— 7 min read
Construction Resource Allocation: Streamlining Projects for Success
Last Updated Mar 20, 2025
Last Updated Mar 20, 2025
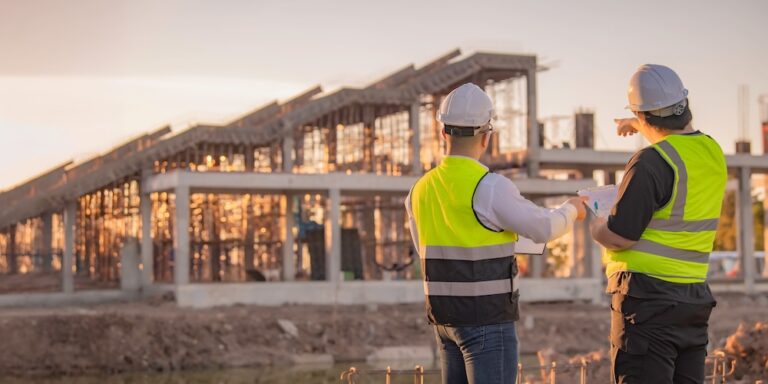
Resource management is fundamental to the success of any construction project. Construction resource allocation refers to the process of resource management that involves the assignment, or allocation, of key construction resources, including materials, workforce and equipment. Without proper allocation and oversight, projects risk delays, inefficiencies and possible financial losses.
This article will discuss how to create a well-structured resource allocation strategy, so all necessary assets are available when needed. It will also look at how efficient resource management can enhance communication among project teams and boost overall project quality.
Table of contents
Benefits & Challenges of Resource Management
Effective resource management boosts construction project success by reducing downtime, improving workflow and ensuring smooth project execution.
Efficient budgeting and cost monitoring help minimize financial overruns, leading to greater profitability. Strategic planning also allows for early risk identification and can help create solutions that mitigate disruptions as much as possible. Having the right resources available at the right time improves project quality, meets stakeholder expectations and drives overall success.
However, managing resources in construction comes with challenges, such as fluctuating material costs, labor shortages and unpredictable project demands. Poor resource allocation can result in wasted materials and equipment downtime and even impact profitability. A well-executed resource management strategy, however, boosts productivity, enhances worker safety, reduces waste and keeps projects on schedule and within budget.
Allocating Labor Resources & Workforce
Effective workforce management is important for sustaining productivity, meeting deadlines and controlling costs. Strategically allocating labor helps project managers and contractors stay within budget and align resources with project demands and key milestones. Success comes down to assigning the right people to the right tasks, thereby creating a more efficient and seamless project workflow.
While hiring permanent staff to self-perform provides reliability, skill consistency and long-term cost savings, they do come with higher fixed costs and long-term commitments. Depending on the job, it may be useful to hire subcontractors. They offer flexibility, specialized expertise and reduced overhead costs. However, there will be more coordination and oversight required.
Finding the right subcontractor for a construction job requires a strategic approach to guarantee quality and efficiency. Start by defining the project scope and required skill sets, then research subcontractors’ credentials, past projects and client reviews.
Recommendations from industry peers, subcontractor directories — including the Procore Network or Dodge Construction — and local trade associations can help identify reliable options. Some subcontractors are part of trade unions, offering benefits like standardized wages and specialized training but often at higher costs.
One key reason to hire subcontractors is to mitigate risk and liability. Subcontractors are specialists in their fields, whereas a general contractor typically oversees rather than performs specialized work.
Ben Ashburn
Staff Trainer & Program Manager
Procore Technologies
Location is also key. Hiring subcontractors near the project site reduces travel time, transportation costs and scheduling conflicts.
Once shortlisted, evaluate bids based on cost, expertise and availability. Verify licensing, certifications and insurance — and conduct interviews to assess communication and reliability. Clear contract terms and open communication create accountability and project success.
Material Resource Allocation
Material resource allocation requires careful planning to make sure the right materials are available at the right time without excessive waste or delays. Project managers must create a procurement strategy that includes accurate quantity estimation, supplier coordination, and just-in-time delivery to prevent stockpiling or shortages.
