— 6 min read
Modular Construction and MEP: A Collaborative Pairing
Last Updated Apr 11, 2025
Last Updated Apr 11, 2025
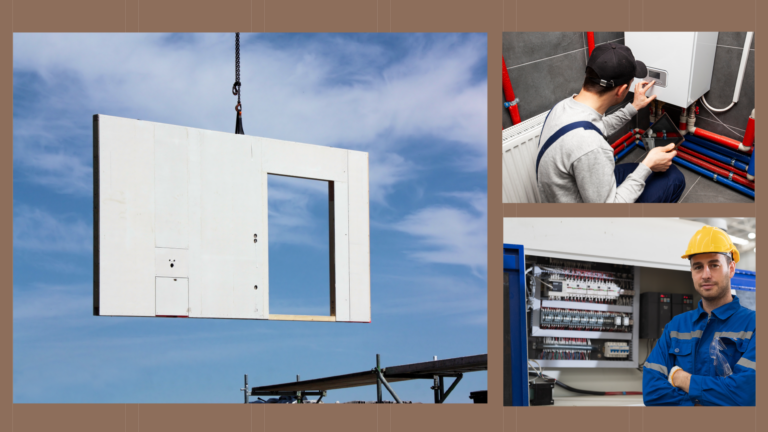
In an age of supply chain disruptions, workforce shortages, and rising material costs, off-site construction — including modular construction methods and prefabricated materials — is surfacing as a multipurpose solution.
Modular construction is streamlining the coordination of mechanical, electrical and plumbing (MEP) tradespeople and tasks on jobsites — but yielding its advantages demands strict attention to quality control, logistics and planning.
This article discusses how and why to integrate modular construction into MEP practices to simplify coordination and boost project performance.
Table of contents
Using Off-site Methods & Materials
Off-site prefabrication for onsite placement can generate efficiencies and minimize risk through just-in-time delivery, streamlined assembly and reduced material waste. Increasingly, projects involving hospitals, hotels, schools and multifamily housing deploy permanent modular construction (PMC) to save costs and time.
Two types of PMC further expand the options available. In prefabricated prefinished volumetric construction (PPVC), complete rooms or units, such as bathrooms or apartments, are built identically or customized in groups for ADA adaptations.
Other projects leverage the versatility of panelized, or non-volumized, walls, ceilings, or floors, prefabricated with wiring or chases. Their compact size simplifies transport, and onsite, they can be assembled in varied configurations.
The Advantages of Modular Construction
Modular units are precision-built by manufacturers in climate-controlled conditions for fewer defects and more consistent quality. Other benefits of modular construction include:
Shortened Timelines
By preventing weather delays and facilitating prep work on the jobsite while modular construction is underway, modular projects can outpace traditional construction by 30-50%.
Mitigating Risk
The risk of accidents declines when workers are laboring indoors and fewer are needed on-site. As a bonus, modular construction can help ease the pressure created by labor shortages, as much of the labor is not done on-site.
Cost Savings
Fewer on-site labor hours and reduced waste can generate savings of 5–10%. However, savings can depend on the contractor’s experience, the differences in labor costs onsite and offsite, and the replicability of the modules.
Less Waste
Offsite manufacturers can order supplies to exact specifications, for less waste than the onsite practice of cutting down oversized materials. In one Modular Building Institute study of comparable multifamily housing projects, modular construction reduced wood waste by at least 23%.
MEP Integration in Modular Units
Modular construction can streamline mechanical, electrical and plumbing management and speed up MEP connections in the structure.
For general contractors, modularity can change the scope of specialty contractor relationships. It can cut down on the number of MEP tradespeople needed onsite, or it might involve contracting with manufacturers who both build and install their units.
There are a lot of different parts and components to modular construction, but when it comes to MEPs and other finishers, you're now taking all the trade work and doing it in a warehouse. That is five to seven fewer trades that are working on top of each other — which can significantly aid in preventing trade stacking.
Jacob Kunken
Solutions Engineer, Heavy Civil
Procore
After prebuilt units are delivered and secured in place, MEP tasks can be performed in straightforward fashion, as electrical connections are made from room to room, or prefinished bathrooms are linked to building systems. With fewer people onsite, coordinating MEP tradespeople and other finishers is simplified.
Modular construction should be used judiciously because it doesn’t offset the costs or dilemmas associated with every MEP challenge. For instance, simple adjustments to mechanicals don’t demand the time that other trades devour, so modularity might not offer additional efficiencies or risk mitigation.
