— 6 min read
Mastering the Construction Safety Walk
Last Updated Sep 1, 2024
Last Updated Sep 1, 2024
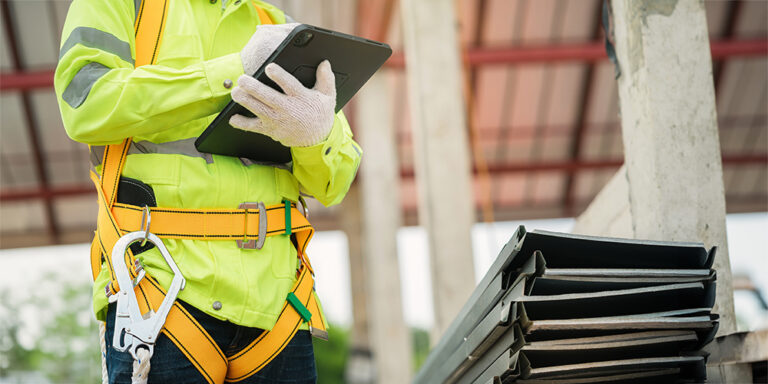
Construction sites are dynamic spaces full of risks. As work progresses and trades cycle through, the site changes from day to day and hour to hour. To stay on top of safety onsite, safety walks are a tool to spot hazards, document them, and initiate the process to resolve or mitigate the situation. Preemptively monitoring the site with regular safety walks can allow contractors to address risks before they grow or potentially cause damage or injury.
Site safety walks are a fundamental component of construction site safety management, and this article will describe best practices so contractors can realize their value in mitigating jobsite risks.
Table of contents
What is a safety walk?
Simply put, safety walks are routine inspections to identify and address any potential hazards on a construction job site. Ensuring that the site is safe for workers and is in compliance with regulations is crucial to managing risk. A site walk can uncover unsafe working conditions, material hazards, and risky work practices so they can be fixed. Ideally, the team can correct problems without stopping work, but that is only sometimes possible.
Daily walks by the site superintendent should be a regular part of the schedule, with checklists and daily logs to file. The safety manager or others can also perform safety walks weekly or at other designated intervals. Regular safety walks emphasize a company’s investment in safety and can help to reinforce a strong safety culture on the worksite.
Preparing for Safety Walks
Planning ahead for site safety walks prepares safety managers or site superintendents to look for hazards relevant to the work being performed on-site and ensure that necessary precautions, such as lighting, barriers, and fire extinguishers, are in place.
Understanding what workers, equipment, and materials are on the site — cranes, scaffolding, excavators, elevator shafts, or general site clutter — allows a safety manager or superintendent to focus on the most likely potential hazards for that site at that time.
Yet part of the purpose of safety walks is to look for unexpected problems that may not have been anticipated during initial safety planning. Remaining alert for unforeseen issues is necessary.
Safety Walk Reporting
Communicating the results of safety walks keeps personnel up and down the chain of command informed of hazards and steps planned to mitigate them. Using construction management software can make communicating with the team more efficient so that appropriate managers or subcontractor foremen can be kept in the loop about hazards and the steps that need to be taken to mitigate them.
Writing construction safety reports can give an overview of the current status of hazards on site. Documenting hazards and designating the personnel or contractor responsible for taking action to correct the problem offers clarity for the team and potentially protects the contractor from liability later.
Stay updated on what’s happening in construction.
Subscribe to Blueprint, Procore’s free construction newsletter, to get content from industry experts delivered straight to your inbox.
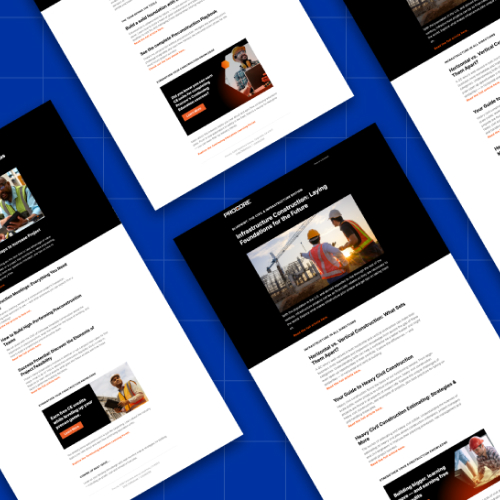
Best Practices for Safety Walks
Each project site and stage of construction will have different hazards to look for, so checklists and the needed frequency of safety walks can vary. Here are some best practices that can help optimize contractors’ use of safety walks as part of an overall safety plan.
Perform walks both regularly and randomly.
Planned daily site walks need to be part of the process. Keeping track of the changing nature of the site and identifying emerging hazards is best accomplished with familiarity. Risks can arise at any point and will be easier to address earlier. Promptly remediating them can prevent an incident from occurring.
Including random safety walks allows safety managers to see site conditions when workers have not had a chance to prepare for an inspection. This can capture additional problems that may not be apparent when the site is cleaned up in expectation of a site walk.
Plan a cadence.
A foreman or superintendent can perform the daily site walks, and a safety manager can plan more detailed weekly walks. Consider a more robust monthly or quarterly walk to further check on the implementation of the entire safety plan.
