— 9 min read
Top 8 Construction Health and Safety Hazards
Last Updated Sep 1, 2024
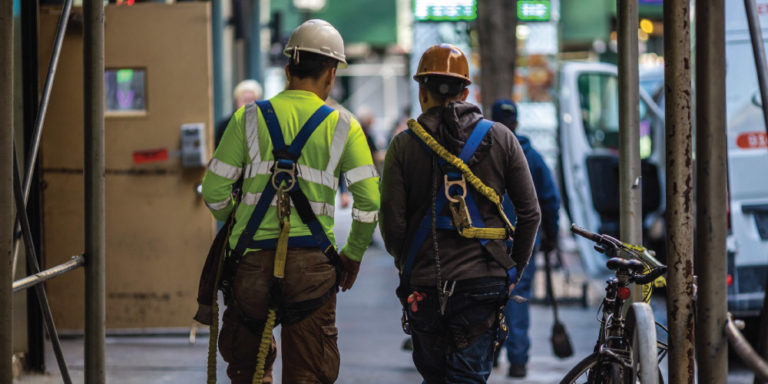
In the construction industry, a lot can go wrong with the progress and completion of the structure itself. By the same token, many potential situations pose risk to the health and safety of your employees and others working on the jobsite. Hazardous conditions can have both short-term and long-term financial consequences along with the possibility of work-related illness or injury.
The Occupational Safety and Health Administration (OSHA) and the American Industrial Hygiene Association (AIHA) have both developed “Focus Four” lists that highlight job hazards that can have long-term negative effects on the health of your employees and your construction business.
Here's an overview of eight of the top safety and health hazards in construction — and preventive measures and resources contractors can use to mitigate these risks.
Table of contents
1. Falls
It's no secret how dangerous — and unfortunately prevalent — falls are. According to data from the Bureau of Labor Statistics, falls accounted for more than 1 in 3 jobsite fatalities as of 2022.
Falls trigger a lot of OSHA safety inspections, and they account for half of the top 10 violations in construction. Many of the accidents stem from oversights that could have been prevented with more vigilance on the job. You must be wary of these hazards and make prevention a part of your formal safety program.
OSHA requires that holes in walking surfaces and skylight areas six feet or higher above a lower level must be protected by covers, guardrails, or fall arrest systems. Guardrail installation also applies to stairs, runways, and ramps situated six feet above a lower level. Establishing and enforcing these guidelines as part of your daily operations can significantly reduce the number of falls on the job.
Contractor resources
- Fall Protection (OSHA): Resources and standards for preventing falls on the jobsite
- Fall Prevention Campaign (OSHA): Educational materials, workplace posters, and training resources
2. Getting caught in or between
Getting caught in a piece of machinery or caught between a piece of heavy equipment and the ground or a wall could result in the loss of life or limb. Clothing or jewelry can get tangled up in an unprotected pulley or conveyor system, while unguarded trenches pose risk for collapse and crushing injuries or suffocation.
To reduce the risk of injury or death, contractors must train employees to be aware of heavy equipment during operation and refrain from wearing loose clothing or apparatuses attached to the body that can get caught up in moving machinery parts. Workers should also stay clear of the radius of operation for devices such as fans, drive belts, or come-alongs, for example.
Contractor Resources
- Caught In or Between Instructor Guide (OSHA): Instructor's manual for conducting safety trainings with staff
- Caught In-Between Hazards Course (OSHAcademy): Short, online course with quizzes for workers
3. Struck-by accidents
Head, neck, or bodily injuries and death most often occur when workers use power tools, walk beneath elevated work areas, and situate themselves near improperly stored building materials. "Struck-by" incidents caused 150 fatalities and 14,000 injuries in 2020. According to OSHA, "75% of struck-by fatalities involve heavy equipment such as trucks or cranes."
Prevention and risk avoidance remain top priorities for your contracting business. Among the top safety measures implemented in your daily operations, you should ensure that all loads being moved are secured, caution employees to steer clear of suspended loads and overhead work, and strictly enforce the use of personal protective equipment (PPE), such as hard helmets and safety glasses.
