— 10 min read
Job Costing in Construction: A Blueprint for Tracking Project Costs
Last Updated Jun 17, 2024
Last Updated Jun 17, 2024

Job costing is the process of tracking costs and allocating them to their associated project. Without recording and analyzing all expenses related to a project, construction companies cannot comprehend the financial health of their projects. By tracking and categorizing all costs on a job, job costing allows contractors to improve the accuracy of their estimates, create more competitive bids, and become more profitable.
In this article, we explore job costing, including the benefits of using this system to track construction costs as well as best practices used in the industry.
Table of contents
What is job costing?
Job costing is a common process in construction accounting in which costs are assigned to individual construction projects, breaking down the expenses to understand where every dollar is spent. This systematic approach allows for early detection of any deviations from the budget, facilitating prompt corrective action to keep project costs within the established cost parameters.
Beyond merely tracking expenses, job costing is instrumental in assessing each project's financial performance: It ensures that projects stay within budget and offers insights into their profitability. Job costing allows construction firms to make informed decisions about pricing, bidding and allocating resources. Additionally, job costing aids in identifying opportunities for cost savings and efficiency improvements, making it a vital tool for the overall financial health and operational success of construction firms.
How to Break Down & Track Job Costs
To begin job costing, the estimator creates a cost breakdown for each project. The scope of work is broken down into categories or activities required by the project. Though different types of projects require specific breakdown structures, the process for breaking down expenses remains the same.
1. Identify costs.
The first step in job costing is the identification of costs associated with a construction project. These primarily include:
- Direct costs: Costs directly tied to project work, such as materials, labor, and equipment.
- Indirect costs: Costs not directly linked to a specific project task but necessary for supporting the project, like site security, utilities and administrative expenses.
2. Allocate costs.
Once the various costs are meticulously identified, they are strategically allocated to the respective construction projects on which they occurred. The allocation involves distributing direct, indirect, and overhead costs to the respective construction projects, each requiring a distinct approach.
Direct Costs
Direct costs are the most straightforward to allocate as they are directly associated with specific projects. These include expenses like materials, labor wages, and equipment used exclusively for a particular project. Since these costs are clearly linked to a specific project, allocating them is a matter of precise accounting of expenditures incurred during the construction process.
Indirect Costs
Indirect costs are not always tied to a single construction task, but they still need to be allocated to projects. These include costs like site security, transportation of materials, and administrative support. Indirect costs are usually allocated based on their direct relationship or proportional use in each project. For instance, the cost of transporting materials can be divided among projects based on the quantity of materials used in each one.
Overhead Costs
The most challenging aspect of cost allocation is handling overhead costs. Overhead costs are the general business expenses that are essential for running the construction company but are not directly attributable to any single project. This includes costs like office rent, insurance, executive salaries, and marketing expenses.
Unlike direct and indirect costs, overhead costs are not incurred for the sake of a specific project, so their allocation requires a more considered approach. Companies will often spread these costs across projects using a systematic formula. This could be based on the proportion of direct labor hours, direct costs, or machine hours each project consumes.
For example, if a project accounts for 15% of the company's total direct costs, it might be allocated 15% of the overhead costs. This method ensures that each project contributes fairly to the company's overhead, reflecting a more accurate picture of the project's true cost and profitability.
3. Monitor job cost reports.
Job costing in construction is not static. It is dynamic and ongoing, requiring continuous monitoring and reporting throughout the lifecycle of a project. This oversight ensures that the project stays aligned with its budget and meets its financial goals.
As the project progresses, costs can fluctuate due to various factors such as changes in material prices, labor rates, and unforeseen challenges. Continuous monitoring allows project managers to understand these changes in real-time, ensuring that the financial picture of the project is current and accurate.
The Benefits of Job Costing
Job costing provides clarity and precision, offering a variety of benefits that are essential for successful construction project management and overall company financial sustainability.
Granular Tracking of Expenses
Job costing provides a granular view of where every dollar is spent in a construction project. By dissecting costs into specific categories — such as labor, materials and equipment — and further breaking them down into more detailed segments like concrete, flooring, electrical work, and plumbing, job costing enables project managers to track expenses with remarkable precision. This detailed tracking helps identify areas where costs are higher than anticipated, allowing for timely interventions to control spending.
Budget Management
One of the primary benefits of job costing is its ability to help construction firms manage and adhere to project budgets. By comparing actual expenses against budgeted amounts continuously, project managers can ensure that the project remains financially on track. This real-time budget monitoring is critical in an industry where even small financial missteps can have significant impacts on profitability.
Cash Flow Optimization
Effective job costing practices allow for better cash flow management in construction. Through the detailed financial insights gained from each project, construction firms are empowered to make informed decisions about resource allocation, payment schedules and mobilization costs of new projects.
