— 7 min read
How a Construction Quality Control Plan Ensures Project Excellence
Last Updated Aug 13, 2024
Last Updated Aug 13, 2024
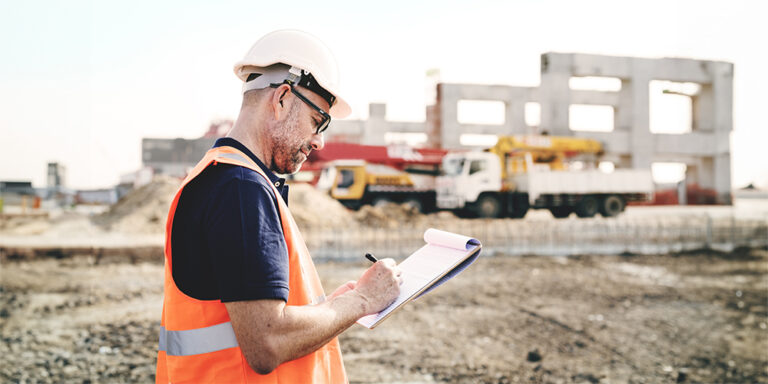
Quality control in construction ensures the safety, functionality, and durability of built projects, protects clients’ and contractors’ reputations and helps avoid costly rework. The quality control plan (QCP) is the document that defines quality objectives clearly, streamlines the construction process, prevents defects, and guarantees the project fulfills the intended design and performance criteria.
Managing the quality of a construction project is connected to every other facet of the process, impacting budget and relationships with owners and subs and requiring integration into the daily work process. QCPs are dynamic documents that can evolve and change as the project progresses, incorporating new insights and needs identified during construction.
Table of contents
Managing Quality Control in Construction
Maintaining quality while staying within budget is a balancing act that impacts most team members in construction. Quality problems can result in costly rework and schedule delays, so the quality control plan aids in risk management.
Developing quality control plans for construction is a collaborative task that requires input from many different stakeholders, including project owners, company officers, project managers, subcontractors and site superintendents, just to name a few.
Because the quality control plan requires a cost-benefit analysis, owners and construction executives often must sign off on the quality control plan. Project managers, superintendents and quality control managers may use the plan to uphold quality assurance and quality control (QA/QC) throughout the project by signing off as specific steps are completed.
Quality standards impact the materials and supplies ordered, the trade subcontractors’ work, scheduled site walks and more detailed inspections. Construction QCPs describe the processes that various team members perform tasks to ensure the end product conforms to specifications.
General contractors often have a company-wide quality control plan and use that as a template to devise project-specific quality control plans for each project. The characteristics of the jobsite, particular quality measurements required in the project specifications, and the knowledge of the construction team can help make QC plans comprehensive and functional to assist in delivering a completed project on time, on budget, and with as few issues needing rework or remediation as possible.
Developing a Construction Quality Control Plan
While a company-wide QC plan is often overseen by an officer like the Chief Operating Officer (COO), project-specific quality control plans are the living systems implemented during the preconstruction and construction process to ensure all elements of the build meet expectations for a specific project.
Collaborate from the start.
The QC plan can be developed concurrently with the other documents during the bidding and preconstruction stages. Because the materials, workmanship standards, and sometimes inspection frequency specified in the RFI will dictate cost estimates, the elements that will go into a project-specific plan are already in play from the start.
When the cross-functional project team is identified, conducting the QC plan discussions early will ensure that all stakeholders have an eye on the final product from the start and that trade partners understand the quality expectations.
Encouraging strong team collaboration early on allows the specialized knowledge of various participants to impact the plan, and all team members will then be on board when it is time to implement the plan during construction.
Establish the QCP team players.
Owners, architects, and designers set the quality expectations for the project in the plans, specifications, and scopes of work. Part of the quality control plan will lay out the responsibilities of each team member. The QCP for a project is often developed by the project manager for the general contractor, or possibly by the quality control manager in a larger construction company.
