— 10 min read
Construction Material Storage: Tips for an Efficient Laydown Yard
Last Updated Sep 1, 2024
Last Updated Sep 1, 2024

Construction sites are full of moving parts – schedules to follow, teams to coordinate, and rules to stick to. But if building materials aren’t organized readily available to install on the project, both time and money are thrown down the drain.
Once planning begins, contractors and project managers have to be in lockstep on procuring and managing materials for the build. This ensures delivery and installation of materials is executed seamlessly.
In this article, we’ll cover the basics of material storage, strategies for managing and housing them, and pitfalls to avoid when planning the laydown yard.
Table of contents
The Challenge of Building Material Storage
Imagine having a complex Lego set with thousands of tiny bricks and other pieces spread out on a table. It can take hours to track down a needed piece to make progress on building a structure. If the parts are sorted early by color, type or size, then finding the correct brick, wheel or character takes just a few seconds.
Materials storage in construction is a similar concept. It involves strategically organizing and placing materials needed to be housed onsite for a project. Precise management and planning that enables quick and easy access to materials when it’s time for installation on the project.
Lost time and delays can easily rack up when materials aren’t properly tracked and stored in an organized way so subcontractors and site leaders can locate them quickly.
Developing an Efficient Site Plan
The key to material storage is efficiency – on a jobsite contractors need to know where everything is, and be able to get to it quickly. When developing construction site plans, it’s important to know what’s on the master schedule and account for materials that will be stored on site early on.
Contractors must also adhere to OSHA’s guidelines for material handling and storage onsite. Vertical construction, specifically in dense urban areas, requires even more strategizing since projects take place within tight areas.
Contractors and project engineers need to keep a close eye on the schedule. The schedule lets them know when different materials will arrive and when they’ll be installed. This helps engineers choose the right spot for the material laydown yard on the site map. The yard is where all the materials are stored until it's time to use them in the build.
Strategic Material Procurement
General contractors (GCs) need to coordinate very closely with vendors and subcontractors when procuring materials, making sure they’re delivered as close to installation as possible to prevent overcrowding the laydown yard.
Reviewing submittals and logging change orders regularly is a must to ensure the correct type and amount of materials are ordered and schedule to arrive on site at the right time.
Access to the Laydown Yard
When delivery trucks arrive on site to deliver materials it’s all hands on deck on the yard. The laydown yard needs to be in an easily accessible area so trucks can get on and and offsite with little to no issue. Forklift operators and workers need to work quickly make sure all materials are unloaded as quickly and efficiently as possible, especially if another delivery is scheduled soon after.
Each delivery driver will need detailed instructions of where they will need to pull in, and each forklift and crane operator will need to be clear on where they are laying down material. Clear site logistics plans prevent unwanted traffic jams and allows drivers to seamlessly enter and exit the site without interfering with other site activities.
Everyone on the yard should know exactly where trucks are going to pull in, where the forklifts or cranes are going to place each object and where the operating equipment is going to move next.
Stay updated on what’s happening in construction.
Subscribe to Blueprint, Procore’s free construction newsletter, to get content from industry experts delivered straight to your inbox.
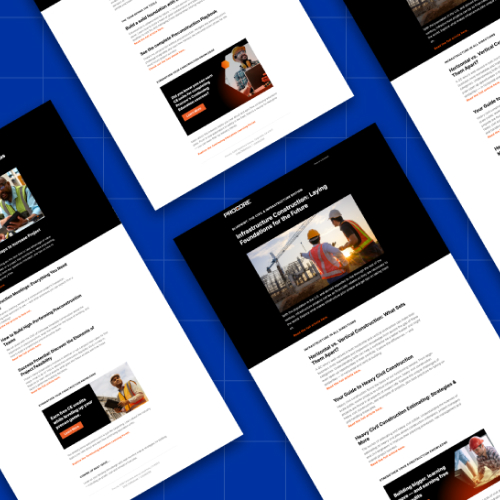
Material Organization
There are several different ways to organize materials that are stored onsite. Below are a couple methods that can help project engineers keep track of inventory.