Factors such as lead times, storage capacity and material expiration must be considered to avoid inefficiencies. Digital inventory management systems can help track material usage and automate reordering processes, improving overall project coordination. Sustainable material management, including recycling and repurposing excess materials, further enhances cost-effectiveness and reduces environmental impact.
Explore data and trends for building materials prices.
Get the latest U.S. retail prices and view historical trends for common building materials.
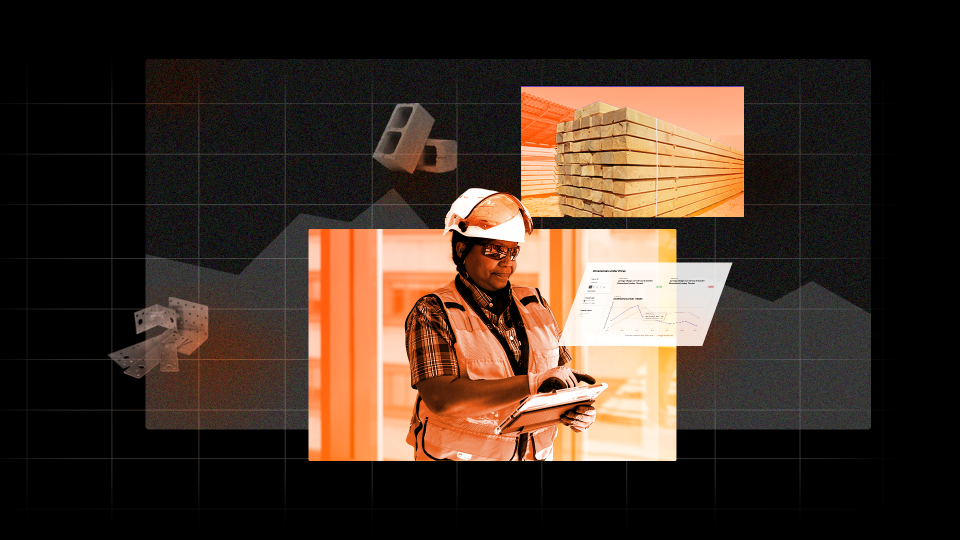
Inventory Management: Tracking Stock Levels and Minimizing Waste
Effective inventory management ensures materials are available when needed while minimizing excess and waste. Utilizing inventory management software allows for real-time stock monitoring, while barcoding or RFID tracking enhances accuracy and efficiency. Establishing clear reorder points helps prevent both shortages and overstocking, so there's always a balanced supply of materials.
To further reduce waste, implement precise planning of material usage. Recycling and repurposing unused materials can help cut costs and reduce environmental impact. Additionally, training workers on proper material handling minimizes damage and unnecessary waste, contributing to a more sustainable approach.
Benefitting From Just-in-Time Delivery
Just-in-time (JIT) material delivery offers several advantages, including lower storage and handling costs, reduced risk of material deterioration or theft and a more organized, clutter-free jobsite.
To implement JIT effectively, close coordination with suppliers is necessary to schedule timely deliveries. Aligning deliveries with project phases prevents unnecessary stockpiling, and having contingency plans in place ensures that any delivery delays do not disrupt workflow.
When combined with intentional collaboration and communication, just-in-time delivery can help project managers and site leadership be more accurate and efficient. And using technology keeps everyone on the same page — so the right materials are installed in the right place at precisely the right time and teams can focus on seamlessly delivering the project.
Daniel Kavanagh
Solution Specialist, Industry Compliance
Procore Technologies
Managing Equipment Resources
Effective equipment allocation is important for maintaining productivity and minimizing downtime in construction projects. Construction managers must balance owned versus rented equipment so the most high-use machinery is readily available on-site, while renting specialized equipment as needed.
Real-time tracking systems — such as GPS and telematics — help monitor equipment utilization and reduce idle time. Proper allocation also includes assigning trained operators to specific machinery. Equipment should be assigned based on qualification level and priority tasks so the equipment operates at the most efficient use possible.
