— 6 min read
Construction Sequencing: Optimizing Timelines & Resources
Last Updated Nov 15, 2024
Last Updated Nov 15, 2024
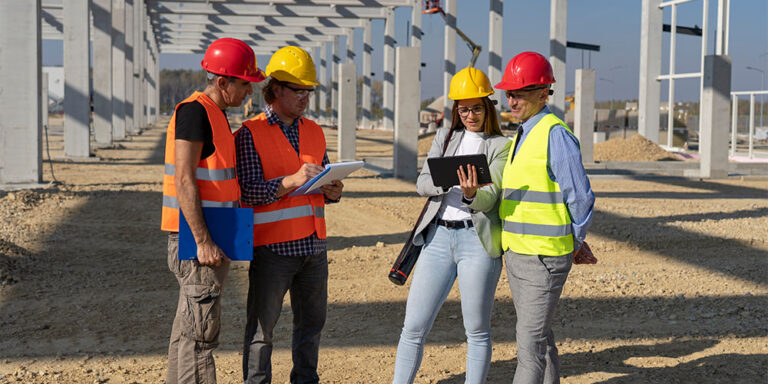
Construction plans can be ambitious and innovative on paper but the real measure of their efficacy is simple: Can they be achieved? Creating attainable plans opens a whole world of projects completed on budget and on time, but it requires effective sequencing.
Construction sequencing, also known as phasing, is the process of ordering required tasks to optimize a project’s resources, budget and timeline.
This article explores the importance of construction sequencing, keys to improving how it’s done and how it’s enhanced by construction technology.
Table of contents
What is construction sequencing?
The work needed to complete a project is usually determined at the very beginning of planning, often through processes such as the work breakdown structure (WBS). Construction sequencing is about finding optimal ways to complete those tasks and hit key milestones, such as rough-in inspections, punch list or project closeout.
Sequencing is a huge factor in many common planning methods, including the critical path method. It’s also a major component of other planning methods that are gaining tractions, such as the last planner system and takt planning.
At its core, sequencing is about managing the flow of people and resources to maximize efficiency and safety. The process usually begins by dividing a project into zones, often by floor, rooms or areas. These zones can be numbered to create an order in which teams will move and work their way through the project.
From there, the work of the trade partners will be divided into phases that ensure crews can move continuously through their tasks without interruptions, such as trade stacking (when multiple trades are in the same area at the same time, leading to delays as partners wait for each other to finish tasks).
For example, a hotel might be divided into floors or rooms and the trades might be sequenced in a strategic order. This allows drywall work to begin in one area while systems are being installed in another. Sequencing can be repeated for zones that are similar, such as in an office building or units in an apartment building.
It’s important that sequencing is not simply finding the shortest possible schedule duration, but instead creates realistic sequences of tasks by accounting for task and sequence durations and feasibility, as well as a few other variables:
- Dependencies and interdependencies
- Resource availability
- Site conditions and constraints, including issues related to weather, anticipated challenges in earthwork or site logistics
- Complying with codes, regulations and other permitting requirements required by the authorities having jurisdiction (AHJs)
- Contingency planning, including buffer time for unforeseen circumstances when possible
- Budget constraints
Explore data and trends for building materials prices.
Get the latest U.S. retail prices and view historical trends for common building materials.
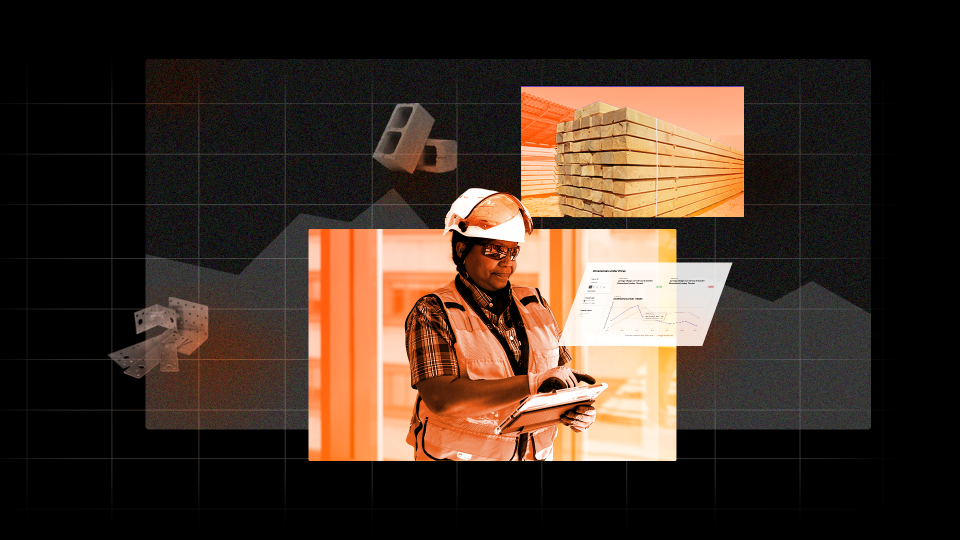
Managing Challenges in Sequencing
There are a few common challenges that often pop up during the construction sequencing process.
