— 7 min read
Creating a Culture of Safety in Construction
Last Updated Mar 21, 2025
Last Updated Mar 21, 2025
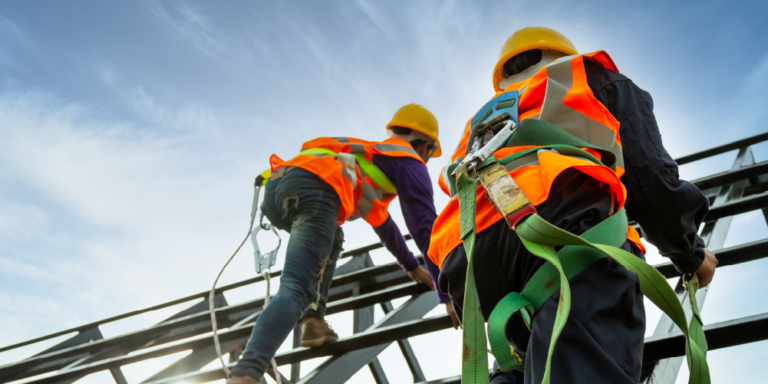
In construction, a positive safety culture impacts a company's productivity, reputation and worker morale — and it also affects the bottom line. Always a high priority, safety culture needs to adapt to the current realities and evolving conditions in the construction industry.
Creating a construction safety culture involves many elements. It starts with leadership commitment but also involves material resources, training, clear policies and open channels of communication. In this article, we'll discuss the factors that influence safety culture and how leaders can support their organization's safety culture throughout construction.
Table of contents
Leading vs. Lagging: Indicators of Safety Issues
Safety incidents — accidents or injuries — are a lagging indicator of potential problems in safety planning and implementation, and they can negatively impact a whole operation. Conversely, a positive safety culture supports identifying site risks and unsafe practices before an incident occurs, focusing on leading indicators.
Upfront incident costs are the tip of the iceberg.
If an employee gets injured, it impacts morale and causes an immediate hit to productivity. However, there are numerous costs beyond the initial cost of an injury. For instance, an incident that costs $1,000 upfront may end up costing $4,000 or more when you add in lost productivity, retraining costs, documentation and hiring people to investigate the incident.
Positive safety culture impacts the bottom line — positively.
Moving from using lagging to leading safety indicators can save money, though that may seem counterintuitive since you need to budget for safety. According to The Center for Construction Research and Training (CPWR), the common misperception that safety hurts profits can be a barrier to implementing improvements to construction safety culture.
However, say a company spends $10,000 per quarter on safety: Just one incident could easily cost more than the whole safety budget. In addition, a better safety risk score saves money on insurance and allows contractors to bid on high-profile projects requiring baseline risk scores.
Stay updated on what’s happening in construction.
Subscribe to Blueprint, Procore’s free construction newsletter, to get content from industry experts delivered straight to your inbox.
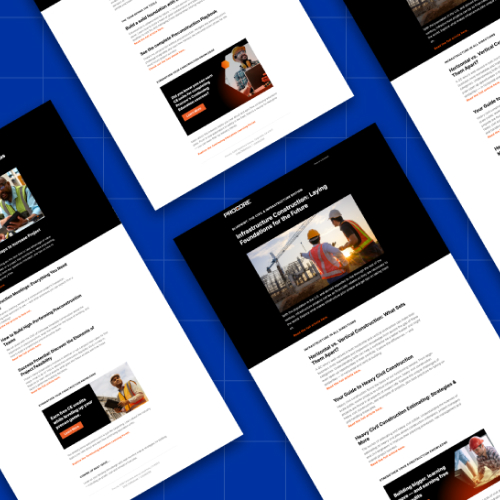
7 Tips to Successfully Implement a Construction Safety Culture
Safety as a value means weaving it into every decision at each operational level. It includes implementing policies and procedures that go above and beyond the minimum set out by OSHA. Communicating those policies clearly to all levels of the workforce is the responsibility of management. Management must also allocate material resources and dedicated time for safety training. Here are some key tips for implementing a thriving culture of safety.
