— 5 min read
Performing a Job Safety Analysis (JSA) in Construction
Last Updated Sep 1, 2024
Last Updated Sep 1, 2024
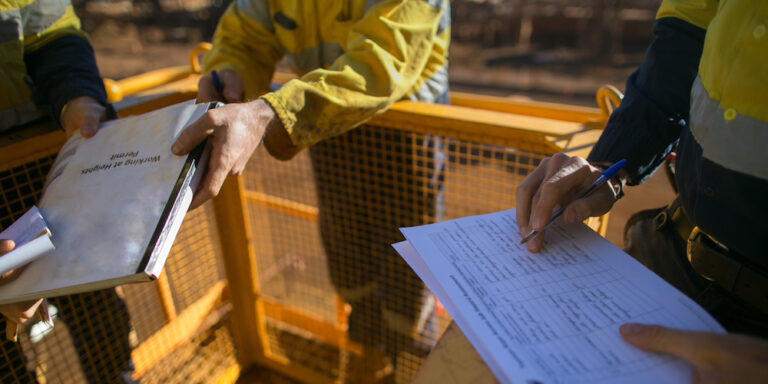
On the jobsite, safety is a contractor’s number one priority. In order to keep workers safe, contractors must first identify potential hazards, then determine how to control or prevent them. A job safety analysis, also called a JSA, enables contractors to identify potentially hazardous tasks and provide controls to mitigate or eliminate those hazards.
Table of contents
What is a job safety analysis (JSA)?
A job safety analysis (JSA) — or job hazard analysis (JHA) — is a procedure for identifying and documenting safety hazards before they occur, and recommending control measures to prevent them. The analysis focuses on the workers performing the task, the task itself, the tools used, and the environment to improve safety. If the JSA reveals uncontrolled hazards, the team must take steps to eliminate them or reduce their impact. This is done through control measures.
A JSA should be completed for any hazardous task on a construction project. And since construction work is fluid and the tasks change as the work progresses, JSAs are required more frequently. The general contractor should work with each of their subcontractors to analyze potentially hazardous tasks before they come on the job, and as their work progresses.
Note that a JSA is different than a construction safety report — which are routine safety inspections that identify specific safety violations that are already happening. These can take place on anywhere from a daily to monthly basis.
Learn more: How to Write a Construction Safety Report
The benefits of JSAs in construction
A job safety analysis helps contractors mitigate the risk of loss or injury on a construction jobsite. Almost every job on a site comes with some risk, and analyzing those risks allows project teams to proactively address those risks before they come up. Injuries and illnesses can cause lost time and reduced productivity, which can delay projects and increase costs.
They also increase safety awareness and improve communication among project team members. They encourage teamwork, as supervisors, safety coordinators, and on-site teams work together to develop the controls necessary to keep workers safe.
By addressing potential hazards, JSAs can also enable contractors to avoid penalties and fines. OSHA can inspections can happen at any time, and penalties and fines for noncompliance can be expensive -- up to $14,502 per violation.
Because safety incidents and injuries can increase workers' compensation insurance premiums, any prevention measure contractors take to reduce By improving safety on the job site, JSAs also reduce workers' compensation insurance premiums, saving contractors money and increasing profits.
Courses about construction.
For construction.
Unlock your career potential with our free educational courses on Health & Safety, Data in Construction, and more.
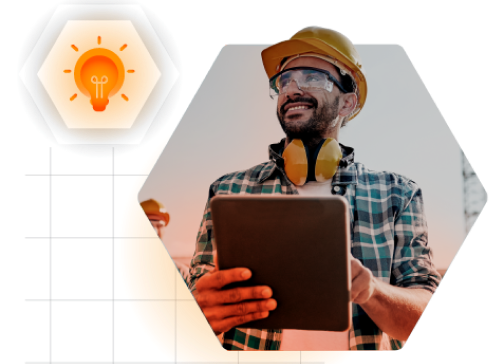
Identifying & documenting hazards
The goal of performing a job safety analysis is to discover the following:
- What can go wrong?
- What are the consequences?
- How could it arise?
- What are other contributing factors?
- How likely is it that the hazard will occur?
Document the answers to these questions as you analyze each job task.
Good hazard descriptions include:
- Where it is happening (environment)
- Who or what it is happening to (exposure)
- What precipitates the hazard (trigger)
- The outcome that would occur should it happen (consequence)
- Any other contributing factors
Go beyond OSHA regulations.
The Procore Safety Qualified program provides construction professionals with everything they need to know to create a culture of safety.