Unexpected Events
Issues related to weather, material procurement or site conditions, such as discovering soil contamination, can cause delays that put a project at risk of falling significantly behind.
Building buffer time into the schedule can absorb some of these delays. However, being reactive usually only puts the project further behind. When something major throws off a plan, it’s often best to pause the project, reassess the work that needs to be done and resequence.
Resource Constraints
Projects don’t happen without labor, materials and equipment, so sequences should account for their availability. The availability of skilled labor can inform how fast a trade might be able to move through a given zone. The number of cranes on a project might limit the amount of work that can be done each day.
There are a few ways to adjust to resource constraints. If a trade is moving at a pace that is slowing down other trade partners, the project can be divided into more zones, split differently or the order of trades can be adjusted to put slower teams last.
Special Project Types
Sequencing can get complicated with certain types of projects. Working in an occupied building, such as adding a new wing on to an in-use hospital, requires careful considerations of safety, site logistics and utilities. Projects in dense urban areas might have constraints on how and when the site can be accessed. A project in a confined space, such as building a restaurant, might have limited space for material storage and storing. Effective sequencing is realistic, so special projects might require more time for planning and execution.
Safety
Sequencing should always account for safety and risk analyses. Being careful now almost always saves significant time later on by avoiding incidents or accidents. Sequencing shouldn’t overextend crews or create the need for overtime that can lead to low quality and dangerous work.
Tools & Technology in Sequencing
Technology can make sequencing easier and improve processes in several ways.
Project Management Software
Project management software can help visualize and track sequencing. Digital tools also make it easier to prototype different sequences and track and monitor their potential impact on budget and timelines. Project management software can translate sequences into schedules, budgets and other visual aids that can be shared with key stakeholders.
Gantt Charts
A Gantt chart is a bar chart that displays a project’s activities along the project’s timelines. It can be used for managing and planning phases and sequences. Gantt charts are commonly displayed or shared throughout project management software to show up-to-date status of the project and a lookahead showing the next three weeks of work.
Pull Planning
Pull planning provides a visual representation of a project’s milestones, starting with the end goal and moving backwards. This planning strategy encourages collaboration from members of the project team to determine the most efficient ways to complete tasks in order to reach an activity’s target completion date.
BIM
Building information modeling (BIM) helps create virtual models of structures before construction begins. These in-depth models display tasks’ durations and required materials, track progress and can be used to anticipate dependencies. All of these things can help create realistic sequences.
Prefabricated Construction
Prefab construction involves manufacturing or assembling components at a separate location and then being delivered to the worksite. Common prefab components include roof and floor trusses, wall panels, bridge components, drainage systems for water and wastewater projects and steel framing. Prefabrication can make sequencing easier, as it reduces work, storage and assembly done onsite.
Achieving Great Sequencing
A lot goes into effective sequencing, but few things go as far as the power of collaboration. Superintendents should strive to be open to communication and feedback from specialty trade foremen. They should encourage collaboration amongst teams and focus on removing roadblocks, rather than making all the decisions on their own. Bringing trade partners into the process, often in the form of collaborative meetings, can help create sequences that are more dynamic, thorough and infused with expertise.
Was this article helpful?
Thank you for your submission.
67%
33%
You voted that this article was . Was this a mistake? If so, change your vote here.
Scroll less, learn more about construction.
Subscribe to The Blueprint, Procore’s construction newsletter, to get content from industry experts delivered straight to your inbox.
By clicking this button, you agree to our Privacy Notice and Terms of Service.