Order of use
Sorting materials in the order that they are scheduled to be installed on the project is one efficient way to systemize how materials are stored. This method minimizes materials handling and streamlines the workflow by giving workers quick and easy access to items that are next in line for installation.
Type & Size
Organizing materials on the yard by type and size speeds up the process when trying to identify, locate and manage space in tighter areas. This strategy can also help with tracking inventory since materials are grouped together and easier to count.
Additionally, grouping the same materials together makes for a seamless drop-off when deliveries are made. Instead of distributing lumber in different locations on the yard, which may requiring extra maneuvering and manpower, designating one area cuts out the need for additional logistical work on engineers and contractors.
Tracking Inventory & Deliveries
As deliveries are made, the project engineer should cross reference the purchase order (PO), take receipt tickets and count everything that’s coming off the trucks. This ensures that what is being offloaded is what was initially ordered. If a GC ordered 2,000 feet of pipe and only 1,800 feet shows up, engineers can quickly call this out and work on a solution to avoid delays.
Material tracking is necessary past the delivery stage, though. Whether through quantity or weight, having an accurate count of materials can help GCs stay focused on managing the workflow, instead of scrambling for missing materials.
If a brick mason shows up to lay a shipment of bricks, for example, engineers should verify how much brick was laid, and ensure the correct amount of pallets are remaining.
Additionally, non-quantifiable materials, like wire, may need to be weighed regularly to keep up with how much has been installed on the project. A 300-lb spool of wire equals about 500 feet. If the spool weighs 150 pounds at the end of the day, the project engineer can estimate that 250 feet of wire was installed and cross-reference that with how much is left.
Proper inventory management gives contractors time to order more materials before they’re needed, instead of in the final hour.
Hazardous Materials
Special considerations need to be taken for any potentially hazardous materials that need to be stored on site. Project engineers have to familiarize themselves with all safety data sheets (SDS), which indicate the optimal storage conditions for different materials. Additionally, any substance with a SDS needs to be fully documented on site.
Toxic materials may require the construction and installation of special cabinets to maintain the proper amount of protection and the correct temperature. However, for the most part, the goal is to keep these materials off the jobsite until they are needed so they don’t have to be stored at all.
Protecting Materials on the Jobsite
Building materials are subject to two primary risks: damage and theft. This is true both for materials stored on site and those already installed or incorporated into the project.
Weather Protection
The unpredictability of weather conditions could jeopardize the integrity of certain materials. Extreme heat or cold, heavy rains or winds, or natural disasters can damage materials beyond usability requiring additional costs to replace them.
Once materials arrive at the yard, they need to be properly protected from the elements as soon as possible. Sheds may need to be put together to protect materials that cannot be exposed to the sun, wind, rain, or cold for extended periods. Project managers or GCs should make sure these contingencies are often built into plans when preparing submittals. This helps ensure all sensitive materials are accounted for and minimally exposed to the elements.
Using just-in-time (JIT) deliveries for materials that are at risk for damage by seasonal or unforeseen weather conditions can save both money and space on the yard for other materials. Having a precise site logistics plan and schedule can allow for certain materials to be installed as soon as they come off the delivery truck.
Additionally, asking vendors to hold on to materials as long as possible before delivery could also keep vulnerable materials out of harm’s way.
For example, a GC may place an order for drywall three months ahead of its installation date, with a one month buffer built in to avoid delays. If the vendor is able to source the material in two months instead of three, they may be able to request for the supplier to hold on to the material up until a few days before the drywall is installed. This saves the GC from having to figure out where to store and protect drywall from the elements for an entire month if the facility hasn’t been roofed in.
Courses about construction.
For construction.
Unlock your career potential with our free educational courses on Health & Safety, Data in Construction, and more.
