— 8 min read
Building Surgical Centers: A Guide to Outpatient Surgery Projects
Last Updated Sep 9, 2024
Last Updated Sep 9, 2024

Healthcare construction is a massively varied and lucrative subsection of construction. Consistently in demand, it offers general contractors (GCs) a chance to engage in longer-term projects with substantial rewards, despite the typically tighter profit margins.
While healthcare projects include many of the same components and steps as more typical vertical commercial construction projects — such as building walls and installing floors — there are some major differences to be aware of.
In this article, we will focus mainly on ambulatory surgical centers. These facilities, predominantly used for outpatient and elective surgeries, have a lot of the same needs as full hospitals but are often built inside existing commercial and mixed-use buildings, bringing their own set of complexities.
Table of contents
Diving Into the Healthcare Construction Space
Building and renovating healthcare facilities is a specialty that requires builders to work on multiple projects to become credible in the space. A general contractor may start to push into this space if there are many new projects popping up in their area, or if other types of construction are slowing down.
A general contractor looking to enter the healthcare construction space may want to break in as a joint venture with another GC that’s more qualified. A GC can provide bandwidth support, manpower, management or fulfill other needs that the specialty contractor has.
By working with a qualified contractor with substantial healthcare experience, contractors can gain experience — and future clients will see that they’ve learned from the best. Very rarely will a newbie be able to win a healthcare contract without having worked under a more experienced contractor first.
Phases of Surgical Center Construction
Planning and Preconstruction
Collaboration amongst various stakeholders to fulfill contractual obligations must be meticulously orchestrated during the planning phase of an ambulatory or surgical center construction project.
Many agreements outline the procedures for potential shutdowns and access requirements to ensure that every action, whether shutting down utilities or gaining entry to certain areas, is carefully planned and communicated well in advance between a GC, superintendent, and the facilities team. This helps establish clear protocols for approvals and stop work authority.
Everyone should be aware of their responsibilities to uphold compliance and efficiency.
General contractors venturing into ambulatory center construction must consider the facility's past use and be aware of the importance of building in a clean and safe environment. Many surgical centers that are constructed in densely populated areas are generally built within a mixed-use complex. Contractors should assess whether the structure was previously an office, a retail space, or, conveniently, a medical facility.
Additionally, GCs need to know what machines and technology will be used in the facility. Some medical devices like MRI machines may require modifications to the building’s structure and be housed in Faraday cages to shield against electromagnetic interference. The ultimate goal here is to ensure the integrity of the future surgical suites before construction begins, in order to reduce risks like mold and structural deficiencies that may present themselves further down the line.
Procurement and Buyout
Although the procurement process can be pretty straightforward with vertical construction projects, there are unique considerations for healthcare facilities. GCs may be dealing with specialized equipment made by a small handful of companies.
For instance, when putting massive surgical lights, unistrut — square, metal tubing with holes in the side, similar to what stop signs are mounted on — is also needed to hang the lights. Very few companies make unistrut, which may put contractors on tight timelines and with budget constraints in a bind if the materials aren’t ordered at the right time.
Lead times for these materials can dramatically change the project schedule. If it takes 19 months for an MRI machine to be delivered, it should be included in the schedule. With medical facilities, procurement of medical equipment is a huge linchpin in the process of moving the project forward.
It’s equally important to select specialty contractors wisely. GCs should focus on contractors with a proven track record in medical facilities to handle specialized installations, such as medical gas plumbing.
Working with Medical Personnel
Unlike other buildings, coordinating construction within a medical facility can be a challenge, especially if the facility is still operating. When working in a medical facility that is still operating during construction, contractors need to be in lockstep with facilities managers, doctors and other staff to make sure there are no scheduling conflicts.
Conversely, a lack of coordination between the construction and medical parties could result in major fines levied against the GC, or medical complications experienced by the patients in the occupied space.
A hospital's operational needs take precedence over construction, which could mean adjustments to utility services must be scheduled around critical procedures.
Coordinated Drawings
Contractors must account for specialized equipment used for healthcare construction projects, such as oxygen, nitrogen, carbon dioxide or other medical gasses. It’s important to know if there are conflicts in the plan space that may interfere with installing certain machines. BIM modeling tools can integrate drawings and plans to ensure the plans are laid out effectively.
GCs should ensure that everything in the building is in the correct space and will fit properly in that area. Typically, a surveyor marks a series of survey points, sometimes shooting them from the street because of a historical survey mark tied into city records. The survey marks are basically the project’s key handbook — every measurement is based on those central points.