Quality Control and Logistics with MEP
Modular construction offers the potential for more accurate lead times and production scheduling, but the need to plan for material staging, delivery, and installation sequences is critical.
The act of triaging — assessing and delivering information to the right person at the right time — drives planning and scheduling at every stage of design, production, transportation, site preparation and installation.
Modular construction also requires multi-stage quality control. First, the manufacturer is responsible for rigorous inspections at the facility. Then, after units arrive onsite, meticulous inspections are needed to check for any damage or changes undergone in transit.
During installation, frequent inspections assure that all connections are being made properly and, if needed, adapted to site conditions. By the building’s hand-off, constant and overlapping vigilance confirms commissioning requirements and earns the space its certificate of occupancy.
Courses about construction.
For construction.
Unlock your career potential with our free educational courses on Health & Safety, Data in Construction, and more.
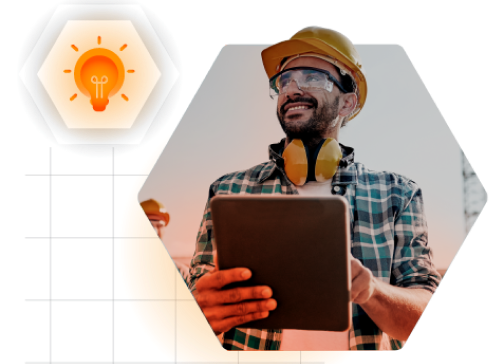
BIM and Technology in Modular MEP
Building Information Modeling (BIM) and its enablement of data-driven decisions can help dovetail MEP into prefabrication.
Use of BIM can speed up the design process by identifying issues in digital space before they become manufactured realities. The power of clash detection and correction before prefabrication alleviates the risk of costly delays and onsite adjustments.
On the jobsite, augmenting BIM with 3D imaging software enables pinpoint planning of modular rough-ins. The software can generate scans that verify whether completed sections are ready to accommodate prefabricated elements.
If any anomalies appear, such as a ductwork opening misaligned with its BIM representation, the prefabricated rough-ins can be adjusted without the need to chip into concrete.
Combining Modular Construction & MEP: Challenges and Considerations
These tips to a strategic approach can help contractors avoid missteps and extract modular construction’s promised cost and labor savings.
Go hybrid.
Build a few units, such as bathrooms, onsite. When the specs are perfected, order the rest for prefabrication offsite.
Account for the unknown.
Site conditions and unforeseen circumstances, from weather delays to archaeological finds, can counteract the gains of modularity. Manufacturing modular units to allow adjustments as needed can minimize change orders and speed up recovery.
Know the necessary codes and regulations.
Modular units must meet building codes and zoning regulations where they are installed, not where they’re built. Strict attention to local ordinances ensures compliance.
Prioritize site preparation.
Counting backwards from the anticipated delivery date, the pull plan to prepare for the people and things that will be needed to accept the modular units, store them, and start timely installations and connections.
Leverage logistics.
Time delivery of prefabricated units to coincide with complementary procedures. For example, position a crane to perform its traditional tasks and, when the time comes, hoist modular units into place — no adjustments needed.
Easing into Modularity
Contractors experienced in modular construction maximize the benefits through proper planning, anticipating unknowns, adding float time in the schedule, and writing unbreakable contractual definitions that protect their interests in case of unforeseeable hurdles.
When integrating modular construction methods into MEP processes, start small to build a track record and trust. Inexperienced contractors won’t win bids for modular-based health centers, but they can learn the ropes with relatively simple developments such as small housing projects.
As covered, it's also very helpful to invest in BIM and imaging technologies. BIM can be an incredible tool to create the data-driven decision-making that efficiently integrates modularity into operations.
Modularity allows everyone in the construction process to be a bit more efficient because you know how many workers you need to have on-site. You know when your material is coming. You know what your lead times are, and you can adjust your schedule accordingly.
Jacob Kunken
Solutions Engineer, Heavy Civil
Procore
Advances in technology and processes are making modular construction central to commercial projects. Its steady integration into MEP will continue driving the productive quest for more operational efficiency and less risk through accelerated timelines, safer jobsites and simplified coordination.
Was this article helpful?
Thank you for your submission.
0%
0%
You voted that this article was . Was this a mistake? If so, change your vote here.
Scroll less, learn more about construction.
Subscribe to The Blueprint, Procore’s construction newsletter, to get content from industry experts delivered straight to your inbox.