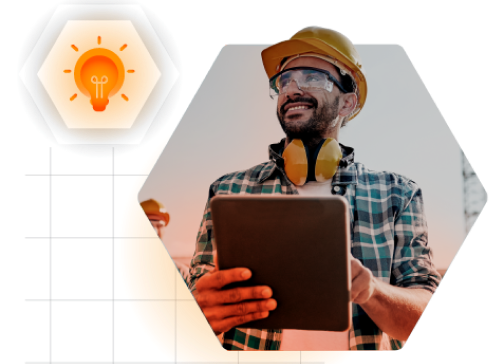
Jobsite Security
Theft on a jobsite is always a risk. A significant amount of jobsite security is necessary when working on a site with a large, open-air laydown yard. It’s a good idea to purchase mobile security systems that include CCTV cameras as well as bright lights to help illuminate the yard. Additionally, investing in a strong fence can help deter intruders from entering the site.
Occasionally, GCs will need to keep expensive equipment on site during off-hours. Machines like welders are sometimes lifted up by a crane and suspended in the air to keep them from being stolen. Another anti-theft technique is to park equipment very close to each other so they are almost tangled together, making it extremely difficult to get any one machine out.
Best Practices for Storing Materials
It can be easy on a jobsite to overlook material storage or consider it a formality. But the best job sites have a firm grasp on all the logistics around their material storage. Below are some key considerations for contractors and site leaders to maintain an organized material laydown yard.
1. Communicate the plan.
Project engineers need to coordinate with subcontractors and site leaders daily. This helps make sure all teams are aware of any deliveries, changes, or specific tasks that are taking place on the project. Additionally, logging issues, such as delays or materials damage right away, can keep further problems at bay.
During the planning phase of a project, even a quick sketch of your laydown yard can go a long way toward efficiently running your project. The preconstruction meeting is a great opportunity to communicate material storage and logistical plans to all subcontractors and vendors in advance.
Coordinating with the procurement team, contractors and project managers and cross referencing material deliveries with the master schedule will keep the yard and the project running smoothly.
2. Maintain clear ingress and egress.
Ensure delivery trucks, forklifts and cranes can easily get in and out of the yard without complicated maneuvers. Project managers, supers and foremen need to communicate closely on jobsite movement, including equipment and material deliveries. Clear pathways for ingress and egress is essential to keeping projects on schedule and reducing the risk of injuries or accidents.
Keeping your yard clean and tidy, even as materials are constantly moving in and out, can seem overwhelming. Organizing and straightening the yard will help mitigate risk of injury or material damage. It also sends a clear message to crews and outsiders about the expectations of maintaining an organized, safe site.
3. Think about waste.
Waste material is still material. Plans for dumpster delivery, management and pickup need to be built into all your schedules.
Having a clear plan for waste is just as important as planning out the logistics of a construction site and the laydown yard. Waste takes up physical space and requires a labor force to move it, just like any other material onsite.
Budgets should allocate for regular dumpster delivery and haul offs. Without enough dumpsters on site to collect waste, GCs can end up in a real jam and be forced to pay a premium to have one rushed over.
4. Keep it clean.
A clean yard is an efficient yard. Cleanliness communicates to both workers and outsiders that the site is being run competently.
Getting materials storage and tracking spot-on sets the stage for a smooth running construction site. It’s all about being efficient with space management, accurately tracking supplies, and planning ahead to avoid any potential issues. When there's a system in place that accounts for every nut, bolt, and beam from the moment they arrive until they’re part of the build, the project stays on track without costly delays.
Was this article helpful?
Thank you for your submission.
100%
0%
You voted that this article was . Was this a mistake? If so, change your vote here.
Scroll less, learn more about construction.
Subscribe to The Blueprint, Procore’s construction newsletter, to get content from industry experts delivered straight to your inbox.
By clicking this button, you agree to our Privacy Notice and Terms of Service.
Categories:
Tags:
Written by
Makenna Ryan
Makenna Ryan is a Solutions Engineer at Procore. Prior to joining Procore, he spent seven years at McDermott International Inc. as a construction Manager and Senior Equipment Engineer. He also spent three years as a Project Engineer at Subsea7. Makenna received his B.S. in Mechanical Engineering and Technology from Texas Tech University. He is based in the Houston area.