Contractor resources
- Handouts, Planning Tools & Training (CPWR): PDF guides and audio recordings to train workers to avoid struck-by accidents in a variety of common scenarios
- Struck-By Instructor Guide (OSHA): Instructor's manual for conducting training sessions
4. Electrocution
Powered-up equipment and electrical lines stand out as two principal risks on a jobsite. Inadvertent contact with exposed or hot wires or improper operation of energized machinery hold obvious peril for employees who have not undergone necessary safety training.
According to CPWR, The Center for Construction Education and Training, electrical contractors account for about 32% of electrocution fatalities. The risk is highest for power line installers, who have the highest rate of electrocution death of any occupation.
Go beyond OSHA regulations.
The Procore Safety Qualified program provides construction professionals with everything they need to know to create a culture of safety.
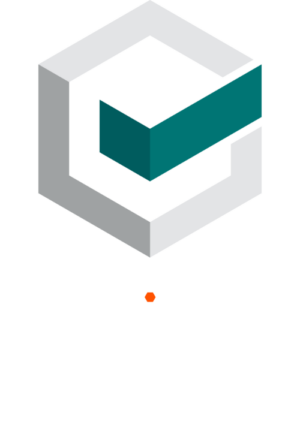
Part of your formal safety program aimed at reducing burns or electrocution must require that workers wear clothing and PPE that includes boots, gloves, long-sleeved garments, and face shields. Keeping a safe distance from power lines and marking areas where powered equipment is in use will also help minimize the risk for electrical accidents. You should also ensure that electrical equipment is adequately powered down and completely shut off.
Contractor resources
- Electrocution Hazards Instructor Guide (OSHA): Training manual for instructors teaching a class on electrocution prevention
- Electrocution Hazards Online Course (OSHAcademy): Short, online educational course
5. Manual material handling
AIHA cautions construction companies that moving building materials and equipment manually can lead to health complications. Pushing, pulling, holding, and carrying construction items often places employees in awkward and unnatural positions that can cause musculoskeletal disorders (MSD).
These injuries often result in missed time or permanent incapacity. Financial distress can result from a lack of skilled labor and possible workers' compensation insurance claims.
Some methods to avoid MSDs involve dropping materials as close as possible to where they’ll be deployed or installed. Heavy loads should be transported by carts, dollies, and lifting tables. Innovative tools that cut down on muscle strain and overexertion should replace less modern items. Analyze work processes to identify how efficiency and proper ergonomics can be optimized.
Contractor resources
- e-Tool for Improving Material Handling (California Department of Industrial Relations): Collection of articles and training materials, including safer methods of handling materials
- Ergonomic Guidelines for Manual Material Handling (CDC): Booklet to help workers identify high-risk work tasks and choose effective options for reducing physical demands
6. Noise
It's no secret that construction jobsites are noisy. But that noise can be more than a simple annoyance: High levels of noise exposure can cause permanent hearing loss. The impairment occurs gradually without an employee recognizing that damage is occurring. While other injuries can often be corrected, hearing loss is neither reversible nor curable. Thus, prevention becomes a key concern for your construction employees.
Employees may be unaware of unsafe noise levels, so continual detection helps reduce the chance of hearing loss. According to OSHA Standard 1910.95, the permissible noise exposure limit for an 8-hour shift is 90 dbA (A-weighted decibels) -- similar to the noise level of a leaf blower or a music concert. (A 2000 report from the Workers Compensation Board of British Columbia found that nearly all construction equipment operates at or above 90 db.) If employees are exposed to noise above established limits, employers must provide personal protective equipment such as adequate ear protection.
If the time-weighted average (i.e., sound levels averaged over the work period) exceeds 85 A-weighted decibels, OSHA requires employers to notify employees, monitor noise levels, and implement a hearing conservation program, among other requirements.
Contractor resources
- Sound Level Meter App (NIOSH): iPhone-only app that indicates sound levels [View in App Store]. On Android, Sound Meter is a similar app with a 4.6 rating.)
- Pocket Guide: Protecting Yourself from Noise in Construction (OSHA): A worker's pocket guide to reducing hearing impairment from noise exposure
- Controlling Noise on Construction Sites (LHSFNA): A guide to preventive measures to mitigate noise levels on construction jobsites.