Special care needs to be taken to ensure that pipes are not getting crossed and other parts of the structure are the correct size. For example, medical gas is sometimes piped into a room using a headboard structure. The wall has to have a specific depth so that the nozzles on the medical gas headboard fit.
For example, if a wall is constructed with incorrect specifications, extender nozzles may need to be purchased to correct the error. This may mean having to purchase additional extenders for each room that needs medical gas hookups and could tack on extra costs that contractors have to incur.
Sterilization
When constructing healthcare facilities, contractors have to be mindful of sterilization requirements once they’ve reached a certain phase of completion. Throughout the space there should be dedicated sterile and non-sterile areas. Working with subcontractors who specialize in working with medical gases, and knowledgeable about navigated sterilized areas is a plus.
Additionally, GCs could benefit from working with specialized HVAC contractors to ensure certain spaces have positive or negative pressure. For example, operating rooms need positive pressure — meaning a breeze pushing air out beneath the door to prevent contaminants from entering the room. The inverse is a quarantine room, with negative pressure, that helps prevent contaminants from escaping.
Once the general construction phases are done, hiring a professional cleaning contractor to deep-clean every room in the facility may be needed to maintain sterilization requirements. Afterwards, extreme care needs to be taken not to recontaminate the building. Workers must be aware for the shift from going from wearing hard hats and other general PPE, to wearing medical booties over their shoes, wearing clean coveralls, and ensuring the space is clean before exiting.
Healthcare Construction Inspections
Navigating inspections during and after the construction of a medical facility can take a substantial amount of time. Specialized inspections are often required and vary from municipality to municipality. Contractors should plan to work with municipalities and governing bodies to schedule inspections and uphold regulations.
In New York City, for example, healthcare construction has its own set of rules — Article 28 facilities require a level of scrutiny that goes beyond a typical commercial construction build. These require being aware of, and passing, medical-specific inspections for critical systems like fire ratings and air pressure, not to mention the additional checks needed for medical gases.
There are fire rating inspections, and although a lot of commercial constructions require fire ratings, medical facilities have multiple additional layers of fire walls that need to be inspected.
Medical requirements are considered throughout the building. Positive and negative pressure is inspected. Therefore substantial time should be built in at the end of the construction to accommodate all inspections.
Closeout and Warranties
GCs must provide warranties, typically covering a one-year period for workmanship and materials. Additionally, any issues arising post-handover, such as floor tiles lifting or leaks, must be addressed promptly.
Project handover may also include training for the hospital staff on maintenance and operation procedures, securing a smooth changeover from construction to medical care.
Best Practices for GCs Constructing Ambulatory Centers
For GCs looking to break into healthcare construction, partnering with experienced contractors or engaging in joint ventures is just the beginning. Below are some tips to help successfully navigate this niche space in the industry.
- Having specialized knowledge: GCs need to possess an understanding of the specific systems unique to healthcare construction, such as medical gases and specialty designs.
- Maintaining a sterile environment: Maintaining a sterile environment during construction is a priority, including managing sterile and non-sterile areas and airflow.
- Awareness of regulatory requirements: It’s important for GCs to carefully navigate working with AHJs and maintain compliance with healthcare-specific regulations and required inspections.
- Thinking outside the box: Contractors need to be able to manage logistics and minimize disruption when working in occupied buildings, especially in situations when utilities cannot be shut off due to regular operations taking place in a medical facility.
Stay updated on what’s happening in construction.
Subscribe to Blueprint, Procore’s free construction newsletter, to get content from industry experts delivered straight to your inbox.
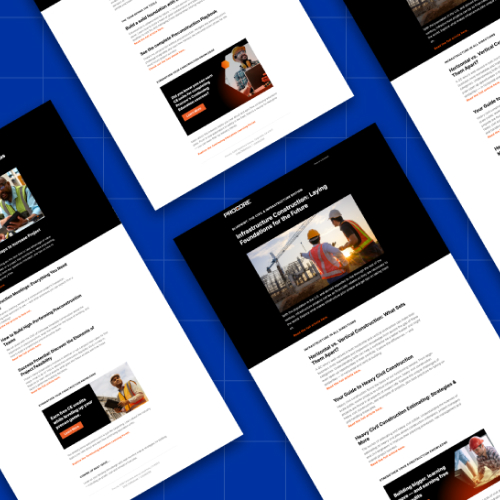
Building Healthcare from the Ground Up
Constructing an ambulatory surgical center is not for the faint of heart. It demands a high degree of precision and the ability to work under stringent regulations.