1. Conduct preconstruction safety planning.
The more you emphasize safety in preconstruction, especially in the bidding phase, the safer your job site will be during construction and under warranty work. In the planning phase for each project, developing a robust safety and emergency plan is crucial. In fact, some owners, developers and public agencies use safety as a qualification factor during contractor selection. A comprehensive safety plan includes identifying risks, planning procedures to avoid hazards and devising a regular safety inspection schedule.
In addition, this is a time to prepare material resources such as PPE and first aid supplies for the job site.
2. Form a cross-sectional safety committee.
As you move into construction and implement your plans, a safety committee composed of workers—from field laborers to the superintendent—can meet regularly to assess specific processes and safety practices, needed training and revisit the job safety analysis. During routine safety inspections, the on-site or outside safety professional generates construction safety reports to give an overview of the status of risks on the site.
As safety managers and committees review safety policy documents regularly, they should also stay informed of industry practices to revise policies with the latest guidance. In addition to formal reports, safety managers can reach out on the job site to ask for feedback on safety practices that workers feel will improve conditions.
3. Take inspection reports seriously.
Leadership teams can maintain a positive safety culture by taking reports from individual workers or safety inspections seriously and mitigating identified risks. Continuous improvement and ongoing attention to safety maintain a culture that uncovers risks before an incident, and open communication helps build the relationships between managers and workers so everyone feels safe.
Learn more: Contractor’s Guide to Jobsite Inspections
4. Underline morale and mental health.
Your company's good reputation for safety helps you attract and retain the best workers. People prefer to work for companies where safety is a priority. If one worker gets injured, it drags down the morale of other on-site workers. The mental health of workers impacts productivity, and job site incidents harm morale. An environment that prioritizes worker safety improves morale.
5. Set an example.
Leading by example is one of the best ways to communicate a positive safety culture. Messaging about safety is important, but actions often speak louder than words. When an owner arrives on a site, if they wear their own safety gear — including a hard hat, high-vis vest, safety glasses, gloves and safety boots — even if they’re just there for a 45-minute walkthrough with an inspector — that exemplifies adherence to procedures for every worker.
6. Conduct regular safety training.
Regular safety training is a necessary preventative measure. Conducting ongoing training is vital as the industry is constantly changing. Training can empower workers to take responsibility for their own safety and follow the guidelines that keep those around them safe as well.
Providing comprehensive training for all employees is crucial, especially because of the current dynamics of the commercial construction industry workforce. The aging segment of the workforce has significant knowledge of how to avoid incidents and injury, yet they can get overconfident; training reminds them of proper procedures. Newer hires need to be brought up to speed and gain experience in safety as the aging workforce retires.
7. Empower and reward employees.
Safety culture should prioritize open communication so that every worker takes ownership of safety and feels free to communicate about hazards and problems they observe. The concept of kaizen — empowering every employee to recommend improvements — is a helpful way to frame this. Offering incentives for reporting instead of punitive responses can help overcome worker reluctance to report hazards.
Recognizing and rewarding safety behavior prioritizes catching leading indicators. For instance, employees who report a near miss, unsafe working conditions or pause work to correct a hazardous procedure could receive rewards for this. Rewards encourage not just the employee who reports incidents, but create an environment where reporting is celebrated rather than penalized, and this helps get buy-in from all of the workers on site.
Special Safety Considerations for Smaller Companies
In a small or medium-sized construction company, the foreperson may act as the superintendent and the project manager, in addition to being the safety person; they're wearing numerous hats. Safety committees may be a more informal process if you're not a huge commercial operation, but the need still exists to address hazards. With less overhead, quick action is necessary, often by the front line, to stop work and come up with a resolution. A safety culture with open communication makes this possible.
Smaller companies can also talk to their insurance brokers for safety resources, including specific policy examples. Insurance carriers can be strong advocates for smaller companies to help mitigate risk and improve safety culture.
