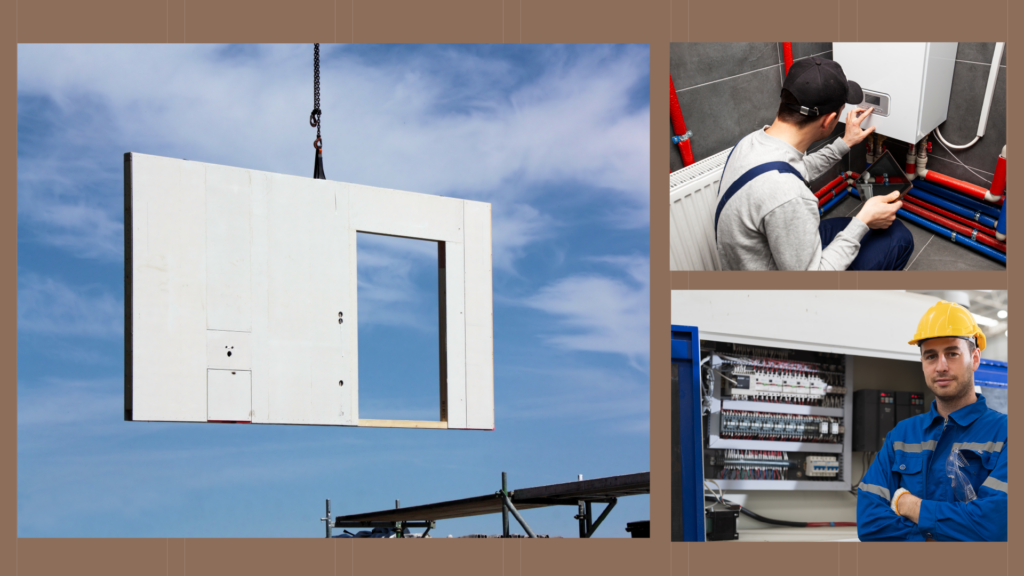
Modular Construction and MEP: A Collaborative Pairing
In an age of supply chain disruptions, workforce shortages, and rising material costs, off-site construction — including modular construction methods and prefabricated materials — is surfacing as a multipurpose solution....
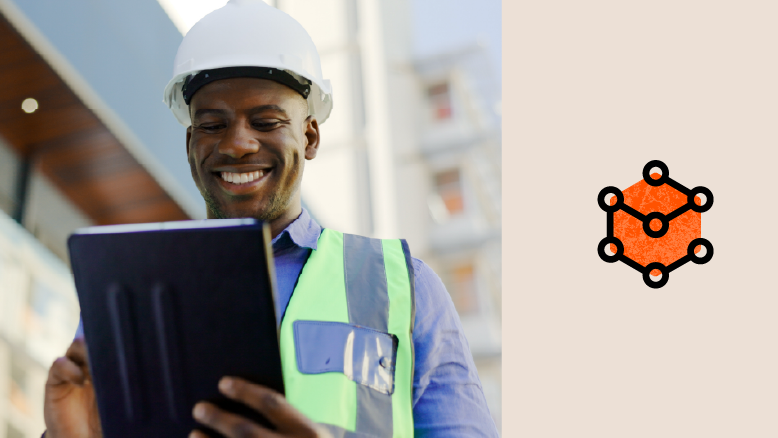
Connected Construction: Transforming the Industry Through Integration
Construction projects are becoming increasingly complex, so companies need to innovate to accurately and profitably complete these modern structures. Connected construction — using technology and data to improve communication, processes...
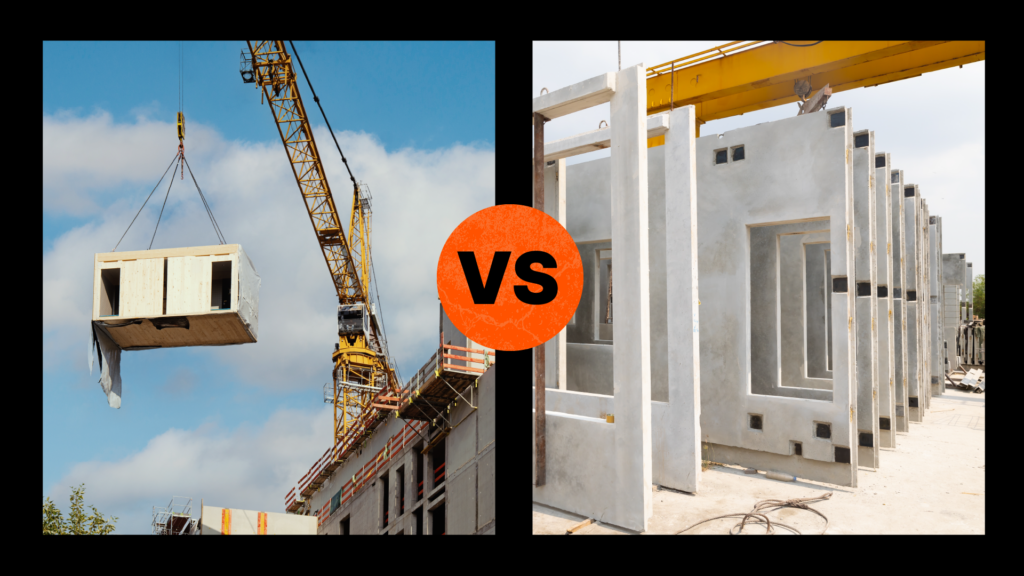
Off-Site Construction: Prefab vs. Modular
As the construction world becomes ever more competitive, deadlines get tighter and the margin for error gets slimmer, project owners around the world are always looking for an edge. Thanks...