This in-depth understanding is enhanced by the use of cash flow projection reports, which are a byproduct of meticulous job costing. These reports provide a forward-looking view of the cash inflows and outflows over the course of a project, allowing firms to anticipate financial needs, plan for upcoming expenditures, and avoid potential cash shortages. By integrating these projections into their financial planning, construction companies can optimize their cash flow, ensuring not only the health of individual projects but also the overall financial stability of the firm.
Data-Driven Estimating
Job costing provides valuable historical data that can be used to enhance the accuracy of future cost estimates. By analyzing past projects, construction firms can identify trends in cost overruns or savings, which can then be factored into new estimates and bids. This data-driven approach to estimating helps in creating more competitive and realistic project proposals.
Dig deeper: The Ultimate Guide to Estimating in Construction
Risk Mitigation
Accurate project estimations, enabled by job costing, play a crucial role in mitigating financial risks. By anticipating potential cost issues before they occur, firms can proactively plan for contingencies. This foresight helps in avoiding unexpected financial pitfalls during the project execution phase.
Client Trust & Satisfaction
When project estimates are accurate, clients are less likely to encounter surprises related to costs. This accuracy builds trust and satisfaction, as clients appreciate transparency and adherence to the budget. In the long run, this enhances the reputation of the construction firm and leads to more business opportunities and repeat work.
Best Practices in Construction Job Costing
These job costing best practices help ensure accuracy, enhance efficiency and maintain budget control throughout the project lifecycle.
Establish a robust cost code system.
A robust cost code system, typically based on the industry-standard MasterFormat, provides the structure for organizing and categorizing project costs. By creating a framework to break down costs, construction firms simplify the process of tracking and reporting expenses, making the management of financial data more efficient and insightful. Consistency in the cost coding ensures clarity and efficiency across different projects and among various stakeholders. This uniformity allows for a comprehensive view of financial health, not just at the project level but also at the firm level, providing a holistic perspective on the organization's financial standing
Balance the level of detail.
Striking the right balance in the level of detail tracked is key for effective job costing. While detailed categorization provides more precise data, excessively granular data can become cumbersome to manage and time consuming to track. The goal is to capture enough detail to inform decision-making without overburdening personnel and the entire system.
Include indirect costs.
Indirect costs, though not directly tied to specific project tasks, impact project profitability. Accurately accounting for these costs ensures a complete and honest financial assessment of the project. It's important to review and include these costs in job costing analyses on a regular basis.
Allocate overhead and executive time to projects.
Recognizing and accurately tracking the time spent by executive and overhead staff on projects is crucial. Often overlooked, these costs can eat away at a project’ profit. Implementing a system for logging the time spent by executives and administrative staff on specific projects allows these overhead costs to be appropriately billed back to the job. Factoring these into the project transparently and accurately ensures a more realistic representation of the project's overall cost.
Use software systems and tools.
Using advanced software systems streamlines the job costing process through automation, greater accuracy and real-time data access. These systems offer functionalities like integrated accounting, project management, and reporting tools, significantly enhancing the efficiency of job cost tracking.
Stay updated on what’s happening in construction.
Subscribe to Blueprint, Procore’s free construction newsletter, to get content from industry experts delivered straight to your inbox.
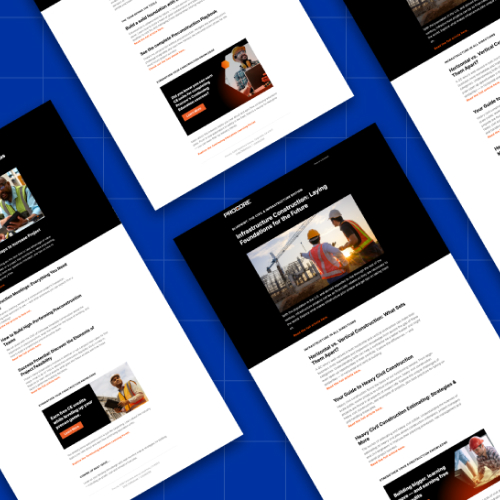
Establish and consistently implement change order tracking systems.
Creating and a system for monitoring change orders — and deciding whether these orders will be tracked under the original job codes or assigned new codes — is important. A robust system is fundamental in managing adjustments to project scale and expenses. In addition to project management, it is key to legal and financial record-keeping, especially when resolving disputes or clarifications
Understand the budget.
It is essential for individuals tasked with coding costs to projects to possess a comprehensive understanding of the project budget and its cost breakdown. This understanding helps to avoid misallocations and to ensure that expenses are precisely categorized accordingly. Additionally, project managers should review all invoices for timely approval. Without their approval, there's a risk of accumulating costs that do not align with the designated budget areas. This vigilance in invoice approval and cost coding alignment plays a key role in maintaining the integrity and accuracy of the overall project budget.
Align expenses with revenue in accrual accounting.