View profileCait Bladt
12 articles
Cait Bladt is a multi-award winning freelance writer and producer. Her work has appeared at Vice, ABC News and Rolling Stone among others. She currently lives in Brooklyn with her cat Patricia.
View profileExplore more helpful resources
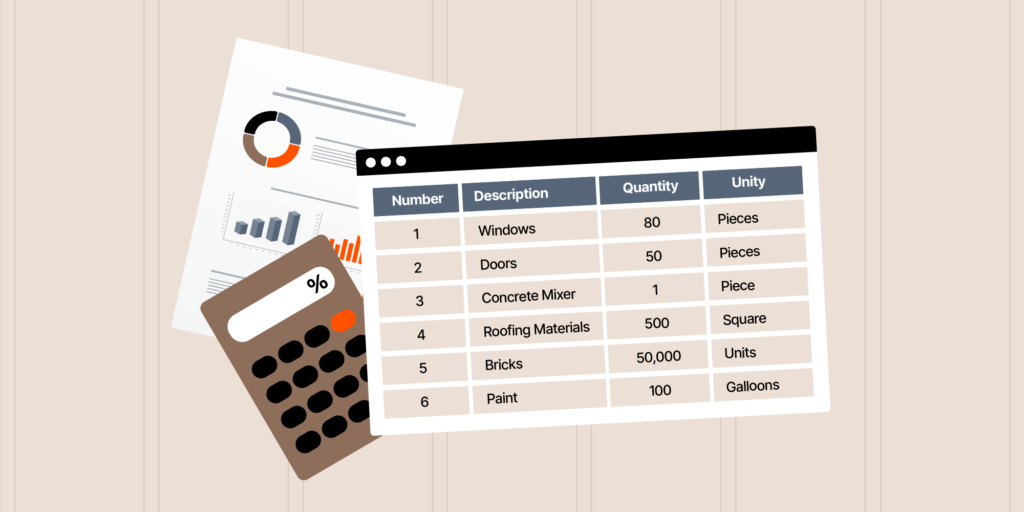
Key Benefits of a Construction Procurement Log (With Free Template)
By the time everything is purchased for a construction project, it represents not just a lot of money. It also represents a lot of energy from the teams involved. Getting...
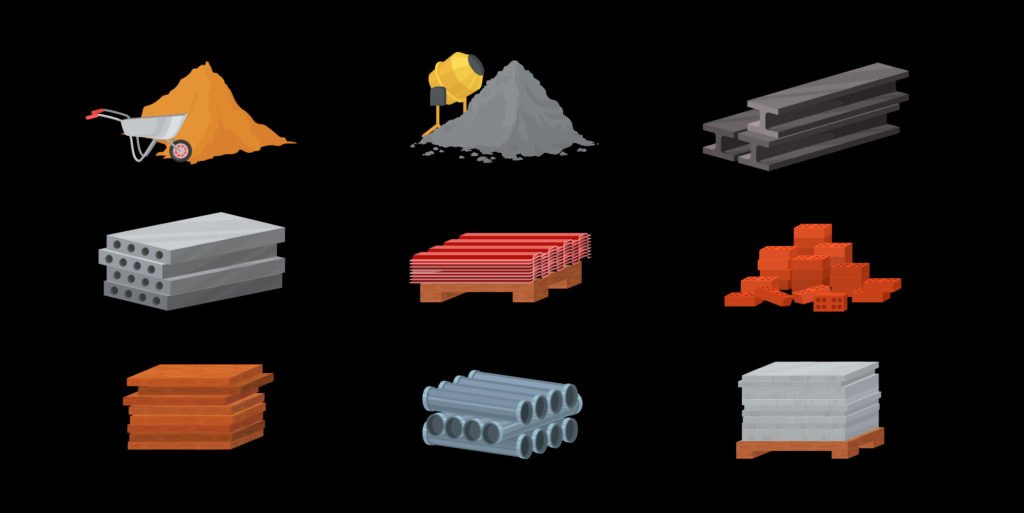
Material Management in Construction: A Project Manager’s Guide
Construction materials represent one of the key components for pulling off successful projects, and also one of the biggest expenses contractors face. Optimally managed materials procurement, storage and installation can...