To make sure equipment breakdowns don't cause extended downtime, it's important to schedule regular preventive maintenance and conduct routine inspections. Train operators to identify early signs of wear and tear — and keep spare parts readily available so that when a repair does happen, it can be completed quickly.
How to Create a Resource Management Plan
Effective resource allocation is only possible with a comprehensive resource management plan.
Define project scope.
Outline the project’s objectives, deliverables and specific resource needs as clearly as possible. Understanding the full scope helps in anticipating requirements and potential challenges early on.
Conduct a resource inventory.
Assess the current availability of workforce, materials, equipment and financial resources. Identifying resource gaps creates proactive solutions rather than reactive adjustments.
Develop a resource allocation strategy.
Distribute resources effectively based on project demands, skill requirements and priority levels. This includes assigning personnel to specific tasks, scheduling equipment use and making sure materials arrive when needed.
Create a scheduling plan.
Develop a detailed timeline that outlines when and how resources will be used. This prevents delays and allows for smoother transitions between project phases.
Establish a resource budget.
Allocate financial resources strategically, ensuring cost efficiency while maintaining project quality. A well-defined budget includes contingencies for unexpected expenses and market fluctuations.
Monitor and adjust the plan.
Continuously track resource usage through performance metrics and project management software. Regular assessments allow for adjustments to optimize allocation, address inefficiencies and adapt to project changes.
The Benefits of Hiring a Construction Resource Manager
Larger general contractors will often hire construction resource managers, a dedicated role to strategically manage and allocate resources. This is a specialized professional responsible for planning, allocating and optimizing resources throughout a construction project. Their primary role is to make sure the correct resources are available at the right time — preventing shortages, delays and cost overruns.
Having a resource manager on a project brings several benefits, including improved budget control, better risk management and increased productivity. A dedicated resource manager enhances project efficiency and reduces waste by coordinating workforce schedules, managing supplier relationships and even overseeing equipment maintenance. Their ability to forecast resource needs and adapt the plan to changing project conditions can help lead to smoother and more timely project execution — and higher overall profitability.
Construction Resource Allocation Best Practices
Leverage project management software.
Utilize scheduling, inventory tracking and management tools to streamline operations and enhance visibility across all project phases.
Always keep communicating.
Establish clear communication channels between teams, suppliers and stakeholders to reduce misunderstandings and enhance collaboration.
Stay flexible.
Adapt resource allocation strategies to accommodate unexpected project changes so the project faces minimal disruptions.
Optimize equipment usage.
Schedule equipment strategically and schedule preventative maintenance to maximize usage and reduce breakdowns and downtime.
Enhance workforce management.
Utilize workforce scheduling tools to optimize shift planning, task assignments and labor distribution based on project demands.
Reduce material waste.
Implement sustainable practices such as just-in-time inventory management, recycling and repurposing materials to minimize costs and environmental impact.
Was this article helpful?
Thank you for your submission.
0%
0%
You voted that this article was . Was this a mistake? If so, change your vote here.
Scroll less, learn more about construction.
Subscribe to The Blueprint, Procore’s construction newsletter, to get content from industry experts delivered straight to your inbox.
By clicking this button, you agree to our Privacy Notice and Terms of Service.
Categories:
Tags:
Written by
Caitlin Sweeney
Caitlin Sweeney is a freelance writer specializing in construction, design, and travel. Her writing has been featured in Building Design + Construction, The American Institute of Architects, ArchDaily, and AIA Contract Documents. Caitlin holds degrees in Public Relations and Psychology from Virginia Tech. In her spare time, she writes fiction, practices French and Russian, and travels as often as she can around the world. She lives in Virginia with her two pets, Pippin and Merry.
View profileReviewed by
Ben Ashburn
20 articles
Ben Ashburn is a Senior Construction Education Trainer at Procore. After a successful career as a construction estimator — working his way up from estimating manager to senior estimator — Ben has spent the most recent part of his career in construction sharing his skills with other as a construction educator. Ben has an extensive background in construction education: He has been an assistant professor in the Department of Construction Science at Texas A&M, and lectured about estimating, scheduling, management, and other related construction topics at Murray State University. He has been a construction training and learning development partner with Procore since 2019.
