— 10 min read
A Construction Pro’s Guide to Crane Safety
Last Updated Sep 11, 2024
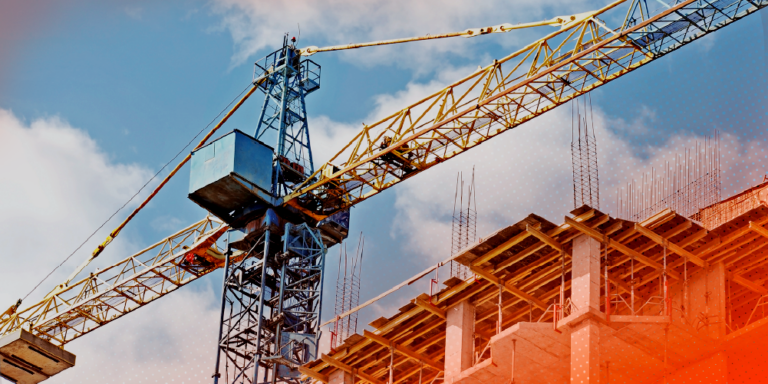
Some of the worst types of accidents that can occur on construction sites involve cranes. Tip-overs, falling on adjacent structures, dropping materials, crushing people — crane accidents can cause catastrophic, and deadly, losses on construction sites.
The Sarens SGC - 250, for example, is considered the largest land-based crane in the world. The ring-based, heavy-lifting crane weighs about 5,511 tons and has a maximum load capacity of about 275,577 tons.
The increased risk that occurs when equipment of this size is on site requires construction site and safety leaders to be vigilant about worker safety. Safety protocols and information about successfully navigating jobsite when cranes are operating should be consistently communicated to the entire project team.
This article will explore all aspects of crane safety — from types of cranes typically used on construction sites, to precautions to take when operating this heavy equipment on projects.
Table of contents
Common Types of Construction Cranes
Different types of cranes have unique operational requirements and safety considerations. For example, static cranes are generally used for long-term construction projects and typically remain on site. They’re either attached to the roof of the structure being built, or anchored to the ground. Static cranes can lift heavier loads and move materials along a preset path.
Mobile cranes are able to move on, off and throughout the jobsite. These types of cranes tend to have lower lifting capacities, but their mobility makes it easier to get materials moved to different locations on the project.
The following is a list of cranes that are commonly used in construction, their uses and the considerations operators and site workers need to take into account when they’re being operated.
Mobile Cranes | |
Floating or Barge Cranes | Floating cranes are used for construction over bodies of water. Stability on the water and ensuring buoyancy are a priority when operating these. On average, floating cranes can haul and lift about 2,500 tons. |
Crawler Cranes | Crawler cranes are tracked and have a crawler undercarriage similar to an excavator. They are heavy and slower to move but are ideal for their stability and lifting capacity. Some of the largest crawler cranes can lift up to 3300 tons. Because crawler cranes can weigh upwards of 5,000 tons, special consideration is needed when assembling and disassembling them due to their massive weight and size. |
Rough Terrain Cranes | Rough terrain cranes are typically wheeled cranes that are capable of moving over rough or uneven terrain. They have a lifting capacity of up to 65 tons. They’re generally easier to set up than other mobile cranes, are maneuverable and can be driven into tight spots. However, rough terrain cranes generally have lower lifting capacities than crawler cranes. |
Vehicle (or truck) mounted cranes | Truck-mounted cranes have a hydraulic crane attached to its chassis that’s used for moving heavier items around the job site. Their lifting capacities vary based on their weight, but some of the heaviest truck-mounted cranes can lift up to 50 tons. |
Overhead Cranes | Overhead cranes, also referred to as Gantry and bridge cranes, are generally used or manufacturing or industrial jobs. Their lifting capacities vary based on the size of the crane, but double girder overhead cranes can lift up to 500 tons. |
Static Cranes | |
Tower Cranes | Tower cranes are some of the most recongnizable cranes in construction. They can reach upwards of 250 feet, and require a stable foundation like a concrete pad or connection to a steel structure. Generally, tower cranes are used on urban development projects for skyscrapers and other elevated structures. There are various types of tower cranes, including hammerhead cranes, luffing jib cranes, and self-erecting cranes. |
Hammerhead Cranes | These T-shaped cranes have a horizontal jib that is fixed at level height to prevent it from moving up and down. The jib on hammerhead cranes include a trolley that allows it to move loads horizontally. Hammerhead cranes generally have higher loading capacity than other types of tower cranes and some models can lift up to 50 tons. |
Self-erecting Cranes | Due to their compact sizes, self-erecting cranes are ideal for small to medium construction projects. Self-erecting cranes can be easily put together and dismantled, and are generally transported to, and around, the construction site on trailers. Typically, self-erecting cranes have a lower lifting capacity than other tower cranes with general capacity around 4 to 5 tons. |
Luffing jib Cranes | Because luffing jib cranes can move up and down, they can lift loads at different angles. Additionally, the swing on luffing-jib cranes is minimal, making them more practical in dense environments like cities or aiport projects. Luffing jib cranes generally have a high lifting capacity and can lift up to 60 tons. |
Training Requirements for Crane Operators
In the U.S., the National Commission of Certification of Crane Operators (NCCCO) is the governing body that certifies crane operators.
