— 8 min read
How to Create a Construction Safety Training Program
Last Updated Jan 24, 2025
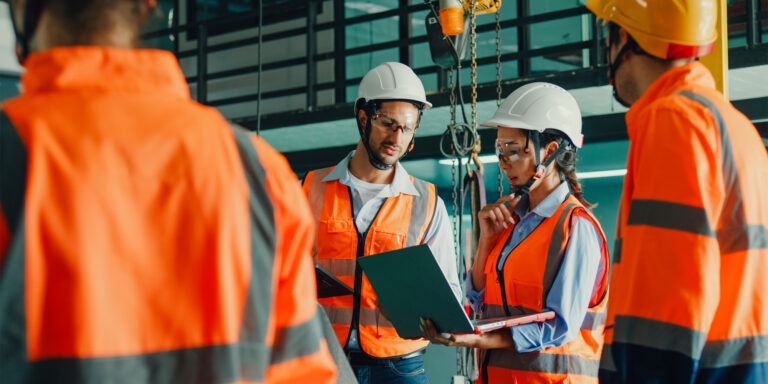
In construction, a strong safety program doesn’t just establish compliance and protect workers—it demonstrates a company’s investment in its people, improves employee morale, drives productivity, and enhances a company’s reputation.
With safety as a daily consideration in construction, training programs must adapt to the evolving demands of a company’s operations, the conditions of its jobsites and shifts in the industry. That’s why the most effective safety training programs are customized to a company’s operations and the specific needs of its workforce.
Table of contents
The State of Construction Safety Standards
OSHA, created by the Occupational Safety and Health Act of 1970, has had a considerable impact on the construction industry, shaping safety protocols and setting specific regulations aimed at protecting workers from the many hazards associated with high-risk tasks.
While OSHA standards created significant improvements in the industry, compliance with OSHA’s safety training standards isn’t a guarantee that a company will mitigate risks effectively. In fact, many construction safety leaders argue that complying with safety training regulations is just the beginning of creating a broad-reaching and effective safety training program.
4 Tips for Developing a Robust Construction Safety Training Program
At the basic level, training curriculums should meet state and federal regulations and also reflect the specific scope of work. To understand training requirements, safety professionals can review guidance from various construction safety organizations. They can also utilize tools such as the OSHA Compliance Guidance on Training and resources from organizations like CPWR - The Center for Construction Research and Training.
Going beyond the basics, here are four tips for up-leveling a construction safety training program.
1. Customize training for your organization and its work.
A customized training curriculum looks different for every organization.
Tailored training
Toolbox talks are a common tool used in safety training. However, these sessions should not be random or forced to a schedule. Toolbox talks should focus on what's applicable to what’s happening on the job site that day, or — going further — can be seamlessly integrated into the day’s schedule.
To bring toolbox talks into the day’s operations, topics can be incorporated into existing plan-of-day or kickoff meetings, where operations and safety conversations can be discussed as one connected concept.
If safety is discussed at toolbox talks or other meetings, managers should include follow-up sessions for questions and answers to reinforce the material covered.
Site-specific Onboarding
Given the transient nature of the construction workforce, onboarding should be conducted at the beginning of every project and also required when each new worker arrives. Onboarding is most effective when it is tailored to address the particular tasks and conditions workers will encounter on your jobsite such as confined spaces, hazardous materials, etc., as well as the common health and safety hazards associated with those environments.
Employer Verification
Employers should always take the time to verify on their own if each worker is competent to do the work expected. For example, let’s consider the operation of a mobile elevating work platform (MEWP). Even though standards for MEWP training are outlined by OSHA and ANSI, training on one machine doesn’t guarantee that a worker can safely operate the specific make and model on your project.
Safety managers can verify competency by performing hands-on safety checks, either by asking a qualified person to conduct a demonstration, or by reviewing the operation manual with employees.
2. Create strategies for employee relevance & engagement.
Unique to construction, the job site offers an excellent learning environment. Of course, while job sites are in full swing, time is a precious commodity, so safety professionals need to get creative with learning opportunities.