Prioritize hazards.
The first priority needs to be the most likely and dangerous hazards, referred to as the “Focus Four” hazards by OSHA. These include falls, caught-in or -between, struck-by and electrocution. Look at all high-risk areas and activities, including working at heights, mechanical or elevator shafts, cranes or underground utilities.
Once the highest-risk issues are checked, then move to other areas of safety, including checking that workers are following safety rules like wearing proper Personal Protective Equipment (PPE).
Document, communicate & follow up.
Document the findings of every safety walk. Ensure that the stakeholders are informed of any issues and that a plan to fix the problem is put in place. Safety managers need to report findings but should also engage with on-site workers to ask questions, reinforce safety measures that need to be followed, and create a transparent safety culture that rewards reporting of hazards.
Follow up on any findings as soon as possible to ensure corrective action has been taken. Create an action plan to implement changes to mitigate risks. Documentation helps track issues, and is especially helpful for contractors using construction management platforms that enable transparent communication with multiple parties.
I remember a time when we had scaffolding on a job site with a new scaffolding contractor. Due to the high-risk nature of scaffolding, we decided to pay extra attention to them. It was windy and cold, as it was fall, so they had to put tarps around the scaffolding. When you put a tarp around something elevated and exposed to the wind, it essentially becomes a sail.
We conducted numerous inspections and communicated our concerns to the contractor, expecting them to address the issues since they were the experts. Unfortunately, the scaffolding eventually failed and fell onto a road, nearly hitting a car with a mother and her children inside. Thankfully, no one was harmed.
Although the incident was serious, we were relieved to have thorough documentation that showed we identified and communicated the risks to the contractor. This documentation was crucial in demonstrating that we fulfilled our responsibilities, which helped us avoid liability.
Clark Jensen
Strategic Product Consultant, Quality & Safety
Procore
Involve outside parties.
Building relationships with other safety stakeholders can be very beneficial. Consider inviting the local fire department, the municipality’s inspector or OSHA to walk the site with you. Take advantage of relationships with an insurance carrier or broken, who often offer risk management services, and use their expert insights to help protect further against risks. At wider intervals, an outside assessment can prove beneficial and offer suggestions or uncover problems that regular walks have not noted.
Engage workers.
Getting buy-in from workers on safety practices can be challenging, but safety walks are one opportunity to engage on-site workers to get their feedback and share best practices. One good technique to share is the “Take Two” process, where workers stop for two minutes to assess the workplace for hazards and take action to protect themselves and others before beginning work. Safety managers can also offer incentives or rewards for reporting hazards, as this can encourage more vigilance on the part of all workers, and can improve an overall safety culture on site.
Safety walks are one piece of the puzzle.
Safety walks are just one integral part of a construction safety plan. There should be continuous oversight to ensure that the safety plan is being implemented and revisions made to the plan as conditions shift. Communications with workers and management and proactive mitigation of potential hazards can avert incidents and keep a job site in compliance with all safety regulations.
this is part of the series
Construction Safety Basics
Was this article helpful?
Thank you for your submission.
100%
0%
You voted that this article was . Was this a mistake? If so, change your vote here.
Scroll less, learn more about construction.
Subscribe to The Blueprint, Procore’s construction newsletter, to get content from industry experts delivered straight to your inbox.
By clicking this button, you agree to our Privacy Notice and Terms of Service.
Categories:
Tags:
Written by
Clark Jensen
10 articles
Clark Jensen joined Procore as a Senior Strategic Product Consultant, Quality & Safety where he spearheads product knowledge education and executes product demonstrations. He brings several years of experience in roles both on and offsite as a former senior project safety manager for a general contractor in Salt Lake City, and a senior risk control consultant for a large U.S.-based insurance firm.
View profileJulia Tell
43 articles
Julia Tell is a freelance writer covering education, construction, healthcare, and digital transformation. She holds a Ph.D. in Media & Communications and has written for publications including Business Insider, GoodRx, and EdSurge, as well as nonprofits, international businesses, and educational institutions.
View profileExplore more helpful resources

The Strategic Partnership Between Construction Safety and HR
A construction safety manager’s role is significant: It entails broad oversight over the construction workplace to prevent incidents that could cause worker injury or property damage. In addition to this...