Positive reinforcement supports a safety-conscious mindset. Incentives for attending safety meetings can motivate workers at all levels to participate in safety initiatives. If a project has had 2,000 reports of unsafe conditions that were taken care of immediately, that can be a milestone to celebrate. Share the success stories and take the lessons to the next project.
Safety starts with leadership.
Leadership initially demonstrates a commitment to safety by establishing it as priority — or better yet, a core company value. As Mark Whitson, President of DPR Construction, said in a 2023 keynote, “A lot of companies talk about safety as a priority. We talk about safety as a value.”
With leadership commitment to safety, open communication and setting the best possible example, everyone involved on a job can be on the same page on safety — and on their way to a safer, more efficient jobsite.
this is part of the series
Construction Safety Basics
Was this article helpful?
Thank you for your submission.
100%
0%
You voted that this article was . Was this a mistake? If so, change your vote here.
Scroll less, learn more about construction.
Subscribe to The Blueprint, Procore’s construction newsletter, to get content from industry experts delivered straight to your inbox.
By clicking this button, you agree to our Privacy Notice and Terms of Service.
Categories:
Tags:
Written by
Clark Jensen
10 articles
Clark Jensen joined Procore as a Senior Strategic Product Consultant, Quality & Safety where he spearheads product knowledge education and executes product demonstrations. He brings several years of experience in roles both on and offsite as a former senior project safety manager for a general contractor in Salt Lake City, and a senior risk control consultant for a large U.S.-based insurance firm.
View profileJulia Tell
43 articles
Julia Tell is a freelance writer covering education, construction, healthcare, and digital transformation. She holds a Ph.D. in Media & Communications and has written for publications including Business Insider, GoodRx, and EdSurge, as well as nonprofits, international businesses, and educational institutions.
View profileExplore more helpful resources

The Strategic Partnership Between Construction Safety and HR
A construction safety manager’s role is significant: It entails broad oversight over the construction workplace to prevent incidents that could cause worker injury or property damage. In addition to this...
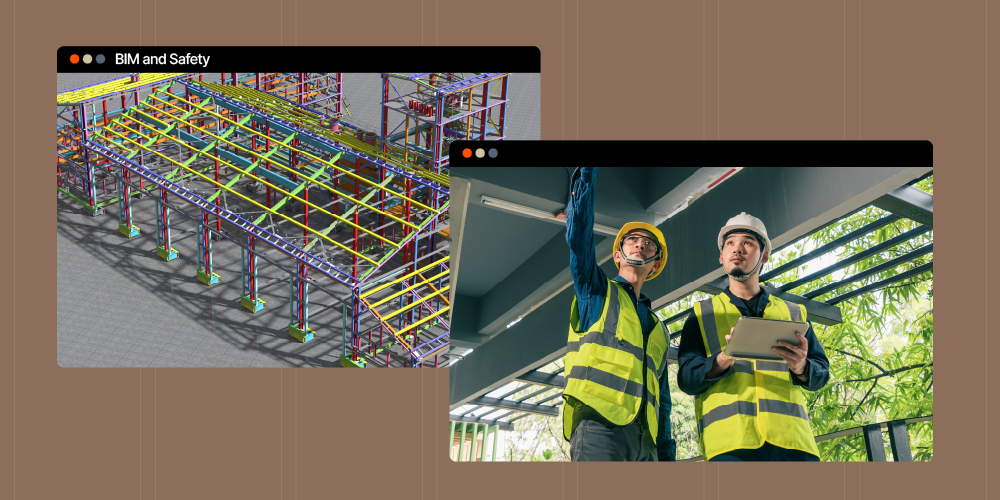
Enhancing Construction Safety with BIM Technologies
The construction industry is no stranger to tools: Even ancient civilizations developed mallets and axes to make their work easier. Today’s latest tools look different, but they can be as instrumental...
