— 11 min read
Lean Construction: Principles, Implementation & Benefits
Last Updated Feb 25, 2025
Last Updated Feb 25, 2025
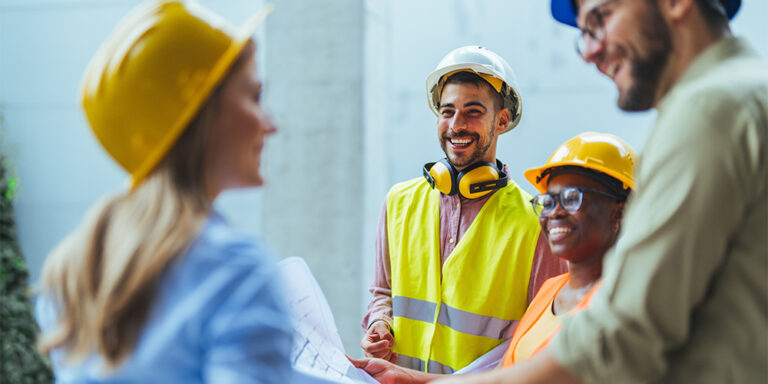
Lean construction is a project delivery method emphasizing collaboration and maximizing stakeholder value while minimizing waste. Taking ideas from manufacturing, lean construction offers the entire project team a framework to continuously learn and implement new ways to collaborate and deliver superior end products within an achievable timeframe. Intra-team relationships are a core part of lean construction, and adopting lean processes can shift the perspective away from adversarial relationships and towards a more integrated functional project team.
This article explores the core principles of lean construction, benefits, implementation strategies, some common challenges and the future outlook of lean.
Table of contents
Understanding Lean Construction Principles
Based on the Toyota Production System, lean construction aims to make work easier for workers while also eliminating waste and improving work practices. Learning about the principles underpinning lean construction can help companies decide whether or when to shift toward this system.
Lean construction focuses on six core principles:
- Value Generation
- Flow Efficiency
- Waste Reduction
- Continuous Improvement
- Respect for People
- Optimize the Whole
1. Value Generation
At a high level, value generation is about delivering a high-quality product or structure that meets the client's needs and lasts a long time. Beyond just delivering to specifications, lean construction strives to uncover meaning in projects so stakeholders can work together toward a common goal.
For example, building a children’s cancer center is about more than putting up walls; it is about providing a healing space to treat vulnerable members of society.
2. Flow Efficiency
Bringing structure to construction processes allows teams to break down big, seemingly insurmountable tasks into smaller, manageable pieces over time. There are numerous ways to improve workflow with effective collaborative techniques.
A core component in lean construction is making everything transparent and visual so it's easy to understand the flow of the project. For instance, collaborative scheduling frameworks such as Last Planner System, Takt, and Scrum allow all workers to identify and tackle constraints or roadblocks together, rather than leaving individuals to figure it out alone.
3. Waste Reduction
The idea behind the waste reduction principle is to connect the design vision with the practical know-how of the trade contractors to limit waste. A significant source of waste is rework, such as installing a wall and then realizing it’s at the wrong dimension. Another common example of excess work is punch lists, and many lean projects adopt a “zero punch” goal or mindset. Rework leads to additional costs and effort to correct the mistake. Earlier collaboration can help reduce rework.
Some waste reduction practices are straightforward, yet can be challenging to implement. Ensuring “nothing hits the ground” entails using carts to move materials, or planning for just-in-time deliveries. Buying all the drywall for an entire floor at once leads to storage issues. Only ordering supplies as they will be needed reduces material waste, but involves accurate planning to ensure teams have what they need to do work when scheduled.
4. Continuous Improvement
Viewing issues as opportunities for improvement and taking the time to review and shift processes regularly can be a positive aspect of collaboration. Showing trust and respect for colleagues by discussing problems openly leverages each team member’s expertise. Lean construction often involves integrated project delivery contracts where everyone is part of one team, which can make identifying and resolving problems less threatening or confrontational.
5. Respect for People
Respect for people means trusting the knowledge and skills that everyone brings to the table. Shifting the perspective from blame to ensuring managers provide the right information, time, supplies, and support that teams need to perform their work creates a culture that values individuals. Respectful teamwork and collaboration underpin all the principles of lean construction.
Respect for people is number one. You can't do any of the elements of lean if you don't trust the other person and respect the knowledge they bring to the table. That's where a lot of folks need training to unlearn habits and assumptions about job roles and hierarchy. People need to spend the time to understand the guiding principles and get on board with them.