The construction jobsite can be the best classroom ever. There are so many different hands-on classrooms that we can use. While looking at the time to use for safety training, I also look around the jobsite to think about where the little classrooms are that I can pop up and use for worker education.
Abby Ferri
Senior Leader
National Safety Council
Ad-hoc sessions that happen in real-time can help make sure topics are hyper-relevant and hands-on, which enhances learning. Safety professionals can carry out practical sessions while work is actively taking place, or they can wait until tasks are winding down to initiate safety sessions and avoid work interruption. The following are some ideas for ad-hoc items that safety professionals can ask workers to do:
- Point out potential hazards in their work area
- Find and review an operator’s manual for the equipment they are using
- Locate and discuss safety sheets related to their task
- Observe competent workers demonstrating work
- Talk about how safety enhances the work they are doing
All ad-hoc sessions should be formalized with a sign-in sheet to capture documentation of safety training.
3. Embrace adult learning models.
Construction safety professionals have many responsibilities, and they are experts in a broad range of duties including risk assessments, safety inspections, reporting, and much more. Because of this, most safety professionals don’t have formal training in educational methods — in other words, they haven't studied how to teach.
However, safety professionals can take some time to learn about adult learning methods, particularly Knowles' principles. Knowles’ principles highlight the crucial role that adult learners play in their own education, advocating for self-led methods as the ideal way for adults to learn.
Knowles’ principles include methods like task-oriented learning and topic relevancy, which has already been covered in this article, but safety professionals can greatly improve the effectiveness of their training sessions by exploring all of the concepts covered in Knowles’ six principles.
4. Consider unique delivery methods.
Allowing safety managers autonomy to implement creative training solutions can transform sessions into enjoyable, memorable experiences. Some ideas include:
Guest Speakers
Safety professionals can keep things fresh by inviting guest trainers from different departments or using insurance partners' consulting hours and platforms to provide additional resources.
Gamification
This engagement tactic doesn't have to be elaborate. A simple system of rewards, such as naming the "king of ladders" among your foremen or providing hard hat stickers for safety skills uses peer pressure positively to enhance motivation.
Edutainment
Incorporating edutainment into training can also maximize impact. Microbursts of training delivered via text messages can extend the life of traditional long-form training sessions and keep safety top of mind.
Seasonal Opportunities
Celebratory occasions such as annual kickoffs in March or federally recognized focus weeks serve as a platform to refresh critical safety topics.
There are training providers out there that provide content that's more like edutainment. There are even raps about lockout tagout. I mean, people remember those details — and I'm just happy that they're singing about lockout tagout.
Abby Ferri
Senior Leader
National Safety Council
Measuring Safety Program Effectiveness
Now that we’ve covered how to create a construction safety training program, let’s explore various strategies for understanding whether concepts are being retained and applied effectively.
It is your responsibility to verify that workers actually know how to perform the tasks you are entrusting them to do. Because if something happens and you didn't check and you relied on someone else's standard of training, then that could be a problem.
Abby Ferri
Senior Leader
National Safety Council
Of course, tests are traditionally used to measure learners’ knowledge. However, this method can induce stress and may not suit everyone, especially those who have difficulty reading or who speak English as a second language.
Here are some alternatives:
- Verbal group quizzes allow for collaborative discussions and ensure comprehension without singling individuals out.
- Encouraging workers to articulate their tasks and safety procedures based on the training they received is another effective method.
- Conducting follow-up inspections after targeted training sessions can also assess whether initiatives have led to improvements.
The effectiveness of training programs can also be evaluated by patterns of behavior revealed through inspections and observations, which can be surfaced by technology platforms or safety reports. Frequent issues identified during inspections can highlight areas of opportunity.
Stay updated on what’s happening in construction.
Subscribe to Blueprint, Procore’s free construction newsletter, to get content from industry experts delivered straight to your inbox.
