— 11 min read
Mastering Construction Resource Management: Strategies for Success
Last Updated Mar 20, 2025
Last Updated Mar 20, 2025
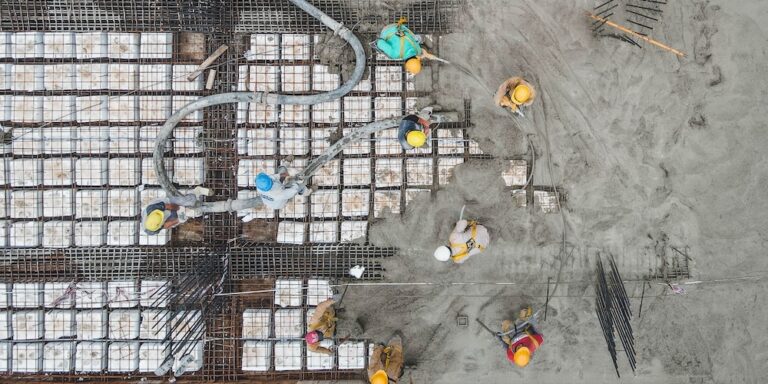
Completing construction projects successfully requires the careful management of various resources: labor, materials, equipment, money, time and information. Since these resources are finite, allocating them wisely is crucial for minimizing waste and maximizing profits. Construction resource management is the process of strategically planning and deploying resources to deliver high-quality projects on time and within budget.
This article explores the advantages of effective resource management, emphasizes the centrality of workforce planning, discusses the challenges of resource management on construction sites and offers practical tips for optimizing resource use.
Table of contents
Types of Resources
Construction resource management involves properly assigning resources to be used most effectively to complete projects successfully. Managing construction site logistics involves organizing many people, machines and materials in a limited space.
Strategic vs Operational Resources
- Strategic resource management is focused on long-term planning for managing company cash flow, assigning personnel to projects and analyzing the company’s capabilities for current and future projects in the pipeline. C-suite and executive leadership are often involved in managing overall company resources with a longer-term focus.
- Operational resource management monitors and assigns resources for daily operations, anticipating the on-site labor, equipment and material resources needed to stay on schedule and within budget. Resource allocation during a project falls primarily to project managers and construction managers.
Project Resources
There are three main groups of operational resources used to build a construction project:
- Labor (direct labor and subcontractors)
- Building materials
- Equipment (tools and machinery)
Each of these needs to be carefully coordinated to ensure the project schedule remains on track.
However, there are a variety of other resource types that a company may need to develop specific management strategies for, including:
- Consumables (PPE, gloves, masks)
- Facilities (offices, jobsite trailers, warehouses)
- Information & communication
- Technology and software
- Financial resources (budget and cash flow)
Steps in Resource Planning
As a part of overall project management, construction resource management contends with labor and skills shortfalls, project delays impacting construction scheduling and constantly changing conditions.
Here is a very general overview of the sequence of tasks involved:
Identify, validate and refine project resource needs
Plan resource allocation, including materials, tools and equipment
Assess team member skills and assign employees to appropriate tasks
Manage and schedule trade contractors
Monitor and schedule availability of material and equipment on-site
Assess sequences of tasks to allocate space and time for work on the construction site
Reallocate resources when the project needs change
Track money spent on labor and materials to compare with budget allocation
Identify resource constraints and conflicts and implement solutions
Maximize use of available resources, known as resource leveling
Stay updated on what’s happening in construction.
Subscribe to Blueprint, Procore’s free construction newsletter, to get content from industry experts delivered straight to your inbox.
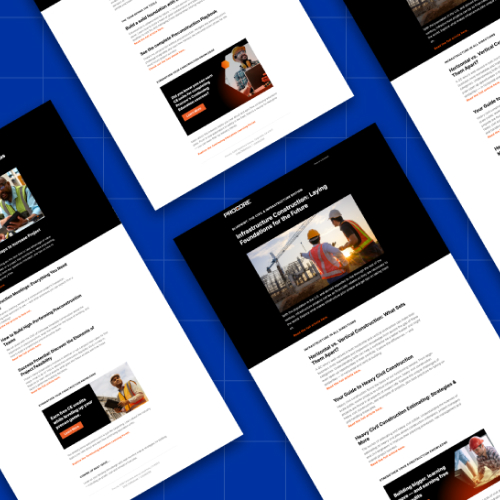
Outcomes of Successful Resource Management
As part of broader construction project management, operational resource management helps projects in the following ways:
Improved Productivity
Assigning employees to tasks appropriate to their skills uses labor efficiently. Not overworking or underutilizing workers reduces downtime, minimizes burnout and safety risks from overburdened team members and helps maintain a positive work environment. By managing materials and equipment well, these resources are available on site where and when needed so workers can begin tasks immediately.