View profileExplore more helpful resources
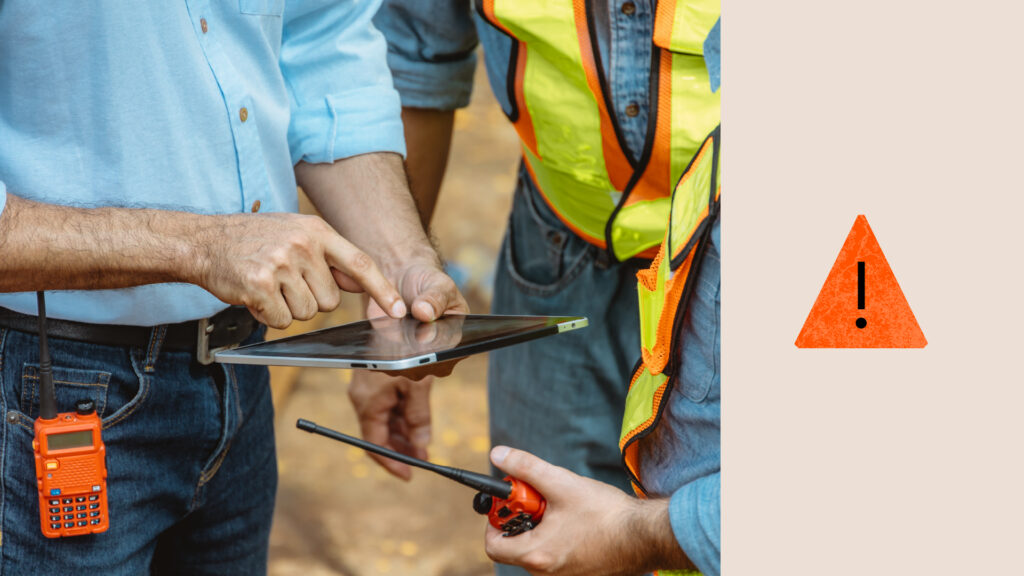
Tackling the Top 10 Construction Industry Issues
The construction industry is constantly evolving, bringing both opportunities and challenges. Companies must navigate an array of construction industry issues — from workforce shortages to integrating new technologies into their...
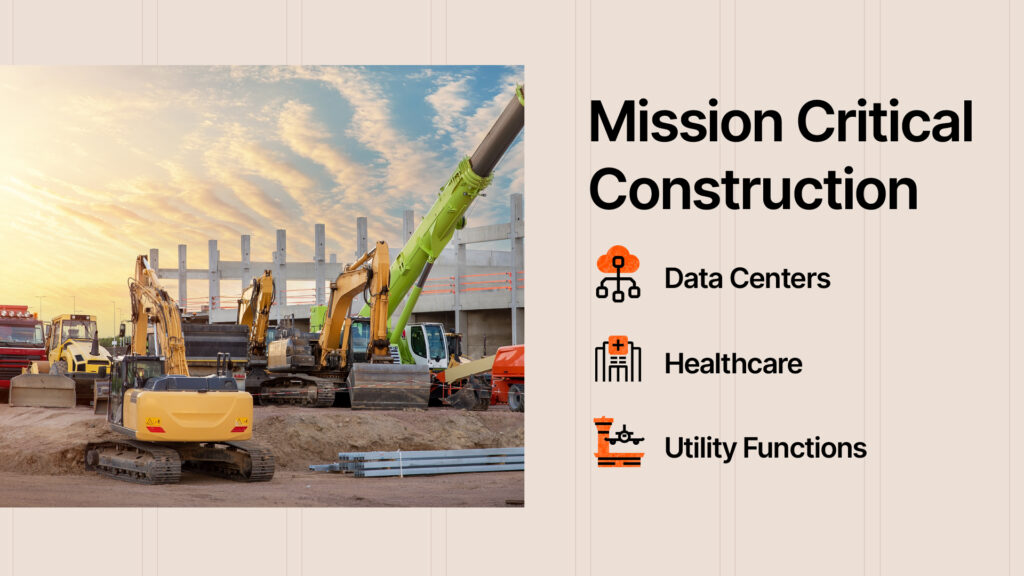
Mission Critical Construction: Strategies for Success
Mission critical construction involves building structures whose functions cannot afford to fail, as any disruptions can lead to significant consequences for society. Keeping data centers, hospitals, power plants and other...