Dave Brown
Senior Strategic Product Consultant, General Contractors
Procore
6. Optimize the Whole
Sometimes, project team members can get "tunnel vision" and focus exclusively on their own work. This Lean Construction principle encourages workers to shift their mindset around a project and focus on how they're contributing to the success of the project as a whole, rather than just accomplishing their specific tasks. This creates a setting where the final successful outcome of the project is what drives decisions, as well as an environment of transparency, communication and open-mindedness.
Benefits of Lean Construction
When everything on a lean construction project operates optimally, stakeholder value is maximized and waste is minimized, as set out in lean's goals. But even beyond tangible value, lean construction may lead to a more satisfying and positive process for owners, managers, and workers. The principal advantages of lean include the following.
Efficiency and Cost Savings
Implementing lean construction principles and techniques can lead to significant efficiency and cost savings. Reducing material waste and worker time means lower costs while still delivering a quality project on schedule. For a company implementing lean for the first time, there will be costs, but the end results include productivity gains, reduced rework and waste, and smoother working relationships. Everyone makes money and finishes on time without excessive stress.
Quality and Safety
Lean construction also improves project quality and safety. Clear communication and stakeholder involvement in planning result in a better-quality product sooner and for less money. Onsite safety is enhanced when superintendents and project managers consult teams about their needs and provide the time, materials, and conditions that will allow for clean and safe work practices.
Explore data and trends for building materials prices.
Get the latest U.S. retail prices and view historical trends for common building materials.
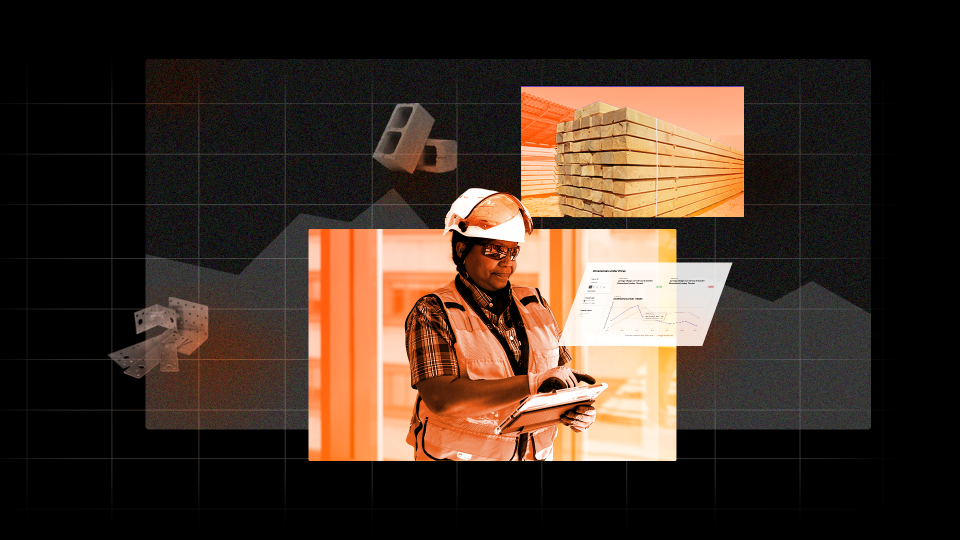
Getting Started with Lean Construction
Implementing lean construction involves a series of steps and a commitment to fundamental changes in mindset and practices. Starting with lean construction requires a cultural shift, training and adopting new tools and techniques.
Involve trade partners early.
When teams are able to provide input in the early stages of the project, they become invested in– and part of– the plan rather than feeling like a plan is being pushed on them.
Whether it’s with design, or coordinating specialty trades such as mechanical, engineering and plumbing, subcontractors and specialty trades can help GCs anticipate project needs, reduce errors and rework, and create more accurate schedules.
Train and build trust amongst project teams.
Building trust is essential for the successful implementation of lean construction. Training both admin and field teams is necessary to help them unlearn old habits and adopt new dynamics that lean construction may require for certain job roles.
On traditional construction projects, teams generally have a more narrowed focus for project tasks. With lean construction, however, project managers and superintendents may have to work more closely and meet regularly to plan the schedule with input from more project stakeholders.
If team members are hesitant to change or more collaborative approaches, it might be helpful to hire a third-party facilitator to help create buy-in for new processes.
Pro Tip
It’s important to note that traditional critical path method (CPM) schedules are typically not considered a lean technique. When adopting lean, teams can continue to use CPM schedules as a means to identify milestones or conceptual schedules which are then used to inform other methods.