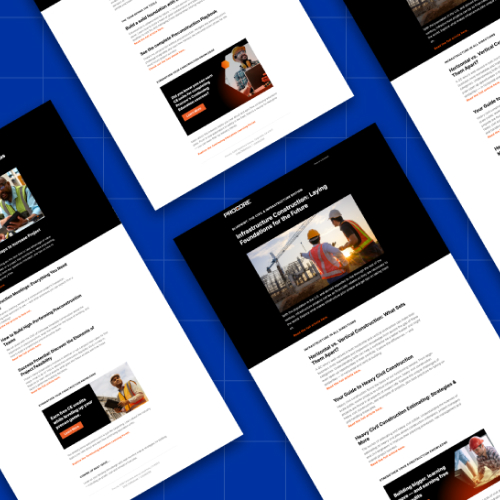
Securing Leadership & Buy-In
In company cultures where safety is championed and quality, efficiency, and safety are highly integrated, safety managers are routinely given autonomy and trust. However, some structures exist where the preference is to meet only minimum safety requirements.
In these circumstances, it is helpful to provide a clear outline of what fulfilling those minimum standards would entail, including the necessary time. Then, safety professionals can offer alternatives to maximize that time. This allows essential safety training to be integrated into the workday in ways that meet both regulatory requirements and enhance overall safety culture.
For example, employers routinely accept (and even require) safety certifications such as OSHA 10 or OSHA 30. These certifications don’t expire, but it's common for employers to ask workers to complete refresher courses.
However, because the online curriculum requires being on a computer (and away from the job site), it is not a particularly engaging method, nor is it a good use of workers’ time.
If your workers must complete OSHA 10 or OSHA 30 and must do so repeatedly for different contractors, you should review what the worker did last time and introduce variety by selecting different electives. There are many alternative training activities workers could undertake—and 10 or 30 hours is likely better spent elsewhere.
Abby Ferri
Senior Leader
National Safety Council
Developing safety training with company- and site-specific components, unique employee-engagement strategies, and creative use of time will significantly boost safety programs — helping to create a robust safety culture and making sure employees are empowered to do their jobs safely.
this is part of the series
The Construction Safety Training Playbook
Was this article helpful?
Thank you for your submission.
100%
0%
You voted that this article was . Was this a mistake? If so, change your vote here.
Scroll less, learn more about construction.
Subscribe to The Blueprint, Procore’s construction newsletter, to get content from industry experts delivered straight to your inbox.
By clicking this button, you agree to our Privacy Notice and Terms of Service.
Categories:
Tags:
Written by
Abby Ferri
Abby Ferri is an influential and award-winning expert in global risk management and worker safety with more than two decades of experience. She is a passionate advocate for advancing women in EHS leadership, ethical technology integration, and STEM education, co-founding the globally recognized "Safety Justice League" podcast and authoring two books. Abby also serves as an adjunct professor and is active in her local community, contributing to advisory groups focused on thoughtful AI strategy and equitable access to STEM careers. Her leadership and innovative approaches continue to shape the future of workplace safety and education.
View profileLindsey Salmony
Lindsey Salmony is a writer and marketing manager with a passion for finding and celebrating the human stories behind resilience and innovation. Her work has appeared in various publications including Engineering News Record, CFMA’s Building Profits Magazine, Industry Dive, AHP’s Advancing Philanthropy, and The Giving Institute’s Member Insights Blog. A native of New England, she has a proven track record of successfully navigating cars through rotaries and cracking lobsters at the dinner table. Outside of the office, she can be found alongside her husband cheering for her children in team sports and championing their growth mindsets.