Early collaboration on plan elements with other stakeholders will ensure that the plan incorporates multiple perspectives to enable it to be smoothly implemented. The GC’s COO and project owners may review the plan to sign off before construction begins.
Role | Responsibilities |
---|---|
COO | Define strategy, establish reporting requirements for quality control and review QCP. |
Construction Manager | Oversee the implementation of the QCP alongside the project manager, construction engineer and site superintendent. |
Site Superintendent | Perform daily job walks and inspections, which will help ensure that potential quality issues are reported and dealt with while they are small to avoid major rework later. |
Foreperson | Assist the superintendent in managing the details of the QCP that affect their work on site. Foremen will communicate requirements to workers so that the quality standards are met. |
Incorporate the plan into SOPs.
Including quality control plans into construction workflow processes enables a checklist approach to each task that can be assigned to responsible parties. The company-wide QCP should align with the general contractor's standard operating procedures (SOPs).
The COO or quality manager who oversees quality control will include lessons from past project data into the overall QCP, and these best practices can then become part of a project-specific QCP.
Many companies employ lean construction principles in their planning, which can be a productive way to develop and execute a quality control plan. Lean construction provides guidance for getting all team members working towards a common goal and adapting the construction process to meet the standards required of the finished product.
Streamlined and organized construction site management will allow site superintendents and foremen to implement the QCP smoothly.
Elements of a Quality Control Plan
Quality control plans bring together the information that stakeholders need for QA/QC, detailing the roles and responsibilities, standards for materials and workmanship, processes to oversee and maintain quality, and documentation to help deliver a completed project that matches specifications.
Plan Overview
A description of the project, the objectives of the QCP and definitions of terms
Matrix of Roles and Responsibilities
Lists of the personnel and responsibilities, the chain of communication, and an organizational chart to define roles in quality control
Quality Standards
Including ISO Standards, specifications from the project documents, workmanship criteria, codes and regulations
Inspections
Details about the personnel, timing, and standards for inspections — including external verifications and assessments necessary to meet the project or government requirements
Logs and Checklists
Daily and weekly logs, including checklists to be included in regular paperwork for the site superintendent, project manager and other quality personnel
Records and Reports
The process for keeping quality records, inspection reports and communication about quality
Communications
Methods and requirements for quality communications and schedule of meetings to oversee and update quality control
Non-Conforming Work
Define the processes to control, identify, document and correct non-conformances
Qualification of Subcontractors and Suppliers
Procedures to verify subcontractors' performance capabilities and suppliers' quality controls
Training
Planning for training workers on quality requirements for workmanship and any outside specialized QA/QC training needed
Resources
Quality control equipment, supplies and outside labs or inspection agencies
Quality Assurance Surveillance
Detail the schedule of quality reviews and audits to maintain adherence to the QCP
Monitoring QCP Effectiveness
Processes to measure the plan’s effectiveness and make adjustments
Project Completion Inspections
Final inspection details for the completed project
QCP Best Practices
When creating a construction quality control plan, gathering all the information pertaining to quality requires focus and organization. Fully understanding the expectations of senior management and clients to define the parameters for productivity, quality and safety that will become part of the plan is crucial.
Be clear.
Focus on writing a clear plan that is straightforward to implement and answers the needs of the personnel who will manage quality. Including as much relevant information as possible from the start is the best practice. However, the QCP can change as problems arise, more clarification is needed, or new solutions are discovered to improve the plan.
Make it accessible.
Project management software can help teams create a quality control plan that is easily accessible for stakeholders to track, update and monitor quality control on projects from anywhere at anytime.
Create a single source of truth.
By providing a central reference source for specifications and plans, storing reports for easy access by stakeholders, and including checklists in processes on-site, software tools help enhance and simplify communications and recordkeeping for quality control plans.
