— 10 min read
Hospital Construction: A Guide to Design & Construction of Healthcare Facilities
Last Updated Mar 21, 2025
Last Updated Mar 21, 2025
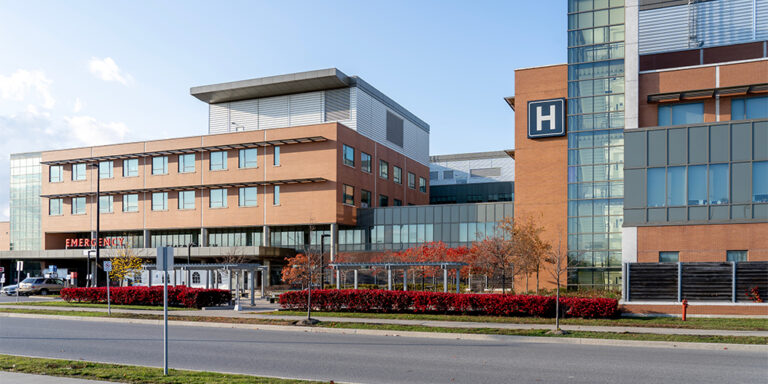
Building a hospital is one of the most societally necessary projects a General Contractor (GC) could take on — but they’re also sprawling, complex campuses with some highly engineered components.
Hospital construction can have similar challenges to building surgical centers, though hospital work is often performed at a greater scale.
This article explores the unique aspects of hospital construction, including its basics and key considerations, the special challenges of working within a healthcare system, and best practices for smoothly transitioning to the handover phase.
Table of contents
Unique Challenges of Hospital Construction
Undertaking a hospital construction project involves unique challenges that set it apart from other types of construction, with necessary consideration for patient safety and infection control.
Equipment can be highly specialized — MRI machines, CT scanners and X-ray machines all need to be accounted for in designs and installed properly to function after handover. Some lab equipment may need specific electrical configurations or cooling systems to operate.
One of the most distinctive elements of hospital construction is the installation of medical gas (often abbreviated as simply "med gas") pipes, which can make the design of structural elements like electrical, plumbing, and HVAC more intricate. Med gas installation also often requires specialty med gas contractors.
Another particular complication of hospital construction is establishing negative pressure — an essential measure to prevent the spread of contaminants. Negative pressure rooms contain harmful particles by making sure that air flows into the room rather than out, using sealed HVAC systems to maintain the correct pressure levels. This is especially necessary in operating rooms and isolation units, where maintaining a sterile environment can mean the difference between life and death for patients.
Finally, hospitals are ever-expanding as populations grow, and it's often necessary to perform construction work inside a busy, 24-hour workplace for doctors, nurses and staff. When working in a still-functioning facility, walk-off mats and airtight barriers can help prevent the spread of dust and chemical fumes, maintaining the safety of the surrounding space.
Key Steps of Hospital Construction
From securing a bid to closeout, hospital construction requires significant expertise and precise coordination. The following lists some of the challenges a GC can expect to navigate while working in a healthcare facility.
Planning and Design
In the initial phase of hospital construction, multiple design documents, including architectural, engineering, and equipment specifications, need to be coordinated—making the use of construction software integral to project success.
Working with an experienced design team is a necessity for hospital construction. Because these buildings have to adequately house medical gas infrastructure and the mechanical, electrical and plumbing, general contractors should invite specialty trade contractors into early planning meetings to mitigate clashes in the plenary space as much as possible.
Designers experienced in hospital construction know that wall and ceiling space in these facilities is prime real estate, and it can be difficult to fit all the necessary components inside. Making use of interstitial spaces between the floor and ceiling can free up some of this space, and make it easier to perform maintenance on these critical systems down the road.
Tiny details matter in hospital construction, even from the start. When surveying land, it’s critical to accurately verify the existing conditions of the site to avoid costly errors. Advanced technology, like ground-penetrating radar, can help to map out the site with precision.
Verifying as-built drawings is also important, as working with incorrect documentation can lead to delays and financial overruns if not addressed early on.