Beyond certification, crane operators should also take continuing education classes at least yearly to stay on top of changes or updates regarding crane operations and new technologies that provide more efficiency when working on jobsites.
Preparing to Safely Operate a Crane
Aside from general site specific safety plans and conducting thorough job safety analyses, site and safety leaders should have a plan in place to keep their teams informed on the entire process from bringing a crane onto the jobsite, the details of its operations on the project, to when the crane is removed.
Conduct regular inspections.
Third-party inspectors should be scheduled to inspect each crane that’s planned to be on site. Annual crane inspections should be conducted to make sure the crane is in compliance with OSHA standards and in good operational standing.
This includes checking the integrity of the crane’s joints, bolts and pins and identifying signs of fatigue on both the rigging and cabling, as well as the structure itself. Inspectors may also conduct diagnostic tests on all electrical systems to make sure they’re functioning properly.
In addition to annual inspections, either the crane’s owner or a third-party inspector should conduct regular inspections on a monthly basis. These informal checks should be done to follow up on any problems that were identified in the annual inspection, as well as closely monitor how the crane is functioning.
Additionally, onsite crane operators should conduct daily operational inspections. The operator is the person most familiar with the crane and its operation, and generally the most knowledgeable about every aspect of how it functions. Daily inspections also allow the operator to catch any last minute issues before they cause a catastrophic problem.
Pro Tip
The first thing that should be done after you clear and grub, or get the site ready after excavation, specifically when you’re working on a basement or going subgrade, is make sure that a pad is engineered to support the crane.
Create a crane pick plan.
A crane pick plan depicts all the details of a crane’s activity while on the project. Plans should outline what is being picked up, who is rigging and tying the materials, what types of knots and fasteners are being used and certifications for each member of the team.
The height of the building and the proximity of the crane to the structure must also be taken into account and noted in the plan.
One major component of a crane pick plan is measuring the soil stability on the construction site. In order to safely operate a crane, the soil must meet a certain compaction rate to ensure stability. In certain regions, underground water tables may also need to be assessed to make sure the crane will not tip over or sink.
If the ground the crane will be placed on is not firm or stable enough, using an outrigger pad is necessary to reinforce stability and prevent the ground from shifting when the crane is operating.
Identify any impact on the community.
Another aspect of planning is to determine whether the crane’s arm has to swing above any roads or other public areas near the jobsite. In these cases, site leaders should proactively plan for traffic diversions and close any sidewalks or other public areas that are in proximity of the crane’s operation.
Part of the planning process involves gaming out worst case scenarios. In the event something catastrophic does happen and a crane falls or drops its load, leaders should have procedures communicated for operators to minimize damage to areas in and outside of the site, and avoid injuries for the general public and onsite workers.
Prepare for using multiple cranes onsite.
Some large-scale projects may require the use of multiple cranes at one time. Tandem lifts, for example, require two cranes for materials that exceed lifting capacity for one crane to do the work. In these cases high-risk scenarios, site leaders and crane operators have to plan carefully to avoid disaster.