View profileExplore more helpful resources
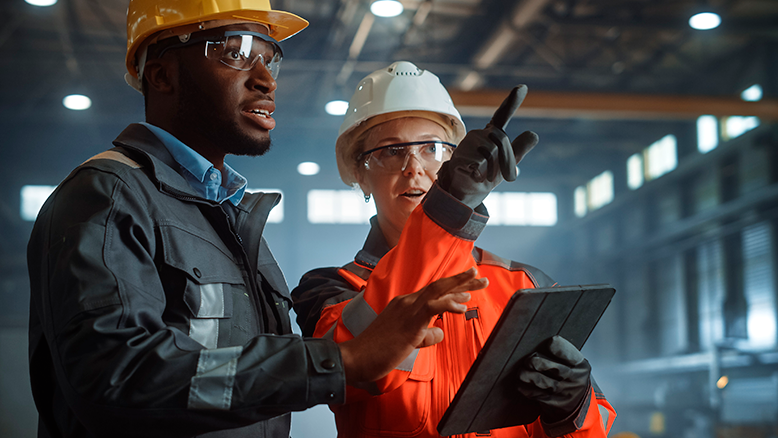
On the Safe Side: Using Data to Boost Subcontractor Safety
Capturing data to mitigate the safety risks incurred by subcontractors as well as in-house workers demands proactive risk management measures, transparent change management and methodical strategy. Applying data to safety...
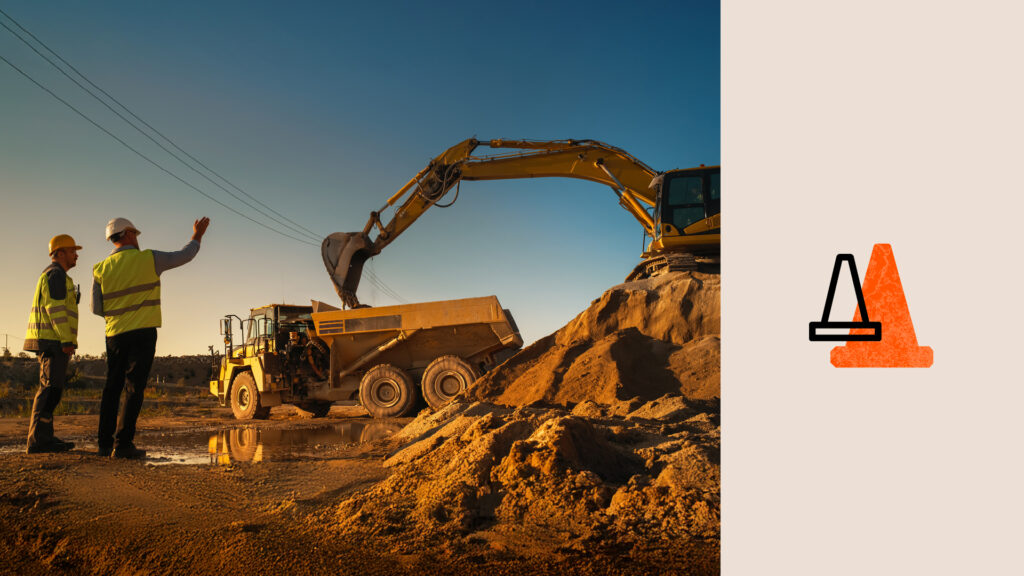
Top Techniques for Heavy Equipment Safety & Operations
Nearly 1 of every 5 workplace fatalities occurs in the construction industry. It is increasingly important to create a culture of safety and reduce the risk of workplace accidents, and...

Preconstruction Partnerships: How Safety Pros Can Collaborate with Estimating & Proposal Teams
Construction leaders and safety professionals are developing a strong understanding of how safety programs positively impact project outcomes. When safety is woven into every aspect of operations from pre-construction to...

The Strategic Partnership Between Construction Safety and HR
A construction safety manager’s role is significant: It entails broad oversight over the construction workplace to prevent incidents that could cause worker injury or property damage. In addition to this...
Free Tools
Calculators
Use our calculators to estimate the cost of construction materials for your next project.
Templates
Find a template to help you with your construction project tasks.
Material Price Tracker
Get the latest U.S. retail prices and view historical trends for common building materials.
Glossary
Explore key terms and phrases used in the industry.