Always double-check the as-built drawings. In one of our projects, we faced a situation where the line on the as-built drawing wasn't actually there. I drove a 360-degree camera in there to see the actual condition and found out it was missing. That cost us $200,000.
Taking full advantage of your camera and radar technology can help ensure that you have precise information before you begin construction, ultimately saving time and money by preventing costly errors and delays.
Dirk Schoenmaker
Project Manager
Halse-Martin Construction
Preconstruction
Hiring a workforce that has already performed hospital construction can be helpful, but crewmembers who demonstrate good teamwork are particularly necessary, especially if the hospital is going to continue operating alongside the build.
Med gas contractors must be skilled and certified to perform the work. In addition, all contractors and subcontractors need to undergo training in infection control in order to understand the risks and know how to mitigate them.
Finally, one of the most important parts of pre-construction is to open lines of communication with the hospital staff, including charge nurses, who are the heads-of-staff for their departments and shifts in the hospital.
Since these staff members may be performing lifesaving work at the same time as the project, this line of communication is as important for moving forward as keeping in regular contact with crew members, foreman, owners and reps.
Construction
During the actual build, effective planning and logistics management are necessary to keep the workspace tidy and safe—and to build momentum that will push the project to completion.
With limited available space, deliveries of materials should be just-in-time. Depending on the design plans, some areas of the hospital may be right for modular construction—and having entire sections of the structure arrive prefabricated and ready-to-be-assembled can both speed up the process and help prevent infection.
Infection control should remain a top priority throughout the construction phase. The GC will need to oversee the setup of negative pressure rooms, use of sealed HVAC systems, and implementation of specialized containment measures—and then continuously monitor these measures to make sure they’re working.
Closeout and Handover
In addition to the regular series of inspections from Authorities Having Jurisdictions (AHJs) required on any construction project, hospitals must comply with stringent healthcare regulations, and pass infection control inspections administered by the Centers for Disease Control (CDC). The GC will need to work these appointments into the project’s busy timeline, and make sure their infection control measures are up to code.
Documentation and training will be extensive, given the large amount of equipment and intricate electrical and structural needs of the facility, but community outreach is likely to be less intensive than more intrusive types of construction.
Learn more: The Construction Closeout Process Explained
Best Practices for Hospital Construction
Building a hospital is a formidable task, but adhering to a few best practices can lead to the project's on-time success and help create a facility that will serve its community for decades to come.
Build strong relationships.
Construction is an industry of people — but in the case of hospitals, investing in relationships beyond simply the crewmembers and subcontractors is key to getting the job done.
Holding regular coordination meetings with hospital administrators, department heads, and charge nurses can help ensure that everyone is on the same page—but it can also be a proactive approach to reduce the risk of tensions between crew members and the staff working in the same building.
Fostering a collaborative environment where hospital staff feel heard and valued is an important part of building the culture of communication that’s necessary to project success.
And when unexpected issues or changes arise, having established relationships allows for swift and effective responses, reducing the risk of delays.
On one hospital project, we had to do some loud drilling near a nursery. By coordinating with the charge nurses, we were able to schedule the work during a time when it would least impact the babies and their parents.
They appreciated being kept in the loop, and it helped us avoid a lot of potential complaints and disruptions. On the flip side, if charge nurses feel that construction work is negatively impacting patient care, they have the authority to stop it.
Matt Strumeyer
Solutions Engineer
Procore
Use digital tools for maximum visibility.
Digital tools provide construction teams the ability to see a finished project before ground is ever broken. Using Building Information Modeling (BIM) software and digital twins can be useful for visualizing these large, complex buildings. They also give design teams a chance to problem-solve early before running into an issue during the actual build.
Learn more: 9 Ways BIM Improves Healthcare Construction
Construction software can make new sets of plans easy to access and distribute to the entire project team.They also give design teams a chance to problem-solve early before running into an issue during the actual build. Construction software can make new sets of plans easy to access and distribute to the entire project team.