Reduced Waste & Cost
With a clear idea of materials quantities and equipment types needed, project managers can purchase, rent or mobilize these resources more accurately, saving on costs. Accurate scheduling also prevents downtime and delays, which waste labor and can have ripple effects on other trades, potentially adding to costs.
On-time Project Delivery
Allocating people to make the most efficient use of their time keeps a project on schedule, which impacts a company’s reputation for on-time delivery. A good reputation equals money in the form of future work and a well-managed schedule helps companies gain the respect and trust of current and future clients.
Reduced Rework
When employees with the right skills are assigned to tasks, the work gets done correctly, improving the quality of the work and reducing the need for rework. Optimized scheduling gives teams enough time to complete their tasks with a focus on quality.
Effective resource management allows for better project tracking and quality control, helping project managers identify problems early.
Enhanced Visibility & Decision-Making
Better insight into resources allows management teams to make more informed decisions. Teams can foresee resource availability, conflicts or constraints and plan for contingencies.
Monitoring resources can reduce risks of delays and give teams the time to proactively plan interventions to reduce delays and reallocate resources in the most productive ways.
Improved Communication
Detailed insight into resources helps teams work more productively by encouraging communication and shared decision-making. As project scope changes or complications arise, teams with information about workforce, material and equipment resources can better adapt and alter plans to accommodate the inevitable changes in construction projects.
A Focus on Workforce Planning
Workforce planning is a central part of resource management, as labor is one of the costliest line items in a construction budget. With labor and skills shortages impacting the industry, using workers appropriately maximizes the amount and quality of work a company can complete.
We're modernizing our resource management in response to a growing pipeline and confidence in the market. We’ve been working off spreadsheets, but we realized the need for a standardized approach to understand our resources better.
We want to be confident that we have the right skill sets to enter new markets successfully and build lasting relationships with owners. This is less about bodies and more about having the skills in our resource pool to staff projects appropriately.
Alison Hart
Senior Manager of Project Solutions
Mortenson
Construction workforce planning involves four main areas:
Supply Analysis
What are the skills of the current workforce?
How are workers allocated to projects, and what is their upcoming availability?
What is the work capacity of the current team?Demand Analysis
What are upcoming project needs?
What are future staffing needs to meet business goals?Gap Analysis
What are the unmet needs for upcoming and future staffing?
What skills are needed but not present?
Are current staffing levels sufficient to build projects in the pipeline?Talent Development
Can current employees be upskilled to meet needs?
Can targeted recruiting add employees with the right skills?
How can employee retention help reduce risks of future labor shortfalls?
As contractors seek to remain profitable and expand their pipelines, retaining and attracting talent is a pressing need. Workforce management software helps contractors track and allocate their people more efficiently, potentially reducing the likelihood of overworking talented workers and burning them out.
Common Challenges in Resource Management
While construction and project managers bear primary responsibility for resource management, problems with resource allocation impact the overall company and the daily tasks of all workers. Many factors make optimal resource management difficult:
Resource Availability
A shortage in any resources – whether labor, materials or equipment – will obviously make managing those resources successfully more of a challenge. Project managers need to keep a careful eye on supply chains and market conditions for events with potential to disrupt the schedule or impact the budget. Items or materials with long lead times need careful planning well in advance to ensure they arrive on site for installation.
Maintaining and managing an inventory of commonly used items, like PPE and other consumables, is a common strategy to limit interruptions and labor downtime.
Site Conditions
Site conditions can significantly affect resource management on a construction site in a number of ways.
Weather Conditions
Adverse weather conditions, such as heavy rain, snow, or extreme heat, can disrupt construction activities and delay the delivery of materials. This can lead to inefficiencies in resource allocation and increased project costs.
Soil Conditions
The condition of the soil on a construction site can impact the type of equipment and materials that can be used, as well as the timeline for excavation and foundation work. Unstable or contaminated soil can require additional resources and time to remediate, affecting the project schedule and budget.