By clicking this button, you agree to our Privacy Notice and Terms of Service.
Categories:
Tags:
Written by
Jacob Kunken
21 articles
Jake Kunken currently works as Solutions Engineer for Procore's Heavy Civil division. He brings 14 years of experience working in various construction roles in New York and Colorado, including laborer, assistant carpenter, carpenter, assistant superintendent, superintendent, construction manager, safety manager, and project manager. Jake also spent time in EHS as an environmental engineer for Skanska. He’s worked on more than 40 commercial projects from ground-up, to heavy civil, hospital work, and tenant improvement. Jake studied Ecological Technology Design at the University of Maryland.
View profileDiane McCormick
Diane McCormick is a freelance journalist covering construction, packaging, manufacturing, natural gas distribution, and waste oil recycling. A proud resident of Harrisburg, PA, Diane is well-versed in several types of digital and print media. Recognized as one of the premier voices in her region, she was recognized as the Keystone Media Freelance Journalist of the Year in 2022 and again in 2023.
View profileExplore more helpful resources
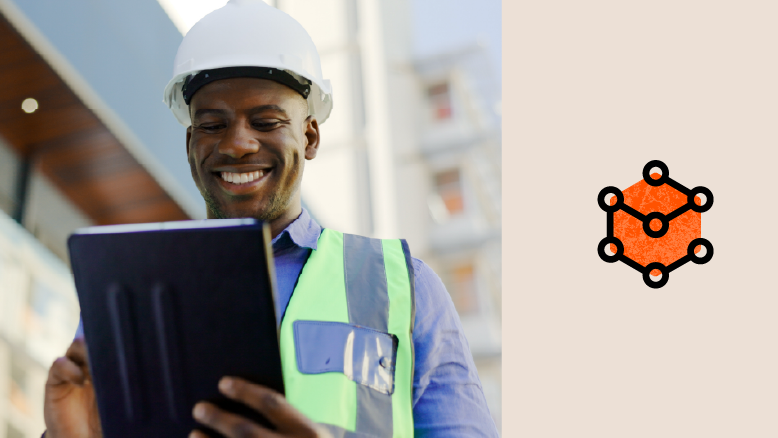
Connected Construction: Transforming the Industry Through Integration
Construction projects are becoming increasingly complex, so companies need to innovate to accurately and profitably complete these modern structures. Connected construction — using technology and data to improve communication, processes...
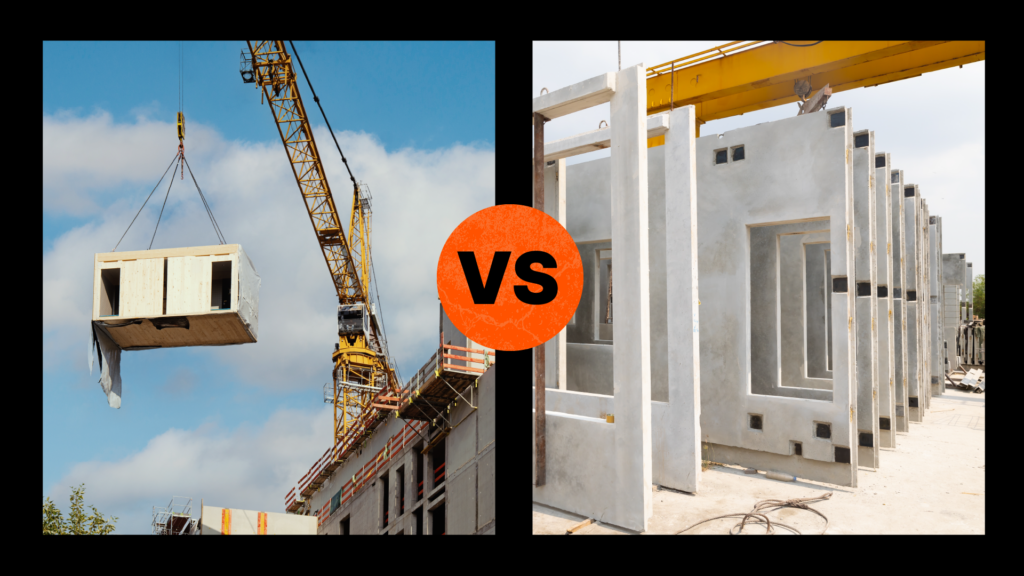
Off-Site Construction: Prefab vs. Modular
As the construction world becomes ever more competitive, deadlines get tighter and the margin for error gets slimmer, project owners around the world are always looking for an edge. Thanks...