Beyond the benefits during construction itself, an investment in A digital twin provides long-term value to the owner after the project is delivered, reducing the cost of maintenance
Future-proof the building designs.
Foresight should be implemented at every possible level, since hospitals also grow over time, and are built to last. As best they can, the design team should implement future-proofing into their work, leaving room for technological upgrades and expansions—especially in electrical and IT rooms, where innovation in hardware is likely to advance most quickly.
Separate ventilation systems and interstitial space are two of the most important focus areas for future-proofing a healthcare facility. Controlling airflow during addition or renovation can be a challenge. Ventilating construction zones within an active unit or from the basement can require long runs to exterior walls. In a high-rise facility, windows may need to be removed. In some cases, the construction crew may need to core an exhaust port through concrete and weatherproof it after the job is done. Designing with the future in mind would include dedicated ports allowing for negative air extraction.
Interstitial spaces between floors — where the critical system infrastructure runs — should be as tall as possible. In addition, the ductwork, pipes, conduit, etc., should be installed at the top of the space for easier access and future system expansion. When designed appropriately, work can be performed in the interstice without the need for costly and time-consuming infection control measures.
Although future-proofing can add construction costs to the project, they can often lead to a lower lifecycle cost for the owner.
Stay updated on what’s happening in construction.
Subscribe to Blueprint, Procore’s free construction newsletter, to get content from industry experts delivered straight to your inbox.
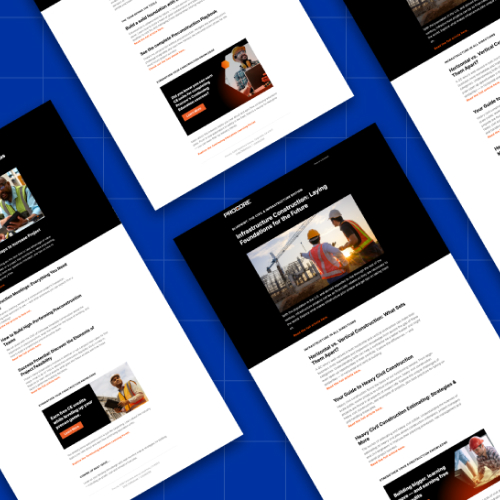
Go above and beyond with safety.
Hospitals are spaces of care — places for people to heal and receive essential, life-saving treatment. When it comes to safety, the bare minimum of healthcare regulations and infection control may not be enough to create a caretaking environment.
For example:
- Before installing the required systems of infection control, temporary barriers may be needed before walls go up to stop pathogens and harmful substances from drifting out of the work zone.
- HVAC ducting needs to be sealed on both ends prior to delivery to ensure contaminants are not introduced into the air system.
- Construction dust must be tightly controlled to ensure it never reaches patient, even if you vent outside, it could still find its way to patients through open windows or air intakes close by
- Vibration from heavy machinery can cause interference with sensitive equipment, like medical imaging machines. Timing of the work needs to be coordinated properly.
In addition, controlling infection in an active healthcare facility also requires staff and crew members to stay informed. It is important to communicate regularly with facility employees and install clear signage about the status of infection control methods.
Maintaining a safety culture may mean more than numbers and control measures—fostering dialogue about how crewmembers and medical staff feel about the facility’s safety, for example, can make sure that safety remains top of mind for everyone onsite.
Serving Communities with Hospital Construction
Successfully constructing a hospital requires more than just technical expertise — it demands a commitment to collaboration, meticulous coordination and uncompromising safety.
By building strong relationships with hospital staff, leveraging advanced software and prioritizing rigorous infection control measures, GCs can navigate the complexities of these hospital projects — and, more rewardingly, leave a lasting positive impact on the communities they serve.
Was this article helpful?
Thank you for your submission.
100%
0%
You voted that this article was . Was this a mistake? If so, change your vote here.
Scroll less, learn more about construction.
Subscribe to The Blueprint, Procore’s construction newsletter, to get content from industry experts delivered straight to your inbox.
By clicking this button, you agree to our Privacy Notice and Terms of Service.