Site Access and Layout
The layout of the construction site can also influence resource management. Poorly planned site access points or inefficient material storage areas can hinder the movement of equipment and workers, leading to delays and increased costs.
Existing Infrastructure
The presence of existing infrastructure, such as underground utilities or adjacent buildings, can restrict the use of certain equipment and materials, requiring specialized techniques and additional resources to work around these obstacles.
To address these challenges and optimize resource management on a construction site, project managers should thoroughly assess site conditions during the planning phase and develop a detailed resource allocation plan that takes into account potential risks and constraints.
This may involve scheduling work activities around weather forecasts, allocating additional resources to address challenging soil conditions and carefully planning the layout of the jobsite to minimize disruptions and maximize efficiency.
Budget Management
Projects require precise budgeting and cost control to avoid overruns. Fluctuations in the cost of materials and labor can impact the project budget if contract controls, like an escalation clause, don't provide protection. Project managers need to stay informed about changes in the cost of materials and labor so that adjustments can be made to the budget if necessary.
Courses about construction.
For construction.
Unlock your career potential with our free educational courses on Health & Safety, Data in Construction, and more.
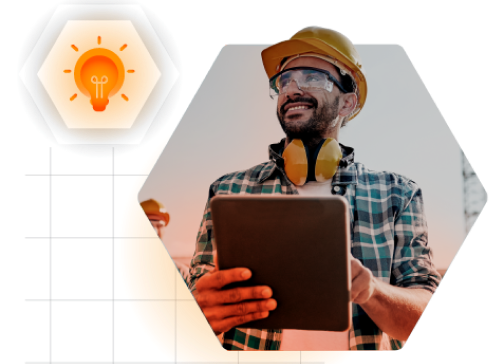
Scheduling
Resource management is inextricably linked with construction scheduling, especially for all activities on the critical path. Resources need to be allocated strategically to ensure that critical work is prioritized.
This may involve pulling skilled workers off of another project, leasing specialized equipment or rescheduling material deliveries to expedite critical activities. By focusing resources on the critical path, project managers can minimize delays and keep the project on track.
Communication and Collaboration
To effectively manage and allocate resources, team leaders need real-time access to project information to react to changes appropriately. This can include the current status of tasks, availability of resources (both human and material), potential bottlenecks or emerging issues.
For many construction companies, this is true both within a single jobsite and across multiple projects — different project teams that rely on shared equipment or labor may be able to move resources quickly to respond to urgent needs — but only if they are aware in a timely manner.
Best Practices for Effective Resource Management
Part of resource management in construction is managing the information that allows for the most productive oversight of all the resources. Using data effectively to analyze, plan, forecast and revise plans requires a deep understanding of available software platform capabilities. Here are some tips for using the data to manage construction project resources:
1. Develop a comprehensive resource plan.
Use historical data to forecast resource needs and availability. Resource management can be one element of a construction management plan. A Resource Breakdown Structure (RBS) is a common framework that works well with other planning documents.
2. Create a realistic project schedule.
Collaborate with team leads and subcontractors to devise a project schedule that accurately reflects the time needed for each task — and can adapt to unforeseen risks. Pay careful attention to the resources needed for all activities on the critical path to ensure they remain uninterrupted.
3. Protect valuable assets.
A construction company’s most valuable resource is human. Attracting and retaining talented employees is a common struggle. Understanding the needs of the people on the jobsite, and giving them opportunities to learn, grow and be rewarded is a long-term strategy for success.
On complex projects, having a very seasoned project manager to mentor newer PMs and project engineers gives them a great experience and helps us retain them for future projects.
We’re also working on a way to note which staff work well together in our resource management system because these pairings create high-performing teams.
Ultimately, people are our biggest asset.
Alison Hart
Senior Manager of Project Solutions
Mortenson
4. Monitor resources regularly.
Collect and track resource data in a system that provides real-time availability and status. Address resource allocation needs and changes during regular weekly and monthly meetings. Anticipate shortfalls and conflicts to implement necessary changes to the resource plan.
5. Prioritize communication and transparency.
Give team members access to resource plans and regularly verify resource needs for different trades and teams. Communication and collaboration can help managers anticipate changes and balance needs with available resources.
Managing Construction Resources for Project Success
Effective construction resource management boosts the success of any project. By carefully allocating resources, project managers can enhance productivity, minimize waste and ensure timely project delivery. Integrating resource management software is indispensable for managing complex data and enhancing decision-making processes.