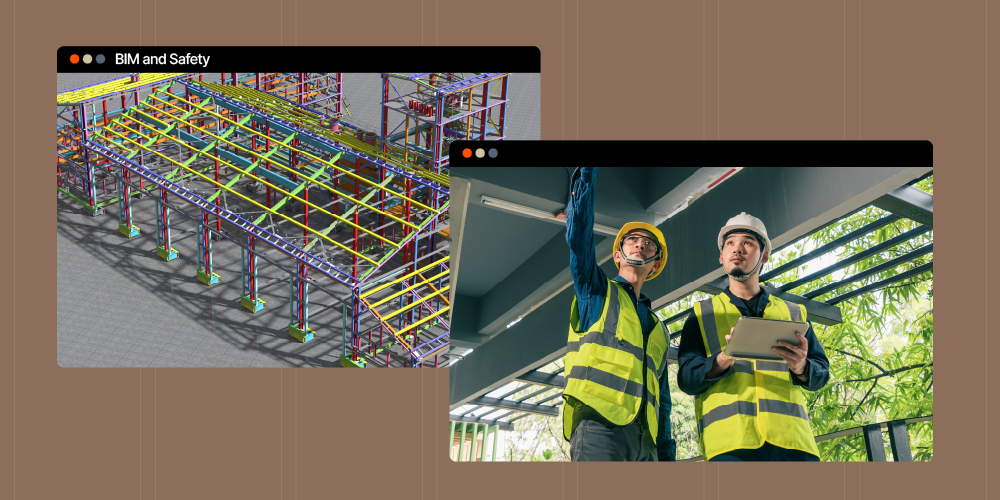
Enhancing Construction Safety with BIM Technologies
The construction industry is no stranger to tools: Even ancient civilizations developed mallets and axes to make their work easier. Today’s latest tools look different, but they can be as instrumental...
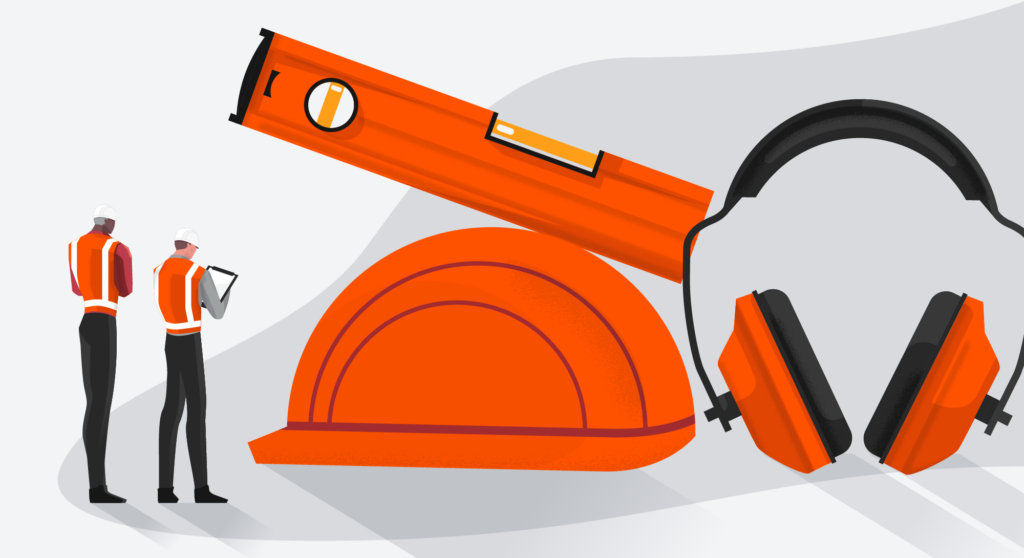
Construction Safety Training – Goals, Benefits & Emerging Trends
Construction safety training (CST) educates workers about the risks they face on construction sites and teaches them how to prevent accidents, injuries and fatalities. The construction industry has the highest...
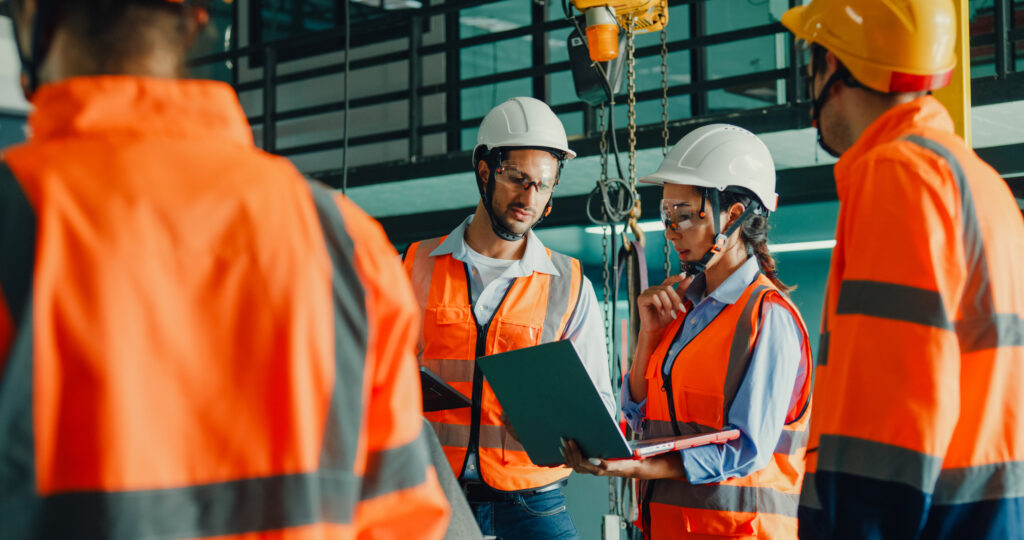
Technology for Construction Safety: Strategies to Supercharge and Scale Safety Practices
The construction industry is no stranger to the arrival of new technology, and builders are realizing its many benefits. Modernization across the industry is helping contractors streamline operations, enhance efficiency,...