Categories:
Tags:
Written by
Dirk Schoenmaker
Dirk Schoenmaker is a Project Manager at Halse-Martin Construction, a Vancouver-based general contractor and construction management firm. He has over 14 years of global experience managing healthcare, heavy timber, and large-scale commercial fit-outs in the US, Canada, Saudia Arabia, Germany, Denmark and the Netherlands. He holds a Bachelor of Science in Construction Management from Bauhaus-Universität Weimar.
View profileMatt Strumeyer
Matt Strumeyer is a Solutions Engineer at Procore. Previously, he worked as a Project Manager for general contractors and real estate developers in the Austin, TX area. He holds a Bachelor's degree in Civil Engineering from The University of Texas at Austin.
View profileTrey Strange
26 articles
Trey Strange is a Peabody and Emmy-Award winning writer and producer based in Brooklyn, NY. Throughout his career, Trey has worked for the Huffington Post, Houston Chronicle, Out Magazine, Brooklyn Eagle, CNBC, INTO, and New York Magazine's Bedford + Bowery. He received his Masters in Journalism and Middle East studies from New York University, and Bachelors in the same subjects from the University of Houston.
View profileExplore more helpful resources
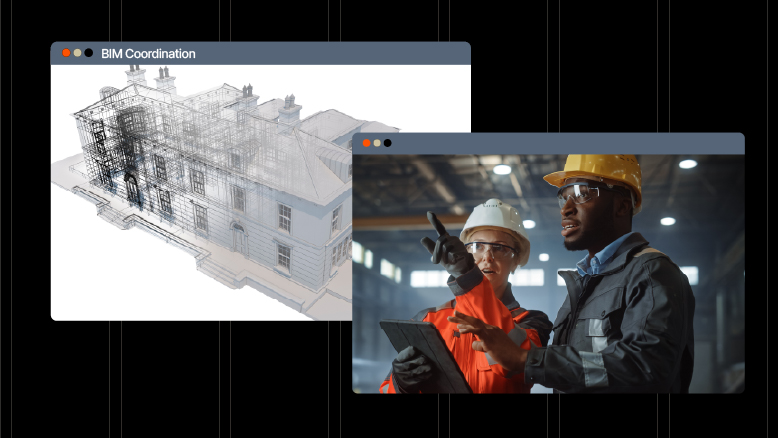
Streamlining Construction Projects with Effective BIM Coordination
The old saying goes: if you fail to plan, you plan to fail. Construction professionals know this better than nearly anyone. To take a project from a vision in an owner’s...
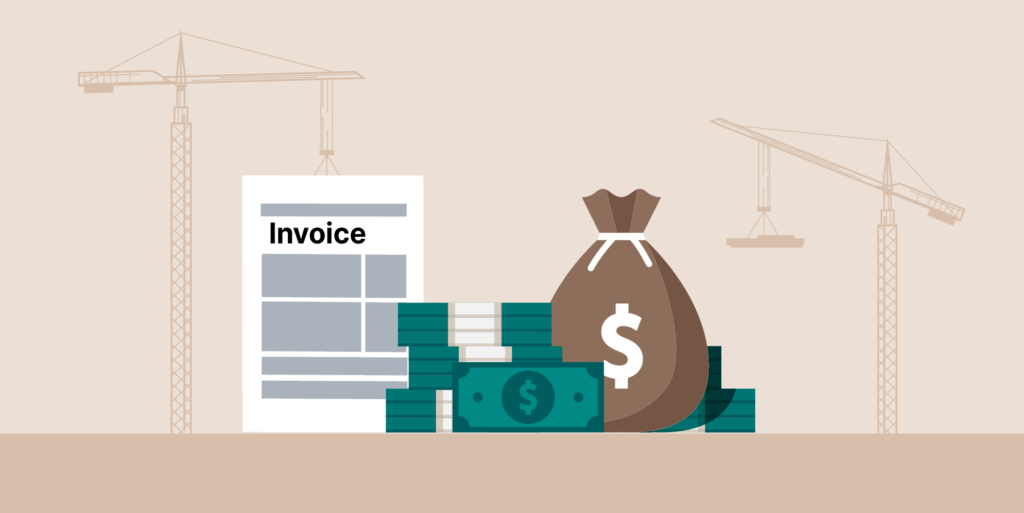
Construction Invoice Factoring: A Quick Guide
Construction companies need to maintain consistent cash flow. Projects can take years to complete, and delays and unforeseen events may keep expenses mounting. Adding to this load are typically high upfront...