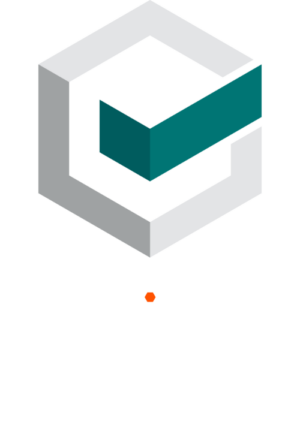
How to complete a job safety analysis
General contractor and subcontractor teams typically work together to develop and complete JSA forms. Supervisors and on-site workers have different assignments when it comes to completing a JSA.
Supervisors work to identify the tasks with potential risks. These are usually the most complicated tasks or ones that have caused accidents or near misses previously. They also watch, review, and document the specific steps needed to complete a task.
Looking at the overall task and the steps required, they then identify potential hazards and recommend control measures to mitigate those hazards. Looking at lists like OSHA’s top violations in construction can help supervisors identify hazards that need to be addressed.
On-site workers that perform a task provide supervisors with the list of steps to complete the task and perform it in front of the supervisors to help them identify potential hazards. Supervisors rely on employees to help them determine the potential hazards and the best way to control them without interfering with the work.
1. Identify the task
The first step to completing a job safety analysis is to identify a specific task that exposes workers to potential hazards. A task consists of several steps that a worker takes to complete it.
2. List the steps necessary to complete the task
Supervisors work with employees who perform the task on a regular basis to detail the steps needed to complete it. Supervisors may want to photograph or video employees performing the task so they can use it to analyze the task steps.
Learn more: Ways to Improve Construction Site Safety
3. Identify potential hazards
For each step in the task, supervisors and workers identify potential obvious and hidden hazards. Hazards may come from the worker’s behavior, the tools being used, the environment where the task is performed, or the task itself. Keeping in mind the most common job hazards can help teams identify potential problems.
4. Determine the proper preventative measures
Once the potential hazards have been identified, supervisors and workers should work together to determine the proper preventative measures that will keep workers safe. Control measures generally fall into three categories:
- Engineering controls seek to reduce the effects of the hazard by physically altering the workspace or tools to improve safety
- Administrative controls reduce a worker’s exposure to a hazard by reducing the time they spend on the task
- Personal protective equipment (PPE) acts as a last resort to protect workers when engineering or administrative controls are not enough
5. Review regularly and adjust as needed
JSAs should be reviewed regularly to determine if any changes need to be made to the list of potential hazards or controls. Any adjustments should be made as quickly as possible to keep workers safe.
this is part of the series
Construction Safety Basics
Was this article helpful?
Thank you for your submission.
89%
11%
You voted that this article was . Was this a mistake? If so, change your vote here.
Scroll less, learn more about construction.
Subscribe to The Blueprint, Procore’s construction newsletter, to get content from industry experts delivered straight to your inbox.
By clicking this button, you agree to our Privacy Notice and Terms of Service.
Categories:
Tags:
Written by
Dawn Killough
34 articles
Dawn Killough is a writer with over 20 years of experience in construction, having worked as a staff accountant, green building advisor, project assistant, and contract administrator. She holds a BA in Psychology and MS in Conflict Resolution, both from the University of Portland. She shares fundamental green building strategies and techniques in her book, Green Building Design 101. Dawn lives in Portland, Oregon.
View profileExplore more helpful resources

The Strategic Partnership Between Construction Safety and HR
A construction safety manager’s role is significant: It entails broad oversight over the construction workplace to prevent incidents that could cause worker injury or property damage. In addition to this...
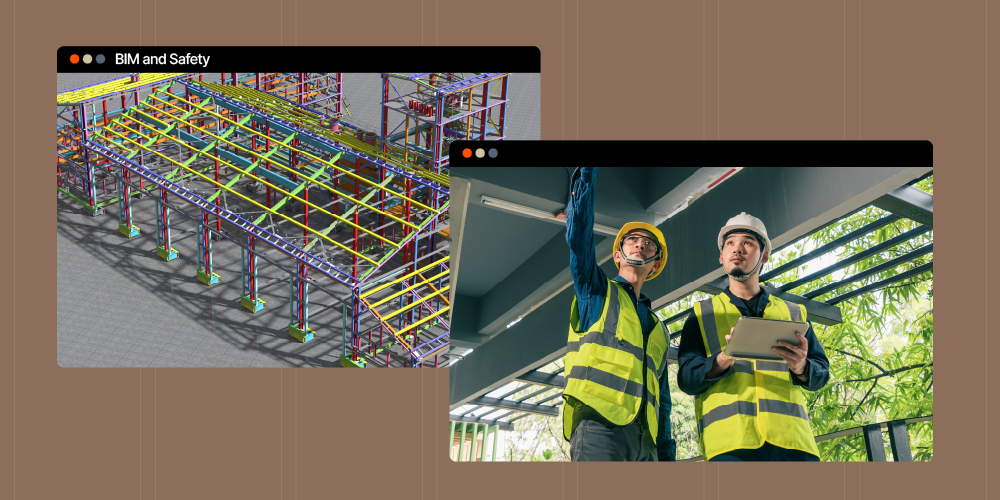
Enhancing Construction Safety with BIM Technologies
The construction industry is no stranger to tools: Even ancient civilizations developed mallets and axes to make their work easier. Today’s latest tools look different, but they can be as instrumental...