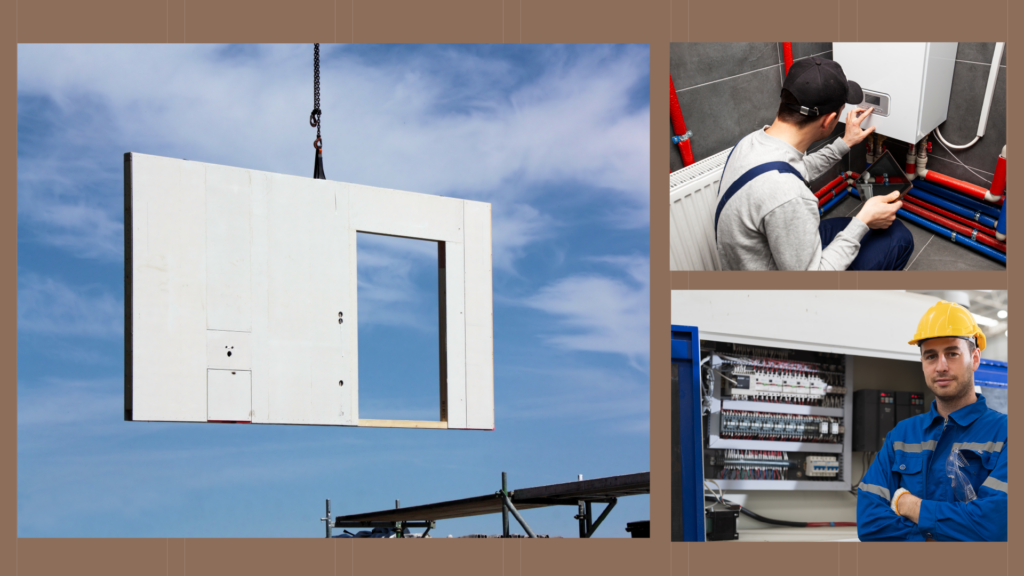
Modular Construction and MEP: A Collaborative Pairing
In an age of supply chain disruptions, workforce shortages, and rising material costs, off-site construction — including modular construction methods and prefabricated materials — is surfacing as a multipurpose solution....
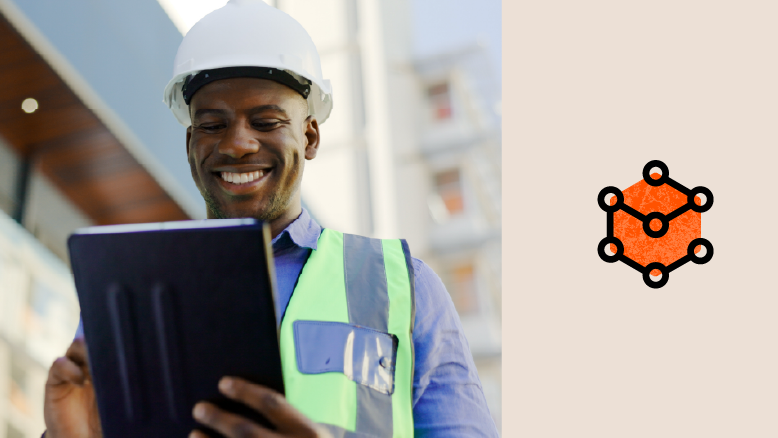
Connected Construction: Transforming the Industry Through Integration
Construction projects are becoming increasingly complex, so companies need to innovate to accurately and profitably complete these modern structures. Connected construction — using technology and data to improve communication, processes...