Challenges such as resource availability, cost management, and scheduling conflicts require proactive strategies and adaptable planning. By focusing on workforce planning, communication and continuous monitoring, construction teams can navigate these challenges and optimize resource use.
Mastering resource management improves project outcomes and strengthens company reputation and client trust. As the construction industry evolves, using data insights to allocate resources adeptly can help companies stay competitive and achieve sustainable growth.
Was this article helpful?
Thank you for your submission.
0%
0%
You voted that this article was . Was this a mistake? If so, change your vote here.
Scroll less, learn more about construction.
Subscribe to The Blueprint, Procore’s construction newsletter, to get content from industry experts delivered straight to your inbox.
By clicking this button, you agree to our Privacy Notice and Terms of Service.
Categories:
Written by
Julia Tell
45 articles
Julia Tell is a freelance writer covering education, construction, healthcare, and digital transformation. She holds a Ph.D. in Media & Communications and has written for publications including Business Insider, GoodRx, and EdSurge, as well as nonprofits, international businesses, and educational institutions.
View profileExplore more helpful resources
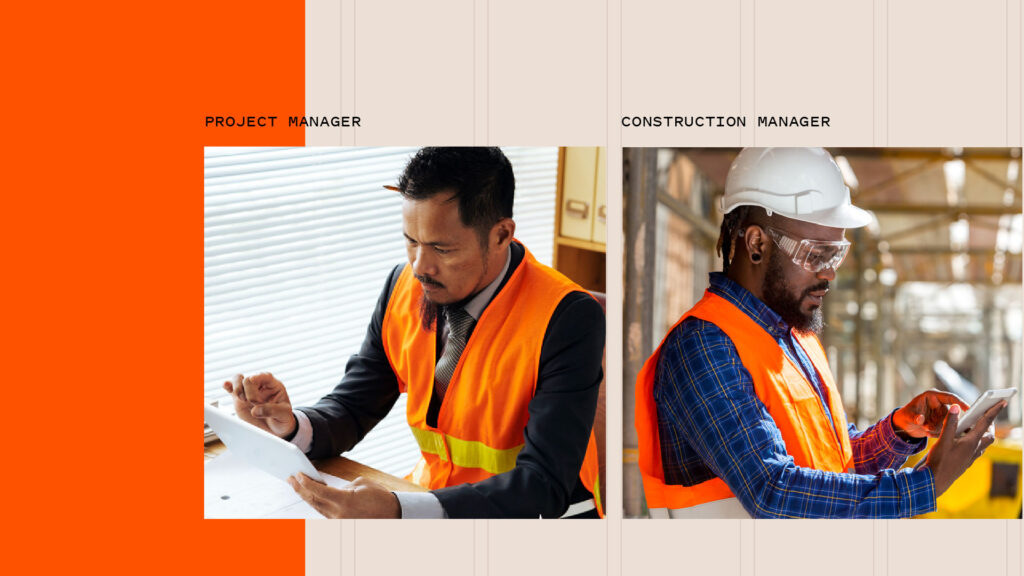
Construction Manager vs. Project Manager: Comparing Leadership Roles
Skillful oversight of construction projects allows companies to deliver to owners on time and within budget. Construction managers (CMs) and project managers (PMs) provide the necessary supervision to keep projects...
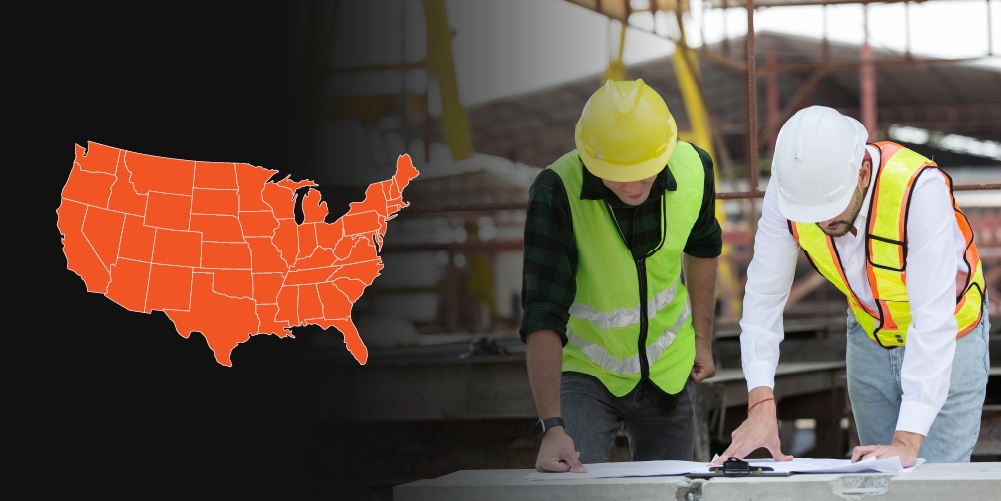
Managing Construction Projects in Different States: A Contractor’s Guide to Working Across State Lines
For many general contractors, taking on work in a new state or region can offer transformative opportunities for building a thriving business and a respected reputation. But managing projects is...