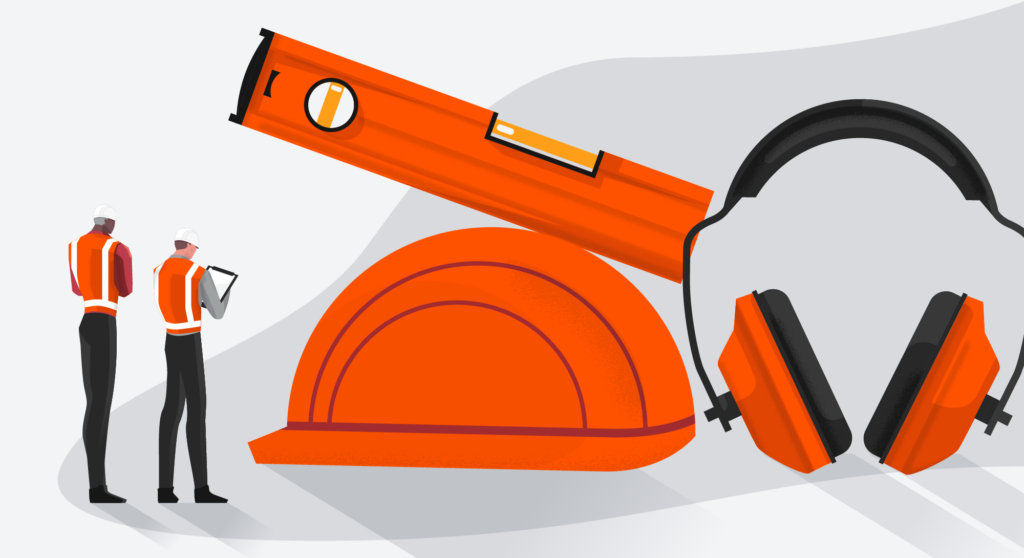
Construction Safety Training – Goals, Benefits & Emerging Trends
Construction safety training (CST) educates workers about the risks they face on construction sites and teaches them how to prevent accidents, injuries and fatalities. The construction industry has the highest...
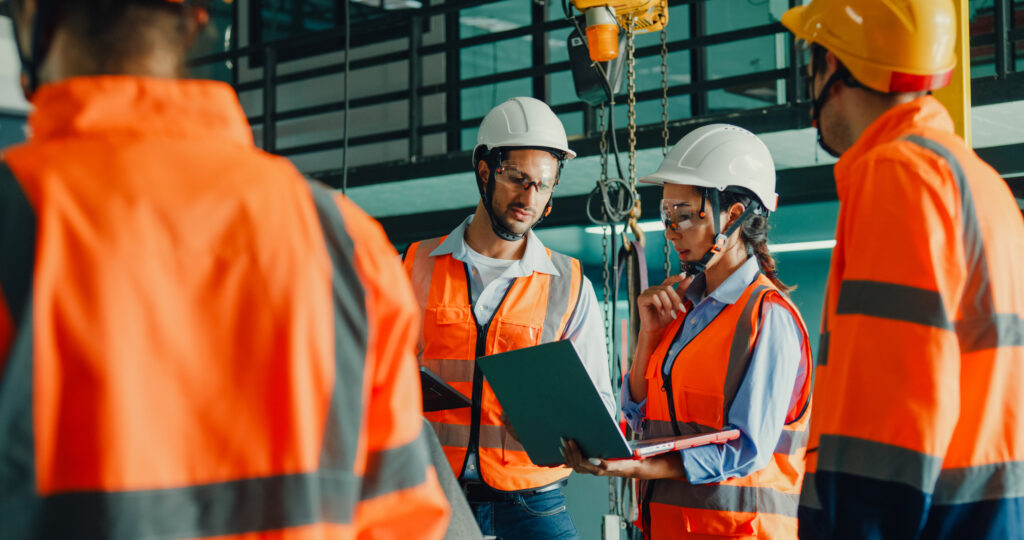
Technology for Construction Safety: Strategies to Supercharge and Scale Safety Practices
The construction industry is no stranger to the arrival of new technology, and builders are realizing its many benefits. Modernization across the industry is helping contractors streamline operations, enhance efficiency,...