For contractors ready to partner with experienced contractors and invest in understanding the unique needs of healthcare construction, the rewards can be both professionally satisfying and financially beneficial. The key to success within this area of construction lies in meticulous planning, coordination, and execution.
Was this article helpful?
Thank you for your submission.
0%
0%
You voted that this article was . Was this a mistake? If so, change your vote here.
Scroll less, learn more about construction.
Subscribe to The Blueprint, Procore’s construction newsletter, to get content from industry experts delivered straight to your inbox.
By clicking this button, you agree to our Privacy Notice and Terms of Service.
Categories:
Tags:
Written by
Jacob Kunken
21 articles
Jake Kunken currently works as Solutions Engineer for Procore's Heavy Civil division. He brings 14 years of experience working in various construction roles in New York and Colorado, including laborer, assistant carpenter, carpenter, assistant superintendent, superintendent, construction manager, safety manager, and project manager. Jake also spent time in EHS as an environmental engineer for Skanska. He’s worked on more than 40 commercial projects from ground-up, to heavy civil, hospital work, and tenant improvement. Jake studied Ecological Technology Design at the University of Maryland.
View profileCait Bladt
12 articles
Cait Bladt is a multi-award winning freelance writer and producer. Her work has appeared at Vice, ABC News and Rolling Stone among others. She currently lives in Brooklyn with her cat Patricia.
View profileExplore more helpful resources
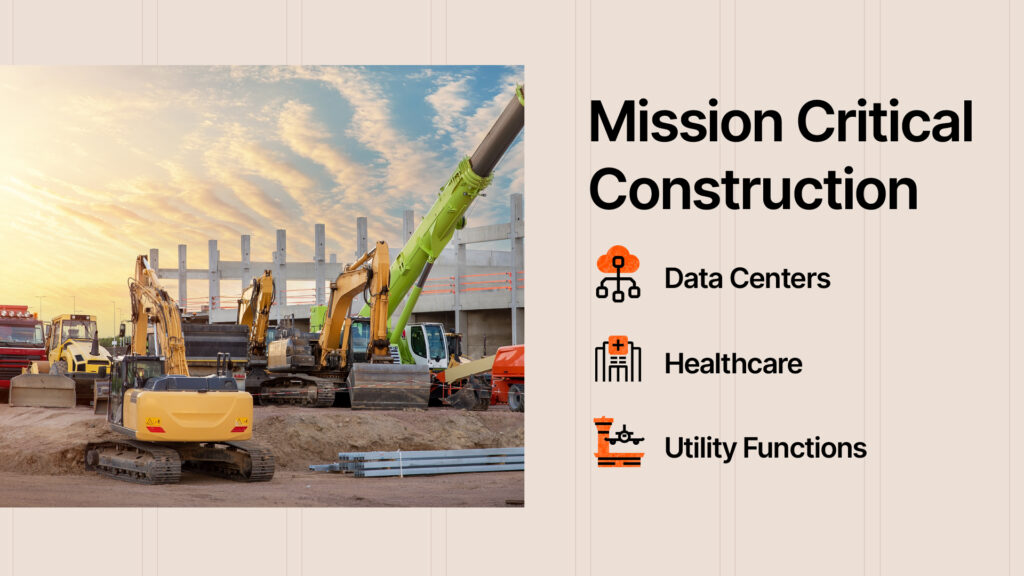
Mission Critical Construction: Strategies for Success
Mission critical construction involves building structures whose functions cannot afford to fail, as any disruptions can lead to significant consequences for society. Keeping data centers, hospitals, power plants and other...
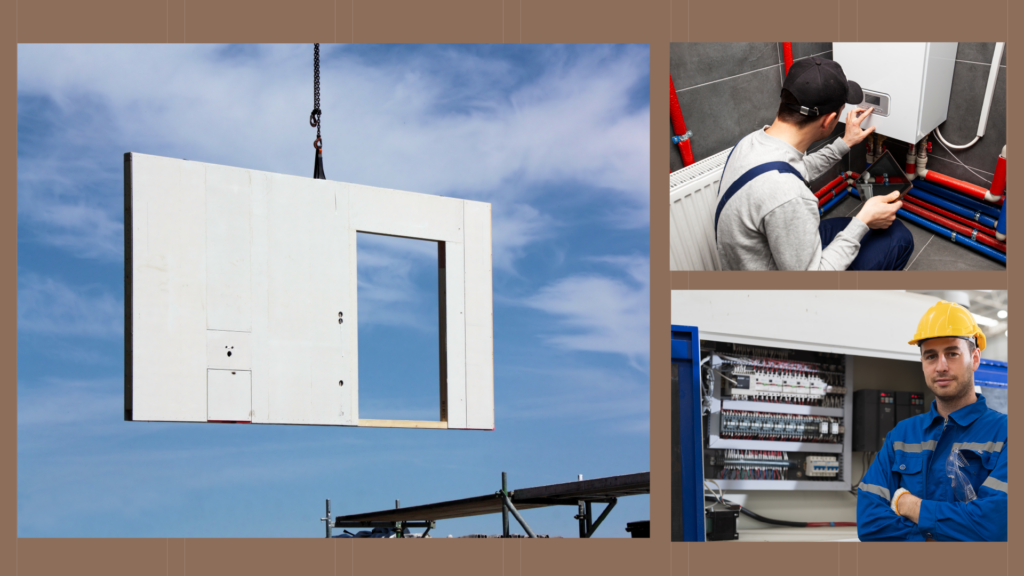
Modular Construction and MEP: A Collaborative Pairing
In an age of supply chain disruptions, workforce shortages, and rising material costs, off-site construction — including modular construction methods and prefabricated materials — is surfacing as a multipurpose solution....