7. Air contaminants
Construction workers are often exposed to fumes, vapors, gases, dust, and other contaminants on the jobsite. These contaminants are inhaled through the mouth and nose, the most common routes of entry. Though less common, swallowing hazardous airborne particles must also be accounted for in safety protocols. According to a CDC survey in 2010, more than half of all construction workers report at least two exposures weekly to such contaminants.
One common contaminant, crystalline silica, is found in masonry and concrete products. Exposure to silica may result in a condition known as Silicosis, which can lead to respiratory disease and even death.
PPE becomes an integral part of how contractors manage the risk of air contamination. Masks and respirators must be used where contaminants come into play. Monitoring constantly changing unsafe levels of contaminants helps drive new safety protocols while adequate ventilation in closed spaces also helps lessen the chance that employee health issues can arise.
Planning for contaminants allows you to provide employees with the appropriate barriers to possible illnesses and injuries.
Contractor resources
- Pocket Guide to Hazardous Chemicals (NIOSH): Smartphone app with database of workplace chemical information including exposure limits, PPE, respirators, and first aid [Download: Apple | Android]
- Improving Workplace Ventilation During Cold Weather (OSHA): One-page guide with recommendations for proper ventilation during winter months.
- Preventing Silicosis and Death in Construction Workers (NIOSH): 11 action steps to protect workers from silica exposure
8. High temperatures
Construction work in hot climates can have severe health implications when overexposure factors into the equation. Heat stroke is one of the most common conditions that you must prevent when working in extreme temperatures.
Dangerously, heat stroke is often difficult to diagnose. Afflicted workers are typically suffering from impaired judgment and have trouble describing their symptoms. Contractors should create a plan for recognizing and treating symptoms work is done in full sun and the heat index rises.
OSHA recommends several steps to reduce heat illness on the jobsite:
- Drink cool water (1 cup every 30 minutes)
- Take rest breaks
- Find shade
- Dress for the heat
- Watch out for each other
- Change masks or face coverings if they get wet or soiled
This is especially important for new employees who haven't acclimatized to working in the heat. OSHA reports that nearly 3 in 4 heat-related fatalities occur during the first week of work. As a result, they recommend the "20% Rule:" On a worker's first day, don't allow them to work more than 20% of their normal shift in the full heat intensity. Increase their work time by no more than 20% each day until they acclimatize to the working conditions.
Contractor resources
- Prevent Heat Illness at Work (OSHA): Jobsite poster with warning signs of heat illness, action steps, and first aid recommendations
- Heat Illness Prevention Homepage (OSHA): Reference page with tips to recognize symptoms of heat-related illness, including guidelines for prevention and first aid
The true cost of health & safety hazards
Besides the obvious humane angle, there are many financial risks that come with health and safety hazards on the job.
Lost days at work can impact the scheduled timeline and projected profitability of a job. Skilled labor will be more difficult to come by if your company has a track record of unhealthy and unsafe business practices. Higher volumes of workers' compensation claims will cause policy premiums to skyrocket, adding yet another unwanted expense to your operations.
And while the timely completion of a project is critical, nothing holds more importance than the safety and well-being of your employees.
Read More: Contractor guide to improving jobsite safety
Was this article helpful?
Thank you for your submission.
100%
0%
You voted that this article was . Was this a mistake? If so, change your vote here.
Scroll less, learn more about construction.
Subscribe to The Blueprint, Procore’s construction newsletter, to get content from industry experts delivered straight to your inbox.
By clicking this button, you agree to our Privacy Notice and Terms of Service.
Categories:
Tags:
Written by
Thomas Tracy
13 articles
Thom is a group benefits consultant with over 25 years of experience as an insurance and financial advisor. He has written for Quickbooks, tED Magazine, Investopedia, the National Bank of Arizona, and others.