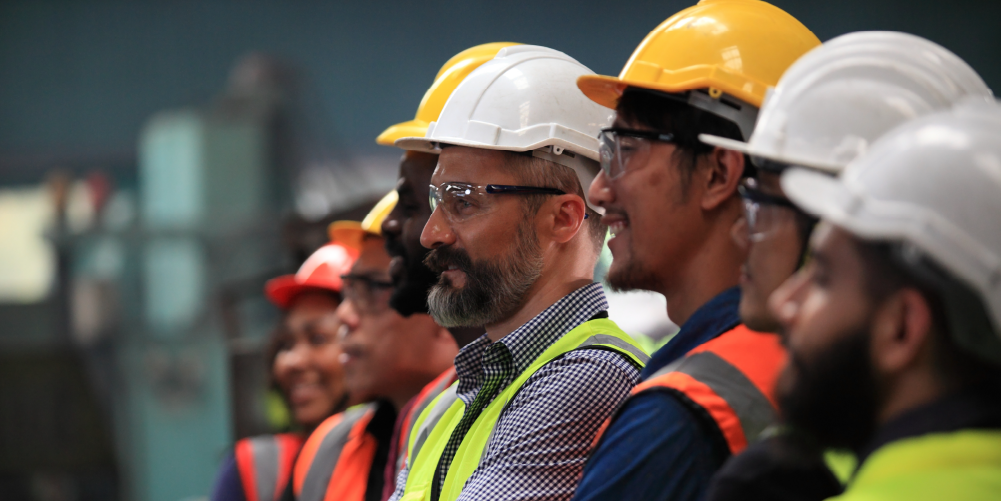
Construction Teamwork: Build a Solid Foundation With the Right Team
Construction is an industry of collaboration — no one person completes any job on their own. It could easily be argued that the most important skill for anyone in this...
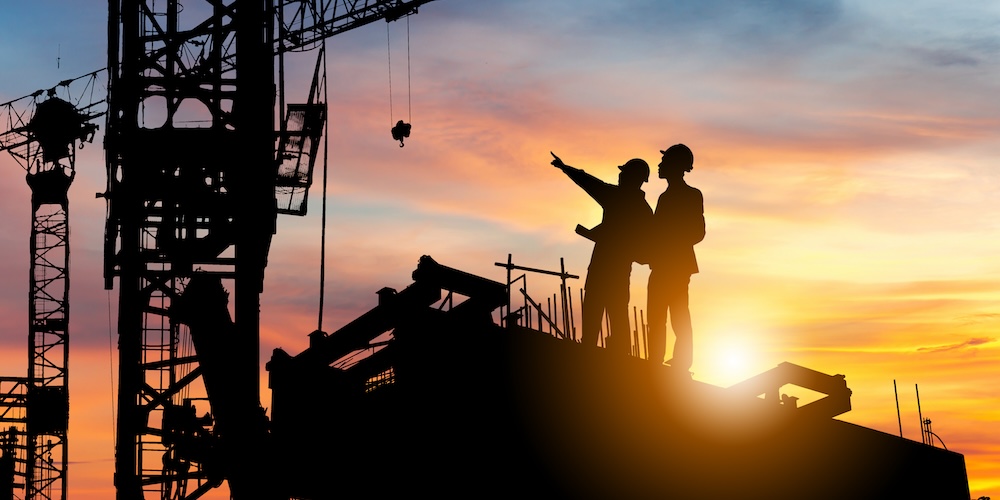
8 Tips for Managing Multiple Construction Projects
By its nature, construction work is a juggling act, with project managers and general contractors (GC) constantly adapting to changing conditions, planning to make sure there are enough materials and...