In accrual accounting, it's important to match expenses with the corresponding revenue in the correct time period. This is more than an accounting formality: It ensures financial statements genuinely mirror the project's economic activity. Accurate reflection of expenses and revenues in their respective periods is vital for a true-to-life financial portrayal, facilitating more effective financial planning and in-depth analysis. It enables firms to make informed decisions based on the actual financial performance of each project, rather than estimates or projections, thus fostering a more strategic approach to managing project finances
The True Power of Job Costing
The true power of job costing lies in its ability to track actual expenses incurred during the project and compare them against the initial estimate. This comparison is not just a retrospective look at spending; it's a critical evaluation of financial performance and profitability. By analyzing how the real-world job costs stack up against the estimator’s predictions, construction firms can gauge the success of their financial planning and execution. In essence, job costing does more than just account for expenses – it provides invaluable insights into the financial health of each project, guiding firms towards more profitable practices.
Was this article helpful?
Thank you for your submission.
88%
13%
You voted that this article was . Was this a mistake? If so, change your vote here.
Scroll less, learn more about construction.
Subscribe to The Blueprint, Procore’s construction newsletter, to get content from industry experts delivered straight to your inbox.
By clicking this button, you agree to our Privacy Notice and Terms of Service.
Categories:
Tags:
Written by
Teresa Buturusis
Teresa is a Senior Strategic Product Consultant at Procore. She has almost 20 years of experience in construction finance, working for large general contractors like Alberici Constructors. Teresa has an MBA from University of Illinois Urbana-Champaign.
View profileTaylor Riso
73 articles
Taylor Riso is a marketing professional with more than 10 years of experience in the construction industry. Skilled in content development and marketing strategies, she leverages her diverse experience to help professionals in the built environment. She currently resides in Portland, Oregon.
View profileExplore more helpful resources
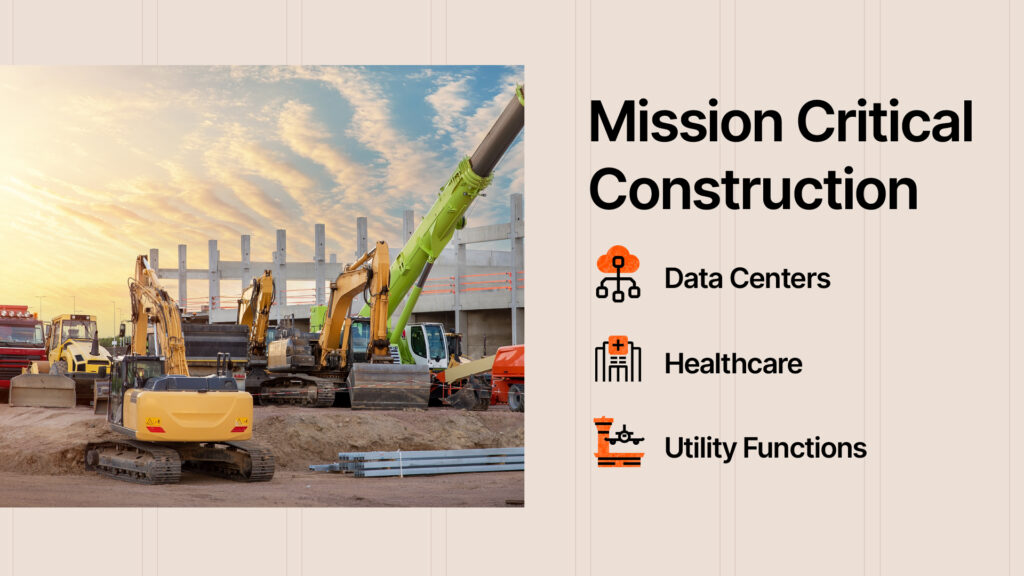
Mission Critical Construction: Strategies for Success
Mission critical construction involves building structures whose functions cannot afford to fail, as any disruptions can lead to significant consequences for society. Keeping data centers, hospitals, power plants and other...