View profileExplore more helpful resources
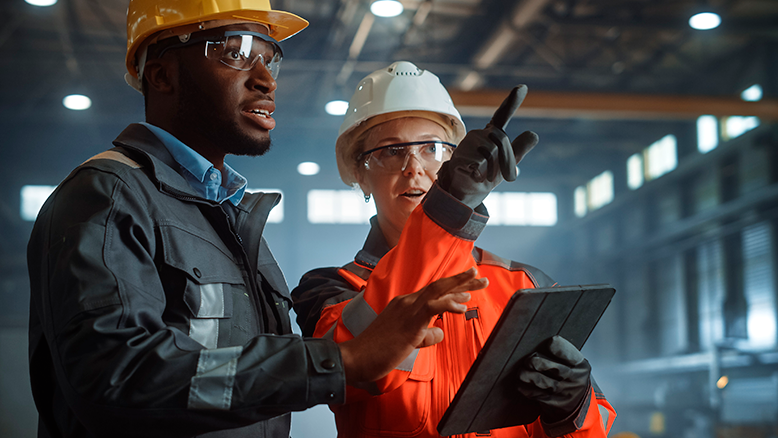
On the Safe Side: Using Data to Boost Subcontractor Safety
Capturing data to mitigate the safety risks incurred by subcontractors as well as in-house workers demands proactive risk management measures, transparent change management and methodical strategy. Applying data to safety...
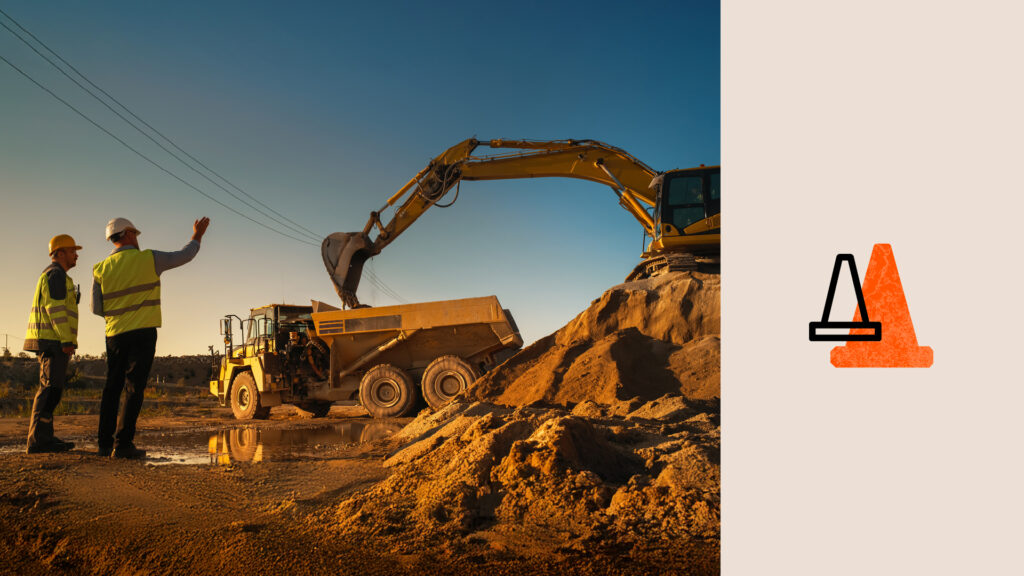
Top Techniques for Heavy Equipment Safety & Operations
Nearly 1 of every 5 workplace fatalities occurs in the construction industry. It is increasingly important to create a culture of safety and reduce the risk of workplace accidents, and...

Preconstruction Partnerships: How Safety Pros Can Collaborate with Estimating & Proposal Teams
Construction leaders and safety professionals are developing a strong understanding of how safety programs positively impact project outcomes. When safety is woven into every aspect of operations from pre-construction to...

The Strategic Partnership Between Construction Safety and HR
A construction safety manager’s role is significant: It entails broad oversight over the construction workplace to prevent incidents that could cause worker injury or property damage. In addition to this...
Free Tools
Calculators
Use our calculators to estimate the cost of construction materials for your next project.
Templates
Find a template to help you with your construction project tasks.
Material Price Tracker
Get the latest U.S. retail prices and view historical trends for common building materials.
Glossary
Explore key terms and phrases used in the industry.