Introduce lean practices in segments.
Lean approaches construction from a different perspective. There's no one way to do lean; it involves a cultural shift and adopting practices that work best for the team. Lean can be used with design-bid-build or design-build project delivery methods, but integrated project delivery (IPD) can allow contractors and owners to realize the full potential of lean.
Lean building methods are increasingly popular in construction, but because construction projects have long timelines, not all companies who want to implement lean have fully adopted it. Many GCs incorporate some elements of lean construction, which can shift workflows and result in financial, quality and collaboration benefits, even while not fully transforming operations.
Prioritize opportunities for collaboration.
Lean construction utilizes various tools and techniques to enhance efficiency and collaboration. Structured events such as daily huddles and weekly meetings keeps information current and allow for modest continuous improvements.
Pro Tip
A good structure for a daily 15-minute onsite huddle is to have everyone go around the room and say what they completed the day before, what they're working on for the day, and what they're stuck on. This keeps meeting time short and focused.
Retrospectives are more formal events that happen after a significant scope of work is completed. This gives teams opportunities to come together and provide feedback on what worked and what didn’t.
Additionally, posting schedules and look-aheads on a wall or board on-site ensures everyone is on the same page. The more eyes on the plan — with mechanisms for feedback — the better the plan will be.
Use lean techniques on pilot projects.
Implementing lean on a pilot project is a way for companies to begin using the process. In the pilot project, the cultural shift and new practices start from the first meeting, and all participants can learn new habits and workflows together.
The pilot project can help demonstrate the benefits of lean construction so the company can consider adopting it in future projects. By embracing a mindset of continuous improvement, teams can take what they learned worked well on pilot projects and apply them on subsequent projects, but avoid repetition of things that didn’t work as expected.
Measuring Success in Lean Construction
Success in lean construction can be measured using specific key performance indicators (KPI). The easiest ways to measure success are to see if projects finish on time or ahead of schedule, stay on or under budget, maintain low incident rates, and avoid punch lists.
Structured feedback mechanisms help support continuous improvement goals. Regularly scheduled meetings with clear agendas allow teams to check in and adjust plans to maximize efficiency.
Retrospectives scheduled at the completion of project segments should focus on learning from each phase and improving for the next. Respectful communication in meetings fosters openness, which is vital for both measuring success and continuous improvement.
Overcoming Lean Construction Challenges
Changing from the long-established ways of performing construction work to a lean mindset is a significant shift for most companies, but creative problem-solving and financial benefits can make the effort worthwhile.
Establish trust among the project team.
Adopting lean construction involves shifting traditional mindsets. Building trust, especially when implementing new technology or processes can sometimes be the hardest part. Leveraging outside facilitators can help start the conversation and build trust.
Get stakeholders on board.
Gaining buy-in from all stakeholders — including trade contractors and design teams — is easier when all participants are involved earlier in the process. General contractors need to rethink their position in the project team and focus on removing roadblocks for trade partners.
Getting everyone to buy into the process often starts with lunch. When we were in trouble on a project and needed to go into recovery mode, we put up a big board and invited stakeholders to take a couple of hours and tackle the problems together. Lunch was on us.
Dave Brown
Senior Strategic Product Consultant, General Contractors
Procore
Plan ahead for upfront costs.
Contractors may see front-loaded costs for training, hiring consultants and resource needs when implementing lean construction for the first time, but downstream, they can realize significant cost savings. Being aware of and planning for the initial costs ahead of time can save contractors for unexpected frustration or unaccounted for losses when starting this new process.
Role of Technology in Lean Construction
Technology can significantly impact lean construction by enhancing collaboration and efficiency. There are many use cases for digital tools and automation. Scheduling and task planning tools encourage project teams to work together and have real-time updates on any project changes. Documenting progress is easier with 360-degree photos and digital software that recognizes and stores what’s in the pictures to validate quality and completion.
Communication is central to lean construction, and software management platforms can help track and keep information flowing and visible across teams. Having access to project docs, internal and external communications and updates mitigates information silos. Video conferencing is a valuable support for geographically dispersed team members to make help keep the project going while personnel is offsite.
Future of Lean Construction
Lean construction continues to evolve with emerging trends in the industry, and it’s slowly working its way onto more projects. Emerging trends that work well with lean include the rise in modular construction and the increased use of prefabrication practices.
At its essence, lean construction is all about early stakeholder involvement, visibility and collaboration. As more owners and contractors see the value of lean, the construction industry's culture and practices can shift toward increased project efficiency.