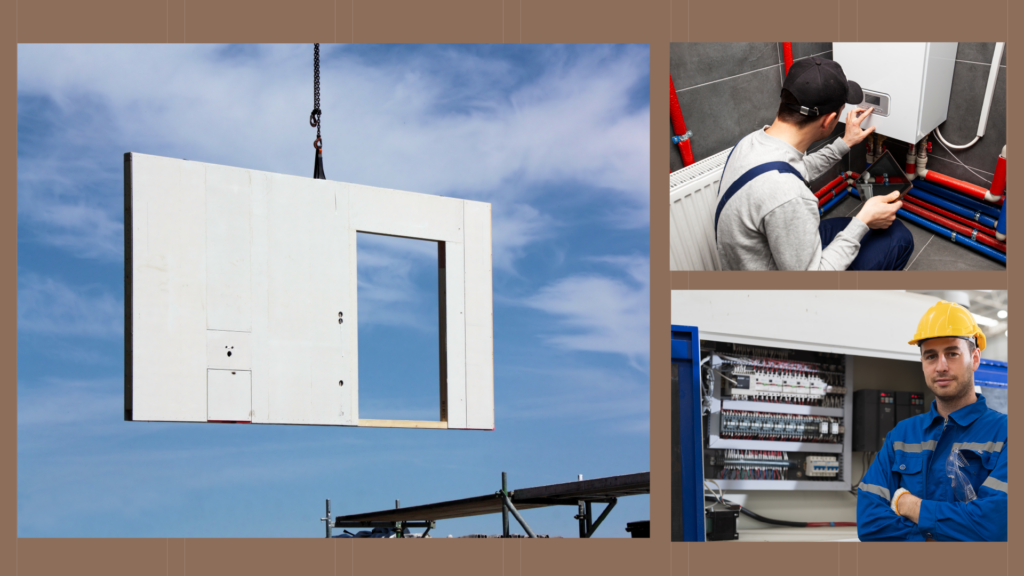
Modular Construction and MEP: A Collaborative Pairing
In an age of supply chain disruptions, workforce shortages, and rising material costs, off-site construction — including modular construction methods and prefabricated materials — is surfacing as a multipurpose solution....
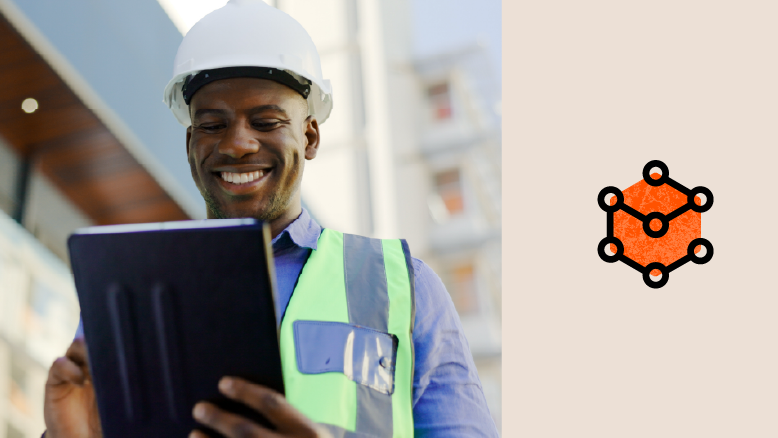
Connected Construction: Transforming the Industry Through Integration
Construction projects are becoming increasingly complex, so companies need to innovate to accurately and profitably complete these modern structures. Connected construction — using technology and data to improve communication, processes...
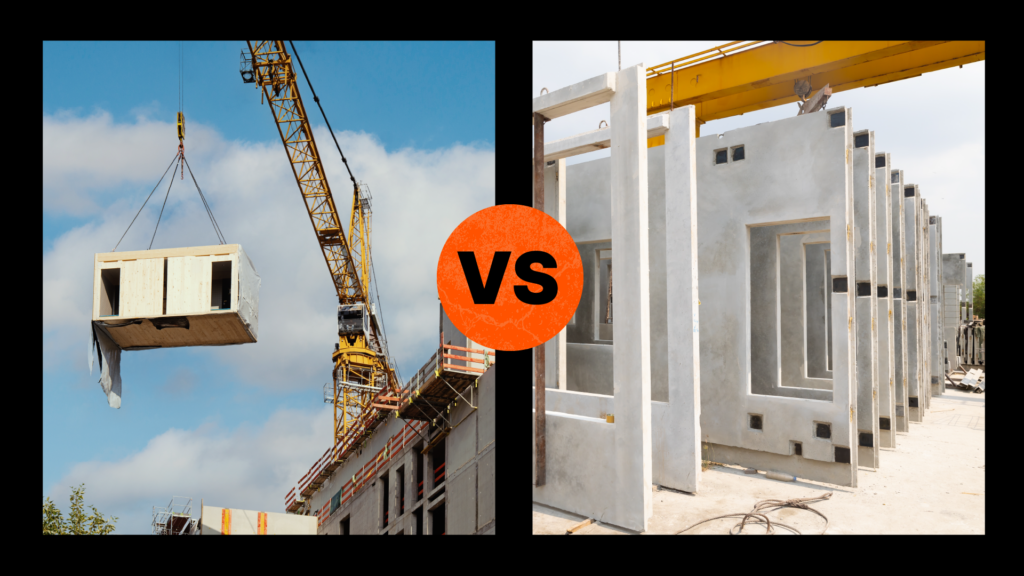
Off-Site Construction: Prefab vs. Modular
As the construction world becomes ever more competitive, deadlines get tighter and the margin for error gets slimmer, project owners around the world are always looking for an edge. Thanks...