Categories:
Tags:
Written by
Dave Brown
Dave is a Senior Strategic Product Consultant for Procore, specializing in General Contractors. Previously, he worked for Consigli Construction Co in Boston and Washington, DC as a Project Engineer and Assistant Project Manager, responsible for a variety of activities including bidding and procurement, contracts, and cost control. Dave holds a Bachelor's Degree in Structural Civil Engineering from Bucknell University.
View profileJames Hamilton
70 articles
James Hamilton is a writer based in Brooklyn, New York with experience in television, documentaries, journalism, comedy, and podcasts. His work has been featured on VICE TV and on The Moth. James was a writer and narrator for the show, VICE News Tonight, where he won an Emmy Award and was nominated for a Peabody Award.
View profileExplore more helpful resources
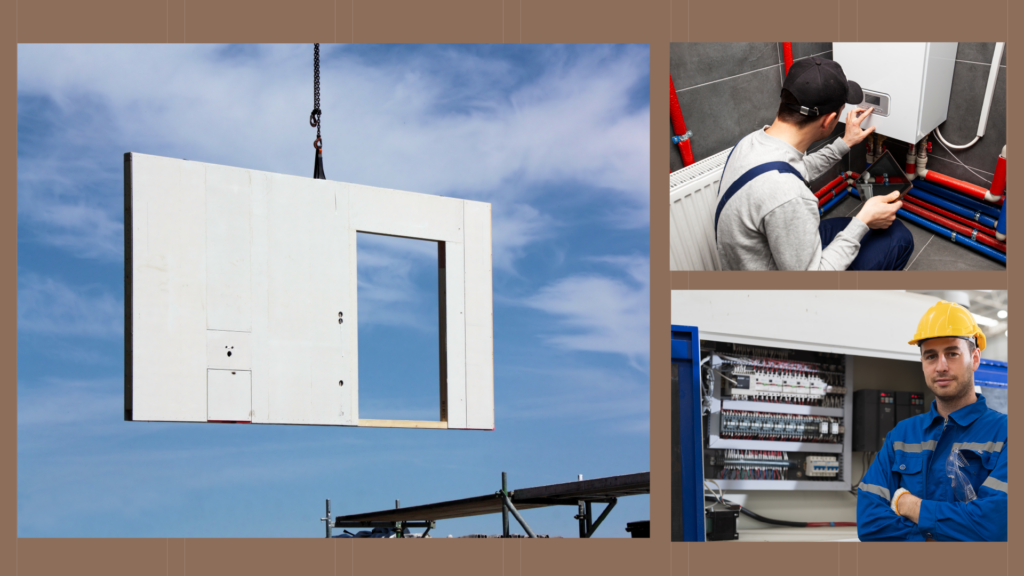
Modular Construction and MEP: A Collaborative Pairing
In an age of supply chain disruptions, workforce shortages, and rising material costs, off-site construction — including modular construction methods and prefabricated materials — is surfacing as a multipurpose solution....
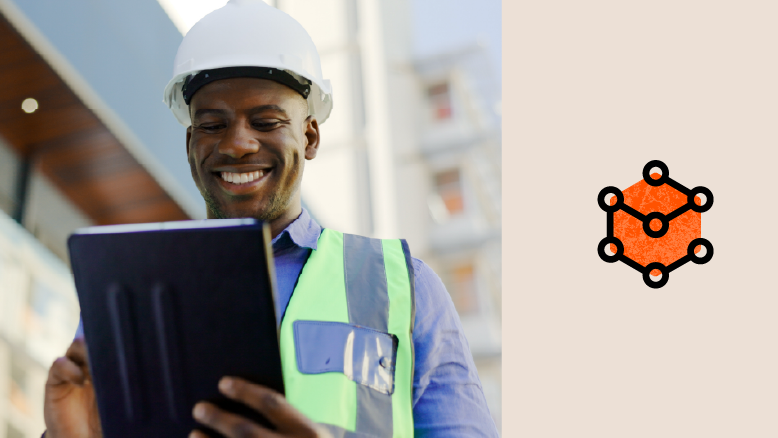
Connected Construction: Transforming the Industry Through Integration
Construction projects are becoming increasingly complex, so companies need to innovate to accurately and profitably complete these modern structures. Connected construction — using technology and data to improve communication, processes...