Was this article helpful?
Thank you for your submission.
100%
0%
You voted that this article was . Was this a mistake? If so, change your vote here.
Scroll less, learn more about construction.
Subscribe to The Blueprint, Procore’s construction newsletter, to get content from industry experts delivered straight to your inbox.
By clicking this button, you agree to our Privacy Notice and Terms of Service.
Categories:
Tags:
Written by
Dave Brown
Dave is a Senior Strategic Product Consultant for Procore, specializing in General Contractors. Previously, he worked for Consigli Construction Co in Boston and Washington, DC as a Project Engineer and Assistant Project Manager, responsible for a variety of activities including bidding and procurement, contracts, and cost control. Dave holds a Bachelor's Degree in Structural Civil Engineering from Bucknell University.
View profileJulia Tell
43 articles
Julia Tell is a freelance writer covering education, construction, healthcare, and digital transformation. She holds a Ph.D. in Media & Communications and has written for publications including Business Insider, GoodRx, and EdSurge, as well as nonprofits, international businesses, and educational institutions.
View profileExplore more helpful resources
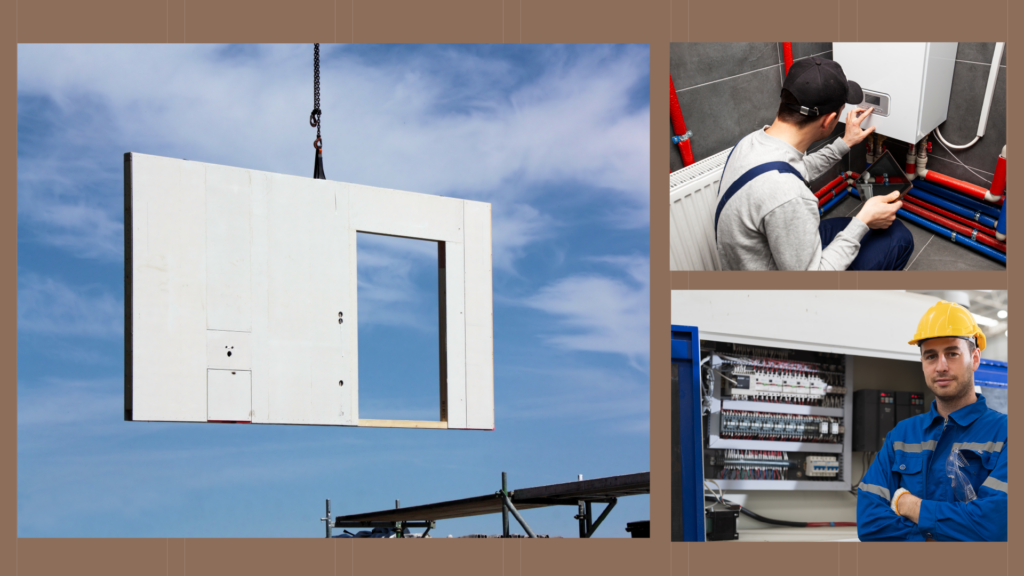
Modular Construction and MEP: A Collaborative Pairing
In an age of supply chain disruptions, workforce shortages, and rising material costs, off-site construction — including modular construction methods and prefabricated materials — is surfacing as a multipurpose solution....
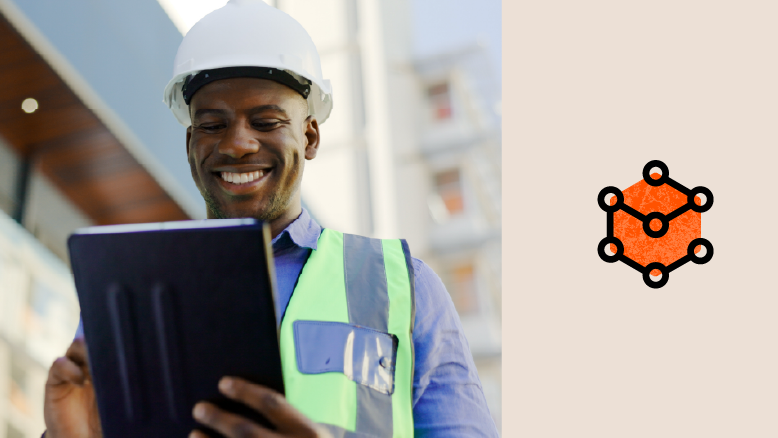
Connected Construction: Transforming the Industry Through Integration
Construction projects are becoming increasingly complex, so companies need to innovate to accurately and profitably complete these modern structures. Connected construction — using technology and data to improve communication, processes...