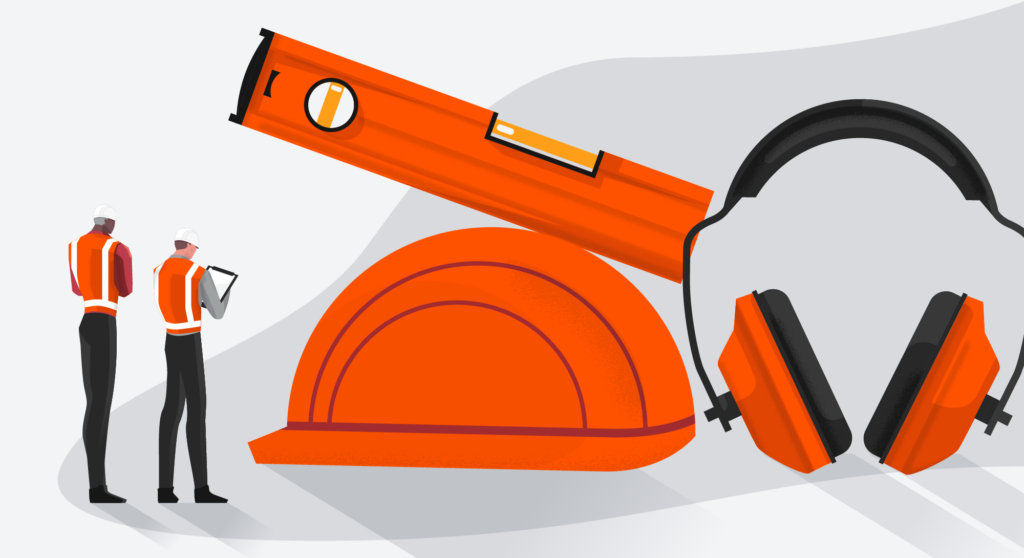
Construction Safety Training – Goals, Benefits & Emerging Trends
Construction safety training (CST) educates workers about the risks they face on construction sites and teaches them how to prevent accidents, injuries and fatalities. The construction industry has the highest...
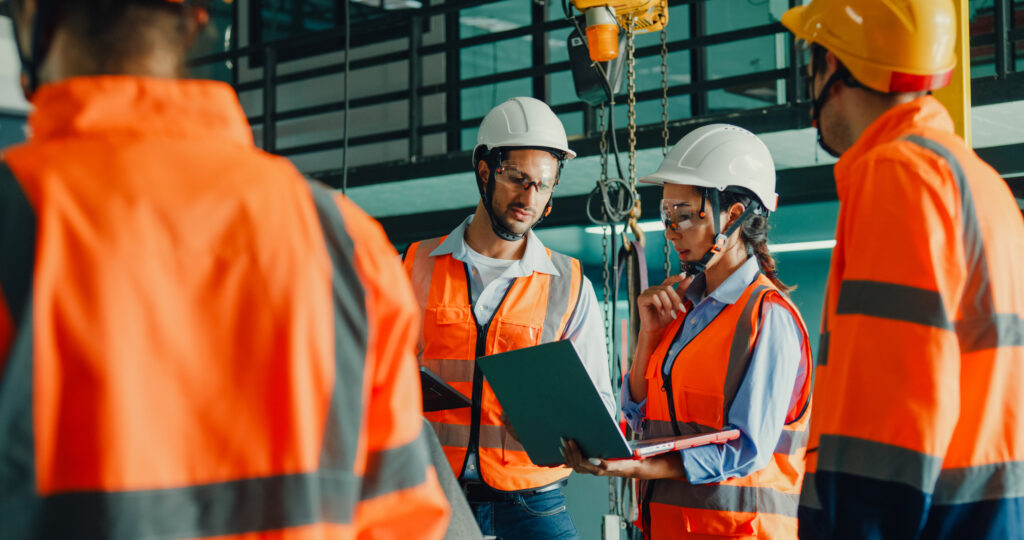
Technology for Construction Safety: Strategies to Supercharge and Scale Safety Practices
The construction industry is no stranger to the arrival of new technology, and builders are realizing its many benefits. Modernization across the industry is helping contractors streamline operations, enhance efficiency,...