Keeping Quality on Track
Quality control affects every phase of the construction process, and a quality control plan is an essential tool for keeping QA/QC on track. Developing a functional quality control plan involves strong collaboration, communication, and documentation and lays out a pathway to ensure a project’s success.
Quality control plans enhance product quality, reduce waste, ensure compliance with regulations, and increase customer satisfaction.
Was this article helpful?
Thank you for your submission.
75%
25%
You voted that this article was . Was this a mistake? If so, change your vote here.
Scroll less, learn more about construction.
Subscribe to The Blueprint, Procore’s construction newsletter, to get content from industry experts delivered straight to your inbox.
By clicking this button, you agree to our Privacy Notice and Terms of Service.
Categories:
Tags:
Written by
Bianca Holtier Coury
15 articles
Bianca Holtier Coury spent 15+ years in various roles managing construction projects, such as Preconstruction Team Lead, Purchasing Agent, and Project Manager. She has a wealth of experience in all project phases, including managing project schedules and budgets, bid management, and coordinating vendors and subcontractors. Bianca is an Associate Member of AIA and a LEED Green Associate. She currently serves as Director of Partnerships for the Construction Progress Coalition. Bianca holds a BA in Urban Design and Architecture Studies from NYU. She lives in Cleveland, OH.
View profileJulia Tell
44 articles
Julia Tell is a freelance writer covering education, construction, healthcare, and digital transformation. She holds a Ph.D. in Media & Communications and has written for publications including Business Insider, GoodRx, and EdSurge, as well as nonprofits, international businesses, and educational institutions.
View profileExplore more helpful resources

The Strategic Partnership Between Construction Safety and HR
A construction safety manager’s role is significant: It entails broad oversight over the construction workplace to prevent incidents that could cause worker injury or property damage. In addition to this...
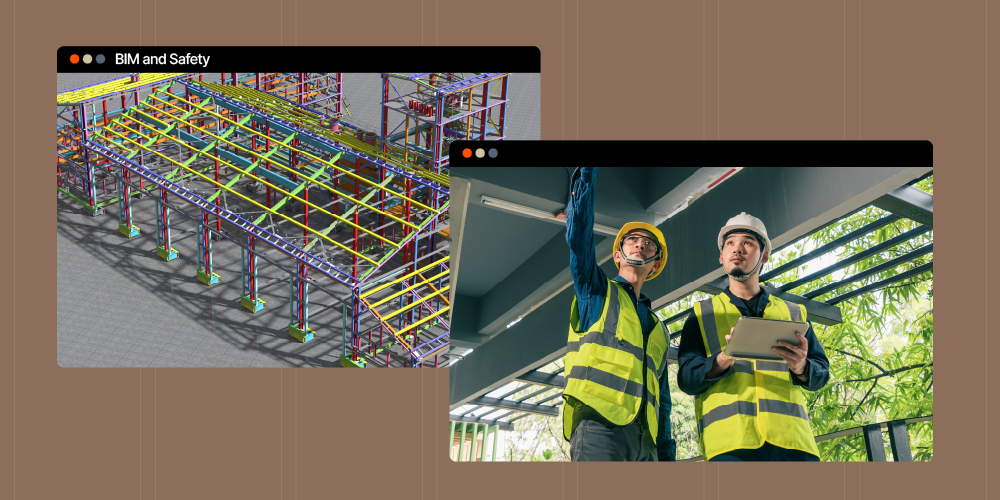
Enhancing Construction Safety with BIM Technologies
The construction industry is no stranger to tools: Even ancient civilizations developed mallets and axes to make their work easier. Today’s latest tools look different, but they can be as instrumental...