Whenever we were operating multiple cranes on a site, there had to be very clear communication. Are the cranes in striking distance of each other? How are the operators going to communicate? Tandem lifts have a high failure risk and we had to be cognizant about what was happening on the entire site whenever we needed to do them.
Clark Jensen
Strategic Product Consultant, Quality & Safety
Procore
Safety Precautions During Operations
Beyond operational safety, specific procedures should be shared and stored in an accessible place for all onsite stakeholders. This information should be updated constantly to reflect any procedural changes that impact safety while cranes are onsite.
Share rigging procedures.
The rigging process involves technical proficiency as well as teamwork, communication and adherence to safety protocols. Understanding and sharing the load radius and operational limits prevents overloading the crane, which could cause tip-overs, and minimizes the risk of accidents or equipment damage.
Keep lines of communication open and clear.
Whether it’s hand signals or radio communication, a clear plan for communication when cranes are being operated needs to established so crane operators and riggers are in sync when assessing and preparing loads. Crane operators rely on the riggers' expertise to confirm that the load is properly rigged and ready for lifting. Each party needs to have a clear line of sight to one another while the crane is operating.
Comply with crane load limits.
Most cranes are equipped with electronic load capacity systems that prevent them from operating beyond their rated limits. These added safety features help prevent failures due to overloading.
Additionally, automated lockouts and alarms restrict crane movement when load capacities or operational limits are exceeded. This provides operators with better controls and monitoring capabilities while moving loads and significantly reducing risks during operations.
Have an emergency plan.
Having an established culture that prioritizes safety sets the precedence for project teams to keep an eye out for unsafe practices. In the event that disaster strikes while a crane is in operation, everyone on site should be trained and aware of what steps to take.
Emergency plans should be included in the overall site-specific safety plan with key people to contact, including first responders and site leaders.
The plan should be easy to access and stored digitally so site workers can respond quickly in emergency situations.
Go beyond OSHA regulations.
The Procore Safety Qualified program provides construction professionals with everything they need to know to create a culture of safety.
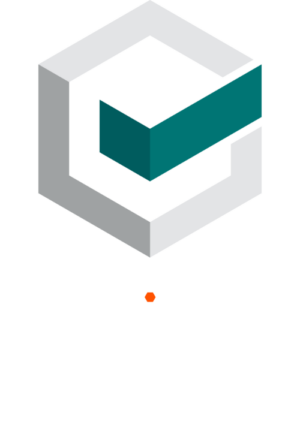
Communication and Preparation for Cranes is Key
When planning for cranes to be brought onto a project, proactive preparation can avoid costly damages and save lives. By creating safety and emergency plans that are easy to follow and are visible to all parties on the jobsite, everyone understands their role and can help reinforce safety expectations when cranes are in operation.
Keeping all crane activities and inspection documentation updated with notes and images on a software management platform boosts operators’ and site leaders’ ability to stay on top of any needed equipment maintenance and in compliance with federal and local crane operation regulations. Proper site preparation and familiarity with scheduled jobsite activities allows teams to come together to ensure everyone’s safety when operating such massive equipment.
Was this article helpful?
Thank you for your submission.
0%
0%
You voted that this article was . Was this a mistake? If so, change your vote here.
Scroll less, learn more about construction.
Subscribe to The Blueprint, Procore’s construction newsletter, to get content from industry experts delivered straight to your inbox.
By clicking this button, you agree to our Privacy Notice and Terms of Service.
Categories:
Tags:
Written by
Clark Jensen
10 articles
Clark Jensen joined Procore as a Senior Strategic Product Consultant, Quality & Safety where he spearheads product knowledge education and executes product demonstrations. He brings several years of experience in roles both on and offsite as a former senior project safety manager for a general contractor in Salt Lake City, and a senior risk control consultant for a large U.S.-based insurance firm.
View profileAnthresia McWashington
19 articles
Anthresia McWashington is a Content Manager at Procore. She previously worked as an editor and reporter for Gulf Energy Information and Houston Media Group. She earned her BA in Communications and Journalism from the University of Houston. Anthresia loves track & field and practicing her French. She lives in Houston.