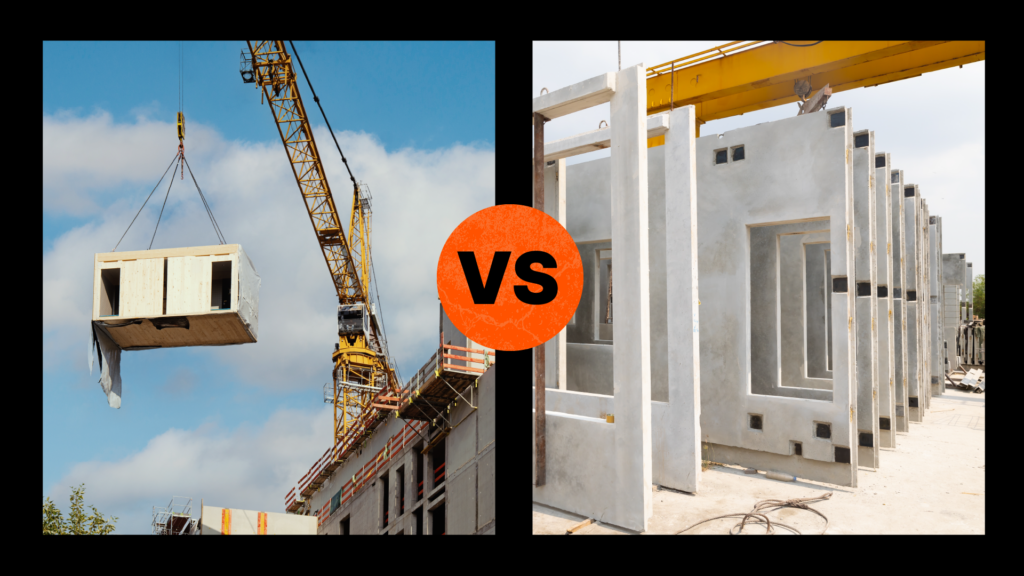
Off-Site Construction: Prefab vs. Modular
As the construction world becomes ever more competitive, deadlines get tighter and the margin for error gets slimmer, project owners around the world are always looking for an edge. Thanks...
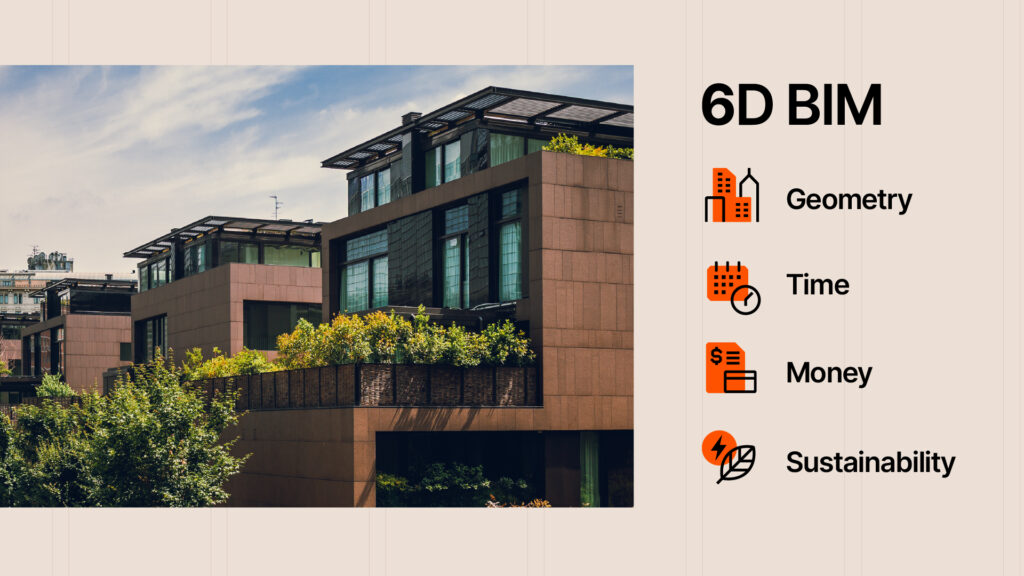
The Role of BIM in Sustainable Construction
Building information modeling (BIM) is transforming the architecture, engineering, and construction (AEC) industry. With this kind of sophisticated modeling, the industry has shifted from designing in 2D to 3D. This helps...