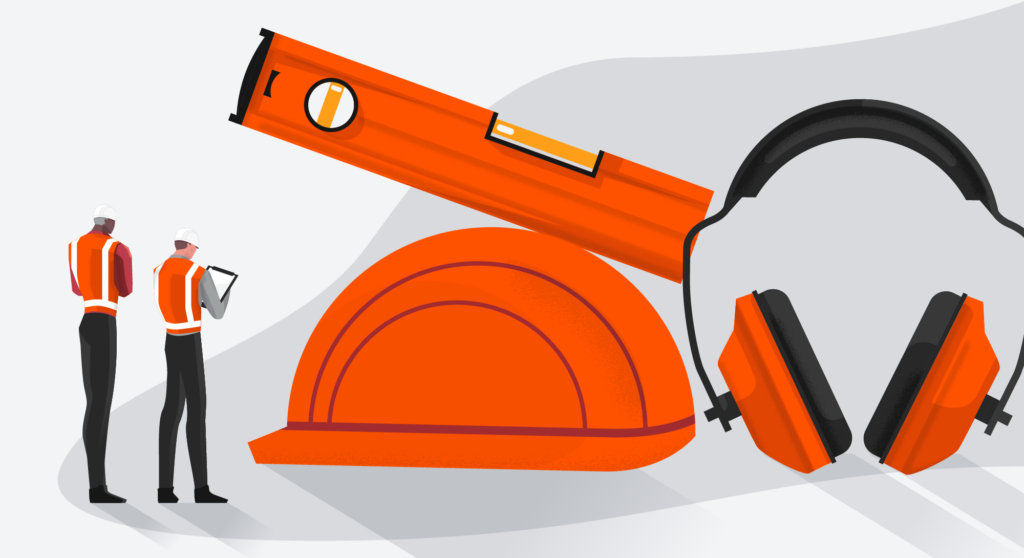
Construction Safety Training – Goals, Benefits & Emerging Trends
Construction safety training (CST) educates workers about the risks they face on construction sites and teaches them how to prevent accidents, injuries and fatalities. The construction industry has the highest...
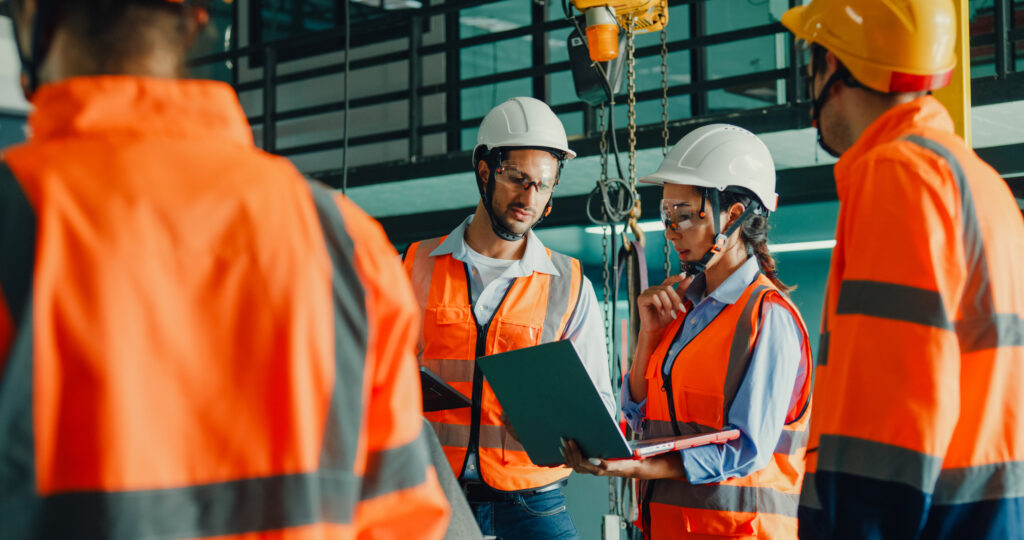
Technology for Construction Safety: Strategies to Supercharge and Scale Safety Practices
The construction industry is no stranger to the arrival of new technology, and builders are realizing its many benefits. Modernization across the industry is helping contractors streamline operations, enhance efficiency,...