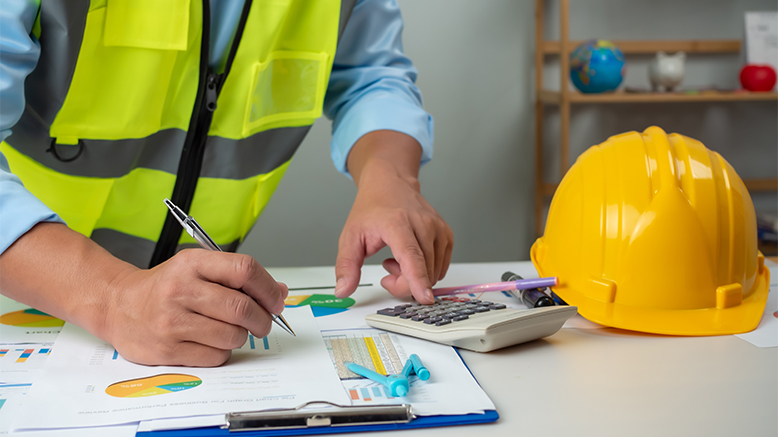
Understanding Subcontractor Bid Packages in Construction
Construction bid packages can have a cascading impact on the success of a construction project. The quality of a bid project may affect the quality of the bids, which in...
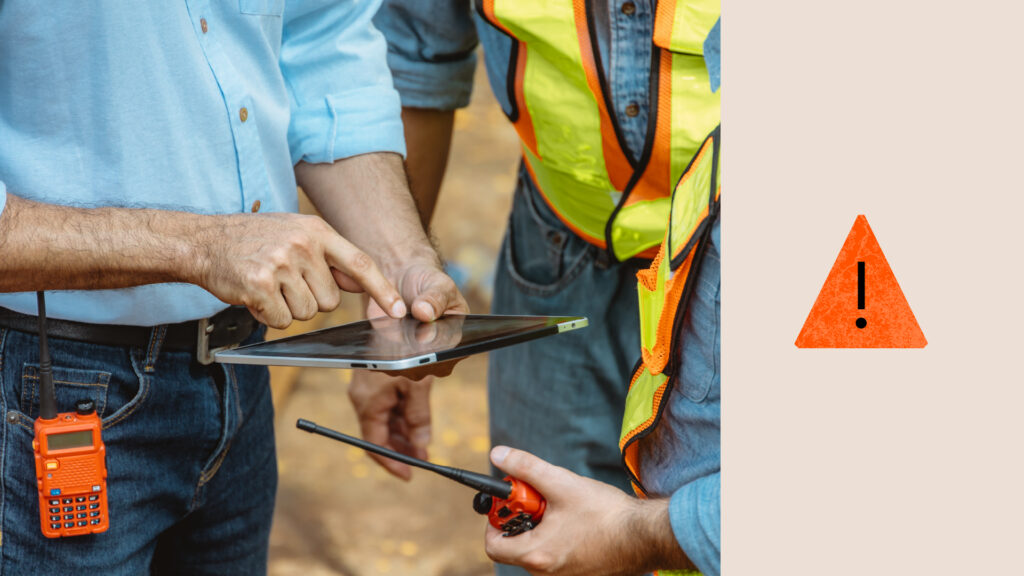
Tackling the Top 10 Construction Industry Issues
The construction industry is constantly evolving, bringing both opportunities and challenges. Companies must navigate an array of construction industry issues — from workforce shortages to integrating new technologies into their...