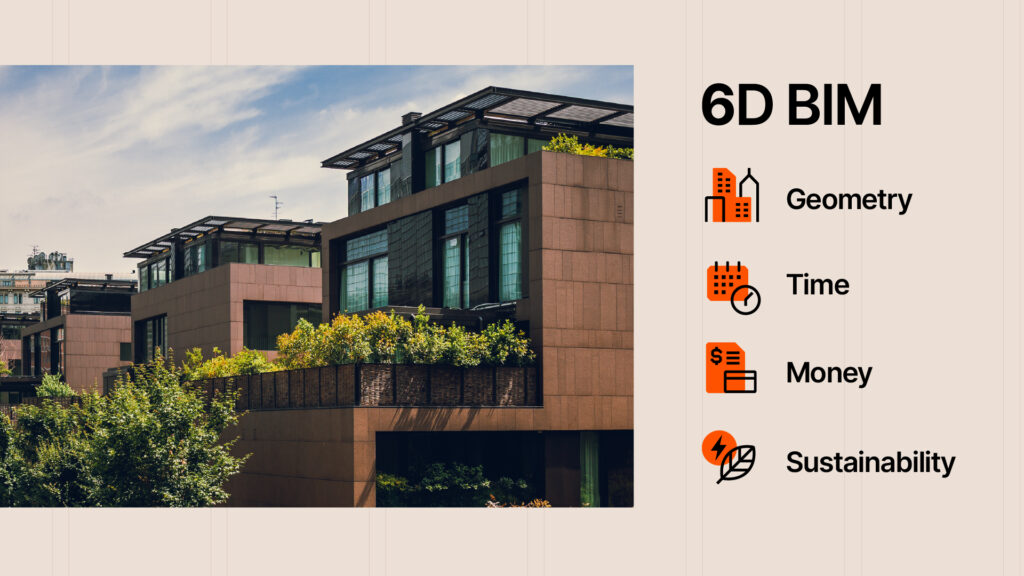
The Role of BIM in Sustainable Construction
Building information modeling (BIM) is transforming the architecture, engineering, and construction (AEC) industry. With this kind of sophisticated modeling, the industry has shifted from designing in 2D to 3D. This helps...
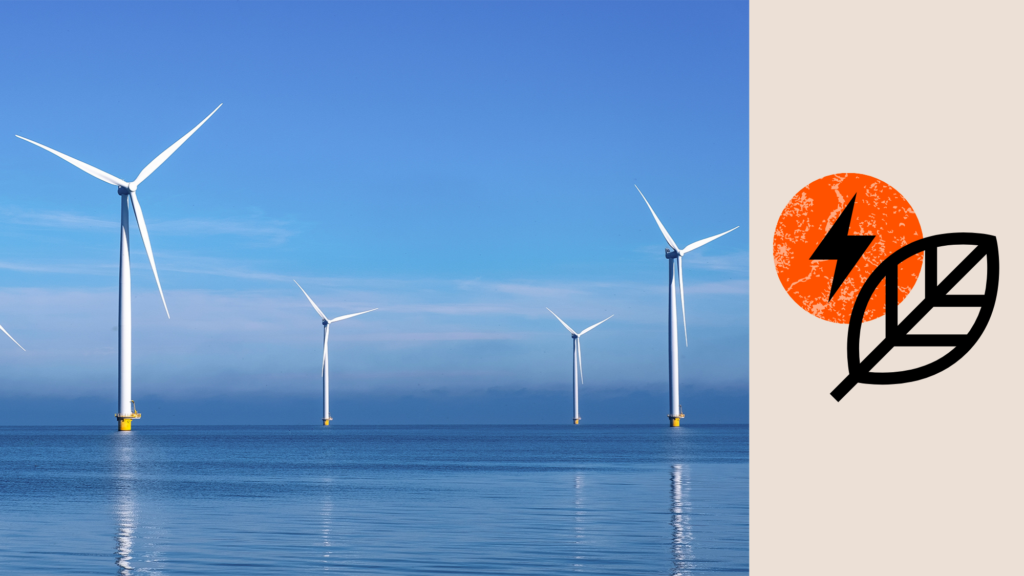
Harnessing Energy: Advancements in Offshore Wind Farm Construction
Offshore wind farms harness the potential of oceanic wind resources, providing a reliable and eco-friendly power source. As energy demand continues to escalate worldwide, these vast installations offer construction professionals...