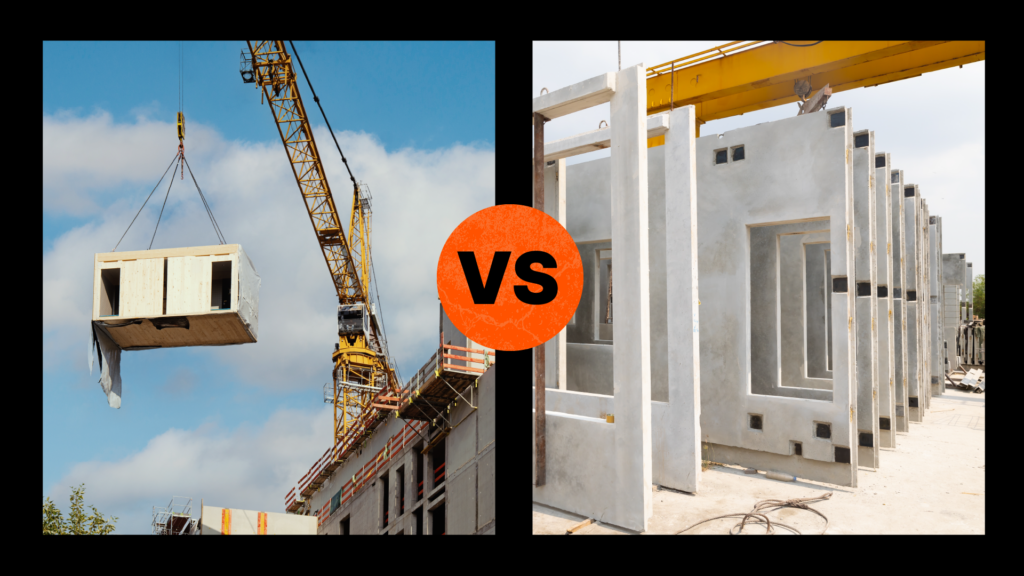
Off-Site Construction: Prefab vs. Modular
As the construction world becomes ever more competitive, deadlines get tighter and the margin for error gets slimmer, project owners around the world are always looking for an edge. Thanks...
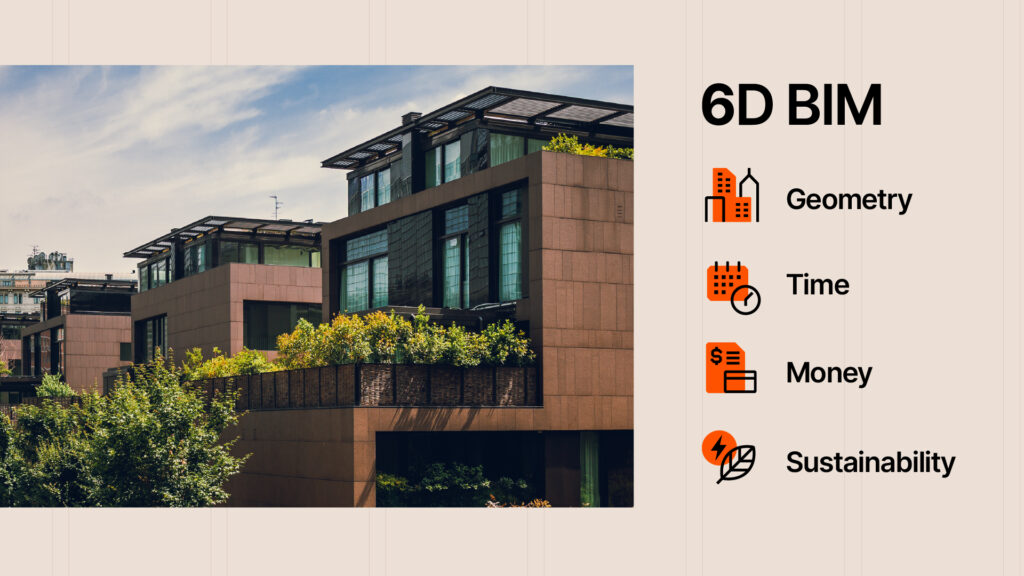
The Role of BIM in Sustainable Construction
Building information modeling (BIM) is transforming the architecture, engineering, and construction (AEC) industry. With this kind of sophisticated modeling, the industry has shifted from designing in 2D to 3D. This helps...