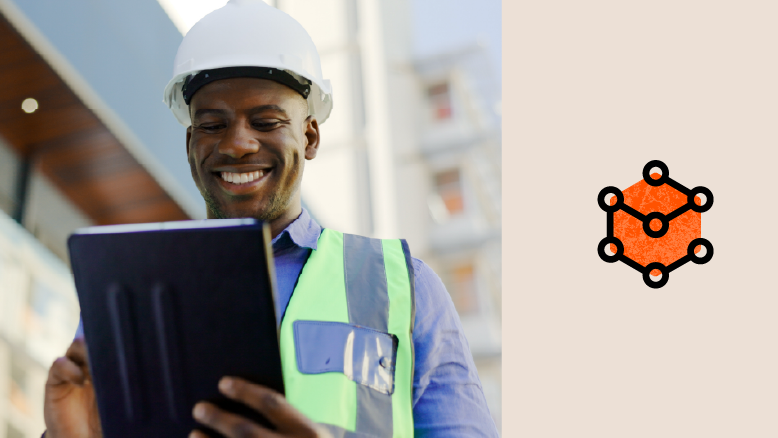
Connected Construction: Transforming the Industry Through Integration
Construction projects are becoming increasingly complex, so companies need to innovate to accurately and profitably complete these modern structures. Connected construction — using technology and data to improve communication, processes...
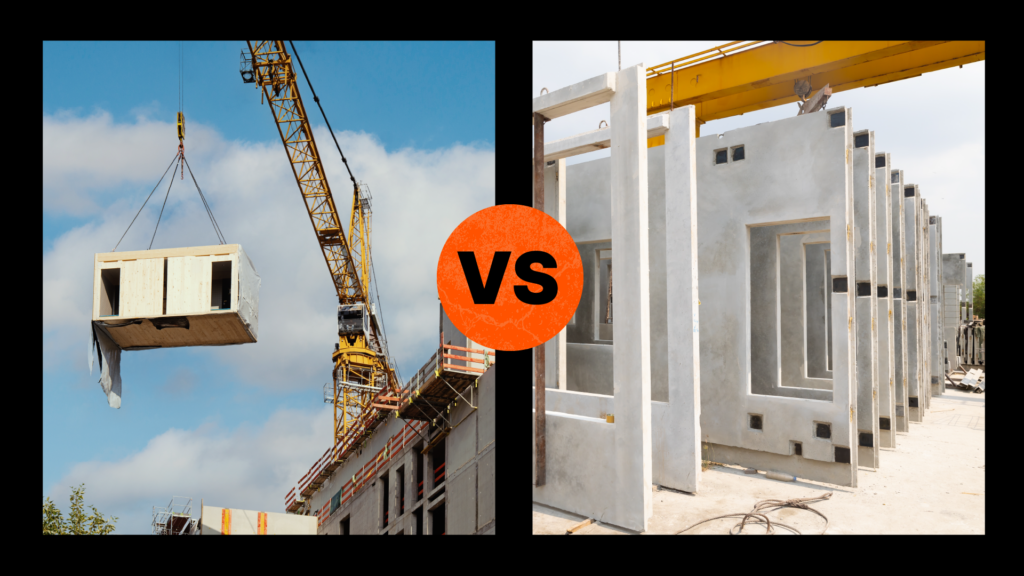
Off-Site Construction: Prefab vs. Modular
As the construction world becomes ever more competitive, deadlines get tighter and the margin for error gets slimmer, project owners around the world are always looking for an edge. Thanks...