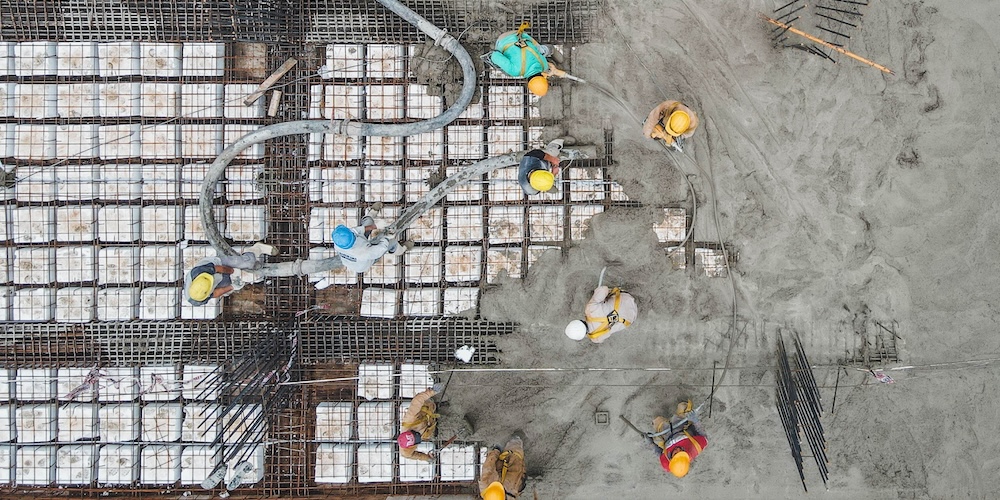
Mastering Construction Resource Management: Strategies for Success
Completing construction projects successfully requires the careful management of various resources: labor, materials, equipment, money, time and information. Since these resources are finite, allocating them wisely is crucial for minimizing...
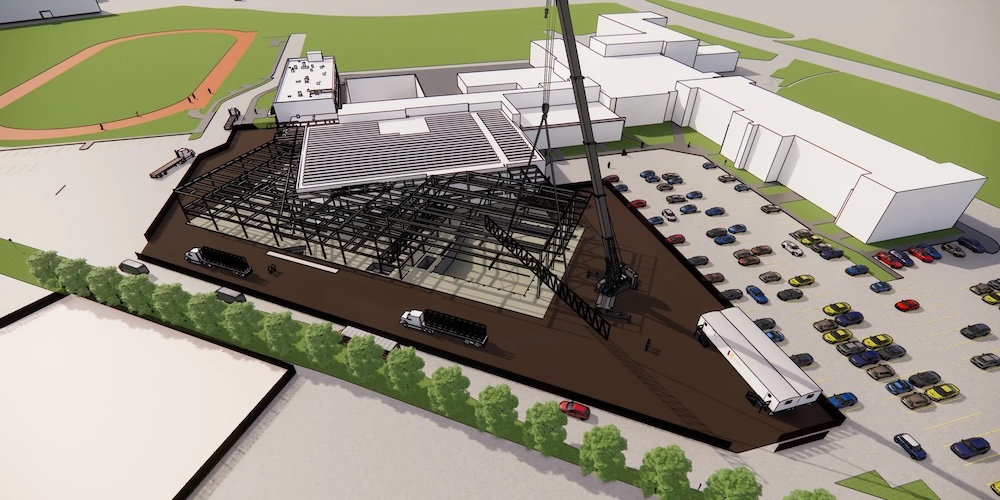
Optimizing Material Logistics & Procurement: Insights from a Sports Facility Project
As an assistant project manager on the Cadigan Wellness Complex Project at Boston College High School, managing material procurement and logistics is one of my primary responsibilities. In addition to...