View profileExplore more helpful resources
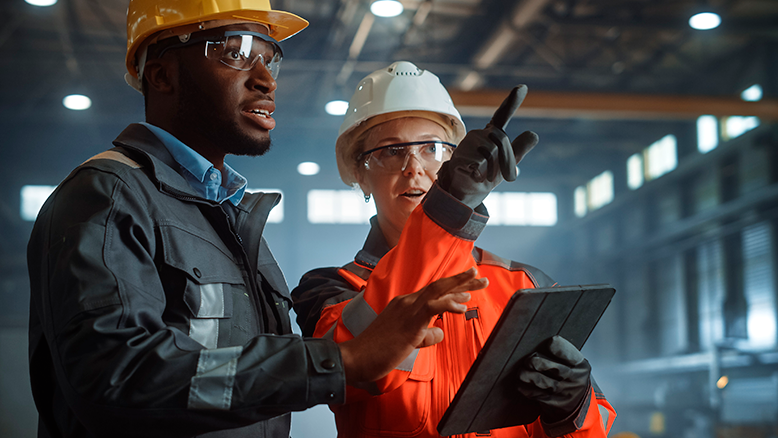
On the Safe Side: Using Data to Boost Subcontractor Safety
Capturing data to mitigate the safety risks incurred by subcontractors as well as in-house workers demands proactive risk management measures, transparent change management and methodical strategy. Applying data to safety...
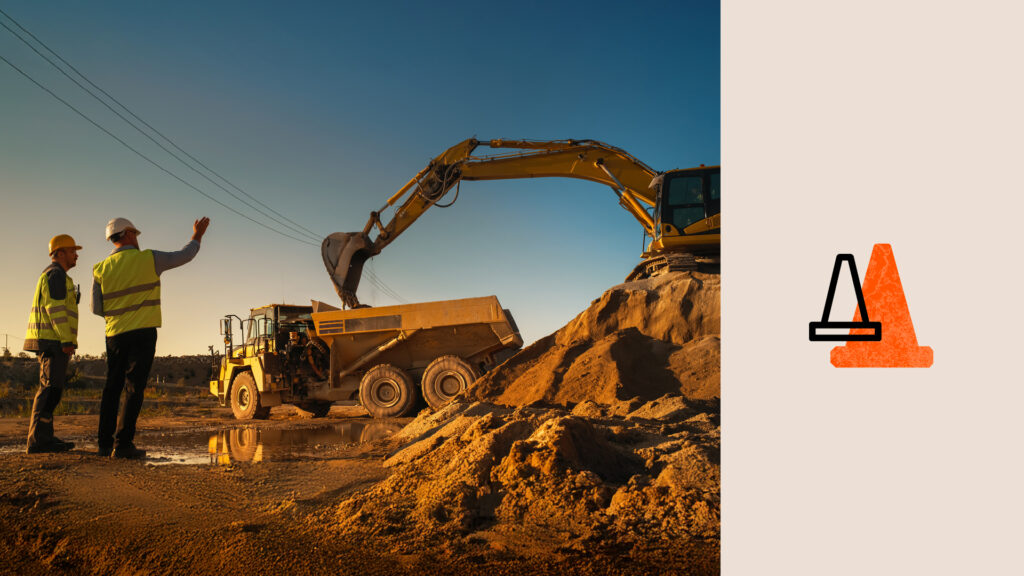
Top Techniques for Heavy Equipment Safety & Operations
Nearly 1 of every 5 workplace fatalities occurs in the construction industry. It is increasingly important to create a culture of safety and reduce the risk of workplace accidents, and...

Preconstruction Partnerships: How Safety Pros Can Collaborate with Estimating & Proposal Teams
Construction leaders and safety professionals are developing a strong understanding of how safety programs positively impact project outcomes. When safety is woven into every aspect of operations from pre-construction to...

The Strategic Partnership Between Construction Safety and HR
A construction safety manager’s role is significant: It entails broad oversight over the construction workplace to prevent incidents that could cause worker injury or property damage. In addition to this...
Free Tools
Calculators
Use our calculators to estimate the cost of construction materials for your next project.
Templates
Find a template to help you with your construction project tasks.
Material Price Tracker
Get the latest U.S. retail prices and view historical trends for common building materials.
Glossary
